20 Minutes With Lynn Massad
Rachel Fowler, Associate Editor | TLT 20 Minutes February 2016
With 25 years of industry experience, this corporate R&D chemist discusses the evolution of quality inspections and technology.
LYNN MASSAD - The Quick File
Lynn Massad is a corporate R&D chemist for Calumet Specialty Products Partners, L.P. She holds a bachelor’s of science degree in chemistry and a master’s of business administration from Louisiana State University in Shreveport, La. Her career in the lubricants industry began in 1990 while employed as a laboratory technician at Specialty Oil Co. in Shreveport.
Since then she has accumulated 25 years of laboratory and quality control experience. Lynn also is an STLE Certified Lubrication Specialist™ (CLS) and Certified Oil Monitoring Analyst I™ (OMA I). She has been a member of the American Chemical Society for more than 25 years.
While earning her chemistry degree, Lynn’s full-time responsibilities at Specialty Oil Co. included analyzing used oil and environmental samples. After graduating she went to work as a chemist for Boots Pharmaceuticals, which was later purchased by BASF. From 1992-2006 she worked in the pharmaceutical industry as a chemist I, chemist II and senior chemist. In 2006 Lynn went to work for TruSouth Oil, LLC as the laboratory and R&D manager. She established the laboratory and developed all products and testing protocols including the TruFuel line of gasoline and oil mixtures. She managed formulations for all lubricant and fuel products. In 2013 TruSouth was purchased by Calumet Specialty Products Partners, L.P., and is now operating as Calumet Packaging, LLC.
In December 2014 she accepted the quality manager position with Lube-Tech for its new facility in Shreveport. She worked to obtain ISO certification, quality systems and establishment of the laboratory. In September 2015 Lynn returned to Calumet as a corporate R&D chemist. She is happy to work in research and development and expand her knowledge base to include the refinery side of the business.
Lynn was born at Elmendorf Air Force Base in Alaska in July 1969. In 1972 her family moved to K.I. Sawyer Air Force Base on Michigan’s Upper Peninsula. In 1980 her father’s transfer took them to Louisiana; she has lived in the Shreveport-Bossier city area since then. In her spare time she enjoys jogging, reading and spending time with her husband, Brad, and two sons, Carson and Barro. She loves giving back to the community by giving presentations to students.
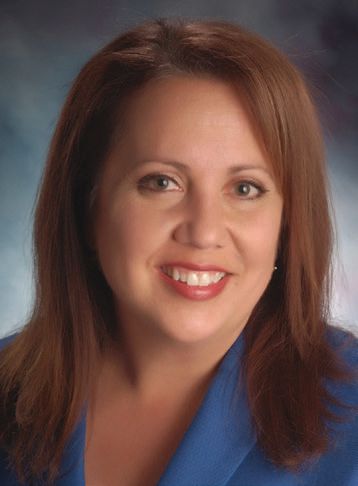
Lynn Massad
TLT: How do you set specifications?
Massad: As a laboratory manager setting the specifications on new products, it is important to have a well-defined procedure for ensuring that the product is inspected and verified at critical points during the entire process as well as a well-defined procedure for setting specifications at each part of the process. As the quality and laboratory manager of blending and packaging facilities, I was responsible for the quality of everything coming into the facility and everything going out. I initiated inspections for all raw materials, blended product and packaged product. Packaged product inspections include everything from the smallest package (2.6 oz.) to the largest package (a rail car).
When setting packaging inspection points it is best to understand the packaging process and consider multiple inspections to cover the length of the process. Approval of the first bottle (beginning) is obviously necessary, but having inspection points like the middle and end need to be defined for package type and length of run. For example, a small run of four 55-gallon drums may only need a beginning and end sample. Longer runs should require more inspections. For example, thousands of quarts need to have beginning, middle and end inspections and start-of-shift if it extended into another shift.
Each inspection point also should have recommended tests for capturing the critical aspects of the fluid. Inspection of raw materials is critical to ensure the fluid integrity, yet it should be quick to prevent demurrage or transportation charges. Inspection of the blend sample typically has the highest number of required tests, verifying that all of the components were added and in the correct ratio. It is critical to have blend procedures that document the correct mixing temperature, the time for mixing and the sampling procedure. It is crucial that the blending department proactively participates in developing the blending and sampling procedure. Bottom line, the sample must be representative of the tank. Inspections of packaged product should be staged based on the stage of the product: a higher number of inspections placed on the beginning sample and fewer on middle and end.
From the beginning of the life cycle of a product, typically the specifications are set as the new product enters into the facility process from R&D. Any chemical or physical specifications required per batch should be defined with the following in mind: industry specifications, supplier specifications, customer specifications and critical fluid identifiers, instrumentation repeatability and reproducibility and the company quality goal. Physical and chemical ranges for licensed motor oils can be found in API 1509 Annex K. Standardized test methods such as ASTM should be used since they are validated and contain the accepted calibration, repeatability and reproducibility requirements.
