The drive for more fuel-efficient engines
Jeanna Van Rensselar, Contributing Editor | TLT Feature Article September 2014
Why the combustion engine and improving lubrication is the most practical route.
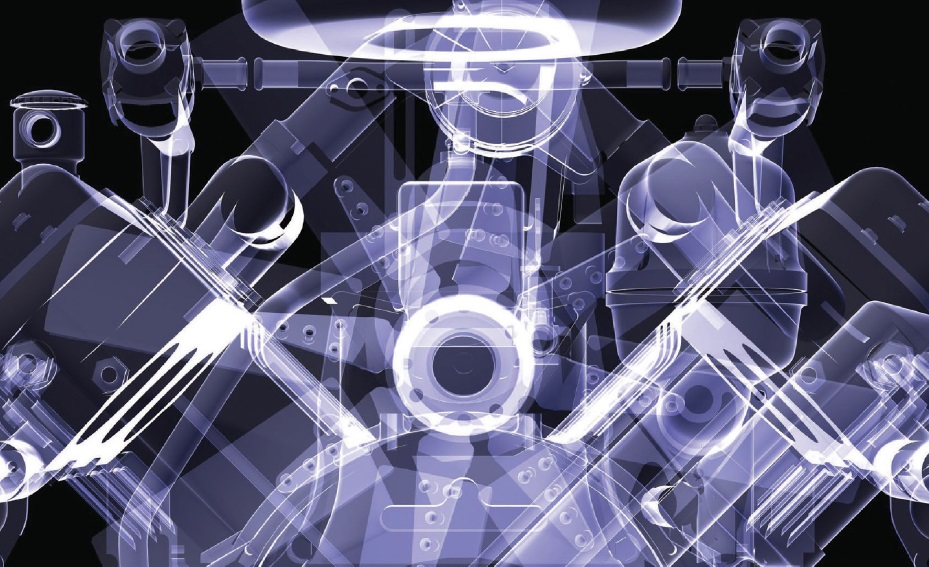
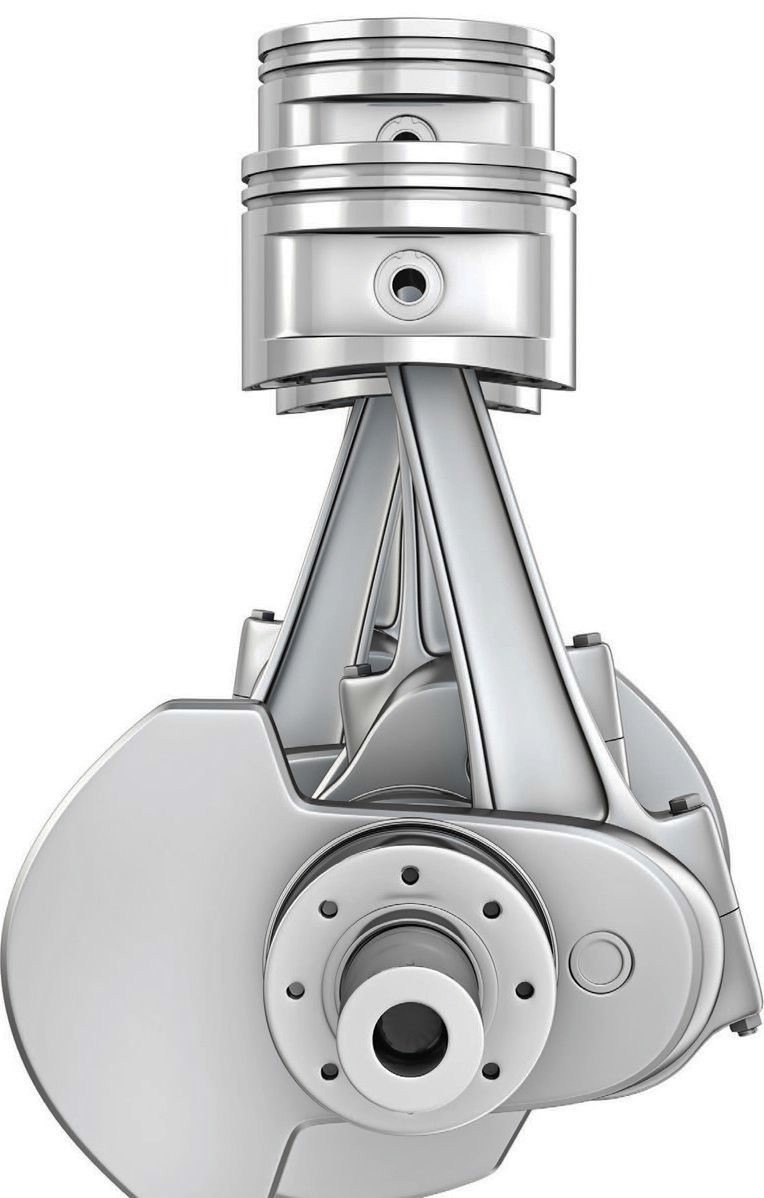
www.canstockphoto.com
KEY CONCEPTS
•
Improving fuel efficiency means either advancing the internal combustion engine or developing alternative engines.
•
The only other successful engine system in the consumer market is the gas-electric hybrid.
•
New engine technologies are plagued by obstacles that are proving difficult to overcome.
FOR NOW AND THE FORESEEABLE FUTURE, most experts agree that the internal combustion engine is still our best option for powering vehicles. So as government restrictions, consumers and the realities of a dwindling petroleum supply propel the drive toward improved fuel economy, it makes sense to stop diluting efforts on alternative engines and focus on improving the fuel efficiency of combustion engines. After all, they’ve been working quite well for more than 150 years.
CONVENTIONAL INTERNAL COMBUSTION ENGINE VEHICLES
Called one of the greatest accomplishments by humans, the internal combustion engine (ICE) first existed as a concept with Leonardo da Vinci in 1509 and then as an actual four-stroke engine developed and built by Nikolaus Otto in 1876. While the engine is used in stationary applications, its real value has always been mobile applications—first small motorized devices like carts and then cars and aircraft. One of the reasons why ICEs continue to dominate is the energy density (density to both weight and volume) of petroleum—giving ICE-powered vehicles a range that remains superior to almost all other vehicles. Even in today’s most advanced hybrid vehicles, the ICE is still the primary power supply (
