Please share one BEST PRACTICE you use regularly in your work and state your job title.
TLT Sounding Board November 2013
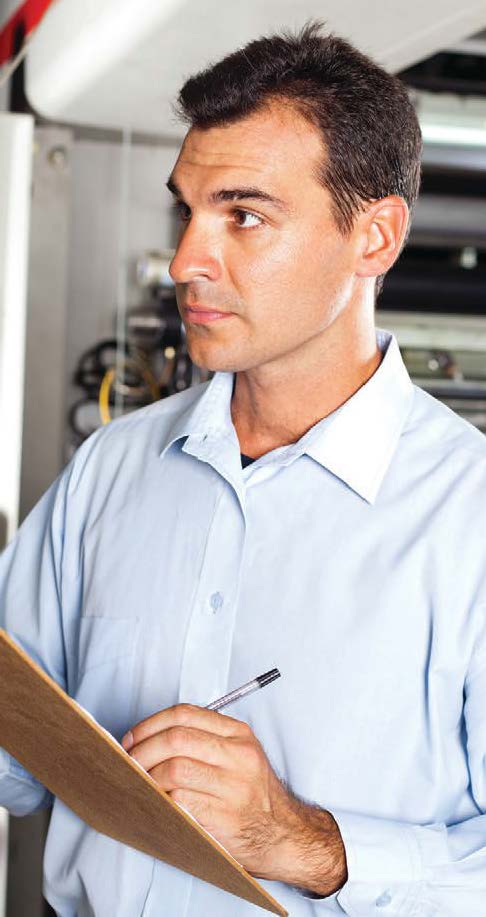
www.canstockphoto.com
Although researchers and academics provided some input, most of the answers to this month’s survey question came from our industry’s sales and technical sides. Technical specialists emphasized the importance of lubricant cleanliness and keeping procedures as simple and direct as possible. Many emphasized the importance of following ASTM methods, conducting consistent oil analysis and staying current on new products and emerging technologies. Sales personnel talked about the importance of setting goals, listening to customers, resolving their issues and following up promptly. And, of course, there were some best practices that apply to everyone. “Take a nap when you need it,” offered a research manager, “sleep is important for your health!”
Conduct routine, schedule oil analysis on hydraulic and thermal oils.
Corporate maintenance manager.
Always use clean, appropriate, properly labeled containers for top-offs.
Establish a central location for all lubrication storage in a climate-controlled area and managed by one person or group with color-coded oil containers for each type of oil.
Oil analyst/lubrication technician with OMA I certification.
Have a game plan for every day.
Sales associate.
Learn from both losses and near losses and decide on what practices and procedures need to be continued, halted or performed differently.
Sales engineer.
Be aware of the tribological system before making any decision.
Technical manager at a special lubricant manufacturer.
Ensure that the correct performance level of lubricant is used in the application. A good example of a bad practice would be using an API GL-4 when the application requires an API GL-5.
Technical manager.
After every meeting with a customer, I make a point of writing him a summary of meeting key points and the finer issues to focus his attention. It also helps me to recall thereafter what was said to the customer during our meeting. Since I categorize my customers into market categories, it is very useful for future reference when I meet another in the same activity category again.
Good follow-up actions with customers!
Marketer.
Help people expand their minds by being open to a new and innovative changing world.
Always follow up on any customer concerns, even if they might seem trivial. What seems like a small issue can be a big problem later. Generally, laziness takes over with salespeople as we are much too busy and can’t seem to get “a round tuit.” Too many people seem to live by the adage, “we don’t have time to do it right, but we have time to do it twice.”
Senior fuel and lube representative.
Make sure you know what your customer’s needs are.
Sales executive.
Take a proactive approach by consistently sampling oil and using oil analysis on a regular basis. Keep data and trending information for necessary corrective actions. Either overhaul the machinery or clean the entire lubricating system, including the reservoir if there is one.
Conduct daily checks on oil condition in oiler bottles and BOA of equipment by draining a little to check if oil level is too high within and with contaminants.
Monitor the viscosity of hydraulic fluids used in pumps and motors on a regular basis to maintain optimum efficiency.
I try to remember that I’m here in this life to serve others and to do this with as much understanding and wisdom as I have. My job is to respond to needs in the area of lubrication.
Vice president of technical development.
Use common sense.
Product engineer.
When I’m working on pilot or production batches, I keep a 5-gallon pail packed with paper towels, gloves, pens, sample jars, etc., so I have everything I need at hand.
Scientist.
Have dedicated containers for the dispensing of lubricants into equipment.
Marketing manager.
Make sure you are focused on the relevant specifications for performance and value in the application. Performance attributes should guide the specification so it always works at lowest cost, not the other way around. Question the validity of old specs when looking at new designs and processes.
President/technical director.
