20 Minutes With Wayne Mackwood
Karl M. Phipps, Managing Editor | TLT 20 Minutes March 2015
Chemtura’s grease and detergents technology manager discusses the future development of calcium sulfonate complex greases and their use in different industrial applications.
WAYNE MACKWOOD - The Quick File
Wayne Mackwood is the technology manager for detergents and grease at Chemtura Corp., and is based in Toronto. He is a recognized expert in the design, manufacture and use of calcium sulfonate complex grease. For over 20 years he has developed more than 150 grease formulations for use in the mining, steel production, pulp and paper, power generation, transportation, food processing and marine industries.
Wayne has spent the majority of his career in R&D as a scientist but has also held roles in marketing and asset management. He has authored or co-authored more than a dozen technical papers, two patents and delivered more than 20 presentations at technical conferences and seminars around the world.
Wayne is a member of STLE, NLGI and ELGI. He previously served on STLE’s Board of Directors. Currently he is serving on NLGI’s Board of Directors.
He holds BESc and MESc degrees in materials science, with a focus on tribology, from the University of Western Ontario.
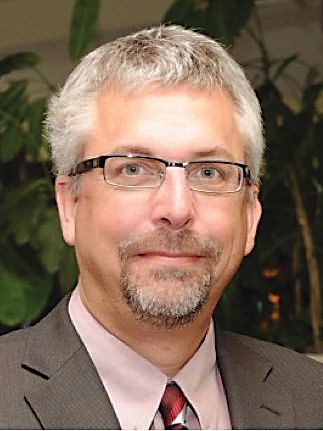
Wayne Mackwood
TLT: How did you end up working with grease?
Mackwood: I have to admit that not a lot of engineers start out thinking that they will end up studying or working with lubricants. I certainly didn’t when I started in materials engineering. It is good to see that professional societies such as STLE and others are trying to change that by raising awareness about the field of lubrication as early as possible.
In my case, I took a third-year summer researcher position with Dr. John Sheasby at the University of Western Ontario, studying the mechanisms of zinc dithiophosphate (ZDDP) in lubrication. That opportunity eventually led to my involvement in a fourth-year project working with ZDDPs and later to a master’s degree studying tribology.
The word
tribology on my resume caught the eye of Ron Muir at Surpass Chemicals in Toronto (which was part of Witco at the time) and next thing I knew I was working with grease, among other things, in their R&D group. That was more than 22 years ago and I haven’t looked back since.
The grease that I work with at Chemtura is calcium sulfonate complex grease. It has been an amazing experience over the years dealing with numerous customers, from one-person companies to the world’s largest, developing new products for an array of applications.
TLT: What is calcium sulfonate complex grease?
Mackwood: Calcium sulfonate complex grease is one of a handful of thickeners that are commonly used to lubricate moving components. It has been discussed since the 1960s, but the early products were more suitable to coatings and were used as such. It wasn’t until the 1980s that Ron Muir developed what we now call calcium sulfonate complex grease.
Since that time, there have been numerous papers and patents on the subject, but the majority build on the technology that Muir developed. Most patents and papers relating to the technology describe it as the reaction of an overbased calcium sulfonate, a C12 detergent sulfonic acid, 12-Hydroxystearic acid, a promoter package including water, acetic acid and/or an alcohol, calcium borate or calcium phosphate, and an antioxidant. The sulfonate itself plays a critical role in the grease formation. Its starting total base number (TBN) (300, 400 or 500) and its structure (the degree of synthetic, natural, branched, linear, dialkyl) affect properties, performance, cost and availability.
Other components, such as additional calcium carbonate, AW and EP agents, copper corrosion inhibitors, PPD, water-resistant polymers, tackifiers, among other additives, also can be employed in the formulation, depending on the desired end properties. The fluids used to make this grease include API Group I-IV basestocks. The API Group I and II basestocks can be either paraffinic or naphthenic. To date, there has been little commercial success with the use of Group V basestocks, particularly natural and synthetic esters, due to the chemistry and the reactive processing conditions (alkaline, water, heat) in making the grease.
Calcium sulfonate complex grease.
TLT: What are the key properties of calcium sulfonate complex grease and where do they come from?
Mackwood: The technology finds its home where there are high loads, high temperatures and/or water. Therefore, its key properties are load-carrying, thermal stability and water resistance. These properties come from several parts of its structure. The sulfonate soap forms an inverse micelle around the calcium carbonate. This highly polar soap structure attaches itself to the lubricating surface, providing some protection of the surface from corrosion through a barrier film. But it is the calcite calcium carbonate found within the micelle of the sulfonate soap that provides the heavy lifting.
Apart from providing the rheological change in the grease, from a Newtonian (fluid) to non-Newtonian (pseudo plastic thixotrope) grease, the calcite provides load-carrying and corrosion resistance. Its hexagonal, close-packed, crystal structure gives the calcite crystals an easy shear plane and therefore excellent lubricity—both under wear conditions and under much more severe EP conditions (
see Figure 1). It is also effectively non-reactive and can lubricate many different sliding materials. Along with the polar sulfonate, the calcite particles provide excellent corrosion prevention properties. They are an excellent source of alkalinity, quickly neutralizing any acidic corrosion products. They are also wafer-like in structure and lay down on the surface, providing an excellent barrier to water (
see Figure 2).
