The advantages of synthetic metal-removal fluids
Stuart F. Brown | TLT Webinars October 2015
Low foaming, no misting and rapid heat dissipation are among the benefits.
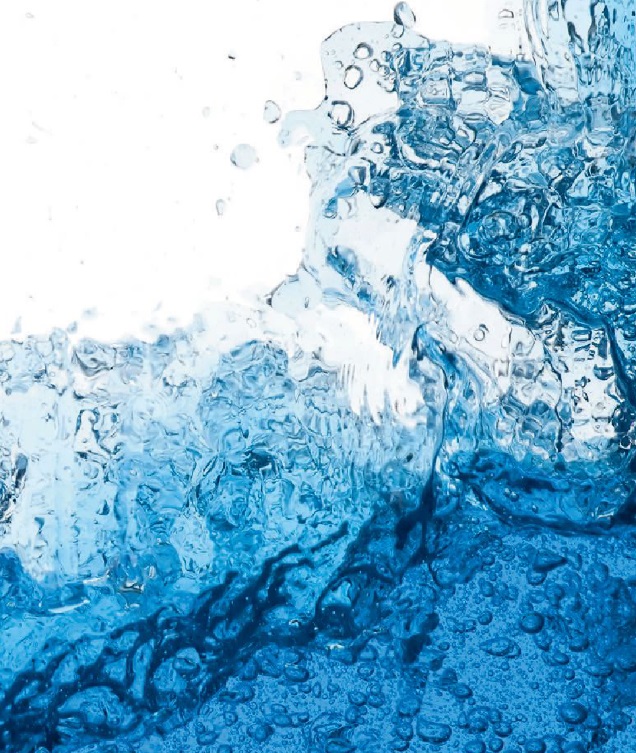
www.canstockphoto.com
KEY CONCEPTS
•
Synthetic fluids began evolving about 50 years ago when an inexpensive and stable fluid was needed for grinding cast iron.
•
The first form of synthetics were chemical solutions of organic or inorganic materials in water—still the most widely used formulation in metalworking today.
•
Synthetic MRF benefits include better thermal and oxidation stability, rapid heat dissipation from tooling and workpieces and no oil misting or smoking.
MEET THE PRESENTER
This article is based on a Webinar originally presented by STLE University. “Synthetic Metal-Removal Fluids” is available at
www.stle.org: $39 to STLE members, $59 for all others.
Dr. Alan Eckard received a bachelor’s in science in chemistry from Rensselaer Polytechnic Institute and a doctorate in physical chemistry from the University of Liverpool, England. He was a research fellow and later a lecturer in chemistry at the University of Keele in England. He later returned to North America as a research fellow at the University of Toronto. Dr. Eckard has been at the forefront of technology for lubrication, corrosion protection and surface finishing for metalworking and fabrication of metals. He holds several patents and has published widely in various trade and technical journals. He is currently affiliated with the New York section of STLE and is a Certified Metalworking Fluids Specialist. You can reach Alan at
eckaral@aol.com.
Dr. Alan Eckard
ALMOST EVERYONE IS FAMILIAR TO SOME DEGREE with so-called synthetic motor oils, but how many in the tribology community have a firm grasp of the attributes that define synthetic metal-removal fluids (MRFs)? Synthetic MRFs have been in use for decades and are favored for their high workpiece visibility and low-foaming properties. “Chemical solution-type synthetic MRFs do not contain an emulsified phase, and if properly filtered and maintained will remain transparent during use,” says STLE-member Dr. Alan D. Eckard. Today the synthetics are niche players in metal removal, accounting for about 10% of the MRF market in the U.S. and perhaps 18% in Europe, where they receive favorable tax treatment due to the petroleum-free composition.
In an STLE University Webinar delivered Sept. 17, 2014, Eckard discussed the attributes that define synthetic MRFs. Eckard has more than 30 years of experience in formulation technology and additive chemistry and holds several patents. He received a doctorate in physical chemistry from the University of Liverpool, England, holds STLE’s Certified Metalworking Fluids Specialist™ certification and is a member of the society’s New York Section.
Following are key points from Eckard’s presentation which defines synthetic MRFs, their typical applications and compositions as well as trends in usage and emerging new technology.
It is generally accepted that
synthetic, as applied to lubricants of all types, means free of petroleum oils. In metal-cutting applications, synthetic MRFs are often further defined as solutions of organic or inorganic non-petroleum chemicals in water.
Offsetting the workpiece visibility benefits of synthetic MRFs are their inherent disadvantages in limited corrosion protection and their incompatibility with most extreme pressure additives, which can limit the lubricity of the fluids. A further potential detriment of the synthetics is their requirement for consistently high water quality to maintain corrosion protection, usually provided by means of deionization or reverse osmosis treatment.
Most people associated with the metalworking industries would accept chemical solutions of organic or inorganic materials in water as being a synthetic MRF. This was the first form of synthetics developed and is the most widely used in metalworking today. A second category includes emulsions of hydrophobes, except petroleum oil, that are often used in the form of a microemulsion and referred to as synthetic emulsions. It’s also possible to have to have neat fluids that are used undiluted and contain a synthetic base such as polyalkylene glycol, esters, polyalphaolefins or natural triglycerides. All of these would include synthetic additives to enhance lubricity and other performance attributes.