(1.) Use desiccant filters in bulk storage/ dispensing equipment. (2.) Proper storage of drums.
Technical sales representative, account manager and CLS holder.
Check and verify that people are following standard operating procedures and that those procedures are current. Compare theoretical model with experiments.
Professor of engineering.
When looking at machine parts for an analysis of damage, don’t clean the oil without saving it for analysis.
Vice president of technical services.
I spend several hours in each customer’s plant every month observing their procedures.
Industrial sales representative.
We use closed, clean containers and are starting a color-coding system for the different oils in the plant site. These are kept in a clean room or in cabinets for that purpose. Clean is the name of the game.
Lubrication specialist.
Use a covered label container for transporting fluid to a properly labeled fill point.
Properly dispose of wastes produced from the laboratory.
Research group leader.
Document what you use in the course of doing your work.
Engineering consultant.
Read TLT cover to cover.
We survey equipment before we recommend lubricants. We review equipment manuals, and we look at plates on the machine.
Vice president-operations.
Nothing replaces good training.
Territory manager.
I always update my knowledge on new developments and improvements of lubricants, mainly metalworking fluids.
R&D manager.
We visually control machine overheating with “Thermax” self-adhesive strips.
Consultant.
Properly mix a sample before using.
Reliability and project engineer.
I always send all technical reference literature and manuals to the end-user of our lubrication products and systems with my offer of full support at any time.
Technical sales representative.
Meticulously plan and execute.
Vice president-global technology.
We use salesforce.com as a sales pipeline management tool.
Executive vice president.
Consult the machinery manufacturer’s lubricant recommendations and develop a equipment maintenance program for lubrication prior to the machine’s startup.
Follow OEM maintenance practices.
Industrial fluid consultant.
Consistency in pulling oil samples.
Director of operations.
Audit the sampling techniques.
Reliability engineer.
Before offering a lubrication recommendation, I always want to know what the OEM recommends.
Sales manager.
Periodic refreshers on specific procedures.
Technical consultant.
Always do the best you can. Often you must do the best practical thing instead of the best technical thing, but you will know what you have compromised.
Senior engineer.
The University of Hard Knocks has taught me valuable lessons. Procedures are a must!
Reliability manager.
When it comes to evaluating a lubricant, the more extraordinary the claim, the more extraordinary the proof needed to back up the claim.
Research engineer.
You have to make the calls.
Sales manager.
Best practice: truly listen.
Technology manager.
Sample new oil.
Consider every breakdown as an opportunity for continuous improvement. Sometimes it requires the work to be planned for a future date, but always look for the cause and ways to improve.
Contract maintenance and mechanical engineering technician.
Always run an EHL calculation when performing a root cause analysis on a machine failure.
Lubrication engineer.
We map all lubricant technologies available in the market, compare with OEM requirements, identify more feasible innovations and technology developments and, finally, evaluate the market demand for each product to cover gaps in our lubricant product line.
Product line manager.
Apply a wear preventative surface technology to lubricated machine components to preserve their condition over time.
Visual sample analysis.
Quality manager.
How often do you see end-users using good lubrication best practices?
Almost all the time
6%
Most of the time
11%
Fairly regularly
26%
Some of the time
45%
Almost never
12%
Based on responses sent to 13,000 TLT readers.
Verify OEM specifications and recommendations. As a
lubrication specialist, I am often required to make recommendations. Understanding the intent and expectations of the equipment designers offers insight to an application’s requirements. My final recommendation should be appropriate for all possible situations.
Perform oil analysis for all incoming new oils in 55 gallon and larger volumes.
Condition-based maintenance technology owner.
Find the real cause of failures through diagnostics.
Technical service manager.
It all starts with the product. Spend your money making and testing your product before you roll it out. The job of marketing is to get the word out about a great product, not make a mediocre product seem great.
Marketing and public relations.
Consider the client’s expectations and perspective.
Laboratory manager.
We developed best practices material on lubricant storage/handling, etc., to show our customer. We also collect best practices documents to help us investigate lubrication issues or equipment failure.
Lubricants technical services advisor.
Always remember: safety first.
Senior research scientist.
Utilize sources for reference in your daily work. These sources can be trade journal articles and industry handbooks. Also, maintain actual contact with professionals in the trade for complex issues.
CLS-certified Sales representative.
Document “standard work.” At the company I work for, design tasks are standardized for major components. This list of tasks is the starting point every time that component is designed (new) or revised. When failures occur or new design practices are invented, this standard work is challenged and reviewed for improved best practice.
Technical advisor.
We use best laboratory practices as outlined in ASTM methods.
Oil analysis business line manager.
Always refer to work from the best tribologists and use their knowledge for your work.
Vice president of manufacturing.
Tag machine fill points, drums and fill containers to keep cross contamination from happening.
