One word: Plastics ― Two words: Hydraulic oil
Jeanna Van Rensselar, Contributing Editor | TLT Feature Article January 2015
New technological advances are taking shape to control hydraulic oils used in plastic-injection molding machines.
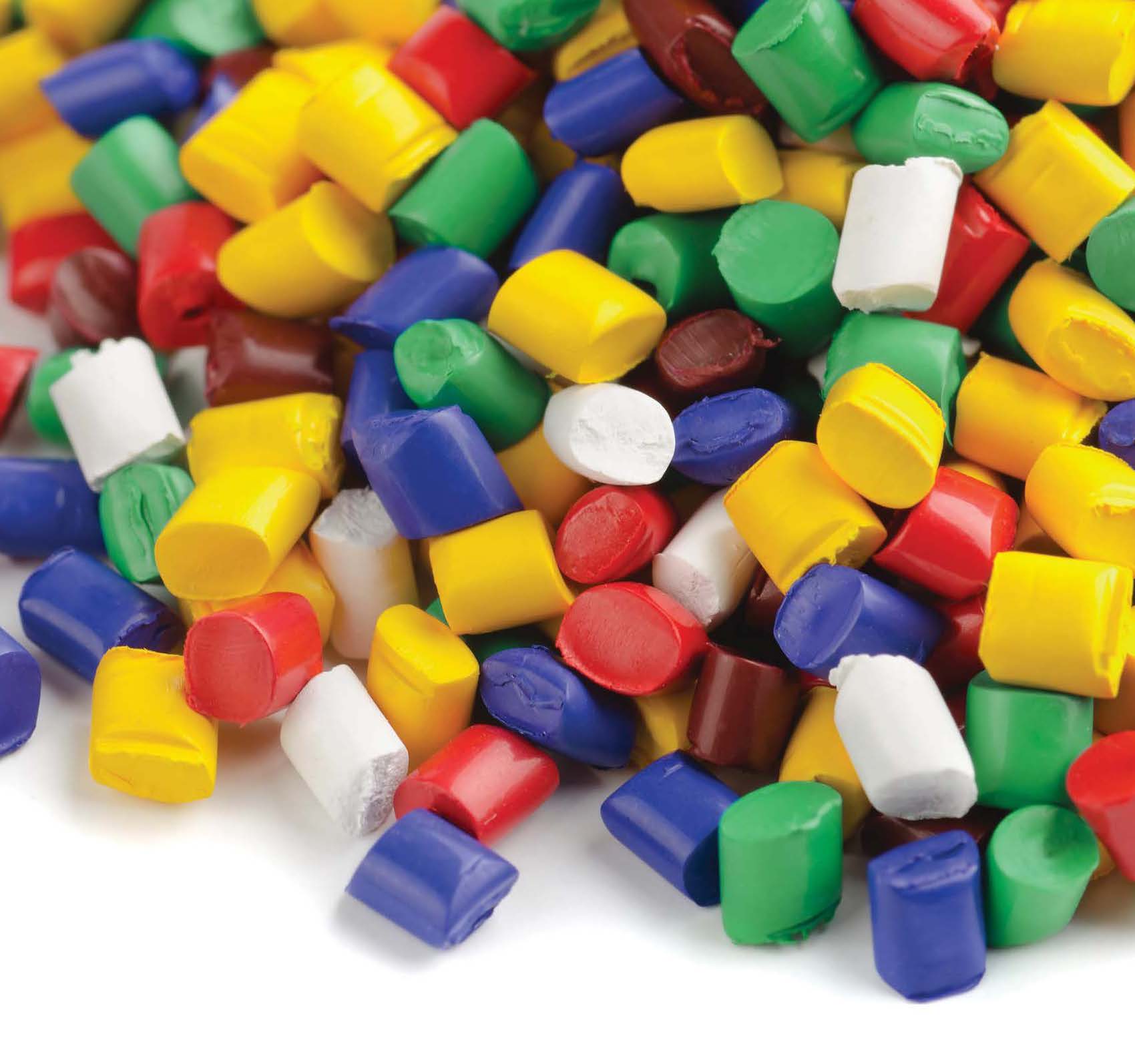
Solid plastic, usually in the form of pellets, is fed into the injection unit, which heats them into a liquid.
www.canstockphoto.com
KEY CONCEPTS
•
Global demand for plastic-injection molded products is expected to increase 5 percent annually through 2020.