1).
Widely adopted upgrades like incremental engine downsizing and weight reduction have doubled fuel efficiency during the last 20 years, but the push is strong for continued improvement. Among the areas being scrutinized for improved fuel efficiency are:
•
The disconnect between engine fuel efficiency characteristics and actual driving conditions
•
The waste of energy caused by braking
•
The waste of energy caused by engine idling
•
The waste of energy caused by friction
•
The waste of energy caused by reducible vehicle weight.
More fuel-efficient ICEs also have been proposed and prototyped, including the Scuderi Split Cycle Engine. And there are plenty of research projects underway. One of these is a project at Argonne National Laboratory (ANL) in Argonne, Ill., to develop a laser ignition system as a more fuel-efficient alternative to the spark-ignition system.
ALTERNATIVE-ENERGY ENGINES (2)
All alternative fuel vehicles come with issues preventing their widespread adoption (
3). But for some alternatives (hybrids), the issues have been nearly overcome, while for others (hydrogen fuel cells and natural gas) the issues are serious obstacles that may prove fatal to the technology. During the keynote address at the STLE 2014 Annual Meeting & Exhibition last May, Dr. Don Hillebrand, director of the Center for Transportation Research at ANL, pointed out the lack of a viable fuel infrastructure in the foreseeable future as the bane of nearly all promising alternative fuel technologies—from ethanol to electric to natural gas to hydrogen (
4).
