Foam: Dealing with a persistent problem
Dr. Neil Canter, Contributing Editor | TLT Feature Article December 2015
Experts discuss the challenges in controlling foam in MWFs and other industrial lubricants.
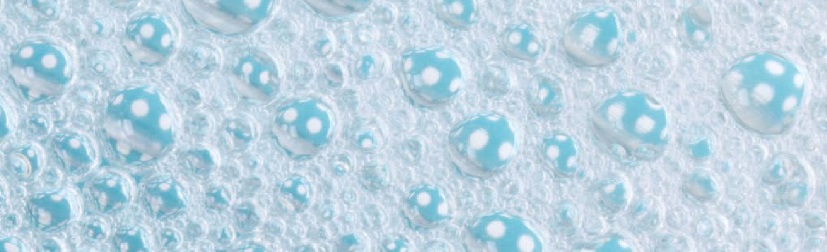
© Can Stock Photo Inc. / FomaA
KEY CONCEPTS
•
Foam can hinder the performance of water-based lubricants such as MWFs and oil-based lubricants such as gear oils and hydraulic fluids.
•
Emulsifiers are a group of additives that can move to the interface between air and water and help stabilize foam.
•
Selection of low-foaming additives is a very important consideration in minimizing foam generation.
IN THINKING INITIALLY ABOUT FOAM, THOUGHT GOES TO PERSONAL CARE APPLICATIONS such as bubble baths and shampoos. Foam does not serve any function other than making the experience of bathing more enjoyable.
But from the lubricant perspective, foam is a major negative in all applications because its appearance means that air, a poor lubricant, is present and hindering the ability of the lubricant to conduct its important functions. In effect, foam prevents the lubricant from being in contact with the metal surface where it is needed. The reoccurring problem of foam generation can be more than a nuisance and can cause major operational problems in lubricant systems.
One of the lubricant applications where foam can be a major factor is metalworking fluids (MWFs) due to the prevalent use of water-based lubricants. But foam can be a problem in other applications such as gear oils and hydraulic fluids. This article mainly discusses the challenges in controlling foam in MWFs but also touches upon the need to control foam in other industrial lubricants.
Insight on how to deal with foam in these applications is provided from interviewing key industry experts who are involved in the development of antifoam additives and emulsifiers (also known as surfactants). The latter is a critical component of widely used emulsifiable and semisynthetic fluids and can be the source of foaming if used improperly. Perspective also is obtained from several MWF formulators on this issue.
The following individuals were contacted:
1.
K. Michael Peck, Air Products and Chemicals, Inc.
2.
Ted Fickert, PMC Crystal
3.
David Bell, Coral Chemical Co.
4.
Dom Ruggeri, DS Additives LLC
5.
Dr. Michael Stapels, Kao Chemicals GmbH
6.
Thomas Wolak, The Lubrizol Corp.
7.
Dr. Ernest Galgoci, The Münzing Group
8.
Robert Austin, QualiChem, Inc.
9.
Dr. Manish Patel, Sasol
10.
Dr. Claude-Emmanuel Hedoire, Solvay Novecare.
FOAM GENERATION CAUSES
STLE-member Dr. Ernest Galgoci, research director-IFL for The Münzing Group in Bloomfield, N.J., indicates that two conditions must be present for foam to be produced. He says, “One condition is a source of the gas bubbles, and the other is a mechanism to retard the bubbles from bursting when within reach of the surface of the liquid. Pure liquids do not maintain foam, as the second condition is not applicable. In MWFs, the main source of the foam bubbles is the incorporation of air into the fluid as a result of the impingement of the fluid onto the tool and part and the vigorous mechanical machining operations that the fluids are designed to enable. The resulting air bubbles are then retarded from bursting through a combination of mechanisms that involve surface-active agents (e.g., surfactants) that stabilize interfacial regions between foam bubbles and their surroundings (i.e., other bubbles and the outside atmosphere).”
Galgoci adds, “For emulsifiable oil and semisynthetic MWFs, the stabilization is caused by the combinations of emulsifiers that are used to produce dispersions of the fluids when they are diluted in water. For synthetics, the water-soluble components can act to some degree as the foam stabilizers. Water hardness plays a role in that systems with harder water have less tendency to foam.”
STLE-member Ted Fickert, director of technology for PMC Crystal in Lansdale, Pa., focuses on operational issues facing MWFs as the chief cause of foam generation. He says, “Increased productivity requirements mean higher speeds that result in higher pressures and fluid feeds. Higher recirculation rates due to small tanks cause less residence time for foam to break. Removal of the active ingredients in antifoam additives through filtration also can lead to foam along with contamination.”
STLE-member Dom Ruggeri, principal for DS Additives in Glenside, Pa., points out three major causes for foam occurring in MWF systems. He says, “The first cause is the fluid formulation itself. Many times a formulator must use high foaming additives to achieve the desired fluid properties. While lab testing can show that the foam is easily controlled, exposure to the stress of the machining operations leads to foam building to the point where it becomes an issue.”
