The pros and cons of ISO
Jeanna Van Rensselar, Contributing Editor | TLT Feature Article October 2014
Establishing uniform standards can help ensure products work well and safely in today’s global economy.
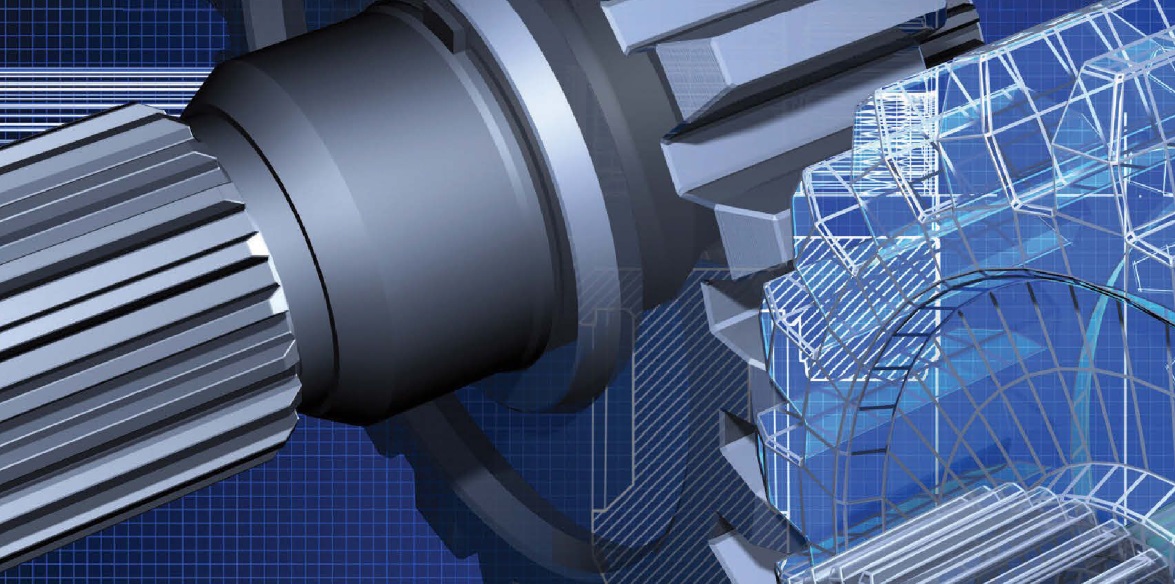
www.canstockphoto.com
KEY CONCEPTS
•
ISO is not a regulator, inspector or manager and is not involved in the certification process for any of its standards.
•
Whether ISO 9001 certification actually improves quality depends on what organizations do after the certification rather than before or during.
•
There are a number of quality management programs that focus on business excellence, but ISO 9001 is not one of them.
Headquartered in Geneva, Switzerland, ISO is the largest developer of voluntary international standards in the world. The goal of these standards is to provide premier specifications for products and services. Because these standards are developed through worldwide consensus, they have the significant value-add of facilitating international trade.
ISO members represent 162 countries that populate 3,368 standard-developing technical bodies. In the U.S., ISO is commonly referred to as an initialism for the International Standards Organization, but this is incorrect. It is actually the International Organization for Standardization, which would have different initialisms in different languages (i.e., IOS in English, OIN in French for Organisation Internationale de Normalisation). Because of this, the organization’s founders decided to give it the universal designation ISO, which is derived from the Greek word isos, meaning equal. So ISO is not an acronym, it is a designation and it does not require “the” before the name.
Since ISO was founded in 1947, it has published nearly 20,000 standards that address nearly all aspects of technology and business—including, but definitely not limited to, 9001 and 14001.
Sandrine Tranchard, ISO’s communications officer, explains, “The most well-known standards are ISO 9001 on management systems and ISO 14001 on environmental management systems. Many people think this is all we have. But that is far from the case. We currently have 20,000 standards in our portfolio. Many times people are looking for a solution and don’t even know that it already exists in our portfolio of standards.”
Tranchard adds, “Standards provide a common language across an industry sector, which means they help open up export markets for products and services. This is particularly important as the economy becomes more global, as it becomes increasingly important for products and parts to work well together across national boundaries.”