Oil seed triglycerides are often accepted as components of synthetic MRFs and are certainly renewable.
The definitions of synthetic MRFs also contain some gray areas that cause a lot of confusion. The problem stems from the fact that petroleum is a naturally occurring material that most would not call synthetic, while a natural material like canola oil is often classified as synthetic when replacing a petroleum oil in an MRF. In reality, neither material is synthetic; they are both naturally occurring materials.
Other gray areas include fluids containing gas-to-liquid hydrocarbons or severely cracked petroleum which are considerably modified in chemical structure and may contain 80%-100% synthetic hydrocarbon structures. Aside from natural triglycerides derived from plant or animal fats, the carbon source for virtually all organic chemicals would be the petrochemical or coal industries and hence be non-renewable. Inorganic chemicals such as boric acid are also mined or derived from natural sources, which strictly speaking are not renewable. As most of these are chemically modified in the final form, they too could be considered synthetic.
Synthetic fluids began evolving about 50 years ago when the need arose for an inexpensive and stable fluid for grinding cast iron. Water is inexpensive, safe and stable but causes serious rust problems when used in metalworking operations. The original solution was to add sodium nitrate to the water as a depolarizing agent that stopped corrosion, but that process left behind abrasive crystals that caused moving parts to seize. The next innovation was adding an alkanolamine—typically diethanolamine (DEA)—to improve corrosion protection and combat residues. The result was a very cost-effective fluid that was widely used in cast iron machining and grinding.
A toxicity problem reared its head, however, when it was learned that DEA can react with nitrate to form N-Nitrosodiethanolamine, a known carcinogen. Beginning in the 1980s, nitrate was phased out and replaced with boric acid salts, monocarboxylic acids, dicarboxylic acids and certain polycarboxylic acids, all of which reacted with alkanolamines to form corrosion inhibiting salts.
Chemical solution synthetic MRFs today can contain additives for boundary lubrication, extreme pressure, corrosion inhibition, alkalinity boosters and antimicrobial pesticides, to name a few. All of those materials must be completely soluble in water because there is no emulsion and no hydrophobic carrier to incorporate them into the product.
Many synthetic fluids are tinted with a dye so that machine operators do not confuse them with water. Blue is a popular color because it has a pleasing appearance and doesn’t resemble anything edible. Several types of water-soluble dyes are available that are stable, non-staining and waste treatable.
Many synthetic fluids are tinted with a dye, and blue is a popular color.
A great advantage of synthetic MRFs is their low-foaming property. “Foam is a really important issue,” says Eckard. “Persistent foaming can shut down a manufacturing operation faster than any other coolant-related problem. Believe me, I’ve been in a number of situations where we ran out of a plant followed by a tidal wave of foam.” Foaming also can cause coolant pumps to entrain air resulting in failure to deliver sufficient coolant to the tooling.
Foam comparisons: 10% during agitation (left) and 10 seconds after stopping (right).
Another benefit of synthetic MRFs is that their high water content provides rapid heat dissipation from tooling and workpieces. The water has low viscosity allowing it to flow freely to the tool interface, which provides excellent cooling and delivery of lubricant additives. An additional advantage of synthetics is that they don’t form an oil mist or smoke in work areas as petroleum fluids can. The latter are considered a health hazard subject to exposure limits. Finally, the synthetics have better thermal and oxidation stability compared to petroleum-based MRFs.
This oil mist or smoke would be cleared with an oil-free product.
High-performance synthetic MRFs can cost more than petroleum formulations, a factor that may catch the eye of a purchasing agent in certain situations. One reason is that there are a limited number of water-soluble synthetic lubricity additives available, and they can be costly. But when you consider such factors as low toxicity, superior oxidation, thermal stability and ease of cleaning up after a spill, synthetics can win the day. And for performing light-duty machining or basic grinding operations, they can be the low-cost solution.
A newer class of fluids called semisynthetics is quickly becoming the most widely used form of emulsified MRF. These fluids consist of 10%-50% synthetic base fluid, typically esters. Using non-petroleum base fluids is an attractive option in applications where there are health and safety concerns. The fluids can be formulated to be high in renewable content, with petroleum oil comprising little or none of the product.
Promising recent developments in the synthetics field include new esters with good lubricity and high viscosity for emulsion-type MRFs and gas-to-liquid synthetic hydrocarbons that make more stable and affordable base fluids for MRFs, Eckard says.
Eckard adds that chemical solution synthetic MRFs can be low cost, low foaming and easy to maintain—provided good quality water is used for dilution. He also observes that synthetic oil-based emulsion MRFs can provide improved performance when compared to similar petroleum-based formulations. These synthetic products, particularly ester-based ones, have high inherent boundary lubricant properties, can be very stable base fluids (except the triglycerides) and in some cases can include renewable content.
Finally, Eckard adds that many classes of synthetics cause less environmental damage in the event of a spill.
You can reach free-lance writer Stuart F. Brown at www.stuartfbrown.com.