20 Minutes With Wolfgang Braun
Rachel Fowler, Associate Editor | TLT 20 Minutes April 2016
This scientific analyst discusses coatings and bearings.
WOLFGANG BRAUN - The Quick File
Wolfgang Braun is an analyst, advanced bearing analysis, for Schaeffler Technologies AG & Co. KG. He studied physics at the University of Würzburg in Germany from 1992-1998. He was a scientific assistant from 1999-2002 for the department of physical chemistry at the University of Erlangen-Nürnberg where he received his doctorate in natural sciences. Braun was then a scientific officer for the department for functional materials in medicine and dentistry from 2003-2006. Since then he has been in product development at Schaeffler Technologies AG & Co. KG.
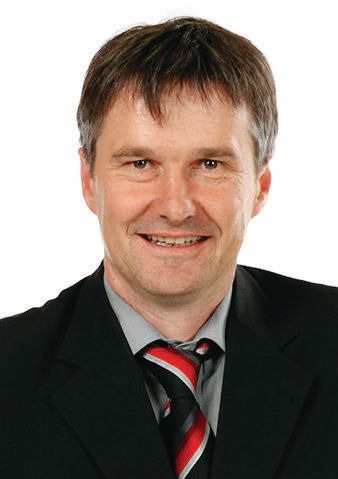
Wolfgang Braun
TLT: Which aspect of your academic education is beneficial for current research?
Braun: The focus during my university time was solid state physics, especially surface science. So from the beginning of my scientific work, I had to deal with surfaces. It was an atomic view. How do physical vapor deposition (PVD) metal layers grow? How are their properties influenced by the substrate in the case of very thin layers? How does this influence the interaction with small molecules? This work is documented in several publications, mainly in Surface Science—a journal devoted to the physics and chemistry of interfaces—and in the doctorate theses with the title Adsorption and Coadsorption of Small Molecules on Transition Metals and Ultra Thin Transition Metal Layers.
I extended my knowledge concerning surfaces and coatings during my work for the department for functional materials in medicine and dentistry. The work was focused on PVD-coated titanium layers as well as calcium phosphates deposited by electro-chemical processes. This work was published amongst others at the European Conference on Biomaterials in 2005 in Sorrento, Italy. Additionally, engineering services were provided concerning corrosion, durability and heat treatment, retrospectively important topics for my later work.
TLT: Was the change from academic to industrial work a great challenge?
Braun: Not at all. For this reason, the lab for functional materials was accredited, and we offered services for external customers. Some of these services also are available at Schaeffler Technologies AG & Co. KG (
see Figure 1). The main change was the step into industrial product development.
Figure 1. Schaeffler Technologies AG & Co. KG company logo.
TLT: What are your main interests and key responsibilities in terms of research and development in your current role in the industry?
Braun: Since I joined the company, one of my main tasks and interests is to look for new technologies and adapt the suitable ones to enhance our products. It is necessary to combine developments from different research areas and to be open-minded to break new ground. My earlier experience in various subjects such as medical technics, surface science, coatings and quite a number of analytical methods from x-ray photoelectron spectroscopy to atomic force microscopy helps a lot.
TLT: What would you describe as the main developments within bearing manufacturing in the last 10 years?
Braun: Coatings and other methods to enhance the properties of acting surface are strongly increasing. Additional improvements concerning manufacturing precisions are made, and new methods for quality inspections are implemented. Since 2005 the focus for bearing improvements was focused more and more on friction reduction. Thus, the interaction of the surface and the lubricant is important. Parallel further developments concerning the models were essential to understanding the mechanism in more detail and in making much better predictions.
One driving force from market view was the strong increase of wind energy. The challenges involved with that, like large bearings and unspecific load situations, have lead to investment in test capacity. Schaeffler acts as cutting edge with our large bearing test rig Astraios.
TLT: What do you think are the challenges within bearing manufacturing in the upcoming years?