ISO History: The Timeline
ISO was founded in 1946 when delegates from 25 countries met at the Institute of Civil Engineers in London and decided to create an organization “to facilitate the international coordination and unification of industrial standards.” ISO officially began operations in February 1947.
1946: 65 delegates from 25 countries meet in London to discuss the future of international standardization.
1947: ISO officially comes into existence with 67 technical committees (groups of experts) with each committee focused on a specific subject.
1949: ISO moves into offices in a small, private house in Geneva, Switzerland.
1951: The first ISO standard (then referred to as a
recommendation), ISO/R Standard Reference Temperature for Industrial Length Measurements, is published.
1955: ISO’s 35 members gather in Stockholm for the 3rd General Assembly.
1960: ISO publishes the standard ISO 31 on quantities and units. The objective is to create worldwide uniformity in units of measurement and how they are used. It was superseded by ISO/IEC 80000.
1968: ISO introduces correspondent membership, which allows developing countries to be updated on international standardization developments without the full cost of membership.
1968: ISO publishes its first standard on freight containers. Freight and packaging is an area where ISO has been particularly active and effective.
1971: ISO creates its first two technical environmental committees: Air Quality and Water Quality.
1987: ISO publishes ISO 9001—its first quality management standard. Standards in the ISO 9001 quality management portfolio are among the most prominent ISO standards.
1995: ISO launches its first Website.
1996: ISO publishes ISO 14001—an environmental management system standard, which provides tools for organizations to identify and control their environmental impact.
2000: ISO begins selling its standards online.
2005: ISO and IEC’s joint technical committee, JTC1, launches ISO/IEC 27001, a management system standard on information security. ISO 27001:2005 is a prevalent ISO standard (
1).
2007: ISO moves to its current offices in La Voie Creuse, Geneva.
2010: ISO launches ISO 26000—the international standard providing guidelines for social responsibility. The working group that developed ISO 26000 is one of the largest and most diverse groups to develop an ISO standard.
ISO MEMBERS
ISO is a network of national standards bodies that are the leading standards organizations in their countries. Individuals and companies cannot become ISO members. Each member organization represents ISO in its country and there is only one member per country. For example, the U.S. representative is the American National Standards Institute (ANSI), which also happens to be a founding member. The German representative is DIN, the German Institute for Standardization.
There are three member categories, each of which has a different level of access and influence within the ISO system.
Full members (or member bodies) influence ISO standards development and strategy by participating and voting in ISO technical and policy meetings. Full members sell and adopt ISO International Standards nationally.
Correspondent members observe the development of ISO standards and strategy by attending ISO technical and policy meetings as observers. Correspondent members can sell and adopt ISO International Standards nationally.
Subscriber members are kept up-to-date on ISO’s work but cannot participate in it. They do not sell or adopt ISO International Standards nationally (
2).
STRUCTURE
ISO is an independent non-governmental organization made up of members from the national standards bodies of 162 countries. It has the following structure:
The General Assembly. This annual meeting is attended by members and ISO’s principal officers that include the president, the vice president for policy, the vice president for technical management, the vice president for finance, the treasurer and the secretary general. The General Assembly is ISO’s ultimate authority and the primary venue for determining strategic objectives.
The ISO Council. The ISO Council is made up of 20 member bodies, the ISO officers and the chairs of Policy Development Committees. The council meets twice a year and handles most governance issues. Membership on the council is open to all member bodies and rotates to ensure that it remains representative of the member community. The council oversees a number of bodies that provide guidance and management on specific issues.
Technical Management Board. The Technical Management Board manages technical work and is responsible for the technical committees that lead standard development and any associated strategic advisory boards.
ISO Central Secretariat. Daily operations are run by the Central Secretariat in Geneva, Switzerland, which is under the direction of ISO’s Secretary General.
TERMINOLOGY
•
ISO: a single term, not an acronym— is the correct name of the organization in every country. It does not require use of the word “the” before the term.
•
Certification/registration: Referring to a third-party attestation related to products, processes, systems or persons. ISO uses the term
certification, but it is also called
registration in some countries, including the U.S.