•
The condition of the hydraulic oil can be a primary determinant of the finished part quality.
•
Hydraulic-plastic-injection molding machines are still prevalent, however, hybrids with servo-powered hydraulics are quickly gaining market share.
Mr. McGuire: I want to say one word to you. Just one word.
Benjamin: Yes, sir.
Mr. McGuire: Are you listening?
Benjamin: Yes, I am.
Mr. McGuire: Plastics.
Benjamin: Exactly how do you mean?
Mr. McGuire: There’s a great future in plastics. Think about it. Will you think about it?
In the preceding dialogue from the 1967 movie
The Graduate, Mr. McGuire turns out to be a sage. And here’s why. The U.S. plastic processing industry is comprised of about 20,000 plastics processors that employ 1.5 million workers, making it the country’s fourth largest industry. The U.S. also dominates the plastic processing industry, which is nearly two times the size of the entire European Union industry. Is there a great future in plastics and the hydraulic oil that makes the industry possible? Research says absolutely.
A plastic-injection molding machine (IMM) includes three basic parts: the mold, the clamping unit and the injection unit. The process involves feeding solid plastic (usually in the form of pellets) into the injection unit, which heats the material to a liquid. The injection unit forces the melted plastic into a clamped (usually two-sided) mold cavity where it is pressurized and remains until it cools. While the process itself is simple, controlling aspects such as the temperature and pressure and maintaining the integrity of the mold and finished product is anything but.
When compared with machining, injection molding offers numerous advantages such as a more desirable finish and shape. Plastic injection molding allows the production of intricate parts that would be too costly and/or difficult to machine and allows many parts to be created simultaneously in the same mold. Other advantages include:
•
Fast production
•
High repeat tolerance
•
Simplicity—no additional finishing is required
•
Relatively low labor costs.
An added bonus is that the scraps (or defective plastic parts) can be used again—recycled for future molds so there is virtually no waste. The primary downsides are the high cost of equipment (both to purchase and maintain) and the inherent limitations of plastic parts. However, the same injection technology can also be applied to stronger substances such as sintered (powdered) metal.
While hydraulic IMMs still dominate the market, electric versions that are cheaper to use, more precise but less powerful have made inroads. Experts say the future is a hybrid molding machine with the compressive power of hydraulics and the energy efficiency of electricity.
HYDRAULIC OIL FOR PLASTIC INJECTION MOLDING
All hydraulic-plastic-injection mold systems are subject to fluid leakage and contamination. Experts say that hydraulic fluid contamination is responsible for nearly 80 percent of all IMM issues. So it’s not surprising that the selection, monitoring and maintenance of these fluids is critically important. Most hydraulic fluids are Group I or Group II mineral oil basestock (
3).
Types of Injection Molding Machines (1)
Injection molding machines (IMMs) are classified by their driving systems, mainly hydraulic, electric or hybrid. Most IMM OEMs offer either all three or hydraulic models and either hybrid or all-electric alternatives. These companies include Bosch Rexroth, Siemens, Mitsubishi, NegriBossi, Engel North America, BMB Plastics Machinery, D&M Machinery, Motan Inc., and Andrew Isaacs Machinery International, among others.
Hydraulic. Hydraulic presses were the only option available to molders until Nissei Plastic Industrial introduced the first all-electric injection molding machine in 1983. Hydraulic machines are not as precise and energy-efficient as electrics. Hydraulics have a number of advantages, including the fact that they are less expensive and compress better than electrics. They have about five times greater energy density than electric. Over the years, they have become more efficient, reliable and operate with less fluid.
