What are the biggest challenges facing a predictive maintenance program in a manufacturing facility?
TLT Sounding Board June 2015
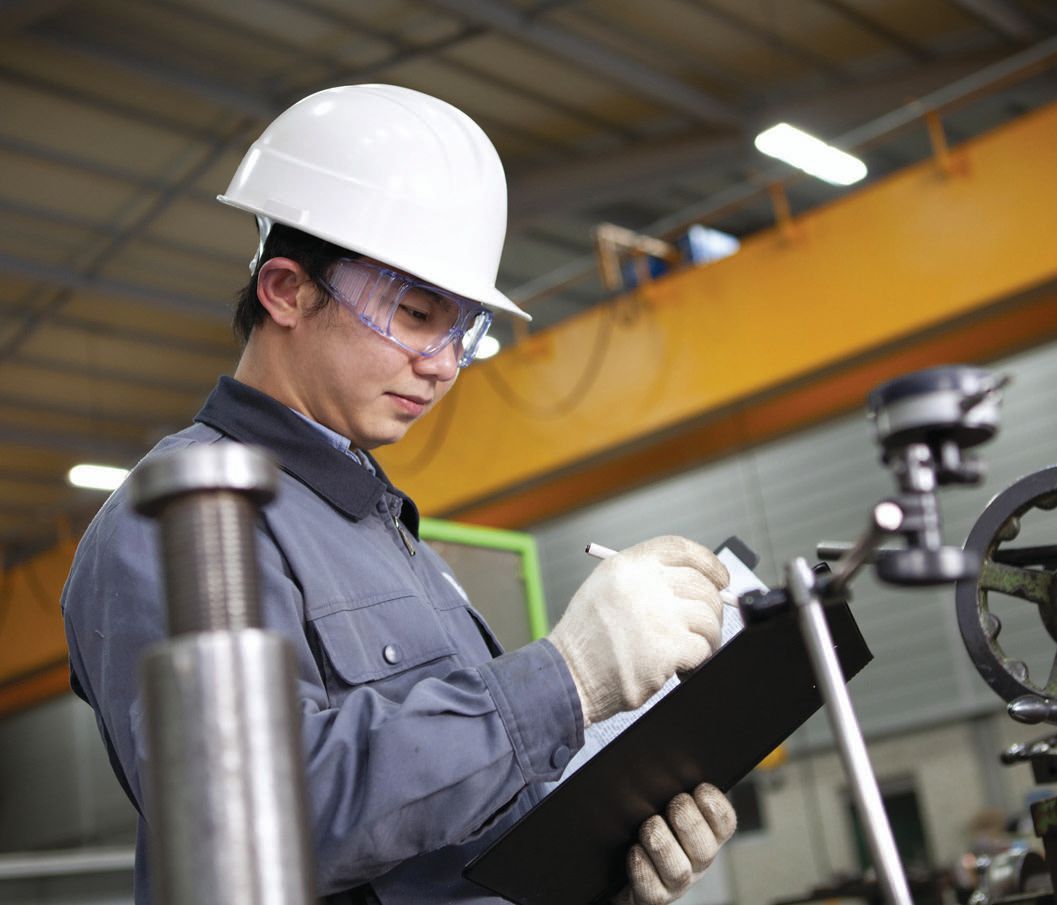
www.canstockphoto.com
Lack of understanding and support from senior managers continues to be a vexing problem for STLE members involved with predictive maintenance. Respondents to this month’s survey stated that poor buy-in from the top remains the single biggest obstacle to implementing sound predictive maintenance programs in manufacturing plants. Many readers say they regularly deal with the “treat the symptoms rather than cure the disease” syndrome. Other issues cited were lack of budget and human resources, not enough time to implement a program and inconsistent practices. On the positive side, technology continues to reduce the time and cost of fluid-maintenance programs, although such changes come gradually. “It’s more evolutionary than revolutionary,” one reader commented.
Buy-in from upper management, finding resources to do it (planning, scheduling, performing) and following through with what the testing results are recommending.
Agreement/commitment from maintenance, purchasing and production.
Manpower shortage, consistency in personnel, training.
Finding time and having parts on hand to complete the job/task.
(1.) Old or out-of-date machinery and equipment. Older technology that isn’t upgradeable. (2.) Lack of trained personnel in maintenance or production. (3.) Lack of understanding that predictive maintenance is the key to maximizing up time. It should be an integral part but can be overlooked due to timing or decreases in staffing or plant economics.
(1.) Under training. (2.) Under staffing. (3.) Under funding.
Consistency, cost, accuracy.
Finding someone who understands the methodology.
Getting senior management to understand the importance of predictive maintenance.
(1.) Buy-in from decision-makers controlling budgets. (2.) Buy-in from manufacturing facility management. (3.) Cooperation by plant operators.
Management budgets.
Production demands—management not honoring agreed-to downtime. Poor lubrication practices—it’s usually done by the least-trained and skilled guy. Treating the symptom rather than the problem, such as putting in a heavier gear oil to slow a seal leak rather than replacing the seal.
Ensuring that the predictive model correlates accurately with the specific conditions on the ground. Ensuring that parameters outside the predictive parameters are still suitably managed, e.g., avoiding contamination, fitting errors, failure of ancillary systems such as oil pumps.
Obtaining buy-in from production and others who don’t fully understand the value and so don’t provide necessary investment—skilled Pdm program employees. Seems there is always one champion of the program (and there needs to be), but it’s hard to find other people as passionate.
Timeliness of scheduling repairs, budgets, workload.
Finding someone with the skill set to develop and maintain the program.
Attitude and a lack of understanding of the benefits of maintaining equipment in a reliable condition.