•
Certification body/registrar: Referring to an independent certifier. ISO uses the terms
certification body and
conformity assessment body. In some countries, including the U.S., the term registrar is often used.
•
Certified to an ISO standard: is the correct term rather than ISO certified. ISO does not certify any organization to any standard.
ISO STANDARD DEVELOPMENT
An ISO standard is developed by a panel of experts within a technical committee. Technical committees are made up of experts from sectors that have asked for such standards. Other international and regional organizations may apply to participate in developing a standard. Once approved, these organizations may comment on drafts or propose new items or documents for fast tracking, but they have no voting rights. ISO expects national members to take the opinions of all interested parties into account (
3).
Once the need for a standard has been established, these experts meet to discuss and negotiate a draft. As soon as a draft has been developed, it is shared with ISO members for comment and an eventual vote. If a consensus is reached, the draft becomes a standard. If not, it goes back to the technical committee for further review.
Following are the four main principles governing ISO standard development (
4):
1. ISO standards respond to a need in the market. ISO does not decide when to develop a new standard. Instead, ISO responds to a request from industry or other stakeholders such as consumer groups. Typically, an industry sector or group communicates the need for a standard to its national member, who then contacts ISO.
2. ISO standards are based on global expert opinion. ISO standards are developed by groups of experts from all over the world who are part of larger technical committees. These experts negotiate all aspects of the standard, including its scope, key definitions and content.
3. ISO standards are developed through a multistakeholder process. The technical committees are made up of experts from the relevant industry but also consumer associations, academia, non-governmental organizations and government.
4. ISO standards are based on a consensus. Developing ISO standards is consensus-based. Comments from stakeholders are considered.
FUNDING
The major source of ISO funding is from organizations that manage specific projects or supply the experts needed to participate in technical work. These organizations are, in effect, subsidizing the technical work by paying the travel costs of the experts and accommodating their work on ISO assignments. Other sources of funds are from:
•
National members who pay dues (in proportion to each country’s gross national product and trade figures)
•
The sale of standards.
CERTIFIERS
ISO is not involved in the certification process of any of its standards. Because of this, no organization can ever claim to be certified by ISO or ISO certified; rather they are certified to an ISO standard. Certification is performed by independent certification bodies that inspect relevant aspects of organizations and issue compliance certificates. ISO does not accredit, approve or control the certification bodies—it doesn’t certify the certifiers.
Although ISO does not perform certification audits, its Committee on Conformity Assessment (CASCO) has produced standards that relate to the certification process. The voluntary criteria in these publications are an international consensus on good certification practice. Companies and organizations usually operate their certification activities in accordance with these international standards.
Before choosing a certification body, ISO recommends that organizations perform the following due diligence:
•
Evaluate several certification bodies
•
Verify that the certification body adheres to the relevant CASCO standard (
5)
•
Check to see if it is accredited; note that accreditation is not compulsory (
6).
Although accreditation for certification bodies is not required by ISO, some countries may require it and some purchasing entities may stipulate that vendors are ISO certified by an accredited certification body. There is an accrediting body, in most countries, and it is often the ISO member organization. For example, in the U.S. it is ANSI-ASQ (
7).
ISO’S LUBRICANT-RELATED TECHNICAL COMMITTEES
Following are ISO technical committees that relate most closely to lubrication:
ISO/TC 28—Petroleum Products and Lubricants
Information
here.
ISO/TC 27—Solid Mineral Fuels
Information
here.
ISO/TC 238—Solid Biofuels
Information
here.
ISO 9001
Even though there are a number of ISO standards that relate directly to tribology, the most commonly requested certification in all fields, including tribology, is ISO 9001 (quality management), with ISO 14000 (environmental management) not far behind. ISO 9001 lays out the requirements of a quality management system based on the following eight quality management principles:
•
Customer focus
•
Leadership
•
Involvement of people
•
Process approach
•
System approach to management
•
Continual improvement
•
Factual approach to decision-making
•
Mutually beneficial supplier relationships.
All ISO standards are reviewed every five years for relevancy and possible revision. The ISO 9001:2015 revision is currently underway and is expected to address areas such as risk management, procedure documentation, supply chain relationships and terminology.