Electric. Although electric IMMs are more expensive to purchase than hydraulic counterparts (now about 10-20 percent higher), they generally have lower operation costs. While electric IMMs have dominated the European market for years, they are just starting to cut into the hydraulic IMM market in the U.S. (
2) What fueled the rise of electric IMMs are advantages such as energy savings, better precision, faster injection speeds, reduced maintenance costs and quieter operation. They also eliminate the environmental concerns of hydraulic fluid.
Hybrid. Also referred to as servo-hydraulics, hybrid IMMs incorporate the best features of hydraulic and electric IMMs―with the precision and energy-efficient operation of electrics and the compression power of hydraulics at a price between the two. For example, Bosch Rexroth combines a variable frequency drive with a synchronous torque motor for hydraulics control. Siemens offers servo-hydraulic pumps with a frequency converter and servo-motor for retrofitting that they say uses up to 70 percent less energy than a pure hydraulic system. These more efficient drives on hydraulic pumps also allow less expensive gear type hydraulic pumps to be used instead of variable displacement pumps. Side benefits of these hybrid, servo-controlled pumps are that they are quieter and run cooler. Adding a servo to a hydraulic pump requires about 55 percent less hydraulic fluid, but the main savings comes from the ability to shut pumps down during cooling time, which can be prolonged.
www.canstockphoto.com
REQUIREMENTS
Acceptable hydraulic fluids for IMMs must have the following properties:
•
A viscosity index (VI) around 100: in order to separate moving parts under highly dynamic conditions. The basestock’s VI can be improved with additives.
•
Hydrolytic and thermal stability: to resist chemical breakdown in the presence of water and maintain a temperature of 110 F to 135 F during operation.
•
Foam control: while the degree of foaming is mainly dependent on the basestock, antifoam additives will help.
•
Filterability: a good hydraulic fluid must have excellent filterability. Some additives, such as corrosion inhibitors, will interact with water to form precipitates that clog filters.
•
Antiwear properties: ZDDP is the additive of choice, except in some areas where a more environmentally friendly additive is mandated.
Because of a challenging operating environment of high heat, high pressure and condensation, one of the primary issues with IMM hydraulic fluid is oxidation.
STLE member Greg Livingstone, executive vice president for Fluitec International, LLC in Jersey City, N.J., explains, “In a plastic-injection molding machine, oil deposits can have dramatic effects on machine performance, which can be measured by production yield and scrap rate. Oil oxidation deposits tend to form in the cooler-temperature and high-pressure zones of hydraulic systems. One of these high-pressure zones is valves, which are a critical component to the efficient performance of a hydraulic system. Small layers of deposits can restrict flow paths, further increasing pressure and causing erratic valve behavior.”
Livingstone continues, “The sticky nature of oil deposits will also attract particles and create what is, in effect, sandpaper. This leads to increased wear rates. Deposits also form on heat exchanger tubes and act as insulators, lowering their cooling efficiency and causing higher operating temperatures. Finally, oil oxidation products are reactive in nature. They can interact with healthy additive systems, causing more rapid antioxidant depletion. It is common to see all of these mechanisms at play simultaneously, and this is why the presence of deposits causes more deposits.”
The Plastic-Injection Molding Industry (4)
According to a recent study by Grand View Research, Inc., the global market for injection-molded plastics is expected to reach $277.78 billion by 2020. Increasing demand for plastic as a packaging material, together with Asia’s growing packaging industry, is expected to be a key factor driving market demand over the next few years. In addition, the growing need for weight reduction in automobiles is also expected to augment the demand for plastics as a substitute for metal. The study’s key findings include:
•
Global injection-molded plastics market demand was 92,312 kilo tons in 2013 and is expected to reach 130,139.7 kilo tons by 2020.
•
Asia Pacific was the largest regional market for injection-molded plastics, with market revenue of $70.18 billion in 2013. In addition, Asia Pacific is expected to have the fastest growth in demand.
•
Because of properties like lightweight and superior flexibility, polypropylene is the most widely used injection-molded resin, with volume estimated at 32,836.1 kilo tons in 2013.
•
The injection-molded plastics market is fragmented with a large number of participants operating in the regional and global market. Major participants include BASF, DuPont, ExxonMobil, Dow Chemical, SABIC, Huntsman and Eastman Chemical, among others.
