20 Minutes With Bryan Johnson
Rachel Fowler, Associate Editor | TLT 20 Minutes June 2016
This 25-year industry professional discusses the challenges of lubricating machinery in a nuclear power plant.
BRYAN JOHNSON - The Quick File
Bryan Johnson has worked for the last 25 years as the predictive maintenance and lubrication engineer at Palo Verde Nuclear Generating Station in Tonopah, Ariz. He holds a master’s of science degree in mechanical engineering from Rensselaer Polytechnic Institute with an emphasis in tribology and is pursuing a master’s degree at Harvard University’s environmental sciences program.
Johnson is the chairman of ASTM’s subcommittee D02.CS96, an international standards committee that develops standard practices, guides and test methods related to predictive maintenance and the condition monitoring of in-service lubricants. Johnson has been awarded Fellow status by ASTM for his contributions and serves as chair of the board of directors for the International Council for Machinery Lubrication. He also is an advisory board member of the Auburn University tribology minor. He is an NLGI International Certified Lubricating Grease Specialist (CLGS) and became an STLE Certified Lubrication Specialist™ (CLS) in 1997. He has presented training internationally on behalf of STLE and is a former chair of the STLE Power Generation Counsel.
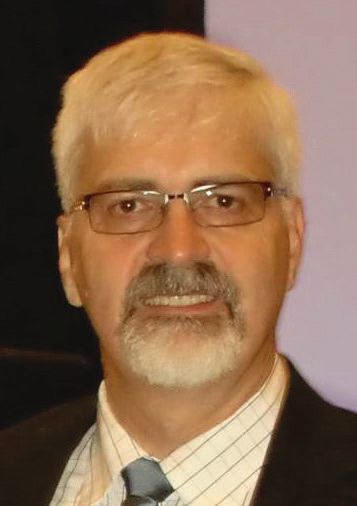
Bryan Johnson
TLT: What are the biggest challenges in running a nuclear power plant?
Johnson: My employer, Palo Verde Nuclear Generating Station, is the largest commercial producer of electricity in North America. Operating a nuclear power generating station is a 24/7/365 business. The station has a highly trained and effective staff to oversee its design, maintenance and operation. Safety is a guiding principle within our business and a core value that we use when making plant decisions. A strong safety focus has many benefits, including improved plant reliability. This in turn has directly contributed to high quality reliable power being available to the plant’s customers.
Palo Verde is located in the Sonoran Desert. This location has extreme high temperatures with a much higher annual ambient temperature than other locations within the U.S. During the summer months the enclosed turbine building has particularly high ambient temperatures of 125 F (52 C) or more. These temperatures result in higher operating temperatures for machinery than those typically found in other industrial settings. Following vendor recommendations listed in their documentation for oil viscosities can result in an inadequate oil film thickness. As oil viscosity reduces with increasing temperature and the plant has higher local ambient temperatures, the use of a step increase or more in viscosity can be required to ensure acceptable lubrication.
TLT: The biggest demand for electricity occurs on summer afternoons. How do you reliably deliver the most power on the hottest days in the desert?
Johnson: The summer season in Arizona has the highest system electric power requirements. Reliable plant operation, though, is more than a focus on the summer period, as our customers require highly reliable power on a 24/7/365 basis.
It is possible to perform too much maintenance. Performing maintenance before it is needed can introduce reliability issues with machinery potentially unavailable for use during peak periods. Palo Verde uses a value-based reliability- centered maintenance strategy to evaluate machinery maintenance requirements (
see What is Value-Based Reliability- Centered Maintenance?). The overall expected benefits to machine reliability in the context of plant performance and reliability are carefully evaluated, planned and then completed. A back-end review of performed work is used as a feedback loop to the overall maintenance requirements to optimize performance. The use of this maintenance strategy ensures a high level of machine reliability 24/7/365.
What is value-based reliability-centered maintenance?
Value-based equipment reliability is the establishment and optimization of preventive maintenance tasks and frequencies in order to balance the maintenance performed on station equipment with its impact to station safety and production. It is the realization that changing out a component before it’s needed can be a detriment to safety, reliability and costs.
Implementation of value-based equipment reliability results in minimizing the total combined maintenance costs of both time-based and condition-based maintenance sectors. Minimizing operation and maintenance cost minimizes equipment downtime, which in turn reduces collateral station resources needed to support maintenance activities. This affords station resource flexibility to focus on needed corrective maintenance, the reduction of corrective maintenance backlogs and the implementation of forward looking items such as modifications and projects.
TLT: Few people in the tribology community have experience with the effect of radiation on our products. Does this significantly change the performance of the lubricants?
Johnson: External environmental effects on lubricants certainly impact performance. Harsh plant environmental conditions might include high temperature, steam, water and radiation. Lubricants at Palo Verde are considered to be important functioning parts within the machine, and their application and expected performance are evaluated in the context of both normal and transient operating conditions. In some cases the lubricant is evaluated analytically or through laboratory or full-scale machine tests that are part of a harsh environment machine test.
