The Lubrizol Corporation
Formulation of Environmentally Considerate Greases
By Gareth Fish, PhD CLS CLGS, The Lubrizol Corporation, Wickliffe, Ohio, USA | TLT CMF Plus November 2015
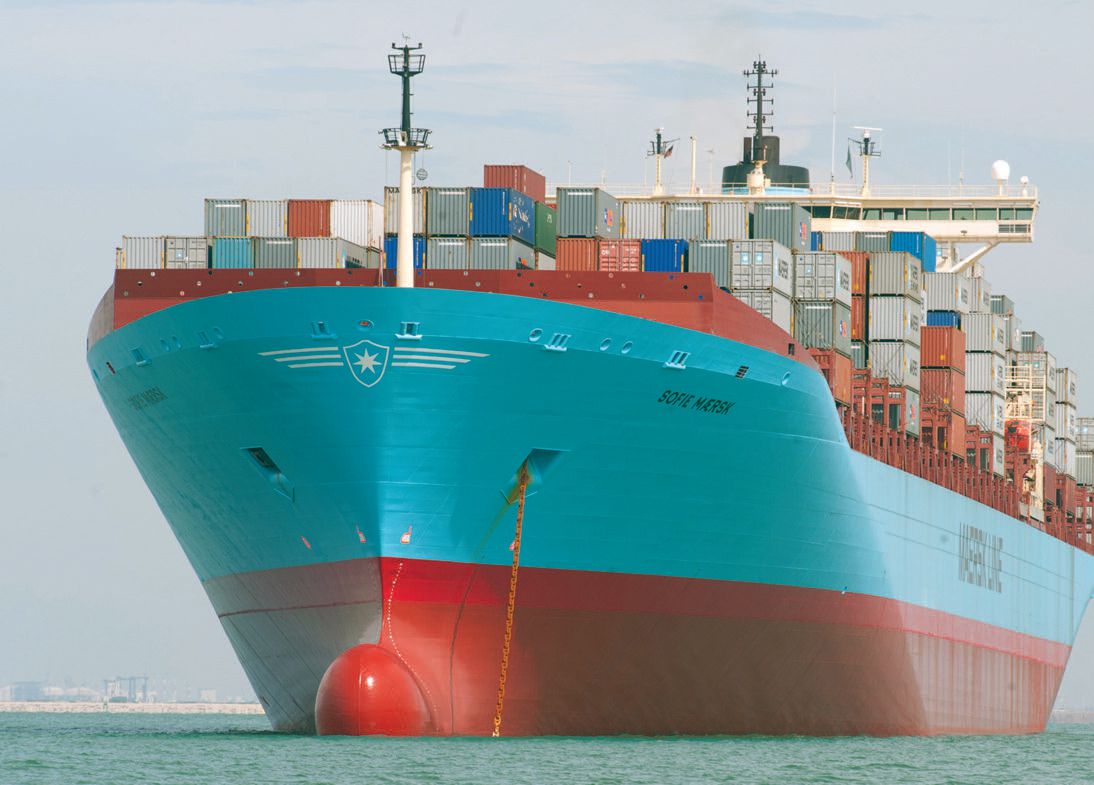
Reduced environmental impact through the choice of suitable greases has become an important consideration of many end users. Government legislation and policies place emphasis on the future protection of natural resources.
Recent Lubrizol technology developments have enabled bio-based and eco-considerate grease products to be formulated to achieve a high level of performance. These can be used in total loss applications including marine, farming, forestry and mining. The commercial marketing forum presentation given at the 2015 STLE Conference dis cussed how Lubrizol components, along with a carefully selected base fluid, can help in the formulation of higher performing environmentally considerate greases.
History
The phrase “environmentally considerate greases” has been used in many working groups and industry forums to encompass the varying terms that are called out in different regulations and specifications. Over the last 20 years, a number of different governmental and regulatory organizations have begun to define this category:
•
In 1992, the European Union (EU) Ecolabel launched a voluntary program, which was extended in 2005 to include lubricants and was modified in 2011 to include a wider range of thickeners for grease.
•
In 1999, the US Army Corps of Engineers (USACE) recommended use of the term “environmentally acceptable” lubricants (EALs) to describe lubricants that were both biodegradable and non-toxic and could be used in non-military USACE facilities such as hydropower plants, flood-control pumping plants, and lock-and-dam sites.
Following on from the US Clean Water Acts of 1972 and 1977, the US Environmental Protection Agency (EPA) identified the need to prevent oil pollution from ships in US waters and reduce annual clean-up costs of $30 million. The first vessel general permit (VGP) covering lubricants used on US waters was enacted in 2008, part of which was a voluntary code to encourage commercial ship owners to use EALs for all water interfaces. In 2013, it became a mandatory requirement to use VGP-compliant marine lubricants if they are available.
Environmentally Acceptable Lubricants
According to the recent NLGI Grease Production survey, environmentally acceptable lubricating greases comprise a small portion of the total lubricant market (<1.0%). In 2014, the annual global production of lubricating grease included approximately 5,500 metric tons with bio-base fluids and 4,000 metric tons with potentially biodegradable synthetic esters.
However, the market for EALs continues to expand, particularly in Europe. In some countries, legislation mandates the use of environmentally compatible lubricants. Examples of this are rail curve greases in Sweden and forestry machinery lubricants and greases in Austria.
Grease technology has moved forward in many areas and the development of sustainable chemistry for lubricants is now on the center stage.