Braun: As I mentioned before, challenges include the accuracy for the product and also for the analytic methods increased. So for further development we focus more and more on very specific interaction details, partly depending strongly on the application parameter. We can describe that as a shift from the macroscopic view to a more microscopic or atomic level view. For example, first the geometry played the main role in tribology. Later they focused on the lubricant by adding additives and making further improvements. Up to now, in electrohydrodynamics theory, the gradient of velocity is fully pictured in the oil film. But more often, also due to different coatings, we observe different friction in fully separated surfaces under comparable conditions so that the question of the interaction of the lubricant with the surfaces gets of interest (
see Figure 2). And from here on it gets complex because from the surface site, we have to deal with different material (chemical) properties and also with slightly different roughness. On the other site we have to deal with lubricants. Thereby we often do not know the exact composition, especially when additives are included.
Figure 2. Different friction forces for different surfaces with similar roughness but different chemistry.
We also will see new challenges from the market. Starting in the automotive industry with the upcoming e-mobility and the further reduction of CO
2, the weight of our product is important. There are two possibilities to manage that: new hybrid designs reducing the common metal part to the minimum or high capacity materials with the possibility for downsizing. But besides CO
2, the whole exhaust emission is to be improved further; thereby oil free bearing solution may be asked for in the future.
These media-lubricated or dry-running systems also might play a rising role in other industrial applications like hydropower.
TLT: What knowledge do you think would be necessary to solve the upcoming challenges?
Braun: We need a deeper view of the interaction between surfaces and lubricants. How the bearing surface is finished may affect the performance. It is not sufficient to describe the surface by simple geometric parameters like mean roughness. Also more sophisticated descriptions by values of the Abbott curve will leave a wide scope of different characteristics as soon as chemical properties have to be taken into account. Besides material and coating properties, the manufacturing pathway also can modify the surface chemistry. Due to the process, different strains will remain or the surface will be activated for favored adhesion partners. If we have the knowledge to understand these differences and processes, we can distinguish between the surfaces and are able to create tailor-made surfaces for each application (
see Figure 3).
Figure 3. VG 320 oil works well with coated surfaces but bad with steel surfaces.
TLT: Does that mean that one can think about new manufacturing methods as well?
Braun: In the first step, we still keep the methods we have, but to understand their different impact on our product we need a closer collaboration between the manufacturing units and the product development. This also leads to the opportunity of breaking new ground. The result can be that in some cases, tailor-made products with less or no supplementary cost can be produced. And on the other side, processes leading to the desired surfaces can be realized.
TLT: What role can surface engineering, especially nanocomposite coatings, play in enhancing performance, reliability and durability of bearings in harsh operational conditions?
Braun: If we talk about oil-free solutions, the surface, for example, needs to be protected against corrosion. This can be done with coatings, but then we have more complicated interacting systems. The load leads to a certain compression up to a certain depth in material. The propagation of these compressions over the intermedia layer will be a challenge for the coating adhesion strength, especially if it is highly repetitive.
With nanocomposite coatings, I combine two effects concerning the word nano. First of all,
nano is related to the grain sizes. A very fine grained metal is more robust, the crack propagation is reduced and stress maxima distributes better. Second, some nanoparticle filler, homogeneously distributed, can affect the material properties strongly. Many improvements concerning hardness, wear resistance or electrical conductivity are well known.
With the right composition and technics, a lot of different properties can be adjusted and matched to the application. We still use the knowledge in our “coating tool box” and provide these benefits successfully to our customers. Finally, the interaction to the lubricant can be improved if we know about the necessary mechanism (e.g., the wettability), matched surface energies or best adhesion to special additives.
TLT: As a bearing manufacturer, you can mainly affect the material and the surface, but as you described, the interaction also is necessary to the lubricant, correct?
Braun: Yes, and on to a more atomic view of the process in lubricated contacts, a close collaboration to lubricant suppliers also is necessary. A tailor-made bearing also needs a tailor-made lubricant since we are talking about sophisticated applications.
For the day-to-day business, we can focus on a few lubricants and optimize our products to the best interaction.
You can reach Wolfgang Braun at w.braun@schaeffler.com.