Radiation can be a harsh environmental condition to the lubricant. Extreme radiation exposure breaks down the bonds within the lubricant molecular structure followed by cross linking and eventually the hardening of the lubricant into a solid material.
However, radiation doesn’t reduce lubricant performance until exposure has occurred at levels
significantly higher than those typically experienced within a nuclear power plant. Palo Verde hasn’t experienced radiation impacts to its lubricants or their machine applications that would pose a challenge to their operations.
The reactor is located in the large domed structure behind Bryan Johnson. The reactor is a vessel containing long thin tubes or pins that house the radioactive fuel pellets. The pins are organized in a series of arrays known as fuel bundles. The reactor is used to heat pressurized water that in turn is used to generate steam. The heated water from the reactor is pumped into a large heat exchanger known as the steam generator. The heated water creates the steam, which flows from the steam generator toward the turbine.
TLT: What key changes have you seen in the lubricants industry during your career?
Johnson: I feel that the new professional entering our industry has many more opportunities to learn than my group had 25 years ago. This is due to increased industry emphasis on knowledge transfer and training. STLE serves a strong role in the development of the lubrication professional through its meetings, training and certification efforts.
Auburn University is another fine example of the industry’s professional growth through its undergraduate tribology minor within its accredited STEM program; the school is producing a stream of young, well-trained engineers and chemists who are ready to step into the job market.
Other groups throughout North America and the world have entered this market with excellent training and certification products targeting market segments beyond the STLE core audience to include frontline mechanics, electricians and lubrication engineers who work directly with plant equipment. The International Machinery Lubrication Council, through its testing and certification programs, is a great example of this.
Increased personal capabilities through training are driving a change. The combined efforts of training and certification organizations have raised the status and importance of all professionals working within the industrial sector. At one time the plant lubrication job was assigned as an entry-level position. With increasing focus on machinery asset preservation and an enhanced plant-management understanding of the vital function of the maintenance technician charged with the implementation of the lubricant program, this role is now going to more experienced personnel. With this shift, the perceived value of the oiler or plant greaser is becoming a better match to their actual plant value. As the stature of the frontline maintenance lubrication professional has increased, so too has the perceived value of the plant lubrication engineer.
The turbine generator has four steam turbines coupled to a generator rotor that rotate in unison. The turbines use steam from the steam generator to rotate the generator’s rotor within a magnetic field producing the electricity. The generator is located behind the three engineers pictured on the left. Three of the turbines are visible into the distance on the right. Pictured from left to right: Dan O’Brien, Mark Brutcher, John Glover, Bryan Johnson, Francisco Diaz Gallegos and James Kosinski. Not pictured: David King.
TLT: Palo Verde’s on-site in-service lubricant condition monitoring test laboratory processes grease samples. Why does this work in house?
Johnson: Grease is an extremely important machine lubricant with broad applications throughout all industries. Oil condition monitoring is a mature industry used to determine both the oil’s and the machine’s condition; greases are not commonly tested. In-service grease testing poses unique challenges. Many grease applications use small volumes of grease. Obtaining a representative sample of the bulk grease is difficult. Once a large enough sample to test is in hand, a lack of standard tests that provide meaningful data becomes an obstacle. These challenges have slowed the growth of grease condition monitoring testing.
Grease must migrate into the machine load zone to provide lubrication. When the grease is too stiff to migrate, it can’t lubricate. Testing to measure grease consistency can provide insight into the grease’s expected performance. Wear occurs when the lubrication is poor, so wear testing is a vital grease test component.
Palo Verde routinely tests grease-lubricated bearings and grease from large motor-operated valves for condition. Samples from these applications are generally representative of the bulk due to the sampling techniques used. Testing performed includes grease consistency, chemistry and wear metals. Test methodologies capable of making these measurements are vital to obtaining useful and trend able data from in-service grease samples.
TLT: Climate change is a significant world environmental and technical issue. How do you see nuclear power fitting into the future generation mix?
Johnson: The world requires reliable sources of electricity to allow economic development. Power generation drives economic growth and is one of many contributors to global carbon emissions when the combustion of fossil-based fuels is used to generate the electricity.
Recently the United Nations sponsored a meeting in Paris and completed an agreement among the leaders of 195 nations to reduce carbon emissions into the atmosphere. Significant new carbon-free power generation will be needed to support continued economic development and growth. Nuclear power generation is a vital power generation technology that is part of the solution to reduce carbon emissions. The use of nuclear power generation can only be expected to grow worldwide, as it is the only available technology that can be readily expanded to produce vast amounts of carbon-free base load green energy. Sixty new nuclear generation plants are under construction worldwide with many more in the planning stage. For more information on this, go to
www.world-nuclear.org/info/current-and-future-generation/plans-for-new-reactorsworldwide.
