Special storage of oils and lubricants
R. David Whitby | TLT Worldwide September 2014
Make sure you’re storing and distributing your products with the highest standards.
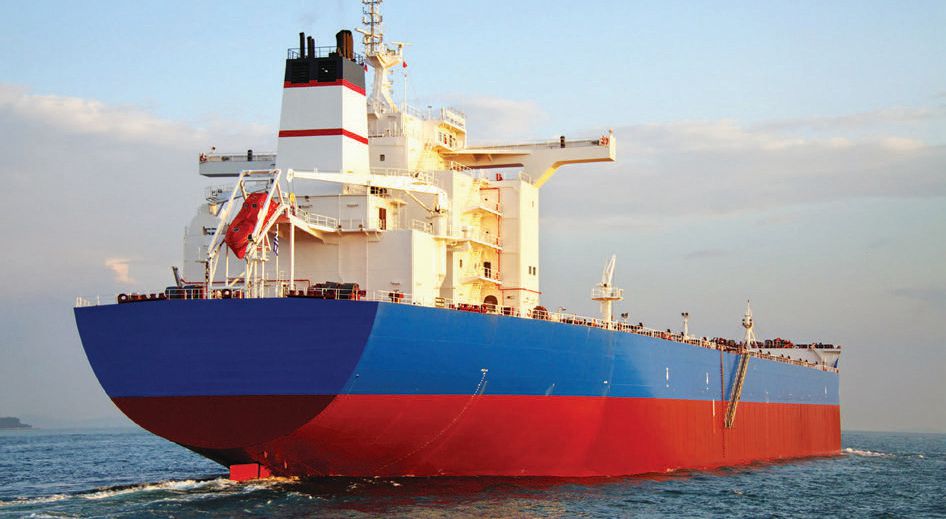
Ships used to transport white oils should have tanks lined with inert material, usually stainless steel.
www.canstockphoto.com
IN MY PREVIOUS COLUMN, we discussed the storage and handling of lubricants. Now let’s shift gears and focus on storing and handling types of oils and lubricants that require special conditions.
White oils, whether technical or medicinal, must be stored and distributed to the highest standards. Any contamination with other oils will mean that a white oil will not meet its required specification. Bulk storage of white oils in manufacturing facilities, main terminals and distribution depots is usually done in stainless steel tanks, which must have both fixed bottoms and roofs. The bottom of a white oil storage tank must be sloped to allow complete drainage of all liquid from the tank.
Ships used to transport white oils should have tanks lined with inert material, usually stainless steel. They should also be completely drainable. Containers that have been used to store or transport medicinal white oils can be used to store or handle future parcels of technical white oils. Containers that have been used to store or transport technical white oils cannot be used to store or handle future parcels of medicinal white oils without being cleaned and dried.
In general, tanks used to store technical and medicinal white oils should only be used for those types of products, respectively. All pipework connections between tanks, bulk loading points and container filling points should be stainless steel, as should all pumps, valves and other equipment.
Storage tanks used for transformer oils are no different from tanks used for other specialty oils or chemicals. The material is normally mild steel or stainless steel. Mild steel tanks can be coated with oil-resistant paints. Compatibility with the transformer oil has to be checked or recommended by transformer or oil producers.
The water content of a transformer oil greatly affects its insulating properties. In storage tanks, this means that contact with humid air must be avoided, especially in warm climates with relatively high air humidity. The most common way of doing this is to equip the tank with a silica gel breather that extracts humidity from air entering the tank. If the product has been contaminated with water, it is important that the tank has a sloped bottom with a low suction point to drain off free water before final drying. The tank should also have a discharge connection some distance above the tank bottom to prevent particles from being sucked out together with the product.
In the storage tanks, for delivery direct to customers, transformer oils normally have a water content of 20 ppm or less. The loading system should be equipped with a particle filter that has a nominal pore size of not more than 5 micrometers.
It is vital to keep the tanks completely dedicated for use with transformer oil. This also applies to all pipes, pumps, hoses and connections that are used to pump the oil to loading stations. All systems used for loading of road tankers, railcars and containers should always be dedicated for transformer oil.
Transformer oils are also extremely sensitive to detergent residues. The cleaning procedure must ensure that no detergent residue remains after cleaning. Any transport or transfer in a non-dedicated system must always be safeguarded through testing of sensitive parameters, particularly dielectric dissipation factor and interfacial tension.
Steam turbine oils are also extremely sensitive to contamination by other oils. Ingress of water into steam turbine oils is always possible, whether from steam from leaking shaft seals, water leaks from coolers or condensation from humid air.
Steam turbine oils require excellent demulsibility and air-release properties so that entrained water or air are shed rapidly. Persistent emulsions can combine with insoluble oxidation products or dirt to form sludges, which can be very damaging to plain bearings. Contamination of steam turbine oils by engine oils, metalworking fluids or used compressor oils is likely to affect steam turbine oil demulsibility and air release severely. So after blending, steam turbine oils should be stored and handled to avoid contamination.
David Whitby is chief executive of Pathmaster Marketing Ltd. in Surrey, England. You can reach him at pathmaster.marketing@yahoo.co.uk.