PRIMARY AND ANCILLARY BATTERY-POWERED VEHICLES
The two main types of batteries used in battery-powered electric vehicles are nickel metal hydride (NiMH) and lithium-ion (Li-ion) batteries. NiMH batteries are used as a secondary energy source in 95 percent of all hybrid electric vehicles (HEVs) such as the Toyota Prius. Li-ion batteries are used as primary energy sources in battery-powered electric vehicles (BEVs) such as the Nissan Leaf.
Battery-powered electric vehicles (BEVs) have some advantages over conventional ICE vehicles such as high-energy efficiency and zero tailpipe emissions. While significant progress has been made in developing automotive batteries, major challenges remain such as:
•
Reducing the cost, size and weight of battery packs
•
Improving battery safety
•
Prolonging the battery life; the estimated battery life is around 150,000 miles or 10 years, while the current average life of all vehicles is 14 years
•
Reducing the battery charging time (
5).
BEVs are currently price competitive with conventional cars. However, energy density is still an issue.
Hybrid electric vehicles (HEVs). Conventional ICE vehicles perform well and have a relatively long operating range. However, they have the disadvantages of poor fuel economy and high carbon emissions.
HEVs, which combine the best features of two power sources, gain the advantages of both ICE vehicles and BEVs and overcome their individual disadvantages. HEVs are more expensive than conventional vehicles because of the extra components and complexity required but less expensive than BEVs due to the high cost of Li-ion batteries.
Comparison of 2012 Model Year Vehicle Specifications for 5 Power Types*
*Information (except for Natural Gas) from Current Status of Hybrid, Battery and Fuel Cell Electric Vehicles: From Electrochemistry to Market Prospects by Bruno G. Pollet, Iain Staffell and Jin Lei Shang, p. 25, natural gas vehicles were not included.
Comparison of 2012 Model Year Vehicle Specifications for 5 Power Types (Note: Most information is from Current Status of Hybrid, Battery and Fuel Cell Electric Vehicles: From Electrochemistry to Market Prospects) by Bruno G. Pollet, Iain Staffell and Jin Lei Shang, p. 25. Natural gas information was added.
Hydrogen fuel-cell vehicles (FCEVs). Hydrogen has an energy content by weight that is about three times higher than petroleum and natural gas, but it has an energy content by volume that is about 3,000 times less than petroleum. This makes storage and distribution prohibitively costly. Hydrogen storage on board the vehicle is the main issue that needs to be resolved before FCEVs can become commercially viable. But even if storage is resolved, today’s fuel cell systems would still be too expensive and fragile. The technology investment in the fuel cell supply chain is in serious decline. Honda’s FCX Clarity is an FCEV that has been in very limited production since 2009 and is currently available for lease only.
Natural gas vehicles (NGVs) suffer from the same fuel storage issues as FCEVs. However, the abundance of natural gas in the U.S. has made them an attractive alternative for fleet vehicles that can return to the same depot for refueling every day (overcoming the refueling infrastructure problem). Some municipalities have been using NGV buses for nearly a decade, and fleet-intensive companies such as FedEx and UPS recently made major commitments to NGVs. But at this time, because of high pressure compression and fuel storage issues and the lack of a practical way to refuel them, there is not a viable natural gas passenger car on the market.
Although FCEVs and NGVs suffer from some of the same obstacles, the reason that NGVs are still on the table and FCEVs are effectively not is the huge disparity in fuel cost. “Natural gas for power generation and transportation is a very attractive option due to its clean burning properties and lower CO2 emissions,” Munidhar Biruduganti, principal research engineer at ANL, says. “The price decline of natural gas since 2009 has impacted research into alternative gaseous fuels. If it sustains at the current levels, there will be more engines adopting natural gas. However, with the issues surrounding fracking techniques coming to light, the price advantage of natural gas remains to be seen.”
GLOBAL ENERGY LOSS DUE TO FRICTION IN TRUCKS AND BUSES
A 2014 study,
Global Energy Consumption Due to Friction in Trucks and Buses, by Kenneth Holmberg, Peter Andersson, Nils-Olof Nylund, Kari Mäkelä and Ali Erdemir concluded the following:
•
In heavy-duty vehicles, 33 percent of the fuel energy is used to overcome friction in the engine, transmission, tires, auxiliary equipment and brakes. The parasitic frictional losses (with braking friction excluded) are 26 percent of the fuel energy. Only 34 percent of the fuel energy is used to move the vehicle.
