Fundamentals of filters and filtration
Josh Fernatt, Contributing Editor | TLT Webinars November 2013
How they uniquely trap damaging intruders while allowing fluids to continue their journey.
KEY CONCEPTS
• Filters prevent particles, even the size of a single bacterium from dooming a machine.
• Modern filter technology does not operate on the principle of a sieve as many believe.
• The greatest quantum leap in filtration technology in the past 20 years was replacing cellulose with glass fiber-based filtration media.
ABOUT THE PRESENTER: JOHN DUCHOWSKI
John Duchowski obtained his doctorate at Carnegie Mellon University in Pittsburgh in 1990. From 1992 to 2004, he held the positions of principal scientist in the Scientific and Laboratory Services Department and vice president of technology in the Machinery & Equipment Division at Pall Corp. In 2005, he moved to HYDAC Technology Corp. where he is director of technology development. His projects focus on the effects of physical and chemical contaminants on the performance of hydraulic and lubricating systems and on the fluids employed in those systems. Dr. Duchowski is an STLE Fellow and holds the society’s CLS and OMA I and II certifications. You can reach John at john.duchowski@hydacusa.com.
This article is the eighth in a series based on Webinars originally presented by STLE University. “Fundamentals of Filters & Filtration” was held Feb. 13 and is available at www.stle.org: $39 to STLE members, $59 for all others.
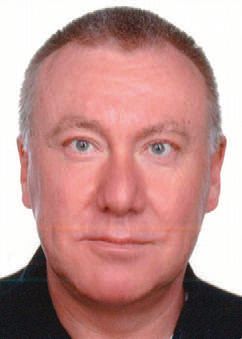
John Duchowski
WHEN IT COMES TO EXTENDING the life of lubricating and hydraulic fluids, it’s the little things that make filters and filtration such a big deal. Even particles the size of a single bacterium can spell a machine’s doom if left to run amok. Enter filters and their unique ability to trap damaging intruders while allowing fluids to continue on their way to work.
The sizes of particles that present difficulties for machines range from the smallest point visible to the human eye (40 micrometers) to a speck of dirt (20 micrometers), continuing down to the focus of most filters—particles in the 6- to 10-micrometer range.
When trying to visualize the design of a particle trap, many envision a woven surface, much like a basket, containing pores smaller than the particles it is meant to catch. This idea is more in line with a common sieve or strainer. Modern filter design employs a three-dimensional matrix with a tortuous path that closely resembles a rubber-band ball split in half—there’s a multilayer structure of fibers where pore openings get tighter and channels become smaller until all particles that fall within the design characteristics become trapped.
“The misconception is that these pores are some sort of a fixed and well-defined size. In fact that is not the case,” says Dr. John Duchowski, director of technology development for HYDAC Technology Corp. and an STLE Fellow. Duchowski presented a Webinar for STLE University on the topic earlier this year. “What we have is a series of flow channels through which the particles must squeeze through,” he adds.
MECHANISMS OF FILTRATION
In modern filter design, there are several mechanisms through which the particles can be caught. Direct interception is a mechanical process that occurs when a particle that is larger than the pore or channel opening cannot pass through the filter media and is trapped. When particle materials are much smaller than the pores, they can still be trapped in filter material as a consequence of their forward inertia, as the fluid they are traveling in is forced to turn through channels while they continue in a straight line. This action is referred to as inertial impaction.
Diffusional interception, which is only operational in gases, occurs when particles are small enough to ricochet off one another and bounce into the fibers of the filter media. “This is akin to the Brownian motion and is only effective for particles that are very, very small,” says Duchowski.
Another mechanism that can be used in filtration relies on electrostatic forces or adsorption. In these instances, the opposite charges attract and particles are pulled into the filter. This type of filtering is only effective in fluids such as water, which is subject to electromotive forces. Because hydraulic and lubricating fluids are highly dielectric, these charges are not present or are not strong enough, so adsorption or surface interaction filtering is not feasible. For the purposes of filtering contaminants from lube and hydraulic fluids, direct interception is the primary operational mechanism.
When a particle enters the mechanical process of direct interception, it can be removed by one of two areas within the filter: on the surface or within the depths of the media. In surface interactions, particles larger than the filter pores cannot pass through the layer, which may be a screen or membrane. However, gels and fibers can still squeeze through at this stage.
“We have to think about the fact that we’re not dealing with particles of a fixed size,” Duchowski says. “They are not all little spheres that will essentially let themselves be easily filtered out as a result of not being able to fit the pore.” To prevent particles from penetrating, filter depth media is designed to throw as many turns and pathways as possible in the way of the particle, capturing unwanted debris while allowing the fluid to continue on.