The physical properties of grease can be characterized with a stress rheometer (instrument inset on the right). The correlation shown using new and used grease samples tested with both a 1/4 scale cone penetration and a stress rheometer allows the use of a stress rheometer to measure and characterize grease samples. This is advantageous in that the rheometer requires significantly less grease to obtain measurements.
TLT: Do lubricants have a beneficial role in climate change mitigation?
Johnson: This is an interesting question. Petroleum products, as you know, are carbon based, and their combustion as fuel is a primary source of carbon emissions (
see Turbine Oil: Reliable and Environmentally Friendly). Lubricants, also primarily carbon based, are a highly beneficial usage of petroleum-based products. Their purpose is very different than fuel in that lubricants aren’t burned; rather, their use preserves the asset by reducing friction in operating machinery. Lubricants allow the modern world economy to function. Lubricants get really interesting when considered in terms of a beneficial role in climate change mitigation.
Turbine Oil: Reliable and environmentally friendly
An example of a lubricant condition monitoring activity beneficial to both a company’s bottom line and the environment might be a turbine oil replacement. The operation of modern large frame gas turbines creates a stressful condition for the turbine oil. These systems, ranging in volume from 2,500-8,000 gallons, have a typical life of six to eight years. Doubling the service of oils through improved maintenance and condition monitoring practices can avoid the cost of one or more full oil replacements. For a 6,000-gallon system, this equates to savings in excess of $100,000 for oil replacement and flushing costs.
The extraction, manufacture, transportation, handling and disposal of new turbine oil carries an environmental burden. Each of these steps requires an energy input that produces an associated CO
2 atmospheric emissions release.
For example, an average motor vehicle gets 21.4 miles/gal and drives an average of 11,318 miles per year. A single car’s emission calculates to 4.75 metric tons CO
2 emissions per year. Associating this emission factor to 6,000 gallons of automobile gasoline burned would result in 53.9 metric tons emissions. As both gasoline and turbine oil are carbon based and since oil has a much greater density than gasoline, and the transportation burden to the end-user is more carbon extensive, it is reasonable to expect a higher multiple volume of CO
2 to be released for each 6,000 gallons of lubricant used (
1).
1. Taken from www.epa.gov/energy/ghg-equivalencies-calculator-calculations-and-references#vehicles.
Reducing friction reduces the machine power requirements. Reducing or eliminating the occurrence of wear within the machine allows extended operation and a reduced energy requirement that would otherwise be needed to manufacture replacement parts or a new machine. These external attributes of the lubricant directly reduce the volume/quantity of carbon emissions and greenhouse gases entering the atmosphere. While this is good, we as an industry can do even better.
Lubricants are readily taken for granted by the end-user simply because many choices (including, sadly, many environmentally poor choices) ultimately work. A strong partnership between the end-user customer at the industrial facility or their vehicles and the lubrication professional can beneficially optimize the choice of lubricant. The careful matching of the lubricant viscosity to machine temperature environment results in a lubricant operating with a lower power requirement. The use of a synthetic lubricant can reduce the machine power requirement further.
The best choice in the use of additive chemistry within the lubricant can further reduce the friction and wear. Each of these positive outcomes results in an incremental reduction of the machine power requirement. Reduced power requirements in turn lower the carbon emissions that are produced from the operation of the equipment.
Machinery drives the economies of the world and the applications of additional machinery can only be expected to grow as more industry is introduced into developing economies. Lubrication is a broad global industry. In making or influencing optimal lubricant choices, we as an industry have a tremendous opportunity to measurably reduce pollution and global greenhouse gas emissions. In doing this, we can make a significant difference to the well-being of others.
As a professional in both the nuclear and lubrication industries, I am pleased that I am positioned to make this difference.
Palo Verde generates electricity with the steam cycle. Major elements of the steam cycle include a heat source (the reactor), large pumps to move water through the reactor and toward the steam generator, large heat exchangers (steam generators) that transfer heat to create the steam, the turbine generator assembly and a cooling source to condense the steam that passes through the turbine back to water.
TLT: How can we as the lubrication community help make your job easier?
Johnson: We consider the lubricant to be an integral part of the design and operation of the machine. When the formulation of the lubricant is altered to include minor changes or full product replacement, an evaluation of the new product is performed to determine if it meets the machine design requirements. A name change to the same formulation requires a similar evaluation to demonstrate that the product hasn’t changed.
We rely on the local product suppliers or the manufacturer to inform us that a product change is planned or has occurred. A timely notification allows for a routine product review and associated documentation. Unfortunately these notifications are often missed, an omission that can lead to plant maintenance challenges.
We use bench top testing of incoming product as a back-up to vendor notifications and as part of our receipt inspection process. Formulation changes that we identify at the point of receipt inspection create emergent needs to evaluate the lubricant, and such a discovery can produce scheduling impacts to planned work in the field. The lubricant manufacturer or their representatives can help make my job easier by ensuring that product change notifications to include minor formulation changes are made well in advance of the product change.