•
47.5 million gallons of fuel was used worldwide in 2012 to overcome friction in heavy-duty vehicles. Any reduction in friction reduces exhaust and cooling losses, as well.
•
Globally a single truck uses an average of 396 gallons of diesel fuel a year to overcome friction losses; a truck and trailer combined average 3,302 gallons; a city bus 3,354 gallons and a coach bus 1,875 gallons.
•
By taking advantage of new technology for friction reduction in heavy-duty vehicles, friction losses could be reduced by 14 percent in the short-term (4 to 8 years) and by 37 percent in the long-term (8 to 12 years).
•
Hybridization and electrification are expected to penetrate only certain niches of the heavy-duty vehicle sector. In the case of city buses and delivery trucks, hybridization can cut fuel consumption 25-30 percent, but there is little to gain in the case of coach buses and long-haul trucks. Downsizing the internal combustion engine and using recuperative braking energy also can reduce friction losses.
•
Electrification is best suited for city buses and delivery trucks. The energy used to overcome friction in electric vehicles is estimated to be less than half of that conventional diesel vehicles.
THE ROLE OF LUBRICANTS
There are two ways that lubricants contribute to fuel efficiency: reducing energy- robbing friction loss and enabling the development of high-performing, fuel-efficient engines. Both of these functions are essential for reaching increasingly stringent fuel efficiency standards.
Friction loss in vehicles includes the energy used to overcome the rolling resistance of tires, brake contact, pumping losses and the rubbing and turning of various mechanical parts in the engine and transmission systems.
RESEARCH INTO PARASITIC FRICTION LOSS
Some sources of friction are unavoidable, but others can either be reduced or eliminated. STLE member Dr. Peter M. Lee, CEng, principal engineer/tribologist for Southwest Research Institute in San Antonio, Texas, explains, “Parasitic losses from water and oil pumps and chain and belt drives can be reduced. Careful design of the transmission and drivetrain will allow the engine to operate within its most efficient range. Further enhancements can also be made to both the gasoline and diesel combustion strategies (
6).”
A recent study to determine the source and magnitude of frictional losses in automobiles was recently conducted by STLE Fellow Dr. Ali Erdemir, ANL Distinguished Fellow and senior scientist, and Dr. Kenneth Holmberg and Peter Andersson of Finland’s VTT Technical Research Centre (
7). According to the study, the energy output of fuel in a car engine breaks down like this:
•
29 percent is used for cooling
•
33 percent is depleted in exhaust
•
38 percent is used for mechanical energy (33 percent for friction losses and five percent for air resistance).
ARGONNE NATIONAL LABORATORY’S LASER IGNITION SYSTEM
The research team at ANL’s Distributed Energy Research Center is developing the Advanced Laser Ignition System (ALIS), which contributes to both higher operating efficiency and lower emissions. Munidhar Biruduganti, principal research engineer at Argonne National Laboratory, explains, “Fuel-efficient engines use less fuel relative to air (lean-burn). However, with this strategy and the current ignition system, charge misfiring limits potential efficiency gains.”
The ALIS extends the lean-burn limit to a new level. Laser ignition enables an engine to operate at leaner conditions (and at higher boost pressures) relative to conventional spark ignition. This improves the engine’s efficiency.
The system uses free-space transmission of high-power pulsed lasers to create an ignition. Compared to a spark ignition system, it also has higher combustion stability. Single-cylinder engine test results showed a 60-70 percent reduction in NOx emissions and/or efficiency gains of up to three percent. Subsequently, the first demonstration of the ALIS was performed on a Cummins six-cylinder engine. The demonstration showed laser operation on all six cylinders and proof of higher efficiencies and lower NOx emissions.
