Emulsifiers 201: Analyzing performance with surface science
Tom Oleksiak, Jennifer Ineman, Joe Schultz, Monica Ford & Kevin Hughes | TLT Webinars September 2014
Direct analytical techniques for understanding and evaluating emulsifier chemistries.
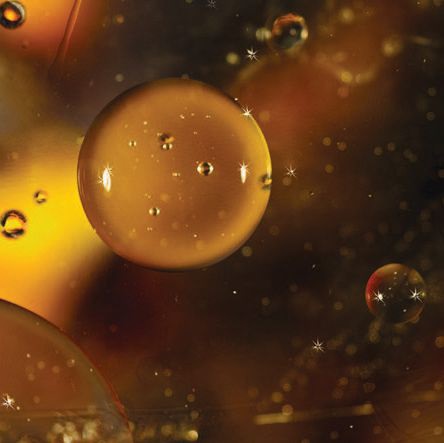
www.canstockphoto.com
KEY CONCEPTS
•
Surface science is used to understand why coolants work better and help in the development of next-generation products.
•
Surface tension can be evaluated under equilibrium or dynamic conditions.
•
Emulsions with narrower particle size distributions are more stable than an emulsion of similar particle size with a broader distribution.
MEET THE PRESENTERS
This article is based on a Webinar originally presented by STLE University. “Emulsifiers 201” is available at
www.stle.org: $39 to STLE members, $59 for all others.
Tom Oleksiak is a chemist for The Lubrizol Corporation’s metalworking additive research group. Tom has 24 years of experience in metalworking formulation and additive development and is a graduate of Duke University with a doctorate in physical chemistry. You can reach him at
tom.oleksiak@lubrizol.com.
Jennifer Ineman is a product manager for Lubrizol where she is responsible for providing technical support to metalworking technical consultants and formulators in the field. While at Lubrizol, she has worked in the areas of chemical synthesis and as a formulator in metalworking R&D and has 10 years of experience as a chemist in the lubricant industry. You can reach her at
jennifer.ineman@lubrizol.com.
Joe Schultz is a technical services chemist for Lubrizol’s industrial metalworking additives group where he provides formulation, application and troubleshooting support for customers and end-users and has worked in the lubricant industry for 18 years. Prior to joining Lubrizol, he worked for a variety of MWF suppliers in roles supporting and formulating specialty metalworking chemistries for producing and finishing steel. You can reach him at
joe.schultz@lubrizol.com.
Monica Ford works in Lubrizol’s applied sciences group as a colloids research engineer where she’s responsible for providing technical support for the characterization, optimization and troubleshooting of colloid-containing formulations from all segments within Lubrizol. Prior to joining Lubrizol, she completed a post-doctoral fellowship at the University of California at Santa Barbara and is a graduate of the University of Florida with a doctorate in chemical engineering. You can reach her at
monica.ford@lubrizol.com.
Kevin Hughes is a research engineer for Lubrizol’s applied sciences group. His areas of expertise include surface and colloid science. He is a graduate of Cornell University with a doctorate in chemical engineering. You can reach him at
kevin.hughes@lubrizol.com.
Tom Oleksiak
Jennifer Ineman
Joe Schultz
Monica Ford
Kevin Hughes
IN THE EARLY 1900s, it was discovered that an oil-in-water emulsion could provide the excellent cooling properties of water and the lubricity of a formulated oil. This discovery led to the marketing of the first soluble oils—oils designed to emulsify in water. Forming an emulsion of oil and water requires the use of emulsifiers. These are molecules that facilitate the combination of two immiscible liquids to form an emulsion. Understanding emulsifier chemistry can lead to the development of differentiated metalworking coolants.
Several topics were reviewed in the Webinar article: “Emulsifiers 101: Who says oil and water can’t mix,” published in the September 2013 TLT (
available digitally at www.stle.org). In the article, the advantages of soluble oils versus straight oils were defined. In addition, basic emulsion chemistry and the types of emulsifiers used in metalworking coolants also were discussed, as well as how the hydrophilic-lipophilic balance (HLB) system can be used to optimize an emulsifier system for a given base oil. We also examined the various water-soluble metalworking fluid types and the advantages and disadvantages of each type.
The goal of Part II of this Webinar article is to discuss how surface science can be used to take metalworking formulation analysis to the next level. As metalworking coolant scientists, we need to understand not only how our emulsifiers affect coolant stability but also how our emulsifier chemistry impacts coolant wetting, foam and its ability to handle metal fines. We can measure properties of emulsions and emulsifiers, which are indicative of coolant performance. These parameters include:
•
Oil phase versus water phase interfacial tension
•
Coolant versus air surface tension
•
Contact angle of coolant on metal surfaces
•
Particle size of oil droplets in the coolant.
