So you want to develop engine oil engine tests?
Jeanna Van Rensselar, Senior Feature Writer | TLT Webinars October 2015
It’s complex, frustrating, time-consuming—and ultimately rewarding.
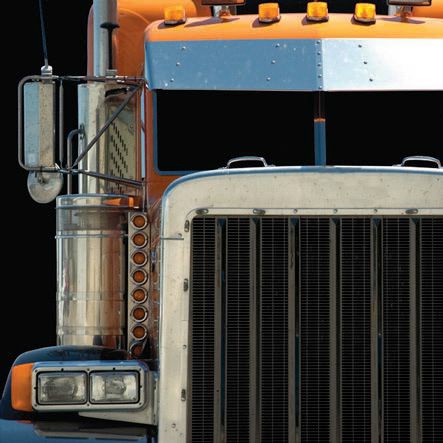
www.canstockphoto.com
KEY CONCEPTS
•
The three engine oil test types are field, bench and dynamometer tests.
•
Test development is an extremely involved process for engine build.
•
The test developer is committed to a great deal of work over a long period of time and is the primary guardian of the test.
MEET THE PRESENTER
This article is based on a Webinar originally presented by STLE University. “So You Want to Develop Engine Oil Engine Tests” is available at
www.stle.org: $39 to STLE members, $59 for all others.
Following his retirement after 33 years at General Motors (GM), Dr. Donald Smolenski is currently the North America OEM liaison manager for Evonik in Grosse Pointe, Mich. His experience covers engine oils, including engine and field tests and development of the GM Engine Oil Life System, as well as industrial lubricants, used oil management and recycling and chemicals management.
While at GM, he co-invented the automatic engine oil life monitor that is now standard on almost all GM North America vehicles. He also co-developed the ASTM Sequence IIIE engine oil test for defining high-temperature deposit and wear protection.
He has a bachelor’s of science degree in chemistry from the University of Michigan-Dearborn and a doctorate in chemical engineering from Wayne State University, where he was inducted into the school’s College of Engineering Hall of Fame.
He has been recognized with several industry honors including SAE’s Oral Presentation Awards (1986-1988), Distinguished Speaker Award (1990), Environmental Excellence in Transportation Award (2001) and SAE Fellow (2008). He also received the GM Research McCuen and Boss Kettering Awards (1988). You can reach Don at
donald.smolenski@evonik.com.
Donald Smolenski
SO WHAT CONSIDERATIONS GO INTO DEVELOPING ENGINE OIL TESTS? It starts with the selection of the test type.
Field tests are the truest measure of an oil’s performance, but they might not assess relative severity, might be difficult to reproduce, are expensive and lengthy (ranging anywhere from six months to two years to complete) and can be difficult to monitor and control. Additional challenges include:
•
Cabs can get lost or destroyed.
•
Driver behavior is a big and uncontrollable variable.
•
Driving conditions have a big impact on test results.
•
The test is usually remote and difficult to oversee—because of this, details such as oil color coding are extremely important.
Bench tests are more reproducible, quicker and much less expensive than field tests. They generally make use of consistent hardware (although special test pieces are sometimes made and used). Bench test pitfalls include the following:
•
It’s difficult to know if the test accurately reproduces the failure mechanism that would occur in the field.
•
It often does not even remotely correlate with real-world performance.
•
OEMs are sometimes not impressed with bench test results.
Then there are engine dynamometer (dyno) tests. Because they are generally conducted on production engines, dyno tests:
•
Accurately simulate real-world performance
•
Can assess relative severity with field test reference oils
•
Can have good reproducibility if properly designed
•
Are not as expensive as field tests
•
Can often be completed in a few weeks or less
•
Are more relevant than bench tests in terms of benefits and manageability
•
Are probably the best compromise between field and bench tests.
So dyno testing is what the rest of this article focuses on.
This article is based on an STLE University-sponsored Webinar presented March 26, 2014, by Donald Smolenski, who is the North American OEM liaison manager for Evonik. See Meet the Presenter for details on the Webinar and how you can download a version.
HOW IS AN ENGINE MODEL SELECTED?