Ruggeri continues, “If the circulating equipment is not maintained properly, pump cavitation will eventually begin to trap air in the fluid. This entrained air will cause foam that is at best difficult to control. System design is a third factor as the MWF must perform regardless of the system configuration.”
STLE-member K. Michael Peck, senior principal research engineer, performance materials for Air Products and Chemicals, Inc., in Allentown, Pa., attributes foam generation to the combination of an air-liquid interface, energy input and a stabilizing surfactant. He says, “Without all three of these factors, foam generation will be minimal; therefore, an important first step in troubleshooting a foam problem is to assess both the process as well as the chemistry of the system. Minimizing mixing of the air-liquid interface and energy applied to the fluid can often eliminate foam generation even with a foamy formulation. Alternatively if a high-energy process is required, addressing the foam stabilization behavior of the formulation itself is necessary to minimize foam generation.”
DIFFERENCE BETWEEN AIR ENTRAINMENT AND FOAM
While formation of bubbles in an MWF is generally classified as foam, air entrainment also is a factor and there is confusion at times about how each of these terms is defined. Ruggeri says, “Foam is a dispersion of air in a liquid on the surface of an MWF, while entrained air represents very small air bubbles dispersed throughout an MWF. As long as the entrained air rises to the surface and agglomerates, it is under control. However, if it remains entrained in the fluid it will cause pump cavitation and generate more entrained air and surface foam until the fluid overflows or the pumps fail.”
Peck focuses on the relationship between air entrainment and foam. He says, “In a system without a stabilizing surfactant, any air mixed into the liquid layer will quickly coalesce into larger bubbles, which rise to the surface and pop. In the presence of a stabilizing material, however, the air bubbles will be inhibited from coalescing, which enables them to linger for a longer time as entrained air. If the rate of air bubble generation is faster than the rate of escape, a system may have significant air entrainment issues leading to process and performance challenges.”
Peck continues, “Foam occurs on the liquid surface and results from the rising and coalescing of air bubbles, which are then inhibited from popping due to the presence of a stabilizing emulsifier. Often, what may be encountered in practice is air entrainment in the high energy parts of the system, particularly at the workpiece, while foam is a problem during recycling of the fluid and in a tank or sump.”
Galgoci also discusses how air entrainment and foam are related. He says, “Usually a distinct phase boundary can be observed between the liquid containing the entrained air bubbles and the foam. If the entrained air bubbles are stabilized, they will eventually become foam as they rise to the surface of the fluid via buoyancy. The amount of foam is related to the rate of generation of the entrained air bubbles and the rate of bubbles bursting at the surface. Obviously if the volume of air being entrained is higher than the volume being expelled through bubble bursting at the surface, then the amount of foam will increase.”
Fickert characterizes air entrainment as small gas particles dispersed in the MWF, while foam represents many gas pockets surrounded by a thin film that floats on the fluid surface. He says, “Air entrainment can happen with high shear from pumping and leaks on the suction side of the pump. Foam is created when fluid is mixed rapidly with free air from the surface or free fall onto the surface of the fluid from recirculation. Entrained air will eventually rise to the surface and also contribute to surface foam.”
STABILIZING FACTORS
Peck feels that the main cause of foam stabilization is the emulsifiers used in the MWF formulation. He says, “Emulsifiers inhibit the escape of air bubbles from the liquid. In a manner similar to blowing bubbles in the backyard, emulsifiers prevent draining of the liquid from the foam lamella around the bubble allowing it to remain stable for an extended period of time. If the dissipation rate of the foam is slower than the rate of air bubble generation, a system will develop a foam problem that can often get out of hand.”
Fickert attributes foam generation to fluid temperature, deactivation of the antifoam and poor chemical control of the fluid. He says, “Nonionic emulsifiers exhibit inverse solubility in water, which means that their solubility in water declines as the temperature of the fluid increases. At a specific temperature known as the cloud point, the MWF will become turbid due to the surfactant coming out of the fluid. The result is that the ability of the emulsifier to contribute to foam generation declines.”
Fickert continues, “Particle type defoamers become emulsified in a relatively short time from pump shear and become inactive, requiring regular additions to the system. The inactivated particles will tend to settle and be filtered out. Poor chemical control of the MWF in not making sure that parameters such as alkalinity and concentration remain within the guidelines of the MWF formulator also can contribute to foam stabilization.”
CONTAMINATION
All of the respondents agree that contamination of the MWF can contribute to foam formation. Galgoci says, “Contamination is not necessarily a major cause of foam in these systems since the necessary ingredients for foam stabilization are already there. However, contaminants such as fine particulates and tramp oil have been implicated in increased foam tendency. Since these contaminants build up as the fluid ages, it may be hard to separate their effects on foam from that of loss of defoamer persistence and/or defoamer depletion. Over time, oxidation and degradation of the base organic components of the fluid can also increase foam tendency. Microbial contamination can be another source of foam stabilization, which is presumably due to the proteins and lipid emulsifiers produced by microbes.”
