The advantages of perfluorinated polyethers
Stuart F. Brown, Contributing Editor | TLT Webinars March 2015
Their unique attributes make them the lubricant of choice for many demanding applications.
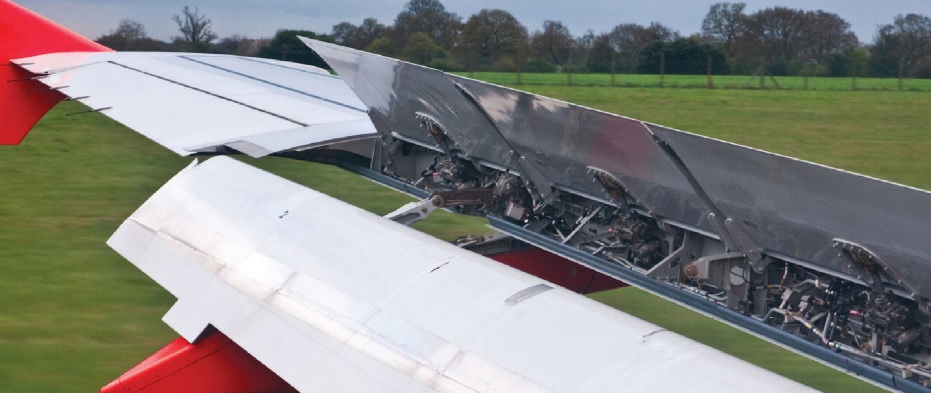
www.canstockphoto.com
KEY CONCEPTS
•
PFPEs possess excellent lubricity and load-carrying capability, are non-flammable and are compatible with most plastics and elastomers.
•
Due to the expense involved in mining and synthesizing their ingredients, PFPEs are costly to make and purchase.
•
Choosing the correct viscosity for PFPEs is critical and depends on the speeds and loads of the application.
MEET THE PRESENTER
This article is based on a Webinar originally presented by STLE University on July 16, 2014. “Fluorocarbons” is available at
www.stle.org: $39 to STLE members, $59 for all others.
Thomas Blunt is responsible for technical service and product development for DuPont™ Krytox® performance lubricants. He joined DuPont in August of 2012. Blunt has been involved in research and development and technical support for the lubricant industry for over 20 years. He holds a bachelor’s of science degree in chemistry from University of Wisconsin–Milwaukee. He can be reached at
Thomas.J.Blunt@dupont.com.
Thomas Blunt
SOME DEVICES—LET'S SAY ELECTRIC MOTORS, VALVES or other equipment that may be difficult to gain access to—can end up not getting the lubricant they need to live long and trouble-free service lives. In some cases, upkeep chores are postponed because they are a pain in the neck to perform, while at other times components fail because they were out of sight and out of mind and never got the routine lubrication they needed. They were forgotten.
Consider bearings that must function in extreme heat or cold conditions in applications such as missiles, gyroscopes or jetliner wing-flap actuators. Think of parts that absolutely must not burn when used in an oxygen-rich environment or vacuum pumps where lubricant outgassing is not acceptable. These are some of the exotic mechanisms that rely on fluorocarbon lubricants for durability and long maintenance intervals.
The information in this article draws on an STLE Webinar originally presented by STLE University July 16, 2014, by Thomas Blunt of DuPont. He is responsible for technical service and product development for the company’s Krytox family of high-performance fluorocarbon synthetic lubricants, which are perfluorinated polyethers (PFPEs).
If one were to construct a lubricant pyramid chart with volume of usage running across the base and cost running up the sloping sides, the expensive PFPEs would find themselves at the peak of the pyramid. The pyramid’s broad base would be occupied by low-cost lubricants derived from petroleum oil. And the middle slopes of the pyramid would be populated by silicones, polyalkylene glycols and polyalphaolefins of intermediate cost.
Due to the expense involved in mining and synthesizing their ingredients—some of which are hazardous—PFPEs are costly to make and purchase, winning them their perch at the top of the pyramid. But their unique attributes make them the lubricant of choice for all sorts of demanding applications.
PFPEs are closely related to polytetrafluorethylene (PTFE), which is commonly known as Teflon. PTFEs are compounded from carbon and fluorine molecules. Adding an oxygen molecule to the mix transforms a PTFE molecule into a PFPE. The PFPEs have a long list of positive attributes. They have the highest stability of the fluorocarbons, low volatility and a wide temperature range of operation. They possess excellent lubricity and load-carrying capability, are non-flammable and are compatible with most plastics and elastomers.
The one shortcoming of PFPEs is the small number of additives that can be dissolved in them. Dupont makes some PFPE additives itself to help users fit the lubricant to their needs. DuPont’s PFPE molecules are shielded against acid attack by the addition of a CF3 group. The company makes its shielded “K” type of lubricants under the Krytox brand name, while two other makers produce three non-shielded varieties of lubricants known as D, Y and Z types.
