The correct industrial gear oil
R. David Whitby | TLT Worldwide March 2016
Viscosity grade and speed are among the determining factors when making a selection.
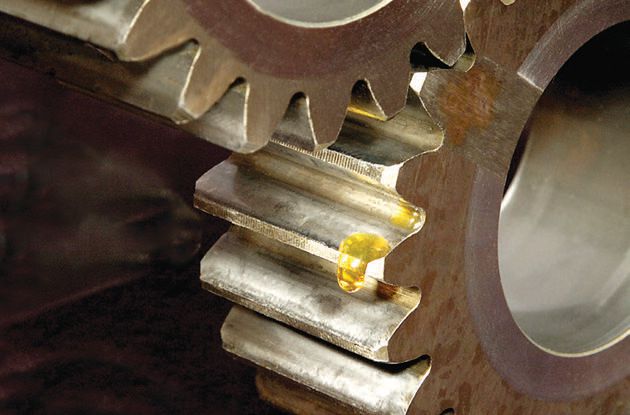
Highly viscous oils generate heat from internal fluid friction and also may consume more power to turn the gears.
© Can Stock Photo Inc. / deryck
INDUSTRIAL GEARS OPERATE IN MANY DIFFERENT ENVIRONMENTS whether indoors or outside. Conditions can be hot, cold, wet, dry, dusty and/or with variable loads. The latest gearboxes often are smaller and made from lighter weight materials, but they can be pushed to transmit more power while also being more durable and reliable. Plant managers expect higher performance, less downtime and more productivity to improve profits.
Smaller gearboxes mean less oil to lubricate and protect gears. Coupled with higher loads, this leads to higher oil temperatures and more rapid oxidation. Oxidation harms industrial gear oils because it can form sludge that can shorten both oil and gear life. Constant gear rolling and sliding also produces friction and heat. In addition, contaminants such as water and dust can compromise a gear system.
Many factors need to be considered when selecting an industrial gear oil.
The appropriate viscosity grade might be found in the equipment maintenance manual. But the manual may not exist or the operating conditions may not be under the manufacturer’s recommendations. A gear oil’s viscosity is primarily chosen to provide a desired film thickness between interacting surfaces at a given speed and load. Because it is difficult to determine the load, this is assumed and the determining factor becomes speed.
One of the most common methods for determining viscosity is the American National Standards Institute (ANSI) and American Gear Manufacturers Association (AGMA) standard ANSI/AGMA 9005-E02. Assumptions are made about the load, viscosity index and the pressure-viscosity coefficient of the lubricant, and these are combined with the type of gear set, gear geometry, operating temperature and the speed of the slow speed gear.
Highly viscous oils generate heat from internal fluid friction and also may consume more power to turn the gears. Less viscous oils can flow more easily through the filtration system. Contaminants are removed effectively, reducing the possibility of gear and bearing damage and increasing equipment life.
Next comes the type of gear oil: rust and oxidation (R&O) inhibited, extreme pressure (EP) or compounded. The gear lubricant type that best fits a given application will be determined by the operating conditions. R&O gear oils generally have good chemical stability, demulsibility, corrosion prevention and foam suppression. They are used in gearboxes operating under relatively high speeds, low loads and with uniform loads but do not perform well or prevent wear under boundary lubrication conditions.
EP gear oils contain additives that enhance their film strength or load-carrying ability by preventing adhesive wear under boundary lubrication conditions. In less severe applications, antiwear additives may be used to provide wear protection under boundary lubrication conditions. Conditions that generally require EP gear oils include heavy loads, slow speeds and shock loads.
In general, a compounded gear oil contains a synthetic fatty acid to increase its lubricity and film strength. They are primarily used in worm gear applications because of sliding contact and the negative effects of EP additives.
High-quality mineral base oils perform well in most gear oils. They typically have higher pressure-viscosity coefficients than common synthetic oils, giving greater film thickness at given operating viscosities. However, many synthetic base oils have greater inherent resistance to oxidation and thermal degradation, making them preferable for applications with high-operating temperatures and/or allowing extended service intervals. Synthetic gear oils can perform better at low ambient temperatures if they have a high viscosity index and low pour point. They may be more suitable for a wider range of ambient temperatures eliminating the need for seasonal oil changes. Some synthetic oils also may offer greater lubricity, which reduces friction in sliding contacts.
Water can creep into a gearbox in several ways, potentially leading to corrosion. Gear oils should have good demulsibility properties so that any water can separate quickly. The ability to rapidly drain water from the system helps extend the life of both the gearbox and the oil.
When choosing a gear oil, ask the supplier if it is approved or recommended by the equipment manufacturer. Also ask for performance information against the international or national specifications. The fluid should be delivered clean and water-free so it will perform at its best. It’s very important to conduct used oil analysis as recommended by the supplier to determine when the oil may need maintenance or replacing.
David Whitby is chief executive of Pathmaster Marketing Ltd. in Surrey, England. You can reach him at pathmaster.marketing@yahoo.co.uk.