Grease: A Niche Market Opportunity
Chuck Coe | TLT Webinars May 2015
A look at the benefits of grease, how it's different from oil and why no two greases are alike.
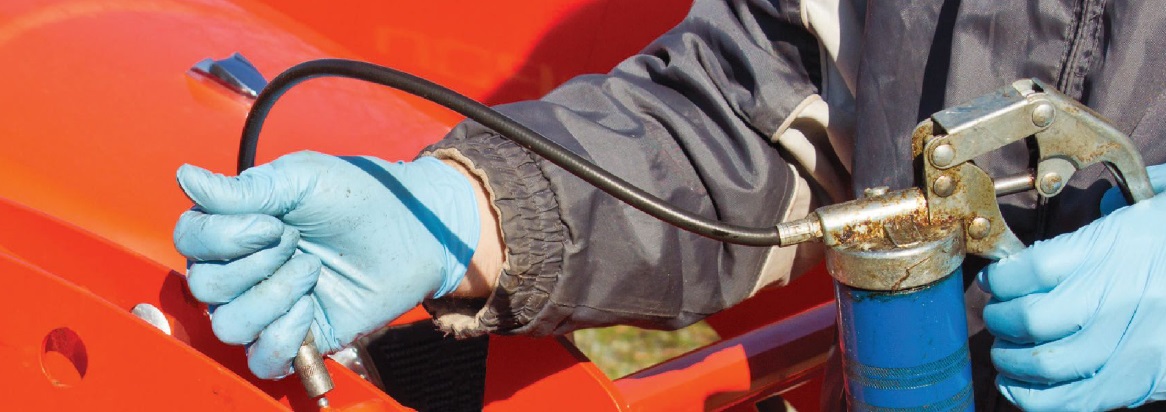
www.canstockphoto.com
KEY CONCEPTS
•
Lubricating oils are mainly composed of base oils and additives while greases are composed of these two elements but also include the thickener.
•
Greases offer the flexibility to utilize different types of thickeners, base oils and additive packages.
•
Grease offers the opportunity to customize to meet specific application needs.
MEET THE PRESENTER
This article is based on a Webinar originally presented by STLE University on August 20, 2014. “Grease: The Niche Market Opportunity” is available at
www.stle.org: $39 to STLE members, $59 for all others.
Chuck Coe holds a bachelor’s of science degree in chemical engineering from Pennsylvania State University, along with NLGI CLGS and STLE Certified Lubrication Specialist™ professional certifications. He worked for Mobil and ExxonMobil for 32 years, including six years as ExxonMobil’s grease technology manager and many years as an industrial oil and grease formulator and technical advisor. He retired from ExxonMobil and launched Grease Technology Solutions LLC in 2009, a grease training and consulting business. He is the immediate past president of NLGI and is the grease education course chair of STLE. He has authored several technical papers and articles on grease, and received Best Marketing Paper and Best Paper awards from both NLGI (2008) and ELGI (2009), and the John A. Bellanti Memorial Meritorious Service Award in 2012 from NLGI. He can be reached at
chuckcoe@grease-tech.com.
Chuck Coe
THERE ARE NUMEROUS INDUSTRY AND OEM standard specifications for engine oils, gear oils, hydraulic oils, turbine oils, etc. Standardized specifications are very useful to the end-user, simplifying product choice and ensuring a certain level of performance. Unfortunately for the marketer, standards also reduce the opportunity for differentiation by facilitating cross-referencing and ultimately fostering product commoditization.
Greases are different. There are virtually no industry standard specifications, and as a result no two greases are exactly alike. Grease performance can vary not just due to formulation differences but also as a result of the manufacturing equipment and techniques used. The wide variety of grease applications creates a major opportunity for grease product differentiation and access to a high margin sector.
GREASE VERSUS OIL
Let’s compare greases to oils for a moment. As a price of market entry, many lubricating oils must meet certain industry and/or OEM standard specifications, and, as a result, they are subject to “read-across” to competitive products. This leads to commoditization and minimizes opportunities for differentiation. Also, lube oils are fairly straightforward to manufacture in a consistent fashion, meaning that manufacturer cannot easily achieve a performance advantage through manufacturing process or equipment advances. Yes, lower manufacturing costs can be achieved, but technical performance of the lube oils will not likely be achieved.
