Machining operations depend on additives in cutting fluids that prevent the metal chips generated from being welded to tool faces by the extreme temperatures and pressures at the tool-workpiece interface. If buildup of welded chips occurs to a degree that alters the effective tool rake, all phases of the operation are seriously affected – resulting in downtime, scrap parts and unhappy customers.
Extreme pressure (EP) additives based on phosphorus, chlorine and/or sulphur are incorporated into cutting fluids to prevent this. Sulphur is typically used for temperatures above 400°C, and there has been an ongoing trend to use light color, low-odor sulphur-containing additives to provide better machining visibility and improved workplace environments.
Lighter and Greener
Dover Chemical used its deep understanding of sulphurised technology as a major supplier to the metalworking fluids industry to develop a new-generation additive to better meet customers’ needs. Dover’s exclusive, novel technology required a new CAS Number and a Pre-manufacturing Notice to be submitted and granted before starting commercial production in the spring of 2014.
Patent-pending Doverlube®LCS-10 is a high performance light-colored sulphurised vegetable ester that has very low sulphur odor and is readily biodegradable. The product is non-staining with no added corrosion inhibitors, produces no H2S and is a Super Compliant material for VOC emissions per the United States Environmental Protection Agency (EPA) Rule 1144. Characteristics are shown below.
Doverlube LCS-10 Performance Evaluation
Performance of Doverlube LCS-10 was evaluated by the following methods: Vertical Drawbead Testing; 4-Ball Wear Analysis; Micro-tap Lubricity and EP Determination; Bridgeport CNC Machining Center Drilling Operation on 1018 Cold Rolled Steel. The standard formula was typical for a metalworking product:
Viscosity: 175 SUS @ 100°F
Sulphur: 1.5% (from included S-additive)
Chlorine: 1.5% (from Paroil®152)
Lubricity: 13% (from Methyl Ester 165)
In two cases, the chlorinated alkane was replaced by Mayfree®133 or Doverlube® NCEP, on an equal percentage basis.
Vertical Drawbead Testing
This testing was conducted using a die load of 500 psi on carbon steel at ambient temperature with an additive loading of 5% in 20cS oil. Higher efficiency numbers equate to better performance; results within +/- 5% are considered equal.
Doverlube LCS-10 100%
10% BASE 10SE -3%
15% Sulphurised Ester -4%
15% Sulphurised Ester -7%
40% Polysulfide -8%
40% Polysulfide -9%
4-Ball Wear Testing
Testing speed was 1,200 rpm, load was 40 Kg at ambient temperature for 60 minutes. Smaller scar diameter demonstrates better performance.
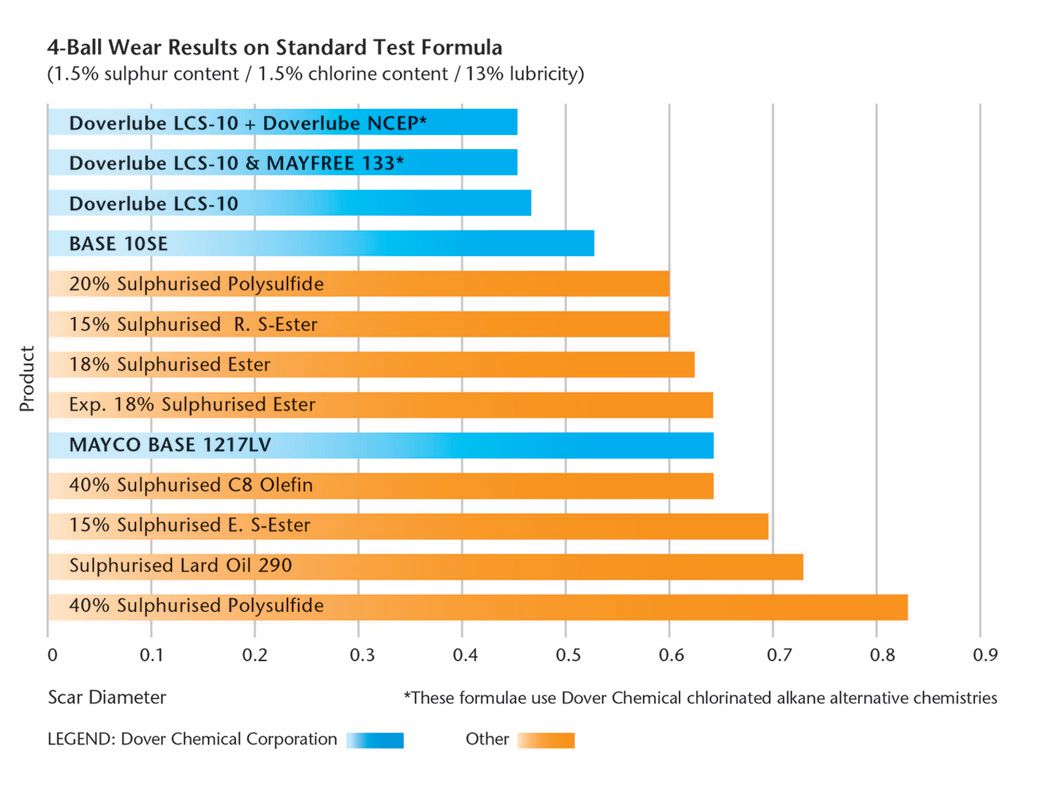
Doverlube LCS-10 outperforms other sulphurised additive options in wear tests. Formulations combining it with Doverlube NCEP or Mayfree 133 offer added EP performance and are chlorine-free.
Tap Torque Testing
Testing speed was 550 rpm to a depth of 15mm on carbon steel. Higher efficiency shows better performance. Efficiency at +/- 3% is considered equal.
Doverlube LCS-10 provides equivalent or superior tap performance compared to alternative sulphurised products and is non-staining.
CNC Testing
HSS 0 1495” drill speed was 2,000 rpm with a feed rate of 25.4cm/min, drilling a plate of 1018 cold rolled steel measuring 10.2cm x 15.2cm x 0.13cm. A difference of more than 5.0 microns is considered significant; lower micron numbers indicate better performance.
Overall performances were considered equal at the conclusion of the test; however, Doverlube LCS-10 demonstrated smooth wear progression, which is desirable. The staggered wear progression of BASE 10SE indicates re peated welding of metal to the tool that breaks free and then reforms and breaks again. This shocking to the drill will eventually lead to tool failure.
Conclusion
Doverlube LCS-10 offers equivalent or superior EP performance for metalworking fluids with a light color that improves visibility during machining. Its very low odor, low VOCs and lack of H2S generation enable formulations that are environmentally- and operator-friendly. It is suitable for use in many types of base oils and vegetable esters for many metalworking applications.
Doverlube LCS-10 entered the market in May 2014 and is commercially available in the United States and selected Asia-Pacific countries.
For formulary assistance contact:
Lou Bona, Global Business Manager, Metalworking:
lbona@doverchem.com, or:
John Nussbaumer, Technical Service Manager, Metalworking:
jnussbau@doverchem.com