The state of condition monitoring
Jack Poley | TLT On Condition Monitoring November 2015
The news is both good and bad.
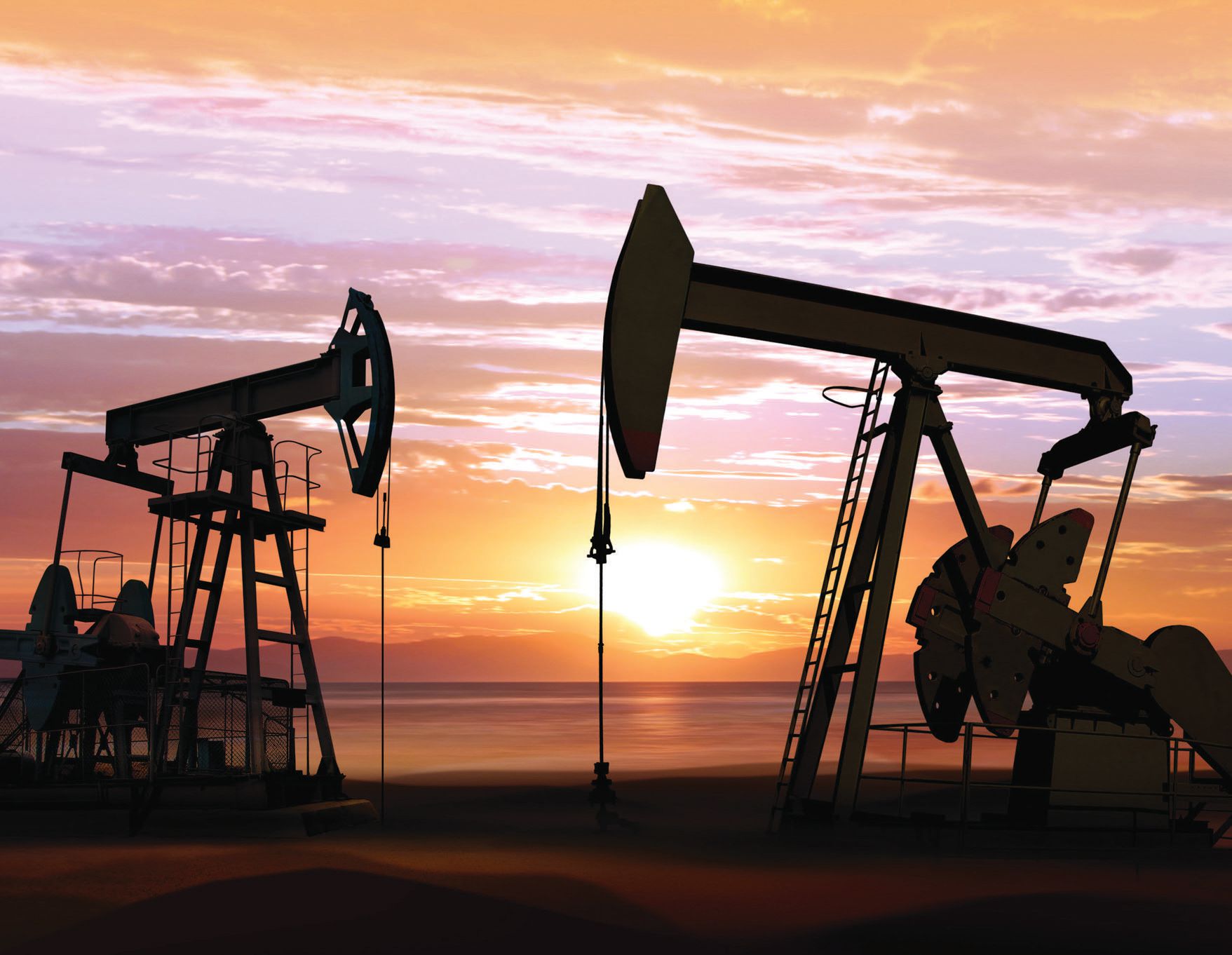
© Can Stock Photo Inc. / ssuaphoto
I’M TEMPORARILY INTERRUPTING THE COMPLEXITIES IN CM series of columns to address a current situation that I’ve seen repeat itself several times over the decades I’ve been in the CM world.