Greases on the other hand present a very different picture. Most greases are not formulated to meet an industry standard specification since there really is only one such spec in the marketplace—the NLGI GC-LB certification mark (more on that later). There are a wide variety of thickener types and formulation approaches to meet a given application challenge. Manufacturing grease is much more challenging and complicated than blending oil, which provides opportunities for manufacturers to achieve improved performance compared to similar competitive products through improved process and/or equipment utilization. And, finally, even the applications in which greases are used are more varied and, in some cases, unusual and challenging in comparison to oil applications.
GREASE: THE BASICS
So what is grease? According to the NLGI, grease is “a solid to semisolid product of dispersion of a thickening agent in a liquid lubricant. Additives imparting special properties may be included.” Without stress, it stays where it is put and is non-Newtonian. A minimum level of stress must be applied (the yield stress) before the grease starts to move, after which it behaves more like a Newtonian fluid (
see Figure 1).
Figure 1. Difference between Newtonian and non-Newtonian fluid.
Grease is used in as much as 90% of rolling element bearings, according to bearing industry lore. It is used instead of oil for a number of rheological reasons:
•
Its semi-solid form allows it to stay in place.
•
Grease resists leakage and loss.
•
Grease forms a physical barrier seal against airborne contaminants such as moisture and dirt.
•
Grease can resist physical removal by water spray or centrifugal forces.
•
Grease typically forms thicker lubrication films than oil with the same base oil viscosity.
In addition, grease can be formulated with solid additives such as molybdenum disulfide, graphite or PTFE.
On the other hand, oils are preferred when heat removal, dirt removal and seal lubrication are all necessary or when high speeds exceed grease apparent viscosity limitations.
So what makes grease different from oil? Lubricating oils are, for the most part, composed of base oils and additives. Greases are also composed of these two elements but also include the critical third component: thickener. As with an oil lubricant, the base oil provides the lubricating film with mineral, synthetic or biobased oils or a combination thereof. As with an oil lubricant, the additives are present to enhance lubricant performance. And with a grease, the thickener provides body and structure with either soap or non-soap components.
The wide variety of applications for lubricating greases call for an equally diverse range of compositions (
see Figure 2). Base oil typically makes up somewhere between 80%-95% of a grease. Thickener content may vary considerably from as low as 2% for semifluid grease to 20% or more for stiffer greases or greases made with certain types of thickeners. Additive content can vary from almost nothing to more than 10% when solid additives such as molybdenum disulfide are incorporated.
Figure 2. The differences in the typical grease composition.
The base oil is extremely important in grease because it provides the lubricating film as it “bleeds” from the thickener. Base oils can be any of the same ones used in oil lubricants and cover a range from about 10-1,500 cSt at 40 C or more. The oil soluble additives used in grease are, for the most part, the same ones used in oil lubricants to improve corrosion control, load carrying and wear prevention and oxidation resistance. Greases also can accommodate solid additives such as molybdenum disulfide, graphite and the like. A variety of different polymers also may be incorporated into grease to improve adhesion and water resistance. A wide variety of different thickener types are used in grease, which are broadly divided into soap thickeners and non-soap thickeners (
see Figure 3). As the figure shows, most are soap-thickened, and most of those are lithium or lithium complex thickeners. However, the smaller volume thickener types exist for some reason—most likely they solve a lubrication challenge at optimal cost.
Figure 3. Grease soap and non-soap thickener technologies.
So how does an end-user choose a grease for a given application? Or for that matter, how does a formulator choose the best components to design a grease to meet an end-user’s challenge? Choices include thickener type, base oil type, base oil viscosity, consistency, additive chemistry, need for polymer and other parameters that might be important.
Thickener type is usually the first decision that is made based on a number of factors. In applications where mechanical stability is important (high-speed rolling element bearings for instance), thickeners like lithium and lithium complex may be good choices. In high-water wash applications such as paper mill wet ends, lithium and lithium complex thickeners also are frequently chosen. High-load or wet environments like mining may lead one to choose calcium sulfonate thickeners. And for high temperature or fill-for-life sealed bearings, polyurea thickeners may be the best choice.
Base oil type and viscosity choice is based on similar factors to those seen in oil-lubricated applications. Viscosity is key and is based on load, speed and temperature of the application. Extreme temperatures may dictate the use of synthetic base fluid, while special requirements may lead to the use of biobased or food grade base oils.
Additives are selected based on requirements to enhance oxidation stability, water or corrosion resistance, load carrying, etc. All in all, grease additive formulation is a careful balancing act—you must provide the necessary performance in all areas without compromising thickener performance.