With current technology, the authors concluded that only 21.5 percent of the fuel’s energy output in a combustion engine is actually used to move the car. But Erdemir also cites technologies that reduce the impact of friction. Included are new surface coatings, surface textures, lubricant additives, low-viscosity lubricants, ionic liquids and low-friction tires.
The piston assembly is the source of greatest mechanical friction loss in most engines—this is primarily because piston faces must slide against the cylinder wall to create the seal necessary to keep the lubricant from burning.
Emmanuel Wornyoh, assistant professor of mechanical engineering at University of Wisconsin-Milwaukee, says, “My research has confirmed generally held beliefs that our understanding of basic friction is still rudimentary. Yet, to improve engine efficiency we need to clarify the causes and effects of friction at a dynamic sliding interface. Doing this requires deterministic multiscale models for surface roughness, friction coefficient and wear coefficient under dynamic conditions. By contextualizing the appropriate friction-velocity coupling effects in dynamic modeling, a universal efficiency criterion may be found that should synergize the efforts of tribologists, dynamicists and material scientists in fighting friction for energy efficiency and sustainability (
8).”
Lee adds, “For new vehicles, the largest fuel economy improvements will be achieved through increasing engine efficiency, followed by reduction in pumping losses and reducing parasitic losses. Lubricant and additive development to reduce friction will continue to play an essential role. But for existing vehicles, the lubricant is the only financially practical route to improving fuel economy.”
SUPER KNOCK
Super knock is a strange phenomenon in newer, downsized high-performance engines that combine turbocharging and direct-injection technology for better braking at low speeds (with the goal of improving fuel efficiency). Super knock is so violent that it can quickly damage engine components. So far, because it is so sporadic and random, it has been difficult to diagnose and control. Researchers are hoping that lubricants might hold the answer.
Dr. Peter M. Lee, principal engineer/tribologist for Southwest Research Institute, explains, “There is still a lot that is not known, but it is quite well accepted that small amounts of oil entering the combustion chamber combine with fuel droplets to reduce their ignition temperature.”
One variable that reduces the propensity toward super knock is oil formulation. For this reason, Lee advocates developing a compatible lubricant for the combustion strategy while the engine is still in the design phase—not as an afterthought. “Engine manufacturers that utilize this methodology will likely see incremental gains in this area,” he says.
MITIGATING PARASITIC FRICTION LOSS
Corporations are making progress in reducing the friction losses stemming from the piston assembly. As far back as 2006, Mercedes-Benz developed Nanoslide, a cylinder-coating technology it first used on the 6.3-liter AMG V-8. During the Nanoslide coating process, cylinder walls are sprayed with an ultrathin layer (4/1000ths to 6/1000ths of an inch) of a molten iron-carbon al loy. A special finishing process creates a smooth surface on the ultra-hard coating. The process also opens tiny pockets in the metal that retain oil for lubrication. Mercedes reports that in the ML350’s diesel V-6 engine, Nanoslide has reduced fuel consumption by three percent.
Other automakers have taken different approaches to producing cylinder surfaces that are as smooth and wear resistant as possible. Honda developed a technique it calls
plateau honing for the cylinder walls of its engines. Rather than a standard single-step machining process with a honing tool—an abrasive that smoothes the cylinder to the required finish—plateau honing uses two stages of grinding to produce a surface that is ultra smooth yet leaves a pattern of very fine grooves to hold oil. Chrysler uses a laser to burn a honing pattern into cylinders (
9).
Because viscous oil requires more power to move through the engine, automakers are specifying lighter viscosities to save fuel. GM designed a computer-controlled, two-stage cooling-system thermostat for its 2.5-liter engine that allows the engine to run hotter (and the oil to be thinner) when conditions are not extreme.
ANL researchers, along with the U.S. Department of Energy and industry partners, identified several major initiatives to reduce friction loss that focuses on two areas:
1.
The role of viscosity and asperity friction on parasitic losses in engines and driveline components.
2.
The development of advanced additives and base fluids.
