20 Minutes With Scott Leipprandt
Rachel Fowler, Associate Editor | TLT 20 Minutes July 2016
Make oil analysis part of a larger reliability program, urges this technical services manager with Lubrication Engineers.
SCOTT LEIPPRANDT - The Quick File
Scott Leipprandt has been involved with maintenance and reliability efforts for most of his professional career. He joined the Lubrication Engineers (LE) team in October 2007 and is the manager of LE’s technical services department. His responsibilities include overseeing a team of engineers and technical experts who help customers develop solutions for their lubrication challenges. Over the years he has helped countless companies with the advancement of their lubrication reliability programs.
Prior to his time with LE, Leipprandt was with a large semiconductor manufacturing plant for almost 20 years. His responsibilities as facility engineering manager included plant maintenance, plant engineering, environmental regulations and construction services. Having the responsibility of providing uninterrupted services for a 24-hour, seven-day-a-week manufacturing operation has instilled in him a high regard for the importance of reliability in achieving production goals.
Scott holds STLE’s CLS™ and OMA I™ certifications. He also is an NLGI Certified Lubricating Grease Specialist and SMRP Certified Maintenance & Reliability Professional. He has earned several MLT certifications. He has a bachelor’s of science degree in mechanical engineering from Michigan State University and has completed numerous graduate level management courses.
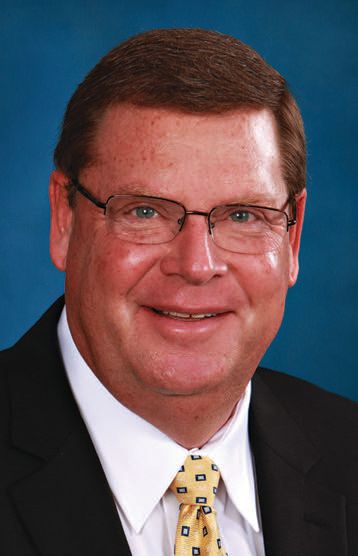
Scott Leipprandt
TLT: How do you help customers better understand and more effectively use in-service oil analysis?
Leipprandt: We have a wide variety of customers, and they differ greatly where they are on the reliability journey and how effectively they use oil analysis. Some organizations only use oil analysis to determine the lubricant health, which of course is very important but not the entire story. We have other customers with very mature oil analysis programs that are an integral part of their condition-based maintenance (CBM) efforts, much like vibration, thermal or ultrasound monitoring would be.
Part of our role is helping customers improve effectiveness by highlighting the difference between just doing oil analysis and developing an oil analysis program that is part of an overall reliability program. If companies approach oil analysis as a tool for developing leading indicators—not just looking at the lubricant health but also for the equipment condition and contamination control—they would have the potential of more effectively using oil analysis and obtaining greater value for their efforts.
TLT: What do you mean by an oil analysis program?
Leipprandt: It may vary depending on whom you ask, but in general an oil analysis program includes these steps:
•
Identify program objectives.
•
Determine sampling strategy.
•
Select appropriate test packages.
•
Establish evaluation program.
•
Manage the program.
TLT: How do you identify program objectives?
Leipprandt: Identifying program objectives is really just documenting what we are trying to achieve with an oil analysis program. Companies often consider program objectives but stop short of documenting them or developing sufficient detail. Objectives become more useful if they are specific, measurable and documented. It also is important to develop a baseline of the current state so we can measure the progress as the program moves forward.
For example, extending component life is a common objective, and controlling outside contamination in the lubricant is a major factor. Knowing the current cleanliness of the lubricant, being familiar with life extension tables and setting a goal for future cleanliness are all important in reaching the objective of extending component life.
Some additional objectives to consider for an oil analysis program are:
•
Improve asset reliability.
•
Reduce unscheduled downtime.
•
Identify and eliminate repetitive problems.
•
Obtain maximum use of lubricants.
•
Reduce maintenance and lubricant costs.
•
Use proactive maintenance, supported by predictive maintenance technology, to help achieve condition-based maintenance.
Scott Leipprandt in the laboratory.
TLT: With regard to the actual taking of the samples, what should be considered?
Leipprandt: A critical part of any program is determining sampling strategy, which includes identification of equipment, sampling schedule and methods.
•
Identify equipment. Survey all equipment and rank according to criticality. Criteria typically include impact to production, replacement cost, replacement lead time, downtime and labor. The equipment list should include the unit ID, manufacturer and model number, sump capacity and filtration information (micron size, lubricant manufacturer, lubricant type and viscosity grade).