I’m addressing the bad news first, because it’s truly bad and sad.
CM AND DOWNTURNS
As I write this column, the oil and gas market is currently experiencing its worst economic downturn since the recession of 2008-2009. Oil prices were well below $50 at points. On the date this article was drafted, oil was fluctuating at ~$50/bbl, well below healthy levels for the industry. The drilling industry received a direct hit, as always occurs when oil prices falter. Significant layoffs and other cost cutting moves necessarily take place. It appears, however, this bout with low oil prices will have the greatest impact ever on offshore drilling. The costs and technical challenges of stacking modern rigs are unprecedented.
As such I’ve seen the departure of significant talent and knowledge in CM, some of whom I know personally. This includes subject matter experts (SMEs) for a variety of CM techniques: vibration analysis (VIB), in-service fluid analysis (ISFA) and so forth. SMEs are the cornerstones of CM application in their respective companies. Their titles, one might say, are self-explanatory. They facilitate the application of VIB and ISFA to best effect and are typically the interface between their company and the vendors that serve their company, with respect to CM.
SMEs also review numbers of CM reports, such as ISFA test results and comments, serving as knowledgeable advisors and support for the maintenance team. Where ISFA is concerned, SMEs also are typically involved with lubrication practices and even lubricants selection. In short, they’re providing a maintenance-critical function.
Competent SMEs are not easy to find because it takes years to acquire the knowledge necessary to perform the functions of the position. A number of the SMEs I know that have been laid off will not be available when the market returns to good profitability because they were middle-aged and will, instead, adapt to early retirement. They also might hook up with other companies that may be hiring their skill set for their remaining five to nine years they may have intended to work. The sad part, beyond the loss of a job, is that the companies that lay off these highly skilled people are weakening their maintenance at a time when it needs to be the best it can be. It is likely no plan was in place for knowledge transfer of these departed SMEs.
My long tenure in CM has led me to conclude that it is treated, more often than not, as a necessary evil—no different than having to do laundry or mow the lawn. In the larger picture, nobody really likes maintenance because it simply restores or preserves the operation of equipment, rarely imparting any added value after a repair, but merely enabling a piece of equipment to resume what it had been doing until it was compromised in one way or another, such that production was curtailed or even temporarily halted. The offensive power of CM,
pre-emptive initiative, is often overlooked as a profit center element.
Many people neglect their health by avoiding a routine physical at some interval, or visit their dcotors or dentists only when pain occurs. The parallel with machinery health is the same. Although CM continues to gain momentum overall, some organizations still practice reactive rather than proactive maintenance—machinery is repaired when it cannot perform. Others might have installed CM programs in name, but they run somewhat rudderless for lack of a solid plan. For these companies it is too large a step to consider the notion of preventive maintenance, from whence CM was born, that necessarily adds expense up front but that virtually always returns more than spent over a period of time. These companies have a limited, binary view of CM.
1.
If times are good, and profits well in place, there’s no need to have CM other than maybe some cursory effort. These are the companies that make profits irrespective of weak maintenance support efforts. Yes, they leave money on the table, but it’s not obvious or necessary to chase it in their minds.
2.
When times are bad, there is no money for CM (or SMEs). CM always takes its own hit in time of this ilk. This is simply the product of lack of discipline, probably from day one where CM was put in place without any sort of fanfare or evangelism
or stated goal (i.e., a plan). When CM’s weakened, or nearly abandoned in a downturn, it’s almost always going to be because ROI was never a mandated measurement in the CM equation—no accountability was put in place. Thus management could not see the value of CM. It was just a necessary evil that was no longer affordable.