CERTIFICATION
An organization applying for ISO 9001 certification has its sites, functions, products, services and processes audited by a certification body. The certification body will then present a list of nonconformities to management. If there are no major nonconformities, the certification body will issue a certificate.
If there are major nonconformities, the company will present an improvement plan to the certification body that details how issues will be resolved. After the certification body is convinced that adequate corrections have been made, it issues a certificate. This is a pass/fail process.
The final certificate includes the scope, such as the production of lubricant additives, and will display the addresses where the certificate applies. As with almost all ISO certificates, it must be renewed periodically. For ISO 9001, that period is three years.
TIME FRAME
A 2007 study found that the average time to implement ISO 9001 was eight months. But for a complex organization or an organization that is starting from ground zero, it could take longer (
8). Variables include:
•
The gaps against the ISO 9001 requirements
•
The commitment and leadership of senior management
•
The available internal resources such as skills, experience and time
•
The size and complexity of the organization
•
The organization’s current state of readiness
•
The existing quality culture— how much change will be necessary
•
Whether the current quality system (assuming one exists) is documented. This means procedures, flowcharts, checklists, forms, policies, job descriptions, etc.
Experts advise that learning and improving along the way is a valuable part of the process and shouldn’t be compromised.
WHERE ISO PROVIDES VALUE FOR SMALL ORGANIZATIONS
Following are the areas where ISO believes its standards provide value for small- to mid-sized organizations:
•
Leveling the playing field
•
Improving the quality of products and services
•
Driving growth
•
Cutting costs and increasing profits
•
Creating a competitive edge
•
Opening up export markets for products and services
•
Opening doors to new customers
•
Strengthening the existing business
•
Enhancing credibility
•
Sharpening business processes and increasing efficiency
•
Facilitating compliance with other regulations (
9).
COSTS
There are two kinds of costs associated with ISO certification:
1.
The cost of the certification itself. This includes the cost of the certification body, which averages $3,500-$5,000 but could be significantly more depending on the size and complexity of the organization.
2.
Preparation costs. Much of this cost depends on whether preparation is performed in-house or through a consultant. In addition to the expense of employee hours, in-house preparations often require a kit, which runs about $1,600. Hiring a consultant to handle preparations runs $5,000-$20,000 and up (
10).
One study concluded that total costs for ISO 9001 certification can run as high as $245,000 (
11).
CONTROVERSIAL ISSUES
There are four controversial issues involving ISO 9001 certification. First is the cost, which can be prohibitive for a smaller company and create an unfair advantage for a larger competitor. This, then, brings up the second and third issues: quality improvement and safety. Finally, there is the issue of oversight. These four issues can generally be applied across the spectrum of ISO standards certifications.
1. Unfair competitive advantage. The largest potential customers (including the U.S. government and major corporations) usually require certification to, at least, one ISO standard. For many companies, this is the primary motivation for achieving standard certification. Although the overall costs is lower for a small organization, certification to an ISO standard does require substantial resources in terms of cost and employee time that are difficult for smaller companies, including promising start-ups, to swallow. One way to leverage the cost is to use the process to achieve actual quality improvement rather than just certification.
Julius Turk, business development manager for a small, but established technology company in Chicago, explains, “Our goal in seeking certification was not only to enhance our processes and procedures but to keep us in the running when ISO 9001 is a requirement for project opportunities.”
Tranchard points out that ISO standards are developed to answer the needs of all organizations, regardless of size or activity. She says, “The way a company decides to use the standard—they may seek certification, but this is not obligatory and they may seek the services of a consultant—will vary significantly from one company to another along with the associated costs.”
2. Lack of actual quality improvement. Whether ISO 9001 certification actually improves quality depends on what the organization does after the certification rather than before or during. In theory, an organization could achieve certification and let everything slide for a year until it needs to undergo a surveillance audit to maintain its certification. ISO 9001 does not provide an absolute guarantee of ongoing product quality. It is only a snapshot taken the day the audit is carried out. For certificates issued by an accredited certification body, full recertification audits are required every three years, with surveillance audits (shorter in duration and focusing on key topics) at least once a year.