Fickert stresses the role of microbial contamination in causing foam production to increase. He says, “Contaminants will promote microbial growth leading to fluid degradation and promoting foam.”
Ruggeri provides more insight into how microbial contamination can cause foam. He says, “Many of the additives used in MWF formulations are low foamers. Consumption of these additives by microbes can only lead to an increase and a stabilization of foam.”
Ruggeri and Peck are in agreement that outside contaminant sources such as floor cleaners are a major foam source. Ruggeri says, “Many of these cleaners have a high concentration of foam generating emulsifiers and exhibit a very high alkalinity that can and will break down silicone type defoamers rendering them at best ineffective.” Peck adds, “Many cleaners are often formulated with powerful foaming emulsifiers due to the aesthetic appeal of foam in cleaning.”
ANTIFOAMS VERSUS DEFOAMERS
The terms antifoam and defoamer are often used interchangeably, but they do not have the same meaning. Ruggeri says, “Antifoams are designed not only to break foam but to prevent it from building once again. These materials need to be replenished to remain effective. Defoamers are designed to break foam quickly and efficiently, but they are not designed for longevity.”
Fickert says, “Antifoams may contain both particle- and silicone-type compounds to prevent foam buildup by causing it to break at a constant rate to prevent significant buildup. Defoamers are particle-type products that disrupt the bubble and break the foam.”
Galgoci draws a distinction between when an antifoam and a defoamer are used. He says, “An antifoam is added directly to the formulation and has the objective of suppressing foam as it forms. Defoamers are added during MWF use to break any undesired foam buildup and to provide a period of foam suppression before additional defoamers may be necessary. Both are designed to disrupt the interfacial forces that stabilize the foam bubbles.”
COMPOSITION
All of the respondents were in agreement that the composition of a defoamer formulation consists of a carrier, an active ingredient designed to eliminate foam and a surfactant package. Fickert says, “The carrier is a base stock such as water, mineral oil or synthetic base stocks such as polyethylene glycols, polypropylene glycols or polyalkylene glycols. Selection of the carrier is based on whether the application is a dispersion process, quench process, emulsion or combination of several of these applications. The active ingredient is a particle or hydrophobic compound such as silica, paraffin or synthetic waxes, bisamide, polyethylene, metallic stearate or dimethyl siloxanes. Surfactants used include esters, alcohols and ether sulfonates.”
Ruggeri agrees and states that a surfactant package is used to enhance the dispensability of the defoamer or to lower the foam. He adds, “An antimicrobial pesticide is used as an in-can preservative package.”
Galgoci provides further detail on the role of the various components in the defoamer formulation. He says, “The primary liquids used as the active ingredient are generally mineral and silicone oils that usually contain hydrophobic particles (e.g., modified silicas or waxes) that synergistically improve defoaming performance. The surfactant facilitates the dispersal of the droplet/particles in the medium and thereby enables the formation of an optimal droplet/particle size distribution that is required for the most effective and long-lasting defoaming. The other components may include a carrier liquid that serves to reduce the viscosity of the formulation and sometimes to further enhance defoaming, compatibility and dispersion.”
ANTIFOAM/DEFOAMER SELECTION
Peck indicates that selection of the antifoam is dependent upon the fluid formulation and application. He says, “Testing and evaluation of an antifoam candidate must be representative of the final end-use conditions. Traditional antifoams based on oils and siloxanes strike a fine balance of incompatibility. Therefore, changing conditions may either cause compatibilization and reduction of efficacy or result in separation of the antifoam chemistry. Molecular antifoams avoid this balance by working within their solubility limit, but the shear forces and foam generation tendency may overwhelm their efficacy and result in false negatives in screening.”
Galgoci states that the first steps in selection are to establish performance and cost-in-use targets and to determine if there is any chemistry or regulatory restrictions (e.g., country registrations such as TSCA and REACH). He says, “Unfortunately, the optimal choice of the antifoam is often best determined empirically since the variations between fluid formulations and the specific performance requirements produce a complexity that makes the choice difficult to predict. Commonly this requires testing of numerous antifoams with different chemistries at various treat levels. However, experimental knowledge and first principles can be used as guidelines to organize more efficiently the search for an antifoam.”
Ruggeri recommends that the MWF formulator ask the following three questions before making a selection:
1.
Does the antifoam/defoamer disperse easily and remain dispersed in the fluid for at least 30 days?
2.
Does the antifoam/defoamer give the level of foam control desired?
3.
Does the foam control last for at least 30 days at freezing, refrigerator temperatures, room temperature and at 50 C (122 F)?