•
Packaging was the largest application segment for injection-molded plastics, accounting for nearly 30 percent of global demand in 2013.
The growing demand for plastic, as replacement for metal in automobiles, is expected to be a major market driver. Injection-molded plastics used in the building and construction segment accounted for close to 10 percent of the market in 2013.
Some of the major polymers used in the molding process include polypropylene, acrylonitrile butadiene styrene (ABS), high-density polyethylene (HDPE) and polystyrene. While polypropylene is the most widely used polymer material for the production of injection-molded plastics, it is closely followed by ABS in terms of demand volume. ABS is widely used in the production of automotive bumpers. High-density polyethylene (HDPE) was the third largest consumed injection-molded plastic, accounting for 17 percent of global demand in 2013. This should increase because of increasing use in the packaging industry.
www.canstockphoto.com
CLEANLINESS
Plastic IMMs, in particular, require a high level of precision in order to avoid underfilling or overfilling the mold. Pumps operating with contaminated fluid are a primary cause of quality issues that are serious enough to produce rejected parts.
The cleanliness of the fluid is determined by the size and number of suspended particles. With the trend toward more precise and complex IMM components, the tolerance for contaminants continues to narrow. Pump and valve components typically have clearances that are less than 5 microns, so most equipment manufacturers recommend return-line filters of 3 microns or less.
Brian Carr, general manager of Perfection Servo in Batavia, Ill., clarifies, “There was a time when the industry was really pushing 3-micron filtration due to all of the servo-valves in operation. However, now that more and more proportional valves that are more tolerant to contaminants are being used, the emphasis on 3-micron system filtration has diminished.”
Routine Oil Analysis Tests that Monitor Oxidation and its Effects (5)
Fran Christopher, director of marketing & business development for ALS Tribology, recommends the following oxidation-related tests:
•
Oxidation by FTIR spectroscopy (ASTM E2412/D7414/, etc.). Increasing the lubricant’s reactive rate of oxidation will lead to an increase in aldehydes, ketones, esters and carboxylic acids. FTIR spectroscopy can measure these increased carbonyl byproducts of oxidation and can provide early notice of a change in the oil’s chemical makeup. This may serve as a warning of reduced remaining useful life of the in-service product. Commonly reported FTIR results exceeding 20 abs/cm are excessive.
•
Acid number by titration (ASTM D664). The increased rate of oxidation and the production of chemical byproducts may also increase the acidic condition of the lubricant. Since new oils have an acidic signature, the in-service oil acid number may be compared to the new oil baseline to determine if the production of acidic constituents in the used-oil sample exceeds allowable levels for the oil’s continued serviceability. In general, a used-oil result that is 2 to 3 times the baseline acid number of the new oil is considered high.
•
Kinematic viscosity (ASTM D445/D7279). As the propagation and termination of oxidation continues unabated, the state of the lubricant continues to degrade to the point where the changes in hydrocarbon molecular structure (sludge) begin impeding the flow of the oil, which causes an increase in oil viscosity. This increase can be measured and reported by kinematic viscosity testing. Generally fluids that increase viscosity 10 to 15 percent above the new oil baseline will need to be changed out.
TYPES OF FILTRATION
According to STLE member Fran Christopher, director of marketing & business development for ALS Tribology in Houston, filtration varies by technology and design. Filter media can be wire mesh, cellulose fiber, fiberglass or another synthetic, composite material. The media is generally characterized as surface media or depth media.
Surface media filter elements allow the fluid to flow straight through the filter. The filter element is usually made of wire mesh and has uniform pores sized to the largest particle that will be trapped. As the surface area becomes clogged with the larger particles, particles smaller than the pore size rating also become trapped.
Depth media filter elements force the fluid to take a difficult indirect path through the filter. The element has a variety of pore sizes that the fluid and its particulates must travel through. Depth media filters engage a larger portion of the filter media than surface media filters so they can sustain a larger load of contaminants for longer periods. Two of the most common filter media used in depth type filters are cellulose and fiberglass. The glass fibers allow for more fibers per inch than cellulose, so fiberglass tends to trap finer particulates with improved efficiency.