Vessel General Permit Greases
VGP marine lubricants must meet a series of criteria when they are used in ship-water interfaces. VGP states that at least 75wt% of the grease must be a readily biodegradable base oil such as bio-based or synthetic ester or a polyglycol. The second requirement is that the grease must be minimally toxic and thirdly it must be not bioaccumulative. The remaining 25% of the grease formulation does not need to meet the readily/ultimately biodegradable requirement, but it does need to be either inherently or non-biodegradable and it cannot be (potentially) bioaccumulative. With respect to having minimal aquatic toxicity, it states that the complete formulation and main components must pass Organization for Economic Co-operation and Development (OECD) or equivalent toxicity tests on algae, crustaceans, and fish at >1000 mg/L for main components.
VGP does not appear to outright ban many of the hazardous substances that the Ecolabel places restrictions on, but waste from ships cannot include substances on the hazardous waste list as defined in 40 CFR 401.15.
One advantage for global lubricant developers is that products approved as meeting the following standards are automatically approved as VGP-approved lubricants: Blue Angel; EU Ecolabel; Nordic Swan; Swedish standards SS 1554434 and 155470; Convention for the protection of the marine environment of the NE Atlantic (OSPAR); and the EPA’s Design for the Environment (DfE).
The Lubricant Substance Classification (LuSC) list
The EU has developed and regularly updates their Lubricant Substance Classification (LuSC) list that defines what chemicals and commercial, branded lubricant components have been tested for biodegradability and aquatic toxicity/bioaccumulation potential and up to what level they can be used in lubricant formulations. In addition to biodegradability and aquatic toxicity/bioaccumulation potential, renewable carbon content is included. When formulating Ecolabel lubricants if a substance, base fluid or additive is already present on the LuSC list and is used below the threshold limit, the need for full testing and registration of that component is unnecessary.
Formulating VGP Greases
While there are many other applications that require environmentally considerate grease, this article focuses on formulating VGP greases. The starting point for all VGP greases is the base oil. The first issue is that the majority of vegetable oils sold on the market today are of much lower viscosity than is desired for greases for higher performance marine or industrial lubricants, with most fluids having kinematic viscosities of <100 mm
2/s at 40°C. Typical industrial greases have base oil viscosities at ISO VG 220 and above. Wire rope greases typically have base oil viscosities of 500 mm
2/s at 40°C, which makes this viscosity even more of a challenge to achieve.
Lubrizol’s formulating solution for boosting the low viscosity of bio degradable base oils is to add polymer esters. Some higher viscosity polymer esters have good biodegradable data and can be based on renewable, plant derived, raw materials. The general properties of several esters are compared with a typical PIB used in industrial greases.
The next selection point is the thickener. The presence of water in a normal saponification reaction causes water-sensitive bio-based esters to degrade and be strongly acidic. The answer to this formulating challenge is Lubrizol® 5280GR; the small particle size (<10 μm) of the lithium hydroxide in the dispersion allows it to react very quickly with 12-hydroxystearic and sebacic acids. The result is minimal hydrolysis of the base oil and less foaming of the reaction. Using Lubrizol 5280GR dispersion technology, high dropping point VGP and Ecolabel lithium greases can be manufactured effectively.
In order to test the additive technology in manufacturing VGP greases, five commercially available readily biodegradable base fluids (soybean, canola, sunflower, an estolide and a synthetic diester) were used to prepare greases. These greases were then tested against sixth performance control grease made with an API group I 600N mineral oil (
Table 2).
From the results in table 2 of the greases manufactured, it is clear that no two VGP usable oils behave in a similar manner with respect to thickening or grease properties and nor do they behave similarly to mineral oils. This makes the task of formulating greases to meet technical targets much more difficult.
Lubrizol® GR213A, a performance additive package for lubricating greases, is on the LuSC list. It was incorporated into four of the base greases shown above and industry standard wear tests were carried out. The data is shown in
table 3 and compared to the grease industry NLGI GC-LB standard for those tests. The results show that all four of the greases gave good 4-Ball EP performance.
For improved wear and corrosion resistance of the grease, the performance can be further enhanced through the use of a supplementary booster. Lubrizol® 4320FG is an amine phosphate that is LuSC listed and can be used in Ecolabel and VGP greases up to 1%wt treat level.
For some applications such as wire ropes and also for enhanced water resistance, it is necessary to add a tackifier. For typical greases, a styrene-isoprene (SIP) or ethylene-propylene (OCP) co-polymers and PIBs are used as tackifiers. Unlike typical tackifiers, Lubrizol® 5994C (SIP) and Lubrizol® 7067C (OCP) tackifiers readily dissolve at up to 4% in most esters and bio-fluids.
Based on the above work, a series of base oil blends were developed to meet the required kinematic viscosities (
Table 4).
Lithium complex greases using the 3:1 12-hydroxystearate and the Lubrizol 5280GR anhydrous lithium dispersion were manufactured initially with 2% of the Lubrizol 5994C added. Lubrizol GR213A was incorporated at 5.3%wt. The greases were milled and de-aerated and standard grease tests were carried out on them. Test results for the greases are in
table 5.
The results in
table 6 showed that good basic grease properties can be achieved when using biodegradable base oils coupled with the LuSC additive package. Adding the Lubrizol 5994C SIP polymer gave the greases very good water resistance and tackiness.
Summary and Conclusions
While formulating an environmentally considerate grease can be challenging, Lubrizol technology is available to help the grease developer produce high quality lithium greases for a variety of applications. These additive packages, when used in a suitable base oil, have been tested and have proven to meet the requirements of specifications like the VGP. A complete list of Lubrizol products and their purpose is shown in Table 6; for more information, please con tact Lubrizol at
successtogether@lubrizol.com.