Fickert stresses that the antifoam/defoamers supplier is a good source for making recommendations. He says, “The supplier can provide assistance to the formulator based on the fluid type and the application. Most suppliers also will screen candidates based on agreed upon test methods.”
FOAM TENDENCIES OF MWF TYPES
The three water-based MWFs—emulsifiable oils, semisynthetic fluids and synthetic fluids—differ in formulation composition and as a consequence in their ability to generate foam. As Galgoci points out, there is a wide variety of formulations for all of these types, so foam tendency varies widely within a given type of fluid. He says, “In general, foam tendency tends to be in the following order: semisynthetic > emulsifiable oil > synthetic. From a compatibility standpoint, the amount of water has a strong influence on the choice of antifoam used. In general, compatibility is better in the following order: emulsifiable oil > semisynthetic > synthetic.”
Fickert comments on each of the MWF types. He says, “With emulsifiable oils, it is generally easy to disperse an antifoam/defoamer in this product type and to have it be stable. However, there is a direct relationship between the stability of the emulsion and the tendency of the fluid to foam. Sodium petroleum sulfonate, nonionic surfactants and fatty acid salts of amines are emulsifiers used in emulsifiable oils that will all contribute to the foam.”
The type of semisynthetic is a factor in whether the fluid will foam. Fickert says, “Low-oil semisynthetics generally have a higher foaming tendency than the high oil semisynthetics. Generally it is easier to disperse and stabilize antifoams/defoamers in the high oil types. Additives used in semisynthetics that contribute to foam include alkanolamides, chelating agents and phosphate esters.”
For those synthetics formulated with synthetic base stocks such as polyalphaolefins and PAGs, foam also can be a problem. Fickert adds, “In general the higher water content in synthetics makes it more difficult to disperse and stabilize antifoams/defoamers.”
Ruggeri believes that emulsifiable oils display the lowest foam levels as long as the additives and emulsifiers are balanced properly. He says, “Considering that emulsifiable oils range from heavy duty to light duty, balancing the additives is not always easy. However, foaming tendencies are lower for emulsifiable oils because they exhibit a larger emulsion particle size. The additive package will have a huge impact on foaming properties.”
Semisynthetics represent a greater selection challenge because they are present as microemulsions and require higher levels and more types of emulsifiers, according to Ruggeri. He adds, “In semisynthetics entrained air may be a bigger problem than surface foam. An antifoam for this fluid type must contain an additive to release entrained air and the hydrophilic-lipophilic (HLB) balance should be more hydrophilic. But a formulator needs to be very cautious because an antifoam that is too hydrophilic will drop out, and an antifoam that is too hydrophobic will float on the surface. In both cases the antifoam is rendered useless.”
For synthetics, Ruggeri considers those formulated with a synthetic base stock to be treated in a similar manner to an emulsified oil. The major type of synthetic is a water solution, which has different antifoam requirements. Ruggeri says, “To control foam, the antifoam needs to be more hydrophilic with an HLB of eight or greater in order to be compatible with the formulation. Otherwise, the antifoam will have a tendency to split and float on the fluid surface.”
TESTING
Galgoci says, “Testing of antifoams/defoamers in aqueous systems varies widely. Test methods include shaking, mixing, recirculation and air sparging. No one test is a standard. Often a first screening test would be a shake test because they are quick to perform. Blender tests also are used. Recirculation tests usually provide the best correlation with field performance.”
Figure 1 illustrates the effect of a defoamer on the foam tendency of a semisynthetic fluid in a recirculation test, where the fluid is circulated from the bottom of the cylinder and reintroduced into the cylinder as a stream from the top. The first cylinder from the left shows the fluid without defoamer (the cylinder is filled with foam). Each fluid in the other three cylinders contains a different defoamer, which clearly reduces the amount of foam generated. The best performance is seen with the defoamer used in the third cylinder from the left.
Figure 1. A recirculation test is used to evaluate three defoamers in a semisynthetic fluid. The first cylinder on the left is a control run without defoamer while the best performance is seen in the third cylinder from the left. (Figure courtesy of The Münzing Group.)
A further example of a recirculation test done with using four defoamers in an emulsifiable oil is shown in Figure 2. The treat rate for the defoamers and the data obtained are shown in Table 1. Initially four diluted samples of the emulsifiable oil each containing a different defoamer were aged for 28 days at room temperature and then recirculated for four hours. The total foam volume after the recirculation was stopped for five minutes and is reported in the far right column of the table. Total foam volumes were reported at the one-hour, two-hour and four-hour time frames.
Figure 2. Data showing the testing of four defoamers in an emulsifiable oil over a four-hour period is compared to a control containing no defoamer (see Table 1). (Figure courtesy of The Münzing Group.)
Table 1. The defoamer treat rates and the foam volumes seen in testing of an emulsifiable oil over time are shown. The graphical results are found in Figure 2. (Table courtesy of The Münzing Group.)