Munidhar Biruduganti, principal research engineer at Argonne National Laboratory, demonstrates the ETECH single cylinder natural gas research engine. The ETECH engine is used to test advanced technologies such as laser ignition, air separation membranes and others to simultaneously improve engine efficiency and reduce emissions. It is a spark-ignited natural gas engine, which is representative of a medium/heavy duty truck engine or a mid-range power generation engine. (Courtesy of Argonne National Laboratory)
Within those two areas, they are focusing on the following:
•
Additives. Nanoadditives (nano-boron and carbon-based compounds) reduce asperity friction to enable use of low-viscosity fluids with a goal of reducing boundary friction by 50 percent or more.
•
Base fluids. Novel base fluids with enhanced flow properties to minimize viscous shear losses. The goal is to enable use of lubricants with up to 25 percent lower viscosities than today’s lubricants.
•
Engineered surfaces. Non-ferrous surfaces that promote formation of tribofilms with improved friction and wear performance, with a goal of reducing boundary friction by up to 50 percent.
•
Modeling. Models of lubricant film formation that correlate friction and wear performance with lubricant film structure and chemistry (specifically asperity friction and scuffing). The goal is to replace the current investigative approach with the development of additives that derive from a science-based mechanistic model.
•
Performance validation. Performance evaluation protocols to improve the lab-scale techniques for reliable prediction of engine performance with a goal of making greater use of rapid, cost-effective, lab-scale rigs to reduce cost and time-to-market of advanced lubricants (
10).
LITHIUM-ION (LI-ION) BATTERIES
While Li-ion batteries store more energy than NiMH, they suffer from major issues such as cost, wide operational temperature ranges, material availability (e.g., Li), environmental impact and safety. At present, Li-ion batteries are expensive, but it is anticipated that the price will decline so rapidly that they will be the least expensive rechargeable batteries by 2022. Currently a replacement battery for a Nissan Leaf is $5,500.
NICKEL METAL HYDRIDE (NIMH) BATTERIES
The major advantage that NiMH has over Li-ion batteries is safety. Furthermore, NiMH batteries are preferred in industrial and consumer applications due to their design flexibility (ranging from 30 Ampere hours to 250 Ampere hours), environmental acceptability, low maintenance, high power and energy densities, cost and, most important, safety. The total price of the battery pack for a hybrid ranges from $600 to $3,000.
As part of ANL’s tribology research group, Erdemir is involved with the following projects geared toward reducing friction. These include:
•
Boron-based advanced nanolubricants can be added to existing oils to improve lubricity by up to 50 percent. These additives are environmentally safe, inexpensive and have the capacity to enhance the antifriction and antiwear properties of sliding surfaces in both diesel- and gasoline-powered engines. The unusual lubricating mechanism of boron-based additives in these oils and fuels is controlled by its unique chemical structure and its ability to form a strongly bonded protective boundary film on rubbing surfaces.
•
Super-hard and slick nanocomposite coatings improve the reliability and performance of moving mechanical systems, including engines. ANL’s nanocomposite reduces friction by 80 percent, increasing energy efficiency, eliminating wear and scuffing-related failures and extending the life of mechanical components. This technology won an R&D 100 Award and has been licensed to automotive manufacturers.
•
Ultra-fast boriding is an innovative heat treatment process that uses boron compounds to convert surfaces into extremely hard, thick layers that provide superior wear resistance. Compared to existing thermal treatment processes, ANL’s ultra-fast boriding method provides much higher energy efficiency, productivity and near-zero emissions. After successfully boriding multiple quantities of industrial parts with a pilot-scale reactor, the ANL technology was licensed to Bodycote for full-scale commercialization (
11).