The engine must be the most current technology possible and simulate cars that are out in the real world. It also must have an anticipated long production life to avoid developing a test for an engine that quickly goes out of production. The engine needs to exhibit the problem or concern within a reasonable scale—for example, a piston deposit rating range from 3.0-9.0 versus 9.6-9.9. Finally the engine needs to be as robust as possible with respect to non-measured performance—tests need to exhibit targeted performance issues but not fall apart in other areas.
Typical engine model selection issues include the following:
•
Engine-build/teardown people want a test engine that is compatible with their classic car, boat, etc.
•
OEM hardware contacts aren’t happy about being asked for engines they don’t think are ready or available for testing. This is especially true for new engine models.
•
The OEM might want to showcase its most impressive engine, which may be inappropriate for test purposes.
The engine build is a critical aspect of the test. Once the engine is selected, the test developer should ensure that almost nothing is left to chance—that everyone is building the engines the same way. Any variation can affect engine operational validity, test severity and test precision. That level of detail is important for troubleshooting in case something shifts with the test. Multiple-build worksheets are often included as appendices in the test report.
HARDWARE AND PARAMETERS
Any part/assembly measurement or pass-fail rating, or any report parameter (e.g., pistons, when piston deposits are rated), is critical. Also, any part is critical when it is crucial to running a valid test (e.g., cylinder hone, ring gap when blow-by rate is specified) (
1).
Anything that materially affects test operational validity, test severity and/or reproducibility is considered a critical operational parameter. These parameters are almost always controlled (sometimes indirectly). Other critical operational parameters (which should be reported in the test report) include:
•
Engine speed
•
Oil temperature
•
Blow-by
•
Oil consumption
•
Engine build.
Critical parameters have specified target values and allowable ranges because most variables, including the temperature, can never be made completely static.
THE TEST
Once the original test intent is determined, the test developer needs to decide how realistic it is and whether the part can be accurately measured (e.g., wear by micrometer—some European tests use a radionucleotide) or quantified (CRC merit rating scale) by a trained rater. Many test factors are interrelated (
see Figure 1). The engine build is the place to start; the test stand and engine have to communicate (
see sidebar titled How is the Test Stand Configured?).
Figure 1. Although many test factors are interrelated, the engine build is the place to start. The test stand and engine must communicate.
HOW IS THE TEST STAND CONFIGURED?
The most important factor is that the test stand is as safe as possible for the operators. Historically this hasn’t always been the case—for example, operators had to work around engine components that were so hot they glowed. The test stand must measure and accurately control all critical operational parameters and be as completely specified as possible. It also must have a robust design and construction to minimize operationally invalid tests.
Instrumentation personnel can make an engine more foolproof through programming, but the test stand must anticipate the unanticipatable.
It’s not that easy to get a test engine running on a stand—that alone can take several months. Emission control devices significantly complicate the process. The plumbing and wiring are relatively easy, but engine control can be extremely challenging.
The test severity must be sufficient enough to consistently separate good and bad oils (
see Figure 2). The degree of precision must be significantly better than the difference in severity between good and bad oils. The more precise, the easier it is to discriminate good from bad. Conversely, the greater the difference between good and bad, the less precise the test has to be (
see sidebar titled Test Fuel and Test Oils).
Figure 2. The degree of precision should be significantly better than the difference in severity between good and bad oils. But the greater the difference between good and bad, the less precise the test has to be.
TEST FUEL AND TEST OILS
The test fuel is nearly always specified. In some cases a commercial fuel with known good batch-to-batch reproducibility might be specified (e.g., an emissions certification fuel). In other cases the fuel might be specifically designed to produce test severity. Each new batch may need to be qualified, then noted and reported in test report. Fuel cannot be stored as long as hardware.
In order to know whether or not a test accurately discriminates between oils that are good and bad, the reference oils need to be good, bad and (ideally) borderline. But since suppliers are not keen on being associated with bad reference oils, they can be hard to come by. Reference oils are most commonly field test oils.
If there is a merit rating, the tester wants it to show that the oils are separating—the repeatability is good and the separation is good. If there is poor separation and poor precision, the good and bad oils will overlap creating a less desirable situation.
Statistics are a great tool for tracking test severity and precision. They can be used to correct minor test severity shifts—but the tester needs to be careful doing this and needs to have a reason. Statistics shouldn’t be used as a substitute for evaluating and correcting a problem.