Ruggeri considers the industry standard test to be the blender test. He says, “But the preferred test in my view is the recirculation test. The problem with the blenders test is that it is not the best indicator of antifoam/defoamer performance because the blades of the defoamer can mechanically render this additive ineffective.”
Fickert maintains that a number of different tests are needed to assess performance. He says, “The first thing that should be looked at is the stability of the antifoam/defoamer in its container. Compatibility with the fluid should be looked at to see if the antifoam/defoamer will remain dispersed, float to the top or drop to the bottom of the fluid. Aging tests at high and low temperatures are useful in determining stability.”
Fickert continues, “Performance tests including ease of incorporation into the MWF and whether the antifoam/defoamer taken out by filtration should be conducted. Shake, blender and recirculation tests should be done depending upon which one best simulates the application.”
EMULSIFIERS
Emulsifiers are one of the main sources of foam generation from an additive standpoint in water-based MWFs. Guidance has been requested from emulsifier suppliers about how MWF formulators can minimize the potential for these additives to cause foam problems.
The first question raised with the industry experts is how emulsifiers contribute to the generation of foam. STLE-member Thomas Wolak, global commercial manager-metalworking for The Lubrizol Corp. in Wickliffe, Ohio, says, “Foam is a network of elastic liquid films separating regions of air. In terms of a metalworking operation, foam is produced when air is mechanically introduced beneath the surface of a coolant that expands to enclose the air with a film of liquid. Emulsifiers, being present in water-based coolants, are by definition surface active. This means they can stabilize gas-liquid interfaces such as entrained air bubbles, thereby enhancing foam stability and persistence when it occurs.”
STLE-member Dr. Claude-Emmanuel Hedoire, customer support manager for Solvay Novecare in Aubervilliers, France, says, “Emulsifiers are surface-active ingredients that move to the interface between oil and water, lower the surface tension and stabilize the resulting emulsion. In addition, emulsifiers also move to the interface between air and water that results in lowering its surface tension and stabilizes the foam generated by the spraying and recirculation of the MWF.”
STLE-member Dr. Michael Stapels, technical manager for Kao Chemicals GmbH in Emmerich, Germany, says, “While emulsifiers have the main function of stabilizing the oil-water interface to prevent their separation into two layers, they also show affinity to adsorb (stabilize) the water-air interface—and this means foam. A certain foamability is the inevitable consequence of the bipolar (hydrophilic-hydrophobic) structure of an emulsifier molecule that is responsible for its surface activity.”
Peck says, “Most common emulsifiers will stabilize foam. Balancing the necessary emulsification against the unwanted foam depends upon both emulsifier selection as well as proper formulation.”
PREDICTING FOAM
No systematic technique is available to predict whether a specific emulsifier will generate foam. Stapels says, “A simplified approach is to evaluate the surface tension reduction and critical micelle concentration of a specific emulsifier. If a specific emulsifier achieves a low-surface tension at a low treat rate, then it will be easier for the emulsifier to generate longer-lasting foam. Only surfactants at the interface lower the surface tension—surfactants in the bulk are inactive in this regard—accordingly, a low critical micelle concentration is required for high foaming.”
Stapels points out that other factors are important in predicting foam and believes that foamability and foam stability can be related to interfacial parameters such as dynamic surface tension. A good summary about the knowledge base for determining whether specific emulsifiers can foam is found in Chemistry and Technology of Surfactants, edited by Richard Farn (
1), and Surfactants and Polymers in Aqueous Solution, edited by Krister Holmberg, Bo Jönsson, Bengt Kronberg and Björn Lindman (
2).
Hedoire feels that predicting which emulsifiers stabilize three-dimensional foam is determined more from experience. He says, “Formulators have an empirical toolbox of low-foam emulsifiers. Four types (nonionic, anionic, cationic and amphoterics) are available for use, but in actuality only nonionics and anionics are used. Nonionics based on short chain hydrophobes such as lauryl alcohol are considered to be high foamers, while those with longer chain hydrophobes such as cetyl and oleyl alcohols are considered as low foamers and widely used in MWF formulations. Anionics can form soaps in hard water that will enhance defoaming but have other negative characteristics that can reduce their use.”
Figure 3 shows how paraffinic oil emulsions of different emulsifier types exhibit foam and emulsion stability in deionized (DI) water and hard water. The data shows that the type of hydrophobe is not only an important factor but the degree of ethoxylation (EO) and propoxylation (PO) present also can play an important role in determining if an emulsifier will generate foam.
Figure 3. The degree of ethoxylation and propoxylation can affect the foam and emulsion stability of an emulsifier in deionized water and hard water. (Figure courtesy of Solvay Novecare.)
Peck indicates that an emulsifier should be initially evaluated prior to incorporation in a formulation. He says, “A good first analysis of any emulsifier is the degree to which it stabilizes foam in water alone. Both foam height and residence time indicate an emulsifier’s foam stabilization tendencies and are good initial parameters to assess early in the selection of an emulsifier.”