This simplistic view is surely not reasonable in today’s competitive marketplaces. It is this mentality that leads companies to remove critical pieces of the maintenance support system in tough times—and perhaps never restore them. Most companies do continue their ISFA and VIB programs when these economic swings occur, but there is frequently no oversight or accountability in place. ISFA reports are generated but no one’s necessarily making sure the results are being put to best use.
WHERE’S THE GOOD NEWS?
This section is primarily for those who already practice CM to good effect and are constantly looking to improve their machinery availability and, thus, their ROI. It’s really not news, but it is opportunity.
1.
My last two articles were to do with database maintenance and updating as pertains to CM and, in particular, ISFA. Now is the time to do it—temporarily rehire that SME casualty, his/her equivalent or a qualified consultant and clean up your database so it’s ready to be mined to best effect. This is a major part of realizing the best yield from your CM program.
2.
This also is the time to be sure of your feedback, i.e., the maintenance reporting thread that produces the justification for your program and that enables accountability and confirms ROI assessments within your CMMS system.
3.
If you’re going to be without an SME, consider an expert system to evaluate your ISFA data. This is the coming trend, wherein SME-equivalent knowledge from domain experts is resident in Intelligent Agents (IAs). This type of software helps you drill down to specific problem types, maintenance triage and development of ROI models, all with statistical support.
Oil will return—it always does. Do yourself a favor and visit the mechanics of your CM program so that you’re ready to reap the maximum benefits when the upturn comes.
WHAT IS THE STATE OF CM?
CM is gaining ground as a way of maintenance life, but economic efficiency is still not a fundamental practice. That is to say the low-hanging fruit is usually availed, but the equally valuable (as money) insights and gains of a more subtle nature are not necessarily achieved. Here are two common reasons:
1. Accountability. The best CM programs are fully supported from top management, in terms of funding and mandates, then carried out by maintenance management that has the mission and authority to carry it out
and the accountability for the program’s success. There just aren’t enough of these yet. Many companies with CMMS systems have yet to fully connect with their CM programs to best effect. Still, the trend toward a CM program with accountability is growing.
2. Weak data evaluation. Many ISFA reports are issued with insufficient, irrelevant or even incorrect comments. When this happens the best action is not taken and money is lost or not conserved. Machinery is more complex than ever, and lubricants are more sophisticated, too. It is unreasonable to expect even the best evaluator (domain expert) to provide in-depth commentary flawlessly over thousands of samples with a variety of unique patterns from a variety of machinery and lubricants.
The solution, of course, is to employ IAs—expert systems informed by domain experts for machinery and lubrication. Complex patterns known to reveal particular problems can easily be programmed as rules to provide the most pertinent and proven advisories consistently and efficiently. Using an IA for evaluation eliminates the frequent issue of extraneous and/or inconsistently sequenced comments that dilute the inference drawn from the advisory when the report recipient reads it.
THE FUTURE OF CM
CM is alive and well; 21st century CM is seeing a variety of new instruments and technologies that give evaluators yet more information while also keeping analysis cost low. I believe it is now true that the majority of routinely performed ISFA tests can be automated using carousels and robots. In a multiple lab situation, this kind of technology greatly enhances quality control and standardization.
Repeating something I related in this column a number of years ago, I was interviewed by a field editor for Popular Science magazine. The editor closed the interview with: “So you can look at a group of test results just like a doctor looks at a blood test and diagnose problems in an engine?” My reply, “Maybe not at the depth of medicine, but that analogy may be more appropriate a few decades from now.” Those decades have passed and, while I’d never posit that we evaluators are as sophisticated as an endocrinologist, I would say the parallel is at least respectable now, whereas not in 1961, when I was interviewed. CM’s surely better now, and it needs to be. It can help make maintenance a partner in profits rather than a necessary evil. There’s never been a better time to take advantage of CM.
Jack Poley is managing partner of Condition Monitoring International (CMI), Miami, consultants in fluid analysis. You can reach him at jpoley@conditionmonitoringintl.com.
For more information about CMI, visit www.conditionmonitoringintl.com.