20 Minutes With Gary L. Doll
Rachel Fowler, Associate Editor | TLT 20 Minutes May 2016
The Timken professor of surface engineering discusses bearings, surface treatments and the future of coating technologies.
GARY L. DOLL - The Quick File
Gary L. Doll is the Timken professor of surface engineering and the director of the Timken Engineered Surfaces Laboratories at the University of Akron. He holds joint appointments in the civil engineering, mechanical engineering and chemical and biomolecular engineering departments. His current research includes surface engineering of materials to address friction, wear and corrosion; nanocomposite materials; and lubrication strategies for challenging environments. He received his doctorate in condensed matter physics from the University of Kentucky where he studied the optical and structural properties of layered materials. As a postdoctoral fellow in physics at MIT, he conducted research on a wide range of materials including copper oxide superconductors, composites, carbon fibers and polyimides. After MIT he joined the General Motors Research Laboratories where he began his research in thin film coatings, surface engineering and tribology. Later he became the chief technologist of tribology at the Timken Co. where he was responsible for global research and development activities in tribology, lubrication, surface engineering and non-ferrous materials. Doll was elected an ASM Fellow in 2009 for his contributions to the field of surface engineering. He currently serves as chair of the STLE/ASME Wind Energy Tribology Committee and is an assistant editor for Tribology Transactions, STLE’s peer-reviewed journal. He is a member of SVC, STLE, ASME and ASM. Doll has published more than 200 articles and book chapters, edited numerous proceedings and received more than 25 U.S. patents.
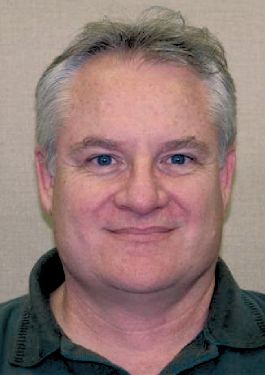
Gary L. Doll
TLT: Early in your career you worked in the automotive industry. What was the key area of research at that time? Tell us about one of the successful applications of surface engineering while you were in this industry.
Doll: I was recruited from MIT by GM Research Laboratories to work in the field of atomically engineered materials, with the specific goal to develop epitaxial diamond layers as thermally conductive buried insulators in CMOS devices. The pathway that I chose to achieve this goal was to first develop an epitaxial cubic boron nitride (cBN) film on silicon that lattice matches with diamond. Although we never completely realized epitaxial cBN, we were able to synthesize films that were extremely wear resistant with very low friction coefficients. This partial success brought our research to the attention of engineers at GM Powertrain that were seeking a solution to increase the load-bearing capacity of a 4T60 planetary gear set so it would function well with a turbocharged engine. My team surveyed the landscape of tribological coatings that could be deposited at temperatures compatible with heat-treated SAE 8620 gear steel and determined that an amorphous boron carbide coating appeared promising. A specific coating recipe was developed in collaboration with a supplier and applied to sun gears for 4-square and back-to-back gear testing. Analysis of the test articles revealed that the ceramic coating on the sun gear effectively polished the mating planetary gears, thereby increasing the lambda ratio (i.e., the ratio of the minimum lubricant film thickness to the composite surface roughness) during operation. The new pitting fatigue life associated with the increased lambda value resulted in a gear set with an increased power density. That is, more power could be transmitted through the gear set without causing a reduction in pitting fatigue life. Based upon a determination of the underlying mechanism for an increased power density in the 4T60 planetary gears, we were able to develop a tungsten-containing diamond-like carbon (W-DLC) coating that was more durable in this specific application than the boron carbide coating. The ability to transform the 4T60 gear set into a 4T65 gear set with the use of a tribological coating on the sun gear resulted in an estimated $200 million-per-year cost savings by eliminating the need to manufacture a specific transmission for turbocharged engine options on a specific platform.
TLT: Later you moved to the bearing industry. Tell us about the research focus at that time.
Doll: In the mid-1990s, GM, Caterpillar and The Timken Co. formed a joint research collaboration in engineered surfaces that was funded by the NIST Advanced Technology Program. One positive outcome of that collaboration was that I was recruited by Timken to develop surface engineering technologies for its rolling element bearing products.
Most rolling element bearings do not fail in applications due to rolling contact fatigue but instead fail from various wear modes. Smearing (or scuffing) is an adhesive wear mode that can occur when the lubricant film in the contact breaks down or vanishes. Abrasive wear and plastic deformation can occur when hard debris particles become entrapped in the contact. Micropitting is a surface-initiated fatigue phenomenon that tends to occur when there exists a negative slide-to-roll ratio occurring in a poorly lubricated contact.