Surface science can help us make better performing coolants and enable us to understand why coolants work better, leading to the next generation of products.
SURFACE AND INTERFACIAL TENSION
When a liquid is in contact with air, the molecules in the bulk of the liquid are differentiated from the molecules at the surface of the liquid. In the bulk liquid, molecules form weak cohesive bonds between nearest neighbor molecules through forces such as hydrogen bonding and Van der Waals forces. However, molecules at the surface of the liquid do not have as many nearest neighbors, and because of this there are a number of “unfulfilled” weak bonds, giving rise to an excess energy at the surface. This excess energy gives rise to surface tension (
see Figure 1).
Surface tension acts to minimize the total surface area-to-volume ratio in a system. Surface tension is part of the reason for the formation of a meniscus, which we see in a graduated cylinder, and is the force that causes the oil droplets in a coolant emulsion to form spheres. The surface tension also means that work must be done to create a new surface. The pressure of surface tension allows water bugs to skate on the surface of a pond without breaking through.
Surface tension can be evaluated under equilibrium or dynamic conditions. We are interested in surface tension of our coolants because it impacts several coolant parameters. The degree to which our coolants wet metal surfaces is influenced by surface tension, but the impact doesn’t end there. Coolant foam is often a function of surface tension, as is the ability of a coolant to disperse fines in a sump. Ultimately since the surface tension influences wetting, changes in surface tension can impact coolant lubricity, leading to problems with machinability and tool life.
The same force imbalance that was seen at a liquid/air interface is also seen at the interfaces between two immiscible liquids, where it is generally referred to as interfacial tension (IFT). Lack of strong intermolecular forces between molecules of the two liquids gives rise to IFT. In metalworking coolants, the IFT that we are interested in exists at the interface between oil and water.
Emulsifiers are surface-active agents used to ease the formation of interfaces between two or more immiscible liquids. Emulsions, by their nature, comprise a very high oil/water surface area, so emulsifiers are often needed for their formation. They function by having a polar head group that is hydrophilic (water loving) and a nonpolar tail that is lipophilic (oil loving). Because of this structure, emulsifiers collect at fluid interfaces and reduce the interfacial tension by buffering the interactions between the two phases (
see Figure 2). It is usually desirable for an emulsifier to reduce the IFT to a very low level, reducing the energy required to form new interfaces in order to encourage spontaneous emulsification.
CHARACTERIZING MWF EMULSIFIERS
The critical micelle concentration (CMC) is defined as the surfactant concentration at which a significant number of micelles are formed in a particular liquid, usually water. A micelle is formed when individual emulsifier molecules aggregate through interactions between hydrophobic tails, forming a larger structure and leaving the hydrophilic heads exposed to the water (
see Figure 3).
When the CMC is reached, micelles start to form, and any additional emulsifier added to the system will only form new micelles while the concentration of individual emulsifier molecules remains constant. Micelles do not affect the surface tension. So above the CMC, the surface tension levels off. Both CMC and the surface tension at the CMC are important factors in determining emulsification efficiency. The lower the CMC, the greater the number of micelles and the lower the concentration needed to form micelles. The lower the surface tension at the CMC, the more efficient the emulsifier is at partitioning to an interface.
The CMC can be determined using surface tension measurements. Increasing the emulsifier concentration from zero results in a decrease in the surface tension, as an equilibrium is established between the bulk and surface concentrations of the emulsifier. Measuring surface tension can be done by several methods. The method used in this study was the Wilhelmy Plate method (
see Figure 4). In this method, a surface tension measurement is achieved by partially submerging a solid plate (roughened platinum in this case) attached to a microbalance into a liquid. The plate is wetted by the liquid, which means a small additional force proportional to the liquid surface tension is felt by the plate and measured by the microbalance. The CMC is measured by determining the point at which increasing the emulsifier concentration no longer leads to a reduction in surface tension, as illustrated in Figure 5.
The CMC was determined for several emulsifiers. Two sulfonate materials were analyzed—a natural sulfonate (NS) and a Gemini/sulfonate blend (GS). A Gemini emulsifier is an industry term for an emulsifier with two hydrophobes bridged together. In our case, two alkenyl succinic anhydrides are bridged by hydrophile and neutralized with amine. Two other pure Gemini surfactants were examined; these are referred to as G1 and G2. In addition, two nonionic surfactants were analyzed—an ester alkoxylate (EA) and oleyl alcohol with five moles of ethylene oxide (OA5). OA5 is widely used as an emulsifier in metalworking and, therefore, can serve as an industry standard.
The CMC data for the emulsifiers are presented in Figure 6. There is no clear trend in the data noted for the studied surfactants by chemical type. The EA emulsifier has the highest CMC and the highest surface tension at the CMC. The lowest CMC values are observed for the G1 emulsifier and the OA5 emulsifier. These two emulsifiers should have the good emulsifying power.
