New welding approach
Dr. Neil Canter, Contributing Editor | TLT Tech Beat February 2016
A new system known as vaporized foil actuator joins dissimilar metals.
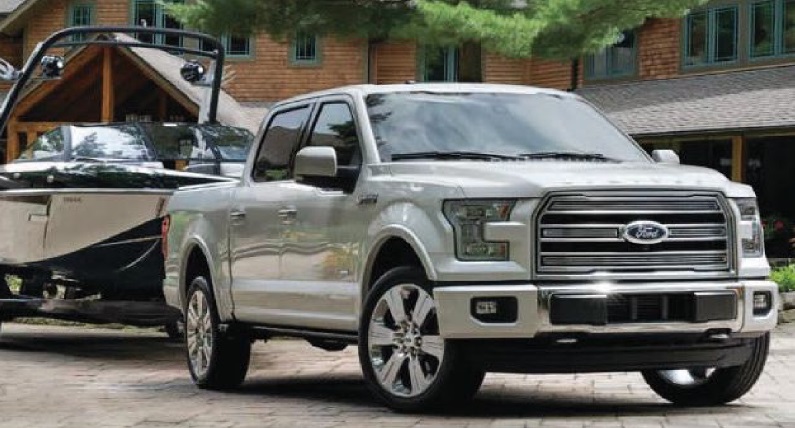
www.ford.com
KEY CONCEPTS
•
The problem with resistance spot welding is the formation of joints that become the weak point of the joined metals.
•
A new process for joining metal known as vaporized foil actuator does not impact the physical properties of the joined metals.
•
Weld strength is dependent upon the types of metal alloys used and the speed at which the two alloys are pushed together.
ONE OF THE CHALLENGES FACED IN MANUFACTURING A COMPLEX PIECE OF MACHINERY such as an automobile is finding the best approach for joining dissimilar metals. This process is becoming more important due to the growing use of lighter-weight, nonferrous metals such as aluminum being used with ferrous alloys in automobile manufacturing.
A significant example is Ford Motor Co.’s replacement of 1,000 lbs. of steel with 600 lbs. of aluminum in its best-selling F-150 pickup truck (
1).
A previous TLT article described a modification of a technique known as cladding that is used to bond one metal alloy (
2). The modification is known as high-energy-density fusion cladding and utilizes a high-density infrared arc lamp to heat the temperature to a point just below the melting point of a metal substrate enabling the second metal alloy to effectively bond to that substrate.
The traditional approach used to join dissimilar metals is resistance spot welding. Glenn Daehn, professor of materials science and engineering at The Ohio State University in Columbus, Ohio, says, “In resistance spot welding, a high electrical current is passed through the two metals that need to be joined. This generates heat that partially melts both metals together, forming a weld.”
Daehn continues, “The main problem with this technique is that the melted portions of metal are never as strong as they were prior to welding. With the continuing introduction of stronger metal alloys, joints have become the weak point. In effect, joints have not become stronger to match the new metals used.”
The result is a decrease in the joint efficiency, which is the ratio of the strength of the joint to the strength of the base material. The goal is to achieve 100% joint efficiency, but this cannot be realized using resistance spot welding. One other problem is the need to generate high currents that require a large amount of costly energy.
Two other methods for joining dissimilar metals are adhesives and fasteners. Adhesives are weaker than metal alloys while fasteners exhibit joint efficiencies less than 100%, add weight and expense and can corrode.
There is need for a new welding approach that can achieve the 100% joint efficiency goal. Such an approach has now been developed.
VAPORIZED FOIL ACTUATOR
Daehn, in collaboration with his colleagues, has developed a new system to join dissimilar metals that is known as vaporized foil actuator (VFA). This system uses a high-voltage capacitor bank to create a short electrical pulse within a thin piece of aluminum foil. After only microseconds, a burst of hot gas is generated by the very rapid vaporization of aluminum pushing two pieces of metal together at very high speeds.
Daehn says, “VFA is a form of impact welding that facilitates the collision of two dissimilar metals at high speeds over a short distance to form a very strong weld without melting the metal. A typical piece of metal will move at a speed of 300-700 meters per second during this process. This is typically the sweet spot for the process.”
VFA differs from other welding techniques in that the physical properties of the metal are little changed, which means that a strong weld should have comparable properties to the base metal alloys used. The researchers have evaluated different combinations of ferrous, aluminum, magnesium, titanium and nickel alloys. Daehn says, “In our experiments, we collide one piece of a metal into a second metal at multiple angles. Then we evaluate the physical properties and welding interface using optical microscopy.”
The strength of the weld is dependent upon the types of metal alloys used and the speed at which they collide. Some alloy pairs weld extremely well and display very distinguished interfaces such as the weld shown in Figure 1—between copper at the top and titanium at the bottom—which shows curls of titanium interacting with the copper.
Figure 1. A microscopic view of the interface formed when copper (at the top) and titanium (at the bottom) are joined together through a new technique known as vaporized foil actuator is shown. (Figure courtesy of The Ohio State University.)
Daehn believes that copper and titanium form the most beautiful interface. In contrast, the interface between aluminum and steel while forming strong welds does not produce distinguishing curls.
Daehn says, “Certain pairs of aluminum and magnesium alloys stick together after VFA but do not exhibit good strength. Our ultimate objective is to push the failure of the welded material into the base metals.”
One area of concern in working with dissimilar metals is the possibility of galvanic corrosion. Daehn says, “We believe that if the metals being welded have corrosion potentials within 150 millivolts of each other, they will not cause problems. One example of an alloy combination that is much further apart than 150 millivolts and may cause problems is ferrous alloys and magnesium.”
The researchers will continue to examine other alloy combinations and work to make the system more robust in the future. Additional information can be found in a recent reference (
3) or by contacting Daehn at
Daehn.1@osu.edu.
REFERENCES
1.
Canter, N. (2014), “Developing metalworking fluids for light metals,” TLT,
70 (3), pp. 46-57.
2.
Canter, N. (2011), “A cost-effective metal-cladding process,” TLT,
67 (12), pp. 10-11.
3.
Liu, B., Vivek, A. and Daehn, G. (2015), “Use of vaporizing foil actuator impact welding of aluminum alloy sheets with steel and magnesium alloys,”
Light Metals 2015, edited by M. Hyland, The Minerals, Metals & Materials Society. DOI: 10.1002/9781119093435, pp. 463-468.
Neil Canter heads his own consulting company, Chemical Solutions, in Willow Grove, Pa. Ideas for Tech Beat items can be sent to him at neilcanter@comcast.net.