Some of the trends we are seeing in the licensed motor oil category are increased certifications by OEMs. Specifications on OEM oils need to be understood and accounted for when adding new items. For example, dexos1™ passenger car motor oils (PCMOs) have a 13.0 maximum on ASTM D5800, noack volatility, where API specifications on the same viscosity grades are a 15 maximum. The dexos specification is not only lower, it adds a significant figure.
In cases where there are no industry specifications for elements, have a procedure for setting specs based on other industry standards or requirements. Know your supplier’s min and max. Are they acceptable for achieving the necessary performance of the product? If so, use API 1509 Annex K as a guideline to set ranges -10% (MIN) and +15% (MAX) ranges. If the supplier ranges are not able to meet the desired performance, develop a procedure to adjust the treat rate per batch of material to meet the performance requirements.
On a positive note, many companies want to set their specifications much tighter than typical industry standards. The desire to be better and eliminate any risk is a great strategy unless your process becomes bottlenecked. Here are some variables that should be considered when setting specifications tighter:
•
Process capability. Is your process capable of meeting the tighter specs? If not, know the cost to continually reprocess to meet the spec.
•
Raw material specifications. If your raw material specifications are wider than your final specifications allow, a procedure to change treat per batch of raw material is necessary or your process will halt.
•
Instrument applicability. Using ASTM methods, allow the reproducibility and repeatability to be factored into the specification for expanded range.
•
Annual product reviews. Continue to monitor changes and perform annual product reviews.
•
Market. Does the market need the tighter specifications?
Calumet Specialty Products Partners’ Cotton Valley, Louisiana, facility.
TLT: Do you use PFMEA to set your quality inspections?
Massad: Process Failure Mode Effects Analysis (PFMEA) is a powerful analytical tool, especially when used by cross-functional teams. I’m speaking from my quality and lab manager experience specific to blending and packaging facilities. Engaging members from quality, product management, sales, laboratory, blending, packaging, engineering and R&D is necessary to understand the impact of failure, define and prioritize action items and eliminate and alleviate and minimize risk.
Although PFMEA may not be new to the industry, I was introduced to it in recent years. Learning and understanding this analytical tool was helpful to me as a quality and lab manager by increasing and developing my understanding of the overall process. Being able to step through the entire process with the product and process owners in itself is a team-building opportunity and a great way to communicate. Defining inspection points, tests and risks is imperative to setting up the appropriate system.
The product inspections ensure the integrity of the fluid by testing to the product specifications. PFMEA can help by ensuring the risk of contamination is minimized as well. Using PFMEA to set quality inspection points and verify specifications is recommended to aid with communication for customer specs and identifying and minimizing risk.
TLT: What is the challenge of keeping R&D in touch with operations?
Massad: Communication, communication, communication! Communication is the foundation of successful businesses.
Lynn Massad testing a sample for ASTM D5293. This instrument is a good example of keeping up with updated ASTM methods. The most current update changed the calibration procedure drastically and it helps improve repeatability and reproducibility numbers.
TLT: Which lab staffing and metrics help identify operations?
Massad: I was fortunate to have the opportunity to work directly with the owners at TruSouth Oil, LLC in setting up the laboratory. I was fortunate because they challenged me to prove myself and my results daily. They challenged me to have a lab with consistent, solid and verifiable results. The owner was persistent in making sure that I knew that the integrity of his company and products depended on the integrity of my lab. His persistence in questioning and challenging the lab processes made me better personally and professionally. I grew more professionally because they invested time discussing details with me.
Laboratories are critical to monitoring plant processes and managing product quality. I treated the laboratory as a miniature version of a plant and built key performance indicators for the lab. Metrics are extremely important in identifying and understanding capabilities. As a laboratory manager, I would report these metrics on a monthly basis:
•
Number of samples. Broken down by type, if necessary.
•
Number of hours, shifts, employees and cost.
•
Sample turnaround time versus the expectation.
•
Number of active products and formulations. Details of changes were listed.
•
Number of instruments and down time due to instrument issues. Examples include calibration, repair, preventive maintenance, etc.
•
Results for ASTM interlaboratory round robin (or other round robin). This is my favorite and most important. I always felt as a lab manager it was imperative to measure yourself. Your numbers are only as good as you know they are. Celebrate the successes and actively correct and learn from errors.
•
Results for one to two plant operations that function from the laboratory results. For example, first time pass for blending. Whether or not they met the plant goal, the data is useful for improving, especially when some of the failures are repeated. This is a good opportunity to use the lab data to help improve production processes.