Lack of vision and long-term commitment.
Culture change, mostly from the shop floor employees. Insufficient ability to properly interpret the data. Only treating the symptoms rather than attempting to cure the disease.
(1.) Proper implementation of the program to all equipment. (2.) Qualify the effectiveness of the program to critical equipments.
(1.) Maintenance operator alertness to early symptoms. (2.) Proper process and guideline for each equipment and application.
Where to start, how to start and what lab or tests to use.
Plant budgetary constraints, downsized maintenance departments and lack of qualified individuals dedicated to the process.
Getting operations and engineers to agree on when equipment can be made available for service.
Production pressures. Perceived lack of importance of the program.
Knowledge of the difference between preventative versus predictive.
Employee turnover, lack of lubrication knowledge, lack of documentation or implementing proper processes.
Convincing management to transform into actions the recommendations issued by a predictive maintenance program.
Communication, laziness, stuck in old ways.
Culture and education. A successful predictive maintenance program needs to have support from the top down. That culture starts with education. Predictive maintenance has maximum benefit when the management of a facility fully understands the value of a well-structured program. Like a safety program, if predictive maintenance becomes the “way things are done here,” you will find success.
Follow through with the program. Documenting long-term savings.
Developing cognitive knowledge of wearing elements.
Program budget, perception that cost savings will include staff reductions, overcoming resistance from time-based maintenance practices to performing maintenance on critical items as needed.
Resources: Financial, manpower. Cost-cutting: ROI calculations are changing the dynamic.
(1.) Obtaining clean, representative samples. (2.) Having knowledgeable people look at the data and understand why it is revealing. (3.) Understanding limits of detection of methods and instruments, condemnation limits set appropriately, preventing the over-analyzing of samples with too many tests that may not be relevant, timely feedback to equipment operator.
Lack of “gray hairs.”
Getting people to regularly check their processes and record the results so that tracking is even possible. Nobody wants to maintain or fix anything until it’s already broken, therefore preventive maintenance is difficult to enforce.
Maintaining the budget for PdM once the program is established.
Not applying PdM to the 20% of the maintenance of equipment that costs 80% of the annual budget!
Availability of equipment to be serviced.
Sampling consistency. Sampling timeliness. Sampling at all.
What best describes the lubrication programs you have seen in most manufacturing operations?
Reactive
60%
Predictive
12%
Preventive
28%
Predictive and preventive
28%
Based on responses sent to 13,000 TLT readers. Total exceeds 100% because some respondents chose more than one answer.
What new technologies and processes are helping predictive maintenance programs?
New testing equipment to perform on-site and real time analysis.
Web-based and wireless monitoring. The company I currently work for is trying wireless notepads to assign and record PdM work and create correctives.
Computer-storing data.
(1.) Outstanding teachers with credentials and 20-plus years experience in the field, the shop and the lab. (2.) Standards from ASTM and others delineating how to collect data and set limits for different threat levels. (3.) New software tools to import laboratory data and make reports facile.
On-site lubricant analysis vibration monitoring systems.
Technology doesn’t replace basic blocking and tackling.
Vibration monitoring. Thermographic inspection. Ultrasonic leak detectors.
SCADA/remote monitoring systems provides real-time feedback on equipment running conditions; this can be linked to vibration monitoring and even online oil analysis.
Entrainment speed control.
Easier-to-read reports and simpler reporting platforms.
Advanced vibration diagnostic. IR oil sample tester.
PQ Index, apps for my phone.
It’s more evolutionary than revolutionary. Recent changes include such technologies as shock pulse monitoring, improved OCM programs including electrostatic discharge monitoring, enhanced and more widespread oil filtration practices, improved equipment/lubricant labeling and sequestering.
Oil analysis software. Price-acceptable in-house testing equipment.
Digital refractometer to accurately measure H
2O content. Ultrasound to measure noise levels in bearings and shafts, advanced oil analysis.
Accurate portable on-site instrumentation to monitor in real time for heat, vibration and lubricant condition.
More availability of testing equipment and sources.
TAN and TBN. Patch testing.
Software to interpret results and establish correlations between signals automatically.
Portable equipment, low-cost microscopes, sensors on line.
Full-blown lab analysis establishing boundaries on the lubrication to establish condemning limits.
Barcode scanners for lube routes.
Expanded use of sensor technology.
Infrared camera, oil sampling vacuum.
Automation is driving down the amount of resources required for the testing. External laboratories are getting more responsive.
Phone and tablet apps.
Reliability programs.
Thermal-imaging cameras that are getting less pricey.
Computer-based maintenance scheduling.
Oil and coolant flush-out machines—they reduce time, money and waste.
Oil analysis technology is better than it was in the past. Vibration analysis can help prevent bearing failures.
The use of ultrasound routines for a quick detection of possible faulty equipment. These routines can precede and complement the vibration analysis routines.
Analysis equipment has become smaller, faster and more dependable.
Companies are sending Internet reminders for sampling or other activities.
Wireless sensors.
On-site data collection and analysis of data at the same time.
When an equipment problem appears in a manufacturing plant, which activity would you say has the most influence in the final decision?
Maintenance
14%
Production
53%
Both departments
28%
Flip a coin
9%
Based on responses sent to 13,000 TLT readers. Total exceeds 100% because some respondents chose more than one answer.
Sounding Board is based on an email survey of 13,000 TLT readers. Views expressed are those of the respondents and do not reflect the opinions of the Society of Tribologists and Lubrication Engineers. STLE does not vouch for the technical accuracy of opinions expressed in Sounding Board, nor does inclusion of a comment represent an endorsement of the technology by STLE.