Emulsifying power is not solely indicated by CMC. Recall that this measurement examines the surfactants without oil present. Thus, the effect of the emulsifier on the IFT between the target oil and water also must be considered. As previously indicated, a low IFT is desirable to encourage spontaneous emulsification. As with surface tension, there are a number of methods for measuring IFT. In this study, IFT was measured using a pendant drop method. In this test, a droplet of liquid (water in this case) is formed on a hollow needle within a second immiscible liquid (oil in this case), as shown in Figure 7. Two opposing forces determine the shape of the drop. Gravity pulls and lengthens the drop, while the IFT holds the drop up in a spherical shape due to the energy penalty associated with forming a new interface (
see Figure 8).
If the densities of the two phases are known, then the effect of gravity on the drop can be determined, and the shape of the drop then can be used to calculate the IFT. An effective emulsifier will lower the IFT significantly, encouraging spontaneous emulsification and generally decreasing the energy needed to form new oil/water interfaces.
IFT data corresponding to the analyzed emulsifiers are presented in Figure 9 for three different basestocks—the results show a clear trend. The IFT for emulsifiers containing sulfonate is significantly higher than the other surfactants. In addition, very low IFT is observed for nonionic emulsifiers. The Gemini emulsifiers have an IFT closer to nonionic surfactants, suggesting that the Gemini emulsifiers studied would have emulsification spontaneity more similar to nonionic surfactants.
FORMULATION ANALYSES
Ultimately, as metalworking scientists, we are interested in the properties of our formulations. For this reason, the emulsifiers were analyzed in a standard metalworking soluble oil formulation (
see Figure 10). These formulations were tested in emulsion form. The emulsions were examined by equilibrium and dynamic surface tension, as well as contact angle and particle size. Using these techniques, a metalworking coolant formulation can be understood well beyond a simple characterization of emulsion stability.
FORMULATION EQUILIBRIUM AND DYNAMIC SURFACE TENSION
Equilibrium surface tension measurements were completed using the Wilhelmy Plate method previously described. However, surface scientists are often not only interested in equilibrium surface tension but also dynamic surface tension. The dynamic surface tension is an indication of the surface tension for a given time after a new surface is formed. Depending on the nature of the system (viscosity, diffusion effects, sticking coefficients and others), surface tension can reach equilibrium on a time scale of seconds to hours rather than milliseconds. Therefore, for dynamic processes, it is desirable to measure the surface tension as a function of surface age (i.e., as a function of time). The measurement of surface tension as a function of surface age is described as dynamic surface tension. An example of this measurement is given in Figure 11.
In this study, dynamic surface tension was measured using maximum bubble-pressure tensiometry. This measurement relies on the fact that the pressure within an air bubble submerged in a liquid varies slightly with the air/liquid surface tension. By precisely measuring the pressure within an air bubble submerged in a liquid, the surface tension can be measured. Maximum bubble-pressure tensiometry has the advantage of being able to measure dynamic surface tension at low surface age by quickly forming and measuring the pressure within air bubbles. Here, measurements were made as a function of surface age from 10 milliseconds up to 10,000 milliseconds (or 10 seconds), where the surface tension approaches equilibrium conditions. Essentially, we are measuring the evolution of surface tension from the formation of a fresh interface until it approaches equilibrium conditions.
Results of equilibrium surface tension measurements for the formulated emulsions are presented in Figure 12. The lowest equilibrium surface tensions were observed for the nonionic surfactants EA and OE5. The equilibrium surface tension of the other surfactants is somewhat higher. If one were to make predictions about our coolants using the equilibrium surface tension results, we would predict that the nonionic emulsifiers would wet metal better and be higher in foam than the other surfactants used.
The metalworking process, however, is very dynamic. If coolant wetting is needed on a vertical surface, then this wetting must take place in matter of milliseconds. Likewise, in predicting foam in a sump, the metalworking emulsion is being pumped and moved at high rates of speed. For these reasons, it is often more appropriate to use dynamic surface tension in a metalworking process.
Dynamic surface tension data for the analyzed formulations are reported in Figure 13. In comparing the curves, the OA5 and GS surfactants have very different behavior. The OA5 has the highest dynamic surface tension, while the GS has the lowest. A more complete comparison of the emulsifiers in formulation under equilibrium and dynamic conditions is given in Figure 14. It is observed that the dynamic surface tension at one-second surface age is much higher than the equilibrium surface tension, and that the equilibrium surface tension of each of the emulsifiers in formulation is not necessarily correlated to the dynamic surface tension.
