Bringing used oil back to life
Josh Fernatt, Contributing Editor | TLT Webinars August 2013
The shift in re-refining continues to grow, helping to resurrect a valuable natural resource.
KEY CONCEPTS
• Typical contaminants found in used oils include lead, benzene, chromium, zinc, halogenated solvents and coolants.
• The EPA recognizes four accepted methods for recycling used oils.
• New technologies have changed perceptions that re-refined base oil is inferior to base oils produced from crude.
WEBINARS: A SERIES FROM TLT
This article is the fifth in a year-long series based on Webinars originally presented by STLE University. In some cases, the Webinar presenter will author the article, and in others, like this one, the Webinar is adapted by a TLT writer.
Scott Miller is vice president of U.S. refinery operations for Safety-Kleen Corp. in East Chicago, Ind., where he is responsible for managing the company’s engineering, operations, laboratory shipping/receiving and office functions. Previously, he worked for Hexicon Speciality and Dow Chemical. Rodney Walker is technical director of refining for Safety-Kleen in Richardson, Texas, and has more than 30 years of experience in plant operations, technical support, sales and general management. He has worked with several industry groups on new solutions/standards to help reduce emissions and improve fuel efficiency for fleets, including serving as chair of API’s Emerging Base Oil Technology Work Group. You can reach them both at scott.miller@safety-kleen.com and rodney.walker@safety-kleen.com.
STLE University has sponsored dozens of Webinars and podcasts on a wide range of technical topics. To see Scott Miller and Rodney Walker’s Webinar in its entirety, review all STLE University offerings and view the lineup of future events, log on to www.stle.org. Webinars are $39 to STLE members and $59 for non-members.
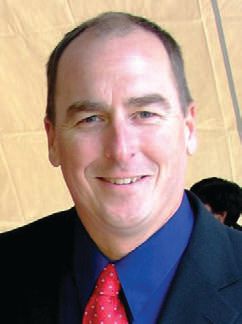
Scott Miller
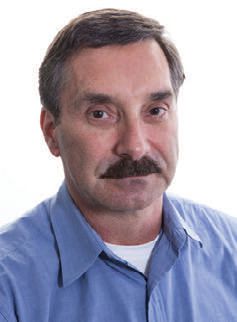
Rodney Walker
In the 1970s the United States got a wake-up call as the era of cheap and plentiful oil was nearing its end. A decade that spawned some of the heaviest, most fuel-hungry cars on the road soon revealed a harsh reality that America wasn’t in control of its own destiny where oil was concerned. Since then the price of a barrel of crude oil has been up and down, but the question of how to decrease U.S. dependence on foreign oil resonates as loudly today as it did 40 years ago.
Among the ideas that surfaced as possible solutions to the oil and energy crises of 1973 and 1979, one harkens back to the old adage “waste not, want not.” The re-refining of used oil into clean, useable base oil is a major step in turning the tanker around.
MAKING THE GRADE
According to the latest statistics from the U.S. Department of Transportation, roughly 250 million registered vehicles travel America’s highways. Considering that even the smallest cars on the road typically require four quarts of engine oil to operate, the amount of oil being drained and replaced on any given day is staggering. Before people began to see oil as a limited resource, most used oil (if it was collected at all) was disposed of by burning it for heat or blending it with other fuels. This form of recycling still accounts for where most used oil (approximately 70 percent) ends up. A significant amount of oil is also consumed in use.
“There’s about 1.3 billion gallons per year of recoverable used oil in North America,” says Scott Miller, vice president of U.S. refinery operations for Safety-Kleen Corp. in East Chicago, Ind., in a Webinar presentation titled “Re-Refining 101” sponsored by STLE University. “Of that about 900 million gallons are collected, and 350 million gallons are re-refined.”
Despite the seemingly big numbers, used-oil supplies are finite but perhaps not for the reasons you would expect. “There is a decline in the total amount of used oil in the marketplace for any purpose [burning or re-refining],” Miller says. “People are going a lot longer between oil changes. Many of the cars now are getting up to 15,000 miles between oil changes.” With rising fuel costs, people are cutting down on extraneous road trips, resulting in fewer miles being driven and fewer trips to the quick lube. That boils down to less available used oil for re-refiners.
Re-refiners in North America draw from the same pool of used-oil suppliers, which includes quick lubes and other companies that collect used oil such as auto-parts stores. However, these used oils are not accepted sight unseen. Forty characteristics are analyzed to ensure oil is suitable for re-refining and is not contaminated to the point where it poses a health risk to refinery workers. Oil is also vetted to determine whether it will produce a high-quality end product.
“You cannot take used oil that was not good lubricant to start out with and turn it into good lubricant,” Miller says. “We have a very rigid analytical set of procedures that we go through to quantify what’s in the oil and [to determine if] it is suitable for re-refining.” To further guarantee that the prequalified used-oil sample has what it takes to live again, the oil shipment is tested again once it arrives at the re-refinery before the process begins.
North American Used-Oil Market