•
Industry report. I would monitor the Petroleum Quality Institute of America (PQIA) weekly and report any of our products that were tested. I also would note any items they were discussing.
These metrics are good discussion points, especially when you need to consider new staff, instruments and/or potential expansion. If your turnaround is not meeting expectations and that older instrument has been down for repairs too many times, these metrics will help support the capital request.
TLT: What was your first role or experience in the lubricants industry?
Massad: From 1990-1992 while I was in undergraduate school obtaining my chemistry degree, I worked for Specialty Oil as a laboratory technician testing used oil and environmental samples. I performed viscosity, inductively coupled plasma (ICP), moisture and polychlorinated biphenyl (PCB) analysis by GC.
TLT: What has been your biggest challenge over the years?
Massad: Two things: keeping pace with the growth of business and being a working mother. I’ve been blessed with supportive colleagues and family that are a team and allow me to balance work and family. As my children become more independent, I look forward to participating in more industry groups and activities. I’ve recently joined Calumet’s research and development team. I’m excited about the opportunity to learn from many of my mentors, and I’m ready to focus on what I love. That is why I chose to come home to Calumet.
TLT: In your view, has industry certification (API) helped the industry? How?
Massad: Industry certification is necessary, but is it enough? Unfortunately in the blending and packaging industry there are a number of uninformed consumers and suppliers providing substandard products. Certifications like the API starburst and donut are a start to standardizing products. For blended lubricants, the API offers certifications for PCMOs, diesel oils and diesel exhaust fluid. The API motor oil matters (MOM) program is intending to provide a place for reporting problems, educating consumers and licensing distributors. Did they wait too long to act on motor oil quality issues? Were they not aggressive enough? Is this working and is this enough? In my opinion this is a good start. However, I believe much more is needed.
Has API struggled to enforce the requirements? I believe that API struggled at developing, implementing and enforcing their monitoring system. This struggle and an uneducated consumer base have left the door open for the entrepreneurial creativity to provide substandard products.
So how do OEMs and consumers who want, at minimum, a standard product ensure they are getting what they pay for? I believe we are about to see a big change in certifications to ensure blended product quality. But this brings up some new concerns. I am concerned with the growing number of OEM certifications and the associated cost of these certifications. The new fees issued for several specifications alone seem excessive. Looking at certifications for PCMO and diesel blended products (API, dexos, Mack, Cummins, Volvo and Detroit Diesel), makes me wonder if ILMA companies will be able to survive in the OEM certification market.
As a formulated motor oil requires balanced components, a balance is needed for certifications to achieve the desired goal.
Lynn Massad’s family. From left to right: Brad, Barro, Carson and Lynn.
TLT: Where is the industry trending?
Massad: I’m thrilled to see our industry trending toward higher quality. A growing number of companies supports PQIA’s efforts to assure the quality and integrity of motor oils in the U.S. PQIA is leading the way to inform consumers by testing and reporting on the quality and integrity of lubricants in the marketplace. They have done an astonishing job on identifying substandard products and protecting and educating consumers. The tactics for substandard products aren’t just for PCMO and diesel. A number of other lubricants don’t have certifications available. I hope PQIA continues its efforts into these other areas.
TLT: How has technology and computing aided your job function?
Massad: I have a passion for new technology at work and at home. Computers have changed the laboratory from data collection and analysis to big improvements in instrumentation. In my 25 years as a chemist I’ve been through four laboratory information management systems (LIMS) implementations. Although it is a struggle getting the information into the system in a usable and structured fashion, it is always beneficial. Having access to data and the ability to manipulate and calculate instantaneously is imperative to keeping on top of processes. Setting an LIMS system up with the laboratory team can develop process understanding and good laboratory practices.
Instrumentation has improved greatly. From chromatography to IRs, we now have smaller, less expensive instruments that have the ability to collect and manipulate data. Accuracy, precision, repeatability and reproducibility improvements can be seen with newer technology as well as faster analysis times and inspection cost savings.
I really enjoy the social aspect of technology. From email and texts to LinkedIn and Facebook, it is very easy to keep in touch with friends, colleagues and businesses. Collaborative efforts are much faster. Information is usually just a few keystrokes away.
My children laugh when I tell them we didn’t have cell phones in school. I wonder what their children will be laughing about in 20 years.
TLT: Has having STLE’s CLS and OMA I certifications benefited your job?
Massad: While I was working at BASF as a chemist I chose to obtain a master’s in business administration to help bridge my gap between chemistry and business. The CLS and OMA I certifications have benefited my job by bridging the gap from chemical and business understanding to application and performance understanding. Understanding the details of the product’s application is imperative to formulating a product for the right application, price and market. I look forward to becoming more involved with STLE.
You can reach Lynn Massad at lynn.massad@calumetspecialty.com.