Damaging particulate materials in working fluid can be traced to four main sources.
1. Built-in particulates originate from the initial manufacturing and assembly processes.
2. Maintenance-introduced particulates find their way into machines when the equipment is opened, worked on, etc.
3. Environmentally derived particles may be blown in through openings and seals or ingress through oil top offs.
4. Wear-generated materials appear as a result of normal equipment wear and tear from frictional processes.
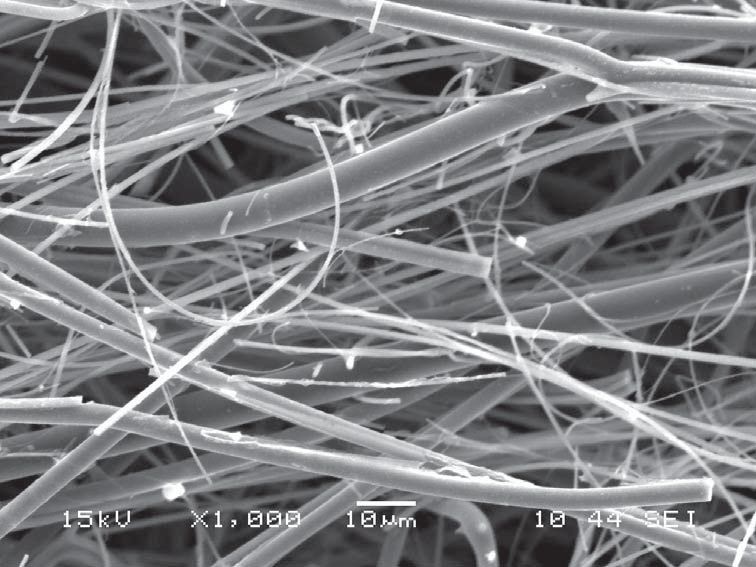
Figure 1. Glass Fiber Filter Media Magnified 1,000X (photo courtesy of HYDAC).
Surprisingly, newly delivered fresh oil is typically dirtier than repeatedly filtered oil cycling through the system.
“One could make an argument that whatever particulate matter is present in the fluid contributes to accelerated oil aging,” notes Duchowski. “Friction increases heat and hence thermal stress on the fluid. Also, some particulate matter, especially that generated within the system, will have very active metallic surfaces that can act as a catalyst in both oxidation and hydrolysis.
“So, in principle, if fluid is kept absolutely clean, its service life should be prolonged,” Duchowski adds. “However, in practice it is very difficult to say what contaminant level will result in a measurable fluid life extension.”
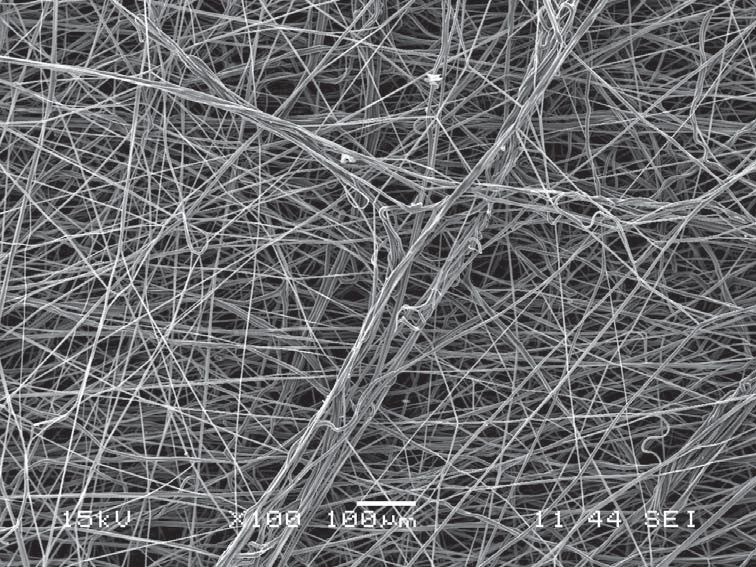
Figure 2. Melt Blown Filter Media Magnified 100X (photo courtesy of HYDAC).
FILTER CARTRIDGE CONSTRUCTION
Filters are designed to capture particles of a given size, depending on their application. Thus, the primary function of the often densely pleated filter media is to capture the dirt particles within its depth. While capturing particles is the ultimate goal, filters also must be capable of allowing the all important lube or hydraulic fluid to continue its flow without losing pressure, which can occur as more and more channels clog with particulates.
