When making a recommendation on bearings, how do you balance reliability/durability issues with cost?
TLT Sounding Board March 2016
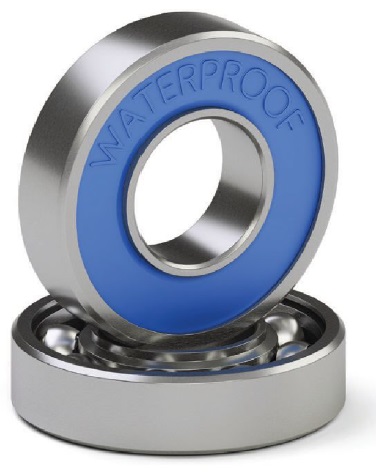
© Can Stock Photo Inc. / maxuser
Reliability is Job No. 1. That is the message advocated by TLT readers answering this month’s question on bearing selection. “Reliability has to be first,” one reader said. “The cost of labor and downtime far outweighs bearing cost.” A recurring theme among survey respondents is to focus on the total cost of ownership. Many readers recommend documenting the cost of quality parts and proper lubrication regimes versus down time and replacement costs and then taking the analysis to decision makers at the operation. “Usually some additional up-front cost pays large dividends through the life of the equipment,” noted one reader. It’s a message that apparently is resonating with end-users. According to survey respondents, only 25% of end-users make a bearing selection based primarily on cost.
The customer, if educated in tribology, can calculate the ROI of investing in a quality bearing but only if they have implemented best practice lubrication reliability programs that ensure the bearing is lubricated by the correct grease, in the correct quantities/interval and that contamination is excluded. Without such a program, even if the bearing is the best in the world, it is highly likely to fail sooner than wanted or anticipated.
I recommend bearing solutions mainly based on reliability. Reliability means for me that lubrication works and lifetime is reasonable—in this order. Only in very extreme cases do I recommend special bearings.
Total cost of ownership.
We always use the OEM-specified bearing.
Reliability and durability are paramount, so we balance by inspecting and testing lower-cost alternatives.
Proper bearing design for load, speed, mounting and operating environment overtakes cost in order to ensure a full bearing life.
In the aviation industry we weigh heavily on the safety of flight.
From an Indian point of view, the durability is much more important than reliability. So here cost plays a vital role. In order to gain confidence on your product, it is very important to prove the durability of the bearing at an effective cost. Reliability is a most important factor for trouble-free running. When it comes to continuous process industries like steel making, reliability is considered above durability. Again, the cost to achieve this matters a lot unless it is a very special product. So depending on the end-user it is very important to take the right balance of reliability and durability issue with the cost.
Customers come to us because we make high-performance synthetic lubricants. We balance things much more toward performance over cost.
It depends on the grade of criticality of the machine to the process.
The key is considering the cost of the total life and function of the bearing (incorporating energy consumption, productivity/downtime, maintenance, lubrication costs, risk of premature failure, expected life) and not just the unit cost of the bearing. Balance is then much easier to achieve.
Reliability is the biggest factor; cost is secondary.
Focus on load capacity balanced with reliability.
Go with the reliability and durability. You can usually show the cost savings of longevity and loss of down time.
Try not to offer a solution where cost cannot justify performance.
I would always prefer recommendations from the OEM whether cost effective or not. I would prefer reliability/durability over cost and would tell the customer as much.
It depends on the level of service and risk of failure.
In my opinion this can only be done with proper selection of the bearing.
Reliability/durability is more important than cost.
If equipment is process critical, cost is not a factor.
Maintenance for higher productivity looks to be the best basis for a recommendation.
Reliability is key in industrial, power plant and commercial vehicle applications.
It depends mostly on the service it will see, but the value of reliability will almost always exceed the cost.
Estimated hours of operation for productivity.
Proper lubrication and maintaining the integrity of the fluid and grease is much cheaper than the failed parts, downtime and lost productivity than the expense of the lubricant or cleanliness procedures. Using reliability-based lubrication calculations to get these costs on paper is very effective in solving problems. I always lean toward reliability/durability over cost.
Cost is secondary. Lubricants are there to do a job and sometimes that comes at a price.
On the typical motor and pillow block bearings, we have done detailed analyses of the largest eight or 10 bearing vendors and found little difference in their quality levels. At times they all have problems, but the proportion is small, especially compared with what North American vendors were producing 40 years ago. On very large bearings—for example more than 400-mm bore—we have seen situations where overseas suppliers have had the bearings in stock for a long time and surface corrosion has occurred. They clean up the corrosion, but the hydrogen damage is still there.