OEM SPECS AND STANDARDS
Now let’s discuss OEM specifications and standards. There are numerous ones for oils, which
define performance requirements:
•
Auto engine oils. API, ILSAC and ACEA service ratings (SL, SM, SN, etc.).
Performance requirements and test methods are established by vehicle and engine manufacturers, technical societies and trade associations.
•
Auto gear oils. API service ratings (GL-4, GL-5, MT-1, etc.) Each designation refers to the
performance required of a gear lubricant for a specific type of automotive service.
•
Industrial oils.
o
Steam or gas turbine oils. D4304 standard spec for mineral steam or gas turbine oils. This specification is intended to
define the properties of mineral oil-based turbine lubricating oils that are
functionally interchangeable with existing oils of this type.
o
Hydraulic oils. D6158 standard spec for mineral hydraulic oils. This specification
defines the requirements of mineral oil-based hydraulic fluids that are compatible with most existing machinery components.
o
Gear oils. AGMA 9005-E02. This standard provides the end-user, original equipment builder, gear manufacturer and lubricant supplier
with guidelines for minimum performance characteristics for lubricants suitable for use in general power transmission applications. In addition, there are DIN 51517-3 and OEMs such as David Brown, Flender, Winergy and Cincinnati Machine.
For greases, there are far fewer standards. NLGI GC-LB (
see Figure 4)
specifies several levels of performance for automotive applications, DIN 51825 provides a classification system according to
performance levels and formulation components and, finally, there are individual OEM specs as well. GC-LB is primarily recognized in the U.S., and DIN is used predominantly in Europe, while OEM specs for greases are not well publicized.
Figure 4. NLGI GC-LB specifies several levels of performance for automotive applications.
COMMODITIZATION OF OILS
So what do all of the industry standards and specs for oil do? They’re definitely great for the end-user, making product choice and interchangeability much easier. But take a look at the cross-reference chart in Figure 5. It is based on the assumption that an oil of a given viscosity grade in a given category is equivalent to every other product in that category with the same viscosity. For example, are the ISO 46 antiwear hydraulic oils from all the listed suppliers equivalent? Maybe so, maybe not, but the cross-reference tables assume so. And, even more dangerous, this table indicates that all the listed EP lithium greases are equivalent. Their equivalency is based on EP additization and NLGI grade—not even a mention of base oil viscosity, which is kind of important!
Figure 5. The lubricant cross-reference chart shows equivalence of oils.
DANGERS OF ‘READ-ACROSS’ FOR GREASES
Let’s look at two examples of why one should be wary of reading across any equivalency in greases:
1.
Manufacturing impact on identical formulations
2.
Impact of formulation differences between two greases with similar-advertised claims.
First a bit of background on grease manufacturing—it is
far more complex than oil blending and is
just as important as the formulation in providing the desired grease properties and performance. Grease manufacturing uses a variety of equipment that can include kettles, contactors, other process vessels, pumps and milling equipment. It also can be manufactured using continuous processing.
In our first example, two greases are made with identical formulations (same thickener, same base oil, same percentages, no additives). The only difference between the two is the processing conditions. The results are rather startling (
see Figure 6). Under one set of operating conditions, a typical NLGI 2-grade grease is formed, but under less optimal conditions a semi-fluid 00-grade grease is formed. This clearly illustrates the importance of manufacturing technology and process control to grease performance.
Figure 6. A typical NLGI 2-grade grease is formed, but under less optimal conditions, a semi-fluid 00-grade grease is formed, which shows the importance of manufacturing technology and process control to grease performance.
In our second example, two commercial polyurea greases sound identical based on product data sheet claims:
•
Both are NLGI 2 grade
•
Both contain approximately 115 cSt at 40 C mineral base oil
•
Both claim over 240 C dropping point
•
Both are recommended for high-temperature lubrication of ball and roller bearings, particularly for electric motors.
However, these greases are anything but equivalent in performance. In particular, see the vastly different shear stability in the 100,000 stroke extended worker penetration test (ASTM D217), as shown in Figure 7. Polyurea grease A softens just over one NLGI grade in this test, while grease B softens nearly three grades, from a No. 2 grade to almost 00 grade. Other testing shows a similar performance disparity in oil bleeding tendency at elevated temperatures. The bottom line is that even though these two greases look very similar when comparing their technical data sheets, they will not perform equivalently in most applications.
Figure 7. The vastly different shear stability in the 100,000 stroke extended worker penetration test.