The typical filter cartridge begins with a sealing device, with O-rings being considered the best link between filter and machine. A support tube might also be present, along with pleated support layers, the filter media itself, followed by an end cap. The entire device is then wrapped in plastic or spiral wound tape.
“The technological breakthrough that has brought about the greatest quantum leap in filtration technology in the past 20 years has been the replacement of cellulose with glass fiber- based filtration media,” Duchowski says. “The extremely well-defined and generally inert glass fibers allowed for a dramatic increase in filtration efficiencies, as well as significant reduction in pressure drops and concomitant increase in dirt holding capacity.”
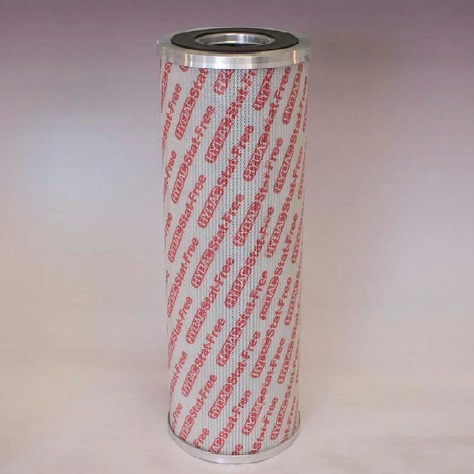
Figure 3. Stat-free Filter Cartridge. (photo courtesy of HYDAC).
FILTER PERFORMANCE & CONDITION MONITORING
Evaluating the performance of a filter through an industry approved system of norms can give operators a good idea of its effectiveness as a safeguard. There are many ways to keep tabs on a machine’s health and well being. Online devices such as particle counters, IR spectrometers and viscometers help detect the signs of declining fluid life that results from degradation, aging and contamination by physical and chemical compounds. These devices share the same basic mission as the filter: to ensure machines can operate at peak efficiency for as long as possible.
With particle counters, placement within the system is the key to recording accurate results. Placing the particle counter directly into the pressure or return lines allows real-time monitoring of fluid as it cycles through the machine.
“Another interesting parameter to monitor is the water content,” Duchowski says. “For this purpose, we use capacitors with a dielectric polymer inside, sandwiched between two gold or platinum electrodes. If the water migrates into this polymer dielectric, the capacitance changes, and it turns out the capacitance is linear with the relative humidity. The sensor reports relative humidity and not parts per million. From the operational perspective, I think it is a valuable parameter to know because it tells us about when we can expect the phase separation to occur.”
Another important parameter to consider, and one directly tied to filter life is differential pressure (DP). Differential pressure indicators can be used to tell when a filter is plugged, but paying attention to the DP curve can also indicate how fast and in which way the filter is becoming plugged, i.e., in the depth or on the surface.
FILTERS’ FUTURE
With the advancement of glass fiber as filter media, Duchowski explains that there are few calls for additional filter efficiency where hydraulic and lubricating liquids are concerned, as these systems do not require it. Most equipment operators he has communicated with seem satisfied with the current level of filter service life, so room for improvement now lies in bringing down costs.
“At some point, it becomes impracticable to employ filter elements of extremely high efficiencies because their pressure drop will be too high, even for fresh filter elements, and their service life will be too short because they will tend to block even the finest particulates that can be considered harmless or less harmful to system components,” Duchowski says. “Consequently, it has become an acceptable industry practice to recommend certain contaminant levels, typically specified by the ISO 4406:1999 standard, as being suitable for a given operating system.”
Duchowski describes other possible filter improvements on the horizon, including increased functionality. “Have the filter element perform some additional functions such as reducing or eliminating electrostatic charging, slowing down the rate of additive and/or fluid degradation, replenishing the fluid additive package or providing indication of fluid condition—depletion of additives, increase in acid number, etc.
“At the moment, no filter media on the market exist that can offer performance characteristics equivalent to that of glass fiber-based media,” Duchowski says. “Subsequent to that, I think the ability to fiberize various polymeric materials such as polypropylene, polyester, polyamide, polycarbonate, etc., has certainly allowed us to broaden the scope of available materials which, in many instances, also has resulted in significant cost reduction.”
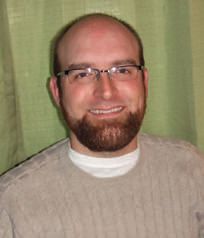
Josh Fernatt is a free-lance writer who can be reached at josh.fernatt@gmail.com.