Cummins QSK19G natural gas engine (for power generation, not autos); Argonne Engine Test Cell. The Advanced Laser Ignition System (ALIS) was used on the Cummins natural gas engine to demonstrate better efficiency than stock ignition systems. (Courtesy of Argonne National Laboratory)
THE SCUDERI SPLIT CYCLE IC ENGINE (12)
The Scuderi engine is an alternative internal combustion engine that has paired cylinders, each of which performs two of the strokes of a conventional four-stroke engine. The compression cylinder performs intake and compression. The power cylinder performs combustion and exhaust. Compressed air is transferred from the compression cylinder to the power cylinder through a crossover passage. Fuel is then injected and fired to produce the power stroke. In a conventional internal combustion engine (ICE), each cylinder performs all four strokes per cycle.
Patent holder, The Scuderi Group says that the engine is more fuel efficient and produces fewer toxic emissions than a convional ICE. The downside is that (depending on the vehicle’s mechanical design) the engine may require an extra valve per pair of cylinders.
“Generally the current position in the industry is that engine manufacturers produce engines with various coatings, and the lubricant industry supplies lubricants for the engines,” Lee explains. “Lubricants are rarely formulated to work specifically with these coatings and non-conventional materials, but they should be.”
Lee cites the example of diamondlike carbon coatings that are generally believed to be inert. “We have done work that shows they do respond differently to different additive packages,” he continues. “So there is an important role for the lubricant to play in protecting these non-conventional materials and a great deal of research work and collaboration between engine, lubricant and additive manufacturers is required. A few engine and lubricant manufacturers do work together from the beginning of an engine design, but this is not the norm.”
Lee is confident that the continued drive toward lower viscosities and high stress operating conditions will continue to spur development of coatings and additives. “From experiments we have undertaken, if the correct combination of coating, lubricant and additive package is brought together, significant improvements in fuel economy can be achieved,” he says. “This will require engine and lubricant manufacturers to work together from the start of engine development.”
So when it comes to improving fuel efficiency, basically there are two routes to go:
1.
Continue to focus on ICEs and mitigating their shortcomings.
2.
Develop new, more energy-efficient engines.
Practically speaking, it makes sense to improve the ICE vehicles that already dominate the market and for which an established refueling infrastructure is already in place. But to meet fuel and emission standards, engineers and researchers still need to make rapid improvements in a relatively short period of time.
“The problem of improving energy efficiency is hardly computational since we have access to unprecedented computational power and advanced numerical schemes,” Wornyoh says. “Rather, fundamental theoretical modeling for predicting and matching experimental friction-based engine efficiency seems lacking. The next generation of engine efficiency innovators will need to understand how to formulate basic physics models that capture at multiple scales, nonlinear friction-based asperity deformations and other mechanical, thermal and physical factors that affect efficiency.”
Wornyoh concludes, “To win the battle of energy efficiency and environmental sustainability, we must restrategize our ongoing fight with friction by carefully reassessing what has worked and which of our tools need transforming.”
REFERENCES
1.
The hybrid vehicle’s ICE is smaller and runs at a high efficiency point longer than the ICE in a conventional car.
2.
Much of the information in this section is from
Current Status of Hybrid, Battery and Fuel Cell Electric Vehicles: From Electrochemistry to Market Prospects by Bruno G. Pollet, Iain Staffell and Jin Lei Shang: available
here.
3.
Alternative fuel is anything other than petroleum;
renewable fuel is anything except (primarily) petroleum, natural gas and coal.
4.
From keynote address at the STLE 2014 Annual Meeting & Exhibition; PDF available
here.
5.
The Nissan Leaf can take up to eight hours to fully charge from a standard domestic outlet or 30 minutes from a 3-phase AC socket.
6.
Note Lee is also chair of STLE’s Engine and Drivetrain Technical Committee.
7.
Fact or Friction: Friction losses significantly impact fuel consumption; available
here.
8.
Wornyoh is also director of the Tribology and Energy Diagnostic Laboratory at UWM and co-director of the UWM Industrial Assessment Center.
9.
Click
here.
10.
Click
here.
11.
Click
here.
12.
Click
here.
Jeanna Van Rensselar heads her own communication/public relations firm, Smart PR Communications, in Naperville, Ill. You can reach her at jeanna@smartprcommunications.com.