We just focus on performance.
Check for speed and type of heat and usage and product being run.
Stick to what is formally recommended by the OEM. When that is followed, cost issues go out the window.
Historical performance versus life expectations in conjunction with cost.
Production will always dictate quality. Price is not a determining factor.
Use life cycle cost evaluation to make an educated decision and sell the economics to those that approve spending. Usually some additional up-front cost pays large dividends through the life of the equipment.
Cost of maintenance. And down time versus the cost of a premium lubricant.
Reliability and durability far outweigh cost.
For end-users making a selection on bearings, do you feel cost is their No. 1 factor?
Yes
25%
No
75%
Based on responses sent to 13,000 TLT readers.
When developing bearings for a variety of industrial applications, how important are corrosion issues?
Having the best possible grease applied to the bearing in the correct quantities and rates helps ensure that bearing corrosion is not an issue for the end-user.
Not so important. Usually bearing construction IP-classification meets requirements.
Very important. We’ve had bearings that have arrived “pre-rusted.”
Corrosion prevention by the lubricant is critical, especially in marine applications.
Corrosion issues account for about 30% of failures and is dealt with through improved sealing, lubricants or material options.
Many bearings work in environments where water is present or nearby. Without proper seal technologies, corrosion becomes an issue. Bearings need coatings and proper lubricants to prevent corrosion.
Corrosion is a big deal! Per the question, I won’t discuss any marine applications. I’m in the southeast, a very humid environment. There is usually a spot or multiple areas of rust and corrosion on bearing new parts prior to installation. Take care of these new parts. Next, bearings in aggregate plants, paper mills and steel mills are very susceptible to water, dirt ingress and abrasive materials they manufacture. Many users are realizing the importance of cleanliness, utilizing particle count diagnose and breathers to help combat dirt and water ingress. On a smaller scale we’ve helped alleviate $80,000 in losses in productivity annually on one gearbox at a small aggregate company. Imagine the costs of some humongous bearing going down in the states when it’s only made in Europe and replacement is months away.
Corrosion can cause bearings to fail rapidly or not work at all. Corrosion prevention should never be overlooked.
Very important. For example, the food and pharmaceutical industries can process some very corrosive materials and can have aggressive machine-cleaning regimes.
Corrosion is an issue for the bearing shell.
Corrosion is application specific; so it’s not always a criteria but still needs to be addressed when necessary.
Corrosion is a factor, albeit secondary to other factors in most applications.
Corrosion issues definitely apply to marine applications (exposure to saltwater environment). Land-based applications in humid environments also need consideration of corrosion potential.
Customers from various industries stress the importance of bearing corrosion issues when they face problems.
Corrosion is a general concern in process industry such as pulp and paper. Corrosive process fluids can degrade grease, thus affecting re-lube intervals and bearing life.
Very important, especially in steam turbines.
In most of my applications in production lines, corrosion is not the biggest problem.
Corrosion generates hydrogen atoms. Some of those atoms don’t form molecules and, instead, wander through the microstructure looking for a vacancy so they can help create one of the forms of hydrogen damage. With the hardened steels in bearings and their tendency toward hydrogen cracking, my opinion is that even light surface rust is enough to scrap the bearing.
For most applications, corrosion is not a concern unless the equipment is in long-term storage.
Corrosion issues are important in outdoors sea coast environments. We often recommend fluorosilicone greases for these applications.
Design of the bearing should include optimal lubricant exposure so as not to be prone to corrosive attack.
Extremely important. It’s very simple—if it’s not designed appropriately for the service conditions (with environment being one of those), we’re not buying it.
Corrosion issues are very important. Food processors and paper mills should always watch that closely.
What phrase best describes most end-users’ knowledge of bearing selection, maintenance and lubrication?
They pretty much know everything they need.
2%
They’re fairly knowledgeable but need help from a lube engineer.
67%
They’re just barely competent.
21%
They’re floundering.
8%
They’re absolutely clueless.
6%
Based on responses sent to 13,000 TLT readers. Total exceeds 100% because some readers submitted more than one answer.
Editor’s Note: Sounding Board is based on an email survey of 13,000 TLT readers. Views expressed are those of the respondents and do not reflect the opinions of the Society of Tribologists and Lubrication Engineers. STLE does not vouch for the technical accuracy of opinions expressed in Sounding Board, nor does inclusion of a comment represent an endorsement of the technology by STLE.