Varnish deposits from steam turbine oils
R. David Whitby | TLT Worldwide November 2013
Use of Group II oils is trending up, but formulating the correct additive package is essential.
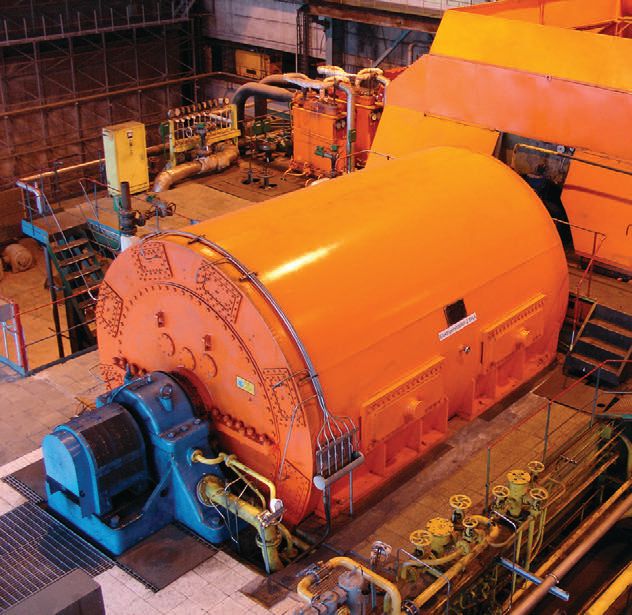
Varnish can be removed from steam turbine oils, but it’s best to prevent varnish formation on metal surfaces in the first place.
www.canstockphoto.com
DURING THE LAST 10 YEARS, changes in steam turbine operating conditions and oil formulations have caused a variety of problems for steam turbine operators. Research by turbine manufacturers, power companies and oil suppliers has shown the main causes of the problems to be an increased use of API Group II base oils in turbine oils, combined with an increase in steam turbine peaking operation. The highest profile problems were entrained air and foam, decreased demulsibility and formation of varnish.
API classifies mineral base oils into three categories: Group I, Group II and Group III. The basis of the classification is the saturated hydrocarbon content, sulphur content and viscosity index of each type of base oil. Saturated hydrocarbons include paraffinic and naphthenic types; aromatic hydrocarbons are unsaturated.
The refining processes used to make Group I base oils mean they contain significant amounts of aromatic hydrocarbons (sometimes up to 20 percent by weight) and higher contents of naphthenic hydrocarbons. Measuring by weight, a typical 150 SN Group I base oil will contain around 50 percent paraffinic hydrocarbons, around 35 percent naphthenic hydrocarbons and around 15 percent aromatic hydrocarbons.
Conversely, the refining processes used to manufacture Group II base oils chemically convert many of the aromatic and naphthenic hydrocarbons into paraffinic hydrocarbons. As a result, a typical 150 N Group II base oil has about 68 percent of its weight in paraffinic hydrocarbons, around 30 percent naphthenic hydrocarbons and only around 2 percent aromatic hydrocarbons. Some Group II base oils contain almost no aromatic hydrocarbons. Naphthenic and aromatic hydrocarbons exhibit higher solvency properties than paraffinic hydrocarbons but are poorer on oxidation stability properties.
As a consequence of better response to oxidation inhibitors, oils formulated with Group II base oils have been found to give better results in some oxidation tests compared to oils formulated with Group I base oils. This has resulted in the increasing use of Group II base oils in industrial lubricants that are subject to oxidation such as steam turbine oils.
When mineral oils are exposed to high temperatures in the presence of air (oxygen) and entrained water, they oxidize. Oxidation products include acids, esters, alcohols, ketones and polymeric compounds, all of which are attracted to each other and to metal surfaces. When present in sufficient amounts, they can precipitate out of solution, forming varnish and eventually sludge.
Unfortunately, because Group II base oils have poorer solvency properties compared with Group I base oils, when they do oxidize they tend to produce varnish and sludge more quickly. Also, when some aminic oxidation inhibitors degrade, they can form varnish on metal surfaces.
The greatest problem with varnish in a steam turbine lubrication and control system is that it plates out on servo-valve surfaces, leading to valve sticking, and plugs the last-chance filters (LCFs) that are part of the servo- valve assembly. LCFs made with sintered metal or fine screens provide a convenient surface for varnish formation because of their location in the low-flow, colder hydraulic control section. Lower temperature promotes varnish formation because of the lower solubility at lower temperatures, which causes it to come out of solution and deposit on the filter’s metal surface.
In addition, varnish precursors form deposits on mechanical seals, Babbitt sleeve bearings, thrust-bearing pads and orifices, resulting in restrictions. When these deposits develop on heat exchanger and reservoir walls, reduced heat transfer and higher temperatures are likely to occur.
Varnish can be removed from steam turbine oils using either electrostatic or adsorptive filters, but it’s preferable to prevent varnish formation on metal surfaces in the first place. If formulators of steam turbine oils decide to replace a Group I base oil with a Group II base oil (to get better oxidation stability and longer oil life), the use of the correct types of oxidation inhibitors and the addition of small amounts of a polar base oil, such as an ester or alkylated naphthalene, is advisable. The polar base oil will improve the solvency properties of the Group II base oils, helping to keep any varnish precursors dissolved in the turbine oil.
David Whitby is chief executive of Pathmaster Marketing Ltd. in Surrey, England. You can reach him at pathmaster.marketing@yahoo.co.uk.