Inline filtration may not be enough to keep up with particulates generated internally and/or externally. In these cases, the use of portable and/or permanent offline filtration is an excellent way to improve performance and reliability. Another option is to install desiccant breathers on machine oil reservoirs and bulk storage containers.
For varnish problems, conventional mechanical filtration usually does not work because the degradation particles (soft contaminants) are submicron in size and flow through the filters unobstructed. Electrostatic and/or cellulose filtration media have been shown to work well. These filters set up a high-potential electrostatic energy field. Since the varnish’s submicron particles already have a high polar charge as they pass through the energy field, they are pulled against the filter media and removed from the oil. This process also collects other submicron contaminants such as dirt. Electrostatic filtration takes time but can be very effective. Christopher adds that if the problem is too advanced for electrostatic filtration, the best option will be to clean the system.
There is really no single ideal hydraulic IMM filter. Because of this, Livingstone says contamination avoidance is the best strategy. “There has always been a strong focus on oil cleanliness and filtration in sensitive hydraulic systems. The microfiberglass filters used to clean the oil, however, are ineffective at removing degradation products,” he says. “The particles are submicron in size and require special filtration processes to remove. Electrostatic oil separators have been shown to be effective at removing these particles. However, their high cost has been a barrier to widespread use. Some depth filters employ a highly polar media, which can adsorb some of the polar organic oxidation products. However, when it comes to hydraulic oil deposits, avoidance is the best policy.”
Varnish Potential Testing (8)
To screen for the more elusive submicron-sized thermal degradation byproducts that can form varnish and lacquer deposits on valves and filters, ALS Tribology’s Fran Christopher recommends the following varnish potential tests:
•
Membrane patch colorimetry. This test (ASTM D7843) tracks the amount of insolubles in the fluid. During the test, insoluble contaminants are extracted from the sample and transferred to a patch where the color of the membrane patch is analyzed by a spectrophotometer.
•
The RULER test. The Remaining Useful Life Evaluation Routine test (ASTM D6971/D6810) uses voltammetry to measure the depletion of antioxidation additives of the specific product, including amines and phenols, and ZDDPs. While particle count is not necessarily a key measurement of deposit formation particles, a low particle count, combined with a high level of particulate weight contamination, would tend to support the existence of insoluble gums or degradation deposit material.
•
Gravimetric analysis. This is used to measure the weight of residual insoluble, as well as pentane insoluble testing (ASTM D4055) of the fluid and an ultra-centrifuge test (
9) for centrifugal separation of insolubles from the fluid. Using these values compared to a sediment rating system, as well as one of the standard color tests, may be useful for supplemental information.
•
Conductivity. Monitoring conductivity (ASTM D2624) as part of a routine oil analysis in a hydraulic system also provides information on the overall increase in degradation products and contaminants in the fluid. As the general level of degradation products and contaminants increase over time, the conductivity will correspondingly increase. This information can be correlated with other test parameters for product integrity and service life.
CONDITION MONITORING
The increasing implementation of predictive versus reactive and preventive maintenance is an excellent fit for IMM hydraulic fluid (
6). For predictive maintenance to be effective (to avoid downtime), the lubricant needs to be monitored regularly during operation.
Online sampling and sampling via mobile sampling equipment are two options. Both allow onsite fluid analysis at regular intervals. Other methods include installing contaminate alarms or pressure switches directly into the IMM. These will alert maintenance engineers of blocked filters or contamination over a certain threshold. All of these options require an upfront investment that is, in some cases, considerable.
A more viable option for most organizations is a fluid analysis provider that will regularly analyze samples and submit an actionable report. The gold standard is predictive maintenance, which will uncover the causes of fluid degradation and, by extension, system degradation before damage occurs.
Christopher explains, “As in-service hydraulic oils degrade, physical and chemical parameters will change. These degradation properties can be trended over time or compared with new oil. The rate of oxidation may be accelerated by catalysts such as heat, water, metals and other contaminants in the oil.