A robust test is very desirable, but there is rarely enough time to thoroughly evaluate and ensure it (
see Figure 3). The best alternative is to consider which operational, hardware or other parameters would be expected to potentially affect test results—which hardware and operational parameters are the most significant. Once selected, each parameter should be systematically evaluated by running at or just outside the upper and lower allowable limit—assessing impact on test results.
Figure 3. The goal is a robust test, but there is rarely enough time to ensure it. The best alternative is to consider which operational, hardware or other parameters could affect test results.
WRITE-UP AND RESULTS
The write-up must include dozens of appendices and specify parts, engine stand details, engine build, operational set point and control details, rating or measurement pre- and post-test, test report format, etc. The write-up has to be done very exactingly. Often it has to exactly fit a specified format (e.g., ASTM).
So now the test looks good. The test developer needs to see if others agree. This involves leaving as little open to interpretation as possible and then reasonable interpretation of the test procedure by reasonable people (
see sidebar titled The Surveillance Panel).
THE SURVEILLANCE PANEL
Once the test is accepted, a surveillance panel (which was formed during the test-development phase) will meet regularly to review test severity and precision. The surveillance panel is composed of the test sponsor, the monitoring agency (e.g., ASTM TMC) and test engineers from labs running the test. If there is a problem the surveillance panel will begin an investigation to determine the root cause (operational, hardware, fuel, etc.), and recommend a fix. The test developer will be centrally involved.
FOLLOW-UP
A test matrix is designed by statisticians to assess true discrimination and reproducibility. Base oil interchange and viscosity grade read-across are generally incorporated into the matrix to generate additional data to evaluate what interpolation or extrapolation of tests results among different oils might be prudent. The first matrix design from statisticians might be overly ambitious and could need to be tempered somewhat. The more repeats, the more statisticians like it, but matrix affordability also is a factor.
Once the precision matrix is run and results analyzed, the industry will decide whether or not the test is acceptable for use in a given specification. OEMs and end-users will look primarily at pass-fail limits. For a test replacing an existing test, they will try to develop equivalent pass-fail limit(s). The difficulty increases exponentially with the number of pass-fail parameters. The limits may be made more severe if there was a request from the OEMs for performance improvement. While the test developer cannot unilaterally set a test limit, their recommendation does carry weight.
The monitoring body—in the ASTM System, the Test Monitoring Center (TMC)—is a good partner for the test developer. The TMC will monitor reference test results to ensure that all calibrated stands obtain proper results. For candidate runs, the test must be registered with the TMC prior to being run; if a test is not registered, it is not a valid test. This registration is to ensure that a past practice of running multiple tests and only showing the one passing result will not occur.
The test developer/sponsor generally has agreed to take responsibility for the supply of critical hardware over the expected life of the test, which could be six to eight years (
see sidebar titled The Test Developer/Test Sponsor). Critical hardware cannot generally be purchased through typical auto parts channels, but must be purchased/supplied according to much tighter standards. This requires ongoing contact with parts suppliers.
THE TEST DEVELOPER/TEST SPONSOR
The difference between a test developer and a test sponsor is mostly semantics. But a test developer will run at least some of the test development work in-house while a test sponsor will contract tests with an independent laboratory. In both cases this person is accepting responsibility for much more than just test development. And in both cases this person is held accountable by stakeholders.
The test sponsor must attend industry meetings and be accessible when there are questions or concerns about hardware, operational severity, discrimination, etc. The test sponsor is often the scapegoat for any problem whether they can reasonably be considered accountable or not.
Finally the test sponsor must be vigilant about protecting the test from misuse or abuse. Sometimes a lab will request a variance for a hardware or operational parameter, possibly because current specifications are onerous and unreasonable to achieve. Other times the relaxation of a parameter could give a stakeholder a competitive advantage.
While developing, overseeing and following through on tests is onerous, often thankless and sometimes aggravating, remembering that the ultimate goal of a test developer is to improve the quality of oils in the field and that a good test helps ensure this, the rewards compensate for everything else.
1.
Blow-by is exhaust gas that gets past the piston rings and into the crankcase.
Jeanna Van Rensselar heads her own communication/public relations firm, Smart PR Communications, in Naperville, Ill. You can reach her at jeanna@smartprcommunications.com.