The importance of studying dynamic surface tension is more readily observed in the foam results reported in Figure 15. In a slightly modified formulation, it can be seen that the OA5 displayed the lowest foam properties when comparing to GS and G2 emulsifiers in formulation. The low equilibrium surface tension of OA5 does not predict this behavior; rather the low foam results directly correlate to the higher dynamic surface tension results at one-second surface age (recall that higher surface tension generally leads to lower foam). This highlights the importance of probing beyond simple surface tension measurements in order to accurately predict and understand coolant performance.
FORMULATION CONTACT ANGLE
In the above discussion of surface tension, we referenced the correlation of surface tension of a liquid to its wetting tendency on a metal surface. A direct measurement of surface wetting tendency can be obtained through contact angle measurements. The contact angle is the angle formed between a liquid droplet and a solid surface (
see Figure 16). In general, lower contact angle means better surface wetting. The contact angle depends on a number of parameters, including the liquid/air surface tension, the solid/air surface tension (commonly called the surface energy for solids) and the solid/liquid surface tension. Thus, the contact angle of a given liquid is dependent upon the specific solid surface. For example, iron has a higher surface energy than aluminum, making it easier to wet. Experienced formulators have likely experienced the difficulty of wetting onto aluminum parts with some formulations.
To measure contact angle, a drop of the test liquid is delivered to the test surface via a hollow needle, then the contact angle is determined through optical image analysis. In metalworking systems, it is desirable for the coolant to wet rapidly, so we are not only interested in the equilibrium contact angle but also how quickly the equilibrium wetting condition is obtained. Therefore, the contact angle is reported as a function of time (
see Figure 17).
A study was conducted to examine the effect of contact angle on soluble oil performance in the IP-287 corrosion test. This test was conducted using polyisobutylene succinic anhydride (PIBSA) salts and a synthetic sodium sulfonate as emulsifiers in a generic soluble oil formulation. The data shown in Figure 18 indicate poor corrosion performance for the PIBSA salt formulation and good corrosion protection for the sulfonate containing formulation. Addition of sulfonate and wetting agent to the PIBSA salt formulation indicates that the corrosion inhibition can be improved. The improvement in the corrosion inhibition is correlated to a lower contact angle. For this formulation, performance in corrosion prevention is correlated to improved wetting.
Referring back to the formulations mentioned earlier, the G2- and OA5-based formulations were examined on an aluminum surface (
see Figure 19). Very rapid wetting is observed for the G2 chemistry on aluminum. These data suggest that when rapid wetting is needed, the G2 formulation would perform better than the OA5 formulation. Experienced formulators have often found wetting to be key to the lubrication performance of metalworking coolants on aluminum. This case illuminates the necessity to measure contact angle on the metal of interest.
FORMULATION PARTICLE SIZE
Recall from our previous discussion that the force of surface tension causes the oil droplets in a coolant emulsion to form spheres. The size of the oil droplets in the coolant can be measured. It has been well established by emulsion scientists that particle size can correlate to emulsion stability. A lower-median particle size is observed for emulsions, which are more stable. In certain processes such as metal rolling, it has also been found that a larger particle size correlates to better lubricity.
Although particle size has been used for decades for measuring stability in larger particle metal rolling emulsions, metalworking coolants measurements have been more difficult because the coolants often have particle sizes of less than 1 micron. In the last 10 years, the technique of dynamic light scattering has enabled measurements of metalworking coolant particle size. This technique offers a rapid determination of coolant emulsion stability. Generally, results are reported as the average or median particle size diameter along with the polydispersity. A low polydispersity is indicative of a narrower particle size distribution. Emulsions with narrower particle size distributions are often found to be more stable than an emulsion of similar particle size with a broader distribution. The formulations were examined for particle size for the various emulsifiers tested (
see Figure 20). IP-263 emulsion stability data are included for comparison. All emulsions were found to have good stability in low hardness (114 ppm) water. In 400-ppm hardness water, the emulsions with the larger particle size and higher polydispersity in tap water are found to be unstable in 400-ppm water. Figure 21 suggests that for this particular formulation, a maximum particle size value of 150 nm could be used to determine which emulsions were hard water stable. Stability measurements are usually conducted for a 24-hour period, while particle size can be determined in a matter of minutes. Particle size measurements can be used as a time-saving tool for metalworking formulation.
CONCLUSION
Analyzing emulsifiers can distinguish performance in two ways:
1.
Critical micelle concentration can be a measure of emulsifier efficiency.
2.
Interfacial tension can be used as an indicator of emulsion spontaneity.
Surface science can be used to differentiate coolant formulation performance and as a useful troubleshooting tool:
1.
When measuring surface tension, the dynamic surface tension is often more consistent with the timescale of metalworking coolant processes.
2.
Contact angle gives a direct measurement of coolant wetting and may correlate to corrosion protection. It is critical to measure on the metal of interest.
3.
Particle size can be used as a rapid screening tool for emulsion stability and emulsion hardness tolerance.