Adhering to new processes
Dr. Edward P. Becker | TLT Automotive Tribology April 2014
Ford’s decision to use more aluminum on its best-selling vehicle opens opportunities for tribologists.
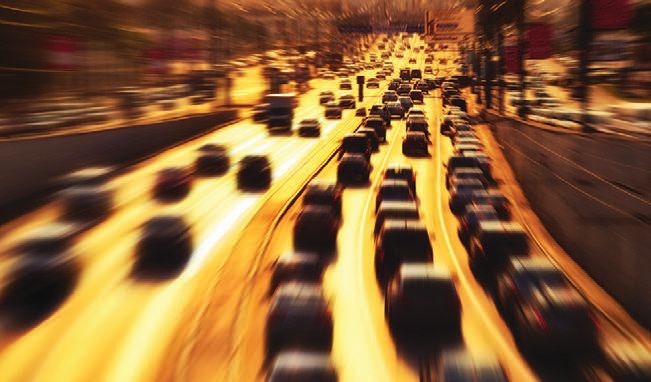
Adhesive bonding is critically important because the average age of a car on U.S. roads is 11 years and rising.
www.canstockphoto.com
THE NORTH AMERICAN INTERNATIONAL AUTO SHOW (NAIAS), held in Detroit each January, is a great opportunity for industry watchers to see the latest trends from automobile manufacturers all over the world. Unsurprisingly, NAIAS 2014 showcased numerous advances in fuel economy for both the near and far term. One very interesting introduction is the new Ford F-150 pickup truck, which the manufacturer claims will weigh about 700 lbs. (320 kg) less than the vehicle it replaces. The weight savings is primarily due to the replacement of steel body panels with aluminum.
Aluminum has steadily replaced ferrous metals in automotive casting for years, and aluminum sheet metal is certainly not new. However Ford’s decision to increase the use of aluminum sheet so dramatically on the best-selling vehicle in North America bodes well for aluminum suppliers. In fact, the Aluminum Association forecasts the demand for aluminum sheet for automobiles will increase from about 200,000 metric tons per year in 2011 to more than 1.5 million metric tons by 2020. That’s an increase of 750 percent!
So what does it mean for the tribologist? There are two main opportunities, as I see it.
First, although pure aluminum is highly formable (you don’t have to look far to find a beverage can whose bottom and sides are a single aluminum back-extrusion), the alloys needed for body panels are high-strength alloys that place severe limitations on the amount of deformation these sheets can tolerate without cracking. Therefore, die lubrication becomes even more critical. Although there are a number of known acceptable lubricants for relatively small-scale production, ramping up to automotive quantities provides a window for new lubricants to enable the kind of throughput typical in assembly plants.
Second, while steel bodies are extensively spot welded, welding of aluminum poses additional challenges. In particular, aluminum reacts with oxygen in the air, producing a thin, tenacious layer of aluminum oxide. This oxide has a much higher melting point than the alloy. Also, aluminum has a much higher thermal conductivity than iron, meaning more heat input must be very rapid, and thermal diffusion will result in a relatively large heat affected zone, a bane of all weldments.
Although it is still possible to weld these alloys, alternative means of fastening are gaining favor, particularly adhesive bonding. This is a classic tribology problem. After all, if we define a lubricant as a substance that reduces friction between two surfaces, then all we need to do is change “reduces” to “increases” and we have the definition of an adhesive!
One of the main challenges of adhesive bonding becomes apparent when you realize that the average age of a car on the road in the United States is 11 years and rising. Any adhesive bond, therefore, must be stable and reliable for decades. Perhaps some of what we know about producing stable lubricants for lowering friction can be applied to making stable, long-lasting adhesives. As we say in academia, actually accomplishing this goal is left as an exercise for the reader.
Ed Becker is an STLE Fellow and past president. He is president of Friction & Wear Solutions, LLC, in Brighton, Mich., and can be reached through his website at www.frictionandwearsolutions.com.