•
Identify initial frequency and sampling schedule. When considering the frequency of sampling, the criticality of the equipment is an important consideration but so are the operating environment and severity of service. Consulting the OEM recommendations and the advice of the lubricant supplier or reliability consultant should help with setting the correct frequency. Oil analysis results will reveal the condition of the lubricant and the equipment, as well as the amount of contamination. As the program progresses, lubricant drain intervals can be extended, but caution should be used when considering extending the interval between samples until consistent baselines have been established.
•
Determine sampling hardware and methods. Many types and brands of sampling hardware are available to help with obtaining oil analysis samples in a safe fashion without interruption to production. The goal is to sample in an active zone where the sample will be most representative of the lubricant in use. It also is important that sampling valves, vacuum pumps and bottles are properly flushed, and the sample is well documented. We frequently see sample results that do not trend with previous history, and the reason is not a problem with the oil in service but with the sample that was taken. Typically if results do not trend with the previous history, a second sample should be drawn before any other actions are taken. And finally, getting the samples to the laboratory quickly after they are taken is imperative.
TLT: How does a client choose tests that are appropriate for meeting program objectives?
Leipprandt: Test slates are frequently determined with the support of the Lubrication Engineers (LE) reliability consultant or by looking at the test packages offered by most major laboratories. Typically we want to determine the condition of the lubricant and if it is suitable for further use. The type of testing done to determine this—such as viscosity, elemental, TAN and TBN—varies with the type of lubricant, but the objective is the same. Oil analysis also can give us insight into the condition of the equipment through trending the wear metals in elemental analysis and particle quantifier. Analytical ferrography is an extremely useful test in determining equipment condition, not just to support root cause analysis.
Another consideration when selecting test packages is evaluating the effect of contamination on the equipment and lubricant. Many companies have recognized the need for contamination control and use ongoing oil analysis to evaluate the effectiveness of the program. This is typically supported with particle count and water by Karl Fischer tests.
TLT: What’s involved in the evaluation process?
Leipprandt: Most of the larger oil analysis labs have an extensive database and have developed flagging limits using statistical software. These standard “alert” and “action” flags are sufficient for most users getting started, as opposed to developing their own internal flagging limits.
It is important for the end-user to understand that the criteria being used for these flags are based on the information provided to the lab. This includes the type of equipment, manufacturer and model number; type of lubricant, viscosity and manufacturer; and filtration size. The length of time the lubricant and equipment have been in service also has an effect. Is 300 ppm of iron in a gearbox a high number? Some may think so, but it makes a big difference if the oil has been in service for six months or 10 years. (An excellent article on oil analysis flagging limits was in the January 2016 issue of TLT.)
It is important to understand how much more reliable the data is when viewed as a trend as opposed to a single data point. Trending and graphing results offer an easy way to read the condition of the equipment, condition of the lubricant and level of contamination. Never base a decision to tear down equipment on a single data point. Reliable trending data can be used by organizations to help schedule CBM for oil changes as well as filter and desiccant breather replacements. The data also is very helpful in determining if the best lubricant is being used for the application.
Scott Leipprandt with Lubrication Engineers’s Full Torque Diesel Fuel Improver.
TLT: What should be considered in managing the program?
Leipprandt: It’s not enough to create a program and then walk away. Has a path and process for taking action been established for when reports indicate an abnormal condition? Many programs are ineffective because they are diligent with taking samples but not as decisive with actions on abnormal reports.
In any reliability program it is important to track performance, benefits and cost. It is critical for metrics to be in place to ensure accountability for results and highlight program health and performance. ROI should be tracked, and the value of the program highlighted as progress is made.
Looking at oil analysis results throughout the year provides many leading indicators of lubricant condition, equipment condition and level of contamination. However, looking at these trends also could be considered as lagging indicators. They could help answer questions on progress made toward meeting some of the program objectives: Has lubricant life been extended? Has progress been made toward meeting cleanliness goals in an effort to maximize equipment life? Changes in trends may warrant shifts in various aspects of the program and need to be considered as part of the continuous improvement, and management, of an effective oil analysis program.
TLT: What are your final thoughts on oil analysis programs?
Leipprandt: Team resources are very important to success. An internal champion should be assigned, and outside resources should be added as needed, such as a reliability consultant with the expertise to assist with these efforts.
An oil analysis program is considered a basic building block of any reliability program. It typically does not require significant capital to get started and implementation does not require any interruption to production. For companies that do not do oil analysis, it is past time to get started.
For those already doing oil analysis, it is always a good idea to look at the program for any areas where improvement can be made to support overall reliability efforts. Remember that reliability is a journey, not a destination.
You can reach Scott Leipprandt at s.leipprandt@le-inc.com.