Lubricants control friction, which is the source of wear in mechanisms. When a device containing bearings is turned on, for example, the moving parts are resting against one another with metal-to-metal contact occurring at the high points of the parts’ mating surfaces. This condition is known as boundary lubrication, and friction is high. As the machine spins faster an oil film begins to develop on the mating surfaces, reducing the friction between them in a state known as mixed lubrication. As the parts spin yet faster, a full oil film forms between them. The parts make no contact with each other in this final low-friction condition, called hydrodynamic lubrication. The same effect is seen in hydroplaning when a car is driven too fast through a deep puddle and temporarily loses steering control as the tires ski atop the water’s surface.
An example of a PFPE application is in grease used to lubricate ball bearings. PFPE grease is made by combining PFPE liquid with PTFE powder and other additives such as sodium nitrite, which acts as an antiwear/anticorrosion additive and molybdenum disulfide as an extreme pressure additive.
PFPEs have excellent wear and load-carrying capacities. This can be validated with the ASTM D2783 four-ball EP test where one steel ball clamped in a spinning chuck is forced down on three stationary steel balls locked in a test fixture and bathed in the lubricant being tested. The ball in the chuck is rotated at 1,800 rpm as higher and higher loads are applied. Eventually wear scars begin to form on the contacting surfaces of the steel balls, followed by welding together of the four balls due to frictional heating. Wear scar depth on the PFPE sample, at 0.36 mm, was half the 0.69-mm scar depth formed when a petroleum oil sample was tested.
The Falex four-ball test is used to determine the relative wear-preventing properties of lubricating fluids and greases in sliding and rolling applications.
DuPont performed another test, placing a PFPE grease sample and a hydrocarbon grease sample in an oven at 232 C for 40 hours. The hydrocarbon sample developed surface cracks and a brownish color and lost 40 percent of its weight. Demonstrating its high temperature stability and very low volatility, the PFPE sample remained unchanged in appearance and lost no weight.
Hydrocarbon grease sample that has been in the oven.
In the ASTM D3336 test, which looks at life of lubricating greases in ball bearings at elevated temperatures, ball bearings were rotated at 10,000 rpm under hot conditions. A variety of competitive hydrocarbon grease formulations lasted from 400 to 3,000 hours in this test while three PTFE/PFPE greases lasted from 2,145 to more than 5,000 hours, and a fourth sample was still in good condition after three years. Blunt says, “The material had run for more than 25,000 hours and we had to turn it off because there were other needs for the test equipment.”
Machine used by DuPont to test ball bearing grease for more than 5,000 hours.
Sometimes components lubricated with PFPE but forced to operate in a severe boundary lubrication condition exhibit a phenomenon called tribocorrosion. The tipoff is often a granular brownish deposit nicknamed “brown sugar” that gives a bearing a dry, rusty appearance. The extreme pressures and temperatures in these conditions can break apart the PFPE molecules, releasing fluorine, which reacts with the iron in the metallic surface to form iron fluoride.
Iron fluoride is a relatively soft iron compound that will serve as a sacrificial surface layer preventing scoring and seizure, much like traditional extreme pressure additives. This active chemistry allows for smoothing of the mating surfaces, resulting in “break-in” that will ensure long, trouble-free service. Eventually, however, iron fluoride’s acid property can prompt continuing decomposition of PFPE molecules until there’s insufficient lubricant remaining. Therefore, evidence of tribocorrosion is not considered a significant issue in properly designed applications, Blunt says, but in the case of a bearing with significant negative clearance, it can help trigger a catastrophic failure once the grease has been totally consumed. This is an issue for all types of lubricants and not just PFPEs.
There are some considerations to remember when specifying a PFPE lubricant for an application. The first is that the parts being lubricated cannot have aluminum bearing surfaces and must be purged of all hydrocarbon or other organic residues by thorough cleaning with non-chlorinated solvents. Choosing the correct viscosity is also critical and depends on the speeds and loads of the application.
Bearings need the correct amount of grease in order to work properly. Because PFPEs have twice the density of other oils and the greases, bearings must be filled with new lubricant by volume and not by weight. Also, because PFPEs form thicker films with lower thermal conductivity than traditional lubricants, bearings may be found to run slightly hotter than they did with a previous lubricant, but the excellent thermal stability of these lubricants is able to handle the higher temperatures. Since PFPE lubricants are so good at forming film layers between parts, a smaller amount of lubricant may be used in some applications, or a lubricant with a lower viscosity rating may be specified.
Blunt predicts that customer concerns about PFPE lubricant purchase costs will be more than offset by the growing popularity of lubricated-for-life applications and the appeal of reducing machinery downtime by making longer relubricating intervals routine.
Stuart F. Brown is a free-lance writer who can be reached at www.stuartfbrown.com.