“When antioxidant additives are depleted, the oil continues to oxidize with nothing to prevent the eventual polymerization of the molecules and destruction of the oil as a lubricant,” Christopher adds. “It is the function of the oil’s finite supply of antioxidant additives to interrupt and prevent the reaction from reaching termination stage (
7).”
Christopher adds that while used-oil sampling can help identify the precursors to deposit formation as well as several other problematic scenarios, to merely test for deposit formation would be shortsighted. Rather, the fluid should be sampled monthly and subjected to the following tests:
1.
Metals (ICP spectroscopic analysis to determine wear metals, metallic oil additives and contaminants). While this analysis component has little to do with deposit formation directly, it is still important.
2.
Kinematic viscosity. This test should be performed at 40 C to make sure the oil is still in-grade and isn’t contaminated or oxidized. Oil will become more viscous as it oxidizes.
3.
Water. Deposit formation is accelerated by the presence of water. Identifying it will allow for preventative removal.
4.
Acid number. This will determine if oxidation is generating acid.
5.
Fourier transform infrared (FTIR) oxidation. This will confirm oxidation.
6.
ISO 4406 particle count. While this will not directly detect deposit formation and insoluble gums, this test is important because, among other reasons, the particulates provide a nucleation site for deposits to form.
Livingstone recommends Membrane Patch Colorimetry (ASTM D7843), FTIR and Linear Sweep Voltammetry. “The combination of all three of these tests will best allow the monitoring of the fluid’s degradation and predict when deposits will start to impact hydraulic system performance,” he says. “When one observes additive depletion and the generation of degradation products, the formation of deposits are close behind.”
Establishing a testing program that meets the reliability needs of the asset is important. This includes determining a cost-effective test package with the proper scope and frequency. Testing scope and frequency also can be dependent on the work environment, operating temperatures, workloads and the consequences if the asset fails. Data that is trended over time is most useful.
A testing schedule can include more frequent routine testing and expanded inspection at intervals that monitor long-term performance of the product in service. During filtration activities for cleanup purposes, monitoring during the cleanup can tell how well the process is going, when targets have been reached, or if a different technology or technique needs to be applied. Proper and consistent sampling techniques are very important, as well as coordinating follow-up activity based on reporting test results.
If the trend toward hydraulic hybrid IMMs (which use less fluid than pure hydraulics) continues, the demand for hydraulic fluid will diminish—but not the need for oil analysis. As with most machinery, the trend is toward smaller footprints, smaller fluid reservoirs and faster cycles. All of this puts additional pressure on hydraulic fluid and more importance on fluid analysis.
REFERENCES
1.
Click
here.
2.
There is some disagreement as to whether hybrids should be counted as electrics.
3.
The American Petroleum Institute categorizes basestocks by their sulfur content, level of saturates and viscosity index (VI). The five classifications are:
•
Group I solvent dewaxed basestock is the least refined—usually a mix of different hydrocarbon chains.
•
Group II hydroprocessing and refining basestock is common in commercial mineral-based motor oils.
•
Group III hydroprocessing and refining basestock is the most refined of all mineral oil basestock.
•
Group IV or PAO (polyalphaolefin) basestock is a chemically engi¬neered synthetic.
•
Group V basestock is usually blended with other basestock. It is used in small amounts as secondary basestock—providing the base ingredient for many additives.
4.
Click here.
5.
Information from Fran Christopher, director, marketing & business development, ALS Tribology.
6.
Predictive maintenance refers to changing fluids only when their actual (and closely monitored) condition shows it is necessary.
7.
Reaction of the lubricant base oil and oxygen occurs in three stages: initiation, propagation and termination.
8.
Information from Fran Christopher, director, marketing & business development, ALS Tribology.
9.
Ultracentrifuge is not a gravimetric test. There is no ASTM method. ALS uses an in-house method based on an established ExxonMobil method.
Jeanna Van Rensselar heads her own communication/public relations firm, Smart PR Communications, in Naperville, Ill. You can reach her at jeanna@smartprcommunications.com.