All of these wear modes can be mitigated by surface engineering technologies. The focus of the research at Timken was to develop surface engineering technologies to address the most typical wear modes encountered by rolling element bearings. One of the most pressing issues was to extend the operational life of rotorcraft roller bearings in the event of a catastrophic loss of lubrication. A loss of lubrication in rotorcraft gearboxes specifically endangers the ability of tapered roller bearings to function since adhesive wear between the large roller ends and rib faces can result in galling and the inability of the bearing raceways to rotate. To address this wear mode, we developed a special diamond-like carbon coating that, when applied to the large roller ends, extended the operational life of critical bearing positions that were subjected to a loss of lubrication by almost a factor of five. This technology is now integrated into many rotorcraft gearboxes.
Following the introduction of multi-megawatt wind turbines, it was observed that various wear modes were limiting the lives of main shaft and gearbox bearings to fractions of their designed lifetimes. Whereas spherical roller bearings were experiencing micropitting in gearboxes and mainshaft positions, cylindrical roller bearings suffered from smearing and a rare phenomenon known as white etch cracking. A tribological coating with a microstructure optimized to withstand high stress cycles in rolling contact was applied to spherical and cylindrical rollers and has been very effective at reducing the instances of micropitting wear in wind turbine spherical roller bearings.
A high-temperature, vacuum environment is one of the most challenging environments for bearing operation. In environments like these, fluid-based lubricants cannot always be used. One such environment is that of rotating anode x-ray tubes that are used in medical imaging technology where solid lubricants such as silver or lead are employed instead of fluid-based lubricants. The ball bearings in these tubes usually have the solid lubricant coatings applied to the rolling elements. During operation the coatings migrate from the balls to the raceways and form a layer that separates the metal contact.
However, the coating material does not migrate to the raceways uniformly but in clumps. These clumps or moguls on the raceways generate a small instability in the x-ray beam causing a longer period of time that the patient must remain in the scanner to achieve the desired resolution.
To reduce beam instability, it was important to develop a solid lubricant coating that clings tenaciously to the balls and does not form clumps on the raceways. This was accomplished by creating a four-layer coating architecture where each layer forms strong chemical bonds to the surface beneath it. Specifically the coating consists of a chromium base layer followed sequentially by layers of nickel, copper and then silver. According to a manufacturer of x-ray tubes, this strategy has been effective at reducing bearing vibration and decreases the amount of time the patient spends in the CT scanners.
© Can Stock Photo Inc. / Leaf
TLT: What recent work are you involved in at your laboratory on surface coatings that would be of interest to STLE’s membership? What are the tribological solutions that would come out of this work?
Doll: We have launched a research project this year through the Center for Surface Engineering and Lubrication Research aimed at developing a novel surface treatment process incorporating both ultrasonic nanocrystalline surface modification and cermet-type coatings. The goal of this project is to create surfaces on mechanical components that are more durable than those with DLC-type coatings.
We have continued our research in the tribology of rolling element bearings at the Timken Engineered Surfaces Laboratories (TESL) at the University of Akron. One example of a research project in this area is Lubrication Strategies for Challenging Environments, where we have studied the properties and evaluated the tribological performance of metallic and oxide dopants in MoS
2 coatings in rolling and sliding contacts in environments where fluid-based lubrication is difficult or undesirable.
Through TESL’s affiliation with the National Center for Education and Research in Corrosion and Materials Processing, we are developing surface treatments to replace cadmium plating on aircraft components and to impart H
2S corrosion and erosion resistance to carbon-containing metals.
We have conducted several research projects aimed at improving the wear resistance of titanium alloys with surface treatments. A duplex process involving solution nitriding and a diamond-like carbon coating has proven to be particularly successful at providing wear resistance and has been commercialized by a firearms company.
TLT: Where do you see the future of coating technologies going in the next 10 years? What is the next set of problems you see being solved by engineered surfaces?
Doll: Although electrodeposition has been highly utilized to apply corrosion-resistant coatings, the wear resistance of these coatings does not typically compare favorably to coatings deposited by physical or chemical vapor deposition. However, recent advancements made in electrodeposition may provide an alternative to vacuum deposition processes. For example, we have recently used pulsed reverse current electrodeposition to deposit antimicrobial platinum onto NiTi alloys at a significant cost advantage over sputtering or e-beam deposition. Because pulsed reverse current electrodeposition can be used to tailor the grain sizes of metallic films to the nanoscale and below, this technology can possibly be used to synthesize wear as well as corrosion-resistant coatings.
To reduce weight and improve attributes such as fuel economy, lightweight metal alloys and polymers are being incorporated at an increasing rate into mechanical and biomechanical systems. Components utilizing lightweight materials are expected to achieve high levels of tribological performance that are unattainable without improving the durability of their surfaces. Therefore, surface engineering technologies that can enable components fabricated from lightweight materials to meet required tribological performance demands need to be created.
You can reach Gary L. Doll at gdoll@uakron.edu.