STLE-member Dr. Manish Patel, research scientist for Sasol in Westlake, La., states that HLB is a good parameter that can predict whether an emulsifier will foam. He says, “As the HLB value of an emulsifier increases, the percentage of polar groups also increase relative to hydrophobic groups leading to the probability that the emulsifier will foam. The structure of the hydrophobe also is a factor with branching leading to lower foaming emulsifiers as compared to straight chains.”
Wolak considers the operating conditions of the MWF (temperature, pressure, water quality and contaminants) and the inherent relationship between foam and bulk viscosity of the fluid as factors that must be assessed in determining the foaming tendency of a specific emulsifier. He says, “The molecular features of the emulsifier are important in determining foaming behavior. In general, charged or ionic head groups tend to provide greater foam generation versus nonionic structures. With anionic emulsifiers, hydrophilic groups containing smaller counter-ions also tend to promote foam generation and stability versus larger counter-ions.”
DESIGNING LOW-FOAMING EMULSIFIERS
To design low-foaming emulsifiers, according to Wolak, “One must create molecular structures that reduce foam stability. In particular this involves disrupting the emulsifier packing efficiency at the air-liquid interface. This can be accomplished through a variety of ways. First, one can introduce asymmetries in the molecule, including the use of multiple hydrophobic groups or the selection of branched hydrophobic groups. Second, it also has been our experience that introducing multiple hydrophilic groups or moving the hydrophilic group to a more centralized position leads to strain and curvature of the hydrophobic part of the foam network. This also results in reduced foam stability. Third, increasing the cross-sectional molecular area of the hydrophilic group provides a similar goal of disrupting surfactant packing and leads to lower emulsifier concentrations at the air-liquid interface.”
Wolak continues, “Another approach, though not in designing surfactants, is proper application. The MWF formulator can minimize total emulsifier loading in a given formulation by utilizing highly efficient emulsifier types or synergistic combinations. Generally a lower emulsifier treat rate will result in less foam generation.”
Hedoire focuses on the use of two functionalities that can lead to emulsifiers that generate little to low foam. He says, “End-capping of molecules with heavier groups and the use of propylene oxide in the hydrophilic section of the emulsifier are options. Many end-capped emulsifiers or ethoxylated/propoxylated surfactants are used in cleaning formulations because they function as low-foaming wetting agents and detergents, but they are poor emulsifiers. The challenge is to design emulsifiers with these characteristics that also exhibit excellent emulsion stability.”
Stapels believes that development of an emulsifier that does not foam is not possible because the component will exhibit low-surface activity since it has little effect in reducing surface tension. He then organizes the emulsifiers currently available into three categories and evaluates them for their positive and negative characteristics as shown in Table 2.
Table 2. The emulsifiers currently used are organized into three categories that are evaluated for their positive and negative characteristics. (Table courtesy of Kao Chemicals GmbH.)
He says, “Ultra-low foaming surfactants are limited in use because of poor emulsification. Examples include fatty alcohol alkoxylates and end-capped fatty alcohol ethoxylates. With classic surfactants, emulsification can be achieved, but foam control is more difficult. One approach is to include fatty acids in formulations used in hard water. The resulting soaps formed from hard water minerals (such as calcium) can have a defoaming effect. A potential compromise between low foaming and emulsification can be found with propylene oxide, ethylene oxide (POEO) emulsifiers.”
An example of a study done with evaluating POEO emulsifiers in a commercial MWF formulation is shown in Figure 4, which depicts how the fluids look after 15 seconds of foaming and 15 seconds of foam collapse. Four versions of the formulation are prepared that contain POEO and oleyl emulsifiers. Anionic and nonionic versions of POEO and oleyl emulsifiers are used in this study as shown in Table 3.
Figure 4. Anionic and nonionic versions of POEO and oleyl are evaluated in a commercial formulation at the treat rates shown in Table 3. (Figure courtesy of Kao Chemicals GmbH.)
Table 3. The anionic and nonionic emulsifiers used in the study displayed in Figure 5. (Table courtesy of Kao Chemicals GmbH.)
Using a foam-testing device known as the
Dynamic Foam Analyzer from Krüss GmbH, foam heights for all four fluids after 15 seconds of air passing through each sample to generate foam followed by a foam collapse period of 30 seconds are shown in Figure 5. The use of POEO anionic and nonionic emulsifiers displays the lowest foaming results.
Figure 5. A dynamic foam analyzer is used to measure the foam heights for the four versions of a formulation shown in Table 3. (Figure courtesy of Kao Chemicals GmbH.)