GREASES AS PROBLEM SOLVERS
In order to truly realize the potential of grease, we will examine several case studies which show how different greases have been used to solve application problems.
Case Study 1
•
Application. Heat treatment furnace bearings, temperature exceeding 100 C.
•
Problem. Grease drying out, regreasing every eight hours, two bearing failures per day, causing downtime and production loss.
•
Grease in use. Various lithium greases.
•
Recommendation. Lithium complex grease with ISO 1500 PAO base oil.
•
Result. No drying of the bearings, regreasing intervals increased to 48 hours and no bearing failures; savings of $21,000 per annum.
Case Study 2
•
Application. Pipe mill bearings.
•
Problem. Water washout with average of four bearing failures per month, causing downtime and production loss.
•
Grease in use. NLGI #2 lithium EP grease with ISO 150 mineral base oil.
•
Recommendation. NLGI #2 lithium complex EP grease with ISO 220 base oil and polymer enhancement.
•
Result. No churning of grease due to water contamination, bearing failure rate reduced to one per month. Savings: $5,500 in bearing costs and $20,000 in lost production.
Case Study 3
•
Application. Paper mill wire, press section, dryer section, heat recovery, coating section, electric motors for rolls, fans, shaft bearings.
•
Problems. Oil bleed (electric motor grease) and desire to consolidate to one grease.
•
Grease in use. NLGI #1 lithium complex, ISO 460 mineral oil for PM bearings and NLGI #2 lithium complex, 115 cSt at 40 C mineral oil for electric motors and fans.
•
Recommendation. Consolidate to NLGI #1 lithium complex ISO 460 mineral oil grease.
•
Result. Excessive softening in electric motors and fan bearings.
•
New recommendation. NLGI #1.5 lithium complex, ISO 220 PAO base fluid grease.
•
Result. NLGI No. 1.5 provided satisfactory pumpability in centralized systems due to ISO 220 PAO base oil and optimized viscosity for both PM and EM bearings; successful consolidation to one grease.
Case Study 4
•
Application. Steel mill reversing mill hot rolls, four high mill with four-row cylindrical backup roll bearings, about 3-4-in. diameter, bearings about $250,000.
•
Problem. Excessive water washout.
•
Grease in use. NLGI No. 1 lithium EP, ISO 150 mineral oil based grease.
•
Recommendation. NLGI No. 2 lithium complex, ISO 680 mineral oil grease.
•
Result. Greatly reduced water washout problem but a new problem emerged with acid etching on backup roll bearings.
•
New recommendation. NLGI No. 1 calcium sulfonate, ISO 460 mineral oil grease.
•
Result. Even less water washout and virtually eliminated acid etching on backup roll bearings due to improved water absorbing properties.
The opportunity:
•
Completely different types of greases can work well in an application.
•
There can be different solutions to a given operating problem.
•
Grease offers the opportunity to customize to meet specific application needs.
•
A different brand of an apparently equivalent grease can perform differently.
•
You won’t sell it by claiming it meets an industry spec, but by proving performance “in the field.”
A WORD ABOUT PRODUCTION TRENDS AND MARGINS
Worldwide grease production has been fairly steady for the last four years between 2.5 and 2.6 billion lbs. (
see Figure 8). Noteworthy trends are:
•
Lithium and lithium complex greases make up about 75% of worldwide grease production.
•
Lithium complex and polyurea thickeners are growing in use at the expense of most other types.
•
Most calcium and calcium complex greases are older technology and their usage continues to decline.
•
Calcium sulfonate grease usage is increasing particularly due to its good inherent water resistance.
Figure 8. Charts show that recent worldwide grease production has been fairly steady over the last four years.
Margins are healthy for greases:
•
Generic/commodity greases: $100-$200/barrel
•
Premium technology high-performance greases: $200-$500/barrel
•
Special purpose greases (food grade, biobased, etc.): $500-$1,000/barrel
•
Synthetic, extreme service, niche application greases: more than $1,000/barrel.
SUMMARY
Greases offer the flexibility in formulation to utilize different types of thickeners, different types of base oil, component-based or additive package technologies, polymer enhancement and incorporation of solid additives. They also offer the flexibility in manufacturing processes to vary performance significantly—even with an existing formulation—and the flexibility in product specifications to meet exactly what a customer or application requires rather than what a rigid industry standard dictates. Greases offer an opportunity to capture healthy margins compared to oil lubricants.
Chuck Coe is the president of Grease Technology Solutions LLC who can be reached at chuckcoe@grease-tech.com.