Have a small kit to check the quality of lubricants on-site.
Lubricants engineer.
Always follow OEM recommendations for the correct lubricants. For fluid analysis, use ASTM test methods through an ISO 17025 A2LA accredited laboratory.
Sales manager.
Approach analysis from a systems standpoint.
Reliability engineer.
Filter incoming oil into storage containers and test those containers regularly.
Keep in touch with major suppliers on latest technology and formulation guidelines.
R&D chemist.
Have a Monday morning meeting to set goals for the week.
Continuing education.
I rely on our production people to keep an eye on raw materials. Their years of collective experience have helped identify problem raw materials. This is not very scientific, but it works really well.
Operations manager.
Almost micromanage. I know this is supposed to be bad, but employees give much more respect when they can see the person giving the instructions actually knows what he is talking about.
Service manager.
Focus on keeping lubes, clean, cool and dry.
Manager-field engineering.
Aim for precision and accuracy. Postulate and then try to prove your theory for better understanding.
Staff scientist.
If lubricants do not contain ester oils, you can do HATR IR spectra of used and fresh lubricants. With a comparison of the max transmission in a range from 2,000 to 1,800 with the transmission at 1,710, it is possible to see the degradation of lubricants.
Keep adequate spill containment products on hand.
Sales representative.
Ensure that all lubrication tasks are completed at the right time with the right lubricant and the right quantity while using the right processes.
Be calm and thorough instead of jumping to conclusions.
I obtain as much information as possible about the real situation as I can—environment, materials, loads, etc. Only then is it possible to develop a test that answers the problem—as opposed to answering the test chosen!
Principal engineer-tribologist.
Oil analysis is a critical component in achieving the world-class lubrication and reliability goals needed to reduce or eliminate the unscheduled downtime that costs end-users millions of dollars a year.
Accounts manager-industry/mining/quarry.
Lubricants rationalization.
Technical advisor.
All fluids must be passed through a filter before being dispensed to the equipment.
Field technical service engineer, continuity manager.
Mix MWFs properly and weekly, if not daily. Tramp oil removal is optimal. However, concentration control is the critical key to MWF success. Without proper concentration control, the previously mentioned best practices become moot. All these procedures must be done properly to create a synergistic approach for long-term MWF life and overall success.
Senior applications engineer.
Install and mark designated lube oil sample ports. Avoid vacuum pump sampling, if possible. This provides for accurate and repeatable sampling.
Drain your email inbox every 24-48 hours completely to zero.
Principal engineer-gear engineering software development.
Instead of ordering in drums, I normally order oils in pails. This prevents contamination and spillage.
Maintenance manager.
Housekeeping (proper storage of lubricants and filters, transfer of lubricants and a clean operating environment) is essential for maintaining machine reliability.
Reliability specialist/lubrication engineer.
We work to continuously improve but do not make changes unless we can verify that they are better. Verification could be as simple as talking to someone already doing it or using it.
Technology manager.
Make a plan, work your plan and lead by example.
Division manager.
Large-scale testing of formulation field trials prior to launch.
R&D scientist.
Be honest and forthright.
Sales representative.
Maintain daily production metrics and hold regular department meetings.
Lab manager.
Start each task with a required checklist. When meeting with plant personnel, always have a survey form with basic required questions available.
Industrial specialist.
Fleets need to monitor fuel economy by unit as a first indicator for predictive maintenance.
Take your time, do it right the first time.
Product manager.
Always take into consideration OEM recommendations, historical data and the operating environment before making recommendations or decisions based on results alone.
Maintenance planner.
Make lubrication recommendations based on equipment and operational specifications, not simply based on a cross-reference.
Regional sales manager.
Clean all lubrication points before applying lubricant. Use oil-safe containers when handling oil.
Maintenance planner.
Keep things simple.
Advanced research associate.
Conduct component oil evaluation immediately upon receipt of sample results.
Senior operations engineer.
All the best practices that I learned came from studying for and passing my ICML MLT, MLA and CLS exams.
Sales & marketing director.
Always use data to back up your hunches.
Marketing manager.
I always had a feeling that I could get more work done at the lab bench when I wasn’t spending so much time sitting in front of a computer. So I started working on the computer standing instead of sitting on a chair. Of course, I needed to rearrange some furniture, but after that I didn’t spend too much time on the computer.
Prioritize tasks and do the important thing first.
Technical sales representative.
Emphasize to the customer that the best value is not always the lowest price!
Senior technical support chemist.
Editor’s Note: Sounding Board is based on an e-mail survey of 13,000 TLT readers. Views expressed are those of the respondents and do not reflect the opinions of the Society of Tribologists and Lubrication Engineers. STLE does not vouch for the technical accuracy of opinions expressed in Sounding Board, nor does inclusion of a comment represent an endorsement of the technology by STLE.