Figure 1. Calcite hexagonal close-packed crystal structure.
Figure 2. Corrosion resistance of calcium sulfonate complex grease.
Unlike many other grease types, the soap structure of calcium sulfonate complex grease absorbs water when mechanically mixed. It will easily absorb 20-50 percent water. What is more interesting here is that the mechanical stability of the grease remains minimally affected. Even at 50 percent water, depending on the base fluid used, the grease will not typically change in consistency more than 25 penetration units. If the other grease types manage to absorb that much water, they generally soften several times that amount, sometimes becoming quite fluid in the process. It is this stability in the presence of water that gives the grease its excellent water resistance (
see Figure 3).
Figure 3. Mechanical stability with water.
Finally, the grease has excellent high-temperature properties. While it still requires the use of a good antioxidant (typically aminic and/or phenolic type, as well as others provide oxidation inhibition), its thermal stability at high temperatures is key to its high temperature performance. It has a high dropping point (the temperature at which the grease matrix can no longer hold the oil) in excess of 300 C, but it also appears to have very good high-temperature rheological properties. It is believed that the calcium borate or calcium phosphate helps to control the rheological properties at elevated temperatures.
TLT: What are the application areas for calcium sulfonate complex greases?
Mackwood: Calcium sulfonate complex grease is used wherever it is hot, wet or it is subjected to high loads. It has been formulated for applications in steelmaking and processing, pulp and paper, railroad, marine, mining and automotive. While we have developed formulations for use in many industries, the two that stand out for me are power generation and food processing.
Prior to Chemtura introducing calcium sulfonate complex grease to the food market, the majority of the products available were based on anhydrous calcium grease for low-temperature applications or aluminum complex grease for high-temperature applications. Other thickeners included clay and polyurea. But the selection of corrosion, AW and EP agents was limited, and the performance of the products was therefore also limited. Calcium sulfonate complex grease, with all its inherent performance properties, became an ideal choice in food-grade applications.
Power-generation applications posed a different set of problems. The grease being used at the time for critical safety systems had been shown to be unsuitable, particularly in mechanical stability. Through years of development and testing, we showed that calcium sulfonate complex grease is very radiation resistant and remains very stable over years at elevated temperature and in the presence of steam. It is now the primary product in grease lubricated, safety-related, motor-operated steam valves.
TLT: What applications would you not recommend for calcium sulfonate complex grease?
Mackwood: Obviously no grease or lubricant can be used everywhere. One area that pushes the boundaries of a calcium sulfonate complex grease is the aerospace industry. The high thickener content, along with the sulfonate itself, is not conducive to providing good torque at very low temperatures. It can meet a -54 C torque requirement with the right process and fluid conditions but with the current technology, lower temperatures will pose a challenge. Many military specifications require -73 C operability.
The other area where I wouldn’t recommend it is in low-noise applications. Its high thickener content, stemming from the high solids content of crystalline calcium carbonate, is not conducive to a low-noise, high-precision bearing environment. One customer who tested it for noise described it as “rocks in a dryer.” Yes, you can tightly control the reaction process, mill the product, filter it (to a degree) and get a grease that won’t plug inline filters. But consistently manufacturing a product that would best be made in a clean room and not contain metal is going to be difficult in this technology.
TLT: What technology does calcium sulfonate complex grease compete with most often?
Mackwood: Calcium sulfonate complex grease has been found useful in most applications. Therefore, by and large, it will compete with most other thickener types. The most common thickeners that we see it competing with are lithium complex, aluminum complex and polyurea. They are the higher-performance technologies. Much of that is driven by application and to that end one could also include lithium grease in that list. It competes with lithium complex grease in most bearing applications and industries, including pulp and paper, steel, mining and general industry.
Aluminum complex is popular in the steel industry, at least in North America, and in mining, but recently the food-processing industry has become the primary area of competition. It offers improved wear, EP and high-temperature properties over aluminum complex in the food-processing industry.
It is generally quite compatible with lithium and lithium complex grease but will potentially face compatibility issues with aluminum complex and polyurea. In general it is always best to review the compatibility with the product it is replacing and even run some tests if the application is critical.
TLT: What do you foresee as the future of this technology?
Mackwood: As a simple response—I would expect to see continued growth. While it currently occupies less than 2 percent of global grease production, according to the latest NLGI grease production survey, its growth in the BRIC region, particularly China, is phenomenal. If you ignore the lithium behemoth (75 percent of the world production), the go-to products are either calcium sulfonate complex or polyurea.
While lithium metal costs (for grease) are relatively stable and have been for some time, the potential for change with lithium-battery production has pushed many manufacturers in China and India to start looking at these two grease types as alternate technology for future growth. We will certainly be continuing to look for new applications and markets for this technology, which is one of the reasons why Chemtura has built a new grease plant in China.
I would also expect to see continued growth in areas such as marine, steel and particularly mining. Mining is surprisingly underrepresented by calcium sulfonate complex grease.
You can reach Wayne Mackwood at wayne.mackwood@chemtura.com.