There are a number of quality management programs that focus on business excellence, but ISO 9001 is not one of them. Programs such as Six Sigma and TQM are designed to continuously detect and reduce quality issues that can affect organizational efficiency and overall business success. ISO 9001 focuses on the processes needed to ensure product conformity and whether these processes are effective (not necessarily efficient).
Business improvement and long-term success is, however, addressed in the ISO 9004 guidance standard, which goes hand-in-hand with the ISO 9001 requirements standard. ISO 9004 covers a much broader range of issues than ISO 9001 and includes a maturity assessment tool for organizations to identify their own strengths and weaknesses and where they need to improve. Because it contains only recommendations and not requirements, ISO 9004 is not subject to certification.
3. Safety. In 2010, Chinese organizations held a total of 297,037 ISO 9001 certifications. This is more than twice the number of the country that came in second (Italy with 138,892) and over 10 times more than the U.S. (25,101) (
12). Yet Chinese companies have their challenges, too. There was the 2006 incident involving defective Chinese drywall used by Hurricane Katrina victims; the 2007 pet food recall; the 2008 tainted milk scandal; lead-based paint on children’s toys; improperly fed fish exported for consumption; toxic toothpaste; tainted “cough syrup.” It is not clear, however, if these companies were ISO 9001 certified.
Back in the U.S., there was the Bridgestone/Firestone incident in 2000 involving tire treads that separated from the sidewalls and caused rollovers in Ford Explorers. There were an estimated 250 deaths and 3,000 serious injuries (
13). Bridgestone/Firestone recalled 6.5 million tires. Both Bridgestone and Firestone were ISO 9001 certified at the time. Since tires are the company’s primary product, this begs the question: certified for what?
In short, there doesn’t appear to be a correlation between ISO 9001 certification and quality and safety of individual products. So the issue here is that certification to an ISO standard can mislead consumers into assuming that it is an assurance of safety and quality, when it is not. Rather ISO 9001 deals with management systems—not directly with product quality (
14).
4. Lack of oversight and accountability. Finally, there is the issue of oversight and accountability. ISO creates requirements for certifications but does not certify organizations or even certify the certification bodies. However, third-party accreditation for certification bodies is an option and ISO publishes standards to help provide international best practice on this. The question is, where is the accountability for adherence to standards in cases such as Bridgestone/Firestone?
Although ISO did receive high marks for processes and transparency in One World Trust’s 2007 Global Accountability Report, it was discovered that ISO did not even have a process for handling complaints (
15, 16). An American Society for Quality (ASQ) debate team charged with arguing the ineffectiveness of ISO 9001 concluded the following:
“Though ostensibly proposed and required by many firms as a quality and safety management program, ISO 9001 has failed, in many cases, to achieve any long-term impact on customer interpretation of quality or to guarantee safety for either employees or customers. It has similarly failed to achieve quality improvement for many firms or the increased profitability, which has been claimed. It does not support the growing trend for rapid customization and seems to inhibit adaptability and response to rapid change in professional fields, which require less routinized processes and thinking. What’s more, management frequently lacks commitment to the program beyond pursuing (certification) because the company is required to do so for business reasons. For these reasons and the others discussed above, we believe the ISO 9001 program is largely ineffective as a quality and safety management standard (
17).”
TOTAL QUALITY MANAGEMENT (TQM)
TQM is a program designed to establish a permanent environment of continuous quality improvement in products and services. It is largely based on previously developed quality control programs.
In 1984, a U.S. Navy affiliate asked some of its researchers to assess statistical process control and the work of several prominent quality theoreticians in order to make recommendations that would improve the Navy’s operations. The bulk of the recommendations centered on the work of W. Edwards Deming (who is responsible for creating a culture of quality in Japan). The Navy initiated the program in 1985 and called it Total Quality Management. TQM then found its way into public and private enterprise and was the springboard for the following:
•
The 1987 creation of the Malcolm Baldrige National Quality Award—still the most coveted quality recognition in the U.S. Winners range from Motorola in 1988 to The Pewaukee Wisconsin School District in 2013.
•
The 1988 creation of the Federal Quality Institute.
Although TQM principles are still practiced, the system was overshadowed by Six Sigma, the Lean Manufacturing process and the widespread adoption of ISO 9000 standards.