Patel feels that a co-emulsifier can help reduce the ability of an MWF formulation to generate foam. He says, “Fatty alcohol ether carboxylic acids are anionic co-emulsifiers that can be tailored to produce low-foaming grades by varying the alcoholic hydrophobe and the degree of alkoxylation. Once neutralized with alkanolamines or alkali metal hydroxides, these co-emulsifiers can provide excellent hard water tolerance and lime soap dispersing properties while also providing corrosion protection and lubricity benefits in addition to suppressing foam.”
TESTING
Most of the respondents indicate that the best approach for evaluating the foaming tendency of an MWF formulation is to use a recirculation test similar to CNOMO D65512 or a lab foam simulator where foam is generated by mechanical means for a specific period of time. Other tests that are available include the simple shake foam test (IP 580, Part C), the aeration test (ASTM D892), the blender test, the bottle test and the cascade test/Ross-Miles foam test (ASTM D1173).
Stapels distinguishes between testing specific emulsifiers and testing the emulsifiers in an MWF formulation. He says, “The best test for evaluating a single component is the Ross-Miles procedure. The main drawback in looking at a single component is the influence of its water solubility. Every surfactant with limited water solubility will show less foamability.”
Wolak points out that a bubble-pressure tensiometer can be used to measure dynamic surface tension; this is heavily influenced by the presence of surfactants. He says, “An air bubble is created via a capillary in the liquid being measured. The pressure required is monitored to the point at which the bubble breaks away from the capillary opening. This method can indicate a given MWF’s ability to generate foam. In general, lower dynamic surface tension results in greater foam generation.”
An example of a lab foam simulation test is shown in Figure 6. Wolak says, “Our in-house procedure uses a recirculating pump to measure the mechanical foam buildup for a given MWF for a set period of time. Afterward the circulation is stopped and foam decay is measured over time.”
Figure 6. Results seen from the evaluation of a tripod nonionic emulsifier compared to a traditional linear nonionic emulsifier in a lab foam simulation test are shown. The samples are evaluated for foam buildup followed by foam decay over time. (Figure courtesy of The Lubrizol Corp.)
Figure 6 shows the foam simulation test results of a water-based MWF containing a tripod nonionic emulsifier versus a fluid containing a traditional, linear nonionic emulsifier.
Testing comparing two alkyl polyglycol ethers of differing HLB values versus two-mole and five-mole oleyl alcohol ethoxylates through the use of the turbine stirring test (DIN EN 13996) is shown in Figure 7. Patel says, “Each sample is subjected to a turbine stirrer for five minutes at 20 C. The resulting foam and liquid is then poured into a cylinder and the foam volume is measured periodically over a 15-minute period. Alkyl polyglycol ethers work better as emulsifiers compared to oleyl alcohol ethoxylates and provide better lubricity, lower foam and better hard water stability as compared to oleyl alcohol ethoxylates and nonylphenol ethoxylates.”
Figure 7. Results from a turbine stirring test comparing two alkyl polyglycol ethers of differing HLB values versus two oleyl alcohol ethoxylates are shown. (Figure courtesy of Sasol.)
FORMULATOR PERSPECTIVE
STLE-member Robert Austin, senior technical support chemist for QualiChem, Inc., in Salem, Va., comments on the reasons foam is a concern for MWFs. He says, “Foam defeats two of the primary functions of the MWFs, which are cooling and lubricating. Air is an insulator that does not transfer heat from that part and tool as effectively as water. If air in any form (surface foam or entrained air) is present, then the cooling capacity of the MWF is reduced. Air also reduces the ability of the MWF to lubricate and flush chips.”
STLE-member David Bell, manager of lubricant technologies for Coral Chemical Co. in Zion, Ill., points out several problems that can occur when foam is present. He says, “Foam in the sump can cause cavitation of pumps, thus reducing the amount of MWF to lubricate during the machining operation. Foam that overflows the MWF sump can cause a dangerous work area, making the floors slippery and unsightly. If left unattended, the MWF will puddle, thus being available for bacterial growth around the machines.”
Besides housekeeping problems, Austin points out that foam can cause flotation of chips and fines that can lead to the formation of residues on internal machine surfaces and pump wear due to cavitation. He adds, “Foam also causes compression of the fluid during high-pressure applications, which reduces the efficiency and productivity of utilizing high-pressure MWFs.”
Bell says, “Other problems created by foam include interference with workers’ view of the workpiece that possibly affects machining accuracy and high loss of MWF from the sump.”
There are a number of factors in an MWF system that can cause foam to be generated. Austin says, “Among the reasons for foam are a higher-than-recommended MWF concentration, the use of extremely soft water to dilute the MWFs, mechanical issues such as plugged strainers on the suction side of pumps and cascading MWF (in the manner of a waterfall), high-pressure coolant delivery systems and depletion of foam inhibitor additives.”
Bell points out that the use of foam-generating ingredients in the MWF formulation leads to the formation of foam. He says, “Fluids with a high degree of surface-active agents tend to foam at a higher level.” Another cause cited by Bell is that insufficient sump capacity does not allow MWF systems with high agitation to dissipate foam effectively.
Austin believes that to reduce foam, MWF concentrations must be kept in the range recommended by the supplier, and extremely soft water must not be used. He says, “A good working relationship with engineers and operating personnel responsible for managing and operating machine tools is required to effectively deal with mechanical issues.”
Bell says, “Mechanical causes for foam generation can be reduced by removing any piping with sharp angles and sizing the MWF system appropriately for the machining operations being performed.”
When asked about the performance of the currently used antifoam/defoamers, Austin says, “Performance improvements are needed in the areas of better compatibility with the MWF, better longevity in the working solution and lower cost. The goal is for the antifoams to remain in suspension in an MWF for an indefinite time frame. The longevity issue mainly has to do with antifoam/defoamers not being removed by MWF filtration systems after multiple passes.”
Bell believes that the demands MWF formulators place on antifoam/defoamers is very challenging. He says, “We ask antifoams to be soluble in our fluids but then rise to the surface to reduce foam. The best approach that a formulator should take is to select low-foaming ingredients in the first place and then add an antifoam to provide a level of insurance against foam.”
The growing use of high-speed, high-feed machining is making it more challenging to keep foam levels low in MWF systems. Formulators will continue to rely on the use of antifoam/defoamers to deal with this issue but will also look to work with components that generate little foam in their formulations. One specific additive area where there will be continuing demand for new technologies is emulsifiers that perform their important role yet do not contribute to foam.
FOAM ISSUES WITH GEAR OILS AND HYDRAULIC FLUIDS
Foam also can occur in mineral oil or synthetic-based gear oils and hydraulic fluids that are not formulated with or diluted with water. Galgoci maintains that the same conditions that generate foam in MWFs also can cause foam to occur in these nonaqueous lubricants.
He says, “Foam stabilization is usually the result of additives such as detergents, dispersants, corrosion inhibitors and antioxidants. Most likely it is the combination of these additives that stabilizes the foam and not necessarily any one individually. Another factor is the fluid’s relatively high viscosities that, according to Stoke’s Law, will retard entrained air bubbles from rising to the surface. Thus, entrained air can be a major source of gas in these fluids. Base oil also can be a contributing factor, though due to a higher purity, will foam less because pure liquids cannot stabilize foam.”
Galgoci indicates that contamination is a major contributor of foam in gear oils and hydraulic fluids. He says, “Three of the contaminants that are culprits are water, degradation (e.g., oxidation) of the oil and the presence of fine particulates (e.g., outside contamination or degradation products).”
Changes in the maintenance interval also can have an impact on the generation of foam. Galgoci says, “If the maintenance interval is increased, a buildup of contaminants will occur, and that will lead to increased foam/air entrainment and other undesired effects. Also, the antifoam may be depleted over time by adsorption onto surfaces (contaminants, particles, fines, etc.) or through filtration, and thus the foam tendency will increase.”
Antifoam selection needs to be done empirically due to the different types of oils commercially available and the specific performance requirements of application. Galgoci says, “Formulators and end-users need to be advised that the choice of antifoam chemistry is mostly limited to silicones, polyacrylates and combinations thereof.”
In evaluating the foaming tendency of non-aqueous lubricant systems, the air sparge test, ASTM D892, is the most common test used. Galgoci explains, “This test is comprised of three “sequences” that encompass different conditions (e.g., temperature) for preconditioning and testing of the oil. A so-called 4th sequence of ASTM D892 is ASTM D6082 that measures the high-temperature foam tendency.”
Table 4 shows an ASTM D892 test evaluating the defoaming of gear oil samples aged for one week at 50 C. Galgoci says, “Sample B4 showed excellent defoaming at a significantly lower use level than other antifoams. Sample A4 was the control used in this study.”
Table 4. Data obtained from an ASTM D892 evaluation of gear oils with four antifoams is shown. (Table courtesy of The Münzing Group.)
Other foam-testing procedures also are available to measure specific parameters or fluid types. Galgoci says, “For gear oils, the ‘Flender’ test is used to monitor the foam tendency in an actual gear box. Air entrainment is measured through the use of ASTM D3427 that measures the density of the oil over time as the air entrained in the oil rises to the surface. Other important considerations are compatibility and performance of the antifoam as a function of time/temperature. The effects of filtration on antifoam performance also should be evaluated.”
REFERENCES
1.
Farn, R., ed. (2006),
Chemistry and technology of surfactants, Wiley-Blackwell Publishing, Ltd.: Oxford, UK.
2.
Holmberg, K., Jönsson, B., Kronberg, B. and Lindman, B. (2003),
Surfactants and polymers in aqueous solutions, 2nd edition, John Wiley & Sons Ltd.: West Sussex, UK. DOI: 10.1002/0470856420.
Neil Canter heads his own consulting company, Chemical Solutions, in Willow Grove, Pa. You can reach him at neilcanter@comcast.net.