ISO’S DEFENSE
No one, including ISO, ever purported that it was ISO’s job to ensure quality and safety. They are not regulators, inspectors or managers. Rather ISO develops international standards, disseminates information and provides a framework for certification—all extremely complex and valuable services it has mastered.
The purpose of ISO 9001 is to demonstrate to customers that the company has a documented, effective and independently verified quality management system that is capable of consistently providing products that meet customer requirements—but not to vouch for the quality of products and services themselves.
ASQ debaters arguing for ISO 9001 effectiveness put it like this, “Simply meeting minimum qualifications once does not automatically mean that a company will continue to meet safety standards. ISO standards simply provide a benchmark by which other companies and consumers can judge the probable level of quality standards in the certified company (
18).”
The key factor for determining the effect that any ISO certification will have on long-term quality is the motivation for pursuing certification in the first place. For those organizations truly interested in improving quality, the certification process (rather than the certification itself) can have profound positive effects on nearly all aspects of the organization.
SIX SIGMA
Six Sigma, developed by Motorola in 1986, seeks to improve the quality of process outputs by identifying and removing the causes of defects (errors) and minimizing variability in manufacturing and business processes. The term Six Sigma is rooted in the sigma rating of a manufacturing process—the percentage of defect-free products it produces.
In a Six Sigma process, 99.99966 percent of the products manufactured should be free of defects. Jack Welch made it central to his business strategy at General Electric in the mid-1990s. Six Sigma is built on discrete quality management tools (including statistics) and promotes an infrastructure of practitioners with varying degrees of expertise that are designated as Champions: Black Belts, Green Belts, Yellow Belts, etc.
Each Six Sigma project follows a discrete sequence of steps and includes quantified value targets such as reduce costs or increase customer satisfaction (similar to Total Quality Management).
A study of companies in four countries designed to test the link between ISO 9001 certification and quality found that registered companies had significantly higher scores on the following measures, which roughly correspond to the eight pillars of ISO 9001 mentioned earlier (
19):
•
Leadership
•
Information and analysis
•
Strategic quality planning
•
Human resource development
•
Quality assurance
•
Supplier relationships
•
Customer orientation
•
Quality results.
A second factor that determines long-term results is management buy-in and follow-through. For organizations that are truly interested in improving quality, pursuing, achieving and maximizing the benefits of ISO 9001 certification requires a continuous commitment of time and attention.
Tranchard explains, “The world goes faster, and ISO is following the trend. For example, in 2013 we sped up the standards-development process by 20 percent compared to 2012. We developed standards in new fields, reflecting market needs such as biotechnology, innovation processing, fine bubble technology, occupational health and safety management systems, sustainable procurement, etc.”
An Interview with Erwin Zaretsky on the ISO 281:2007 Standard for Roller Bearings
STLE Fellow Erwin Zaretsky has been a voting member on two ANSI/ABMA standards committees for more than two decades. One is the ANSI/ABMA B-3 Committee, which directly votes to adopt and/ or modify bearing standards in the U.S. and the other is the U.S. TAG (Technical Advisory Group), which advises the U.S. representative to ISO on how to vote on various issues including adopting and modifying ISO standards.
In the U.S., the two ANSI/ABMA standards that pertain to bearing life and reliability are ANSI/ABMA Standard 9 for ball bearings and ANSI/ABMA Standard 11 for roller bearings. There has been an ongoing campaign to eliminate these two standards and replace them with ISO 281:2007—to which Zaretsky continues to object.
TLT: WHAT IS YOUR ISSUE WITH ISO 281:2007?
Zaretsky: Because of my writings and presentations on this subject, my opinions are well known. I do not believe that the ISO 281:2007 Standard is technically correct.
TLT: WHAT ARE YOUR SPECIFIC ISSUES WITH THIS STANDARD?
Zaretsky: The ISO 281:2007 Standard pertains to a generic bearing, which has an undefined surface finish, heat treatment and material structure that is lubricated with an unspecified lubricant. The standard applies to bearing steel having a fatigue-limiting load or stress below, which no fatigue failures would be expected to occur.
The problem is that through-hardened bearing steels have no fatigue limit. Consequently, the lives of bearings calculated with the standard will result in either an over-prediction of the bearing life and/or a smaller bearing than a particular design or application requires. In other words, the bearing will not necessarily be fit for its intended purpose.
I compare it to a stopped clock. While a stopped clock gives you the right time twice a day, the life you get with the standard is equivalent to having the right time only once a day. It can only be right once for a specific bearing run under a specific load and speed with a specific lubricant. The problem is we do not know what these conditions are.
The most immediate problem with the standard is that it can and does become part of a specification for a new machine design. This can limit the options of the design engineer to using a more conservative design approach when determining the bearing system life and reliability. As a result, a manufacturer can be open to warranty and product liability claims.
TLT: HAVE YOU CONTACTED ISO ABOUT THIS?
Zaretsky: I have had no direct or indirect response from ISO. I do not expect that, outside technical meetings or conferences, I will get a direct response. There are individuals who agree with me regarding the standard and there are those who vigorously defend the standard. However, within the U.S. ANSI/ABMA Bearing Standards Committee, the ISO standard has not been adopted by majority vote. I believe that the standard is a mistake and should be withdrawn. However, that is the responsibility of the member organizations comprising ISO.
IT BOILS DOWN TO…
Any issues with ISO involve misrepresentation, mismanagement and implementation by others, not ISO or the certification standards themselves. It is obviously ISO’s intent that those organizations who receive certification maintain a quality program that extends beyond the certification process. But ISO has no control over that.
As far as the cost, some small businesses find it—regardless of expected return—prohibitive. Others are able to swallow the expense if they can forecast a clear return. As far as the return itself, it depends on answers to these two questions:
1.
Is the certification likely to increase business (i.e., will this open a pool of customers that require ISO 9001 certification?)
2.
How satisfied are company administrators with the current quality and do they intend to follow through with a quality program based on what they’ve learned through certification?
When organizations spend the time and money to become ISO 9001 certified and then don’t follow through with a long-term quality control program, it undercuts the purpose of the whole process. But the reality is that, for many companies, receiving the certificate is the end goal.
Tranchard concludes, “Many people don’t realize the enormous and positive contribution that standards make to many aspects of our lives. They ensure desirable characteristics of products and services such as quality, environmental friendliness, safety, reliability, efficiency and interchangeability—and at an economic cost.”
She continues, “As consumers, when products and services meet our expectations, we tend to take this for granted and are unaware of the role of standards. However, when standards are absent, we soon notice products turn out to be of poor quality, do not fit/are incompatible with equipment that we already have or are unreliable or dangerous. When products, systems, machinery and devices work well and safely, it is often because they meet standards.”
REFERENCES
1.
The IEC (International Electrotechnical Commission) is the world’s leading organization for the preparation and publication of international standards for all electrical, electronic and related technologies—known collectively as electrotechnology:
www.iec.ch/.
2.
From
here.
3.
Fast-track was created by ISO as a way to allow standards organizations to submit one of their existing standards for approval as an ISO standard. This process is limited to a standard that has already been reviewed and approved by that organization.
4.
From
here.
5.
Complete list of CASCO standards: click
here.
6.
To find an accredited certification body, contact the relevant national accreditation body or visit
www.iaf.nu/.
7.
ASQ is the American Society for Quality. For information on ANSI-ASQ accreditation, visit
here.
8.
From
here.
9.
From
here.
10.
Ibid
11.
From
here.
12.
From
here.
13.
From
here.
14.
ISO highly recommends other standards dealing with products in order to complete a quality policy, especially to answer safety and/or regulatory issues at national or international levels. More information can be found in this document: click
here.
15.
From 2007 Global Accountability Report. Available
here.
16.
ISO responds that, while they cannot guarantee a resolution for complaints they receive about false certification or misuse of ISO standards, they do aim to facilitate the dialogue between the parties involved and work toward a more positive outcome.
17.
Ibid. Note: This is the con portion of a debate on the effectiveness of ISO 9001; the pro view is available
here. A PDF of the entire debate regarding the effectiveness of ISO 9001 is available
here.
18.
From
here.
19.
From
here.
Jeanna Van Rensselar heads her own communication/ public relations firm, Smart PR Communications, in Naperville, Ill. You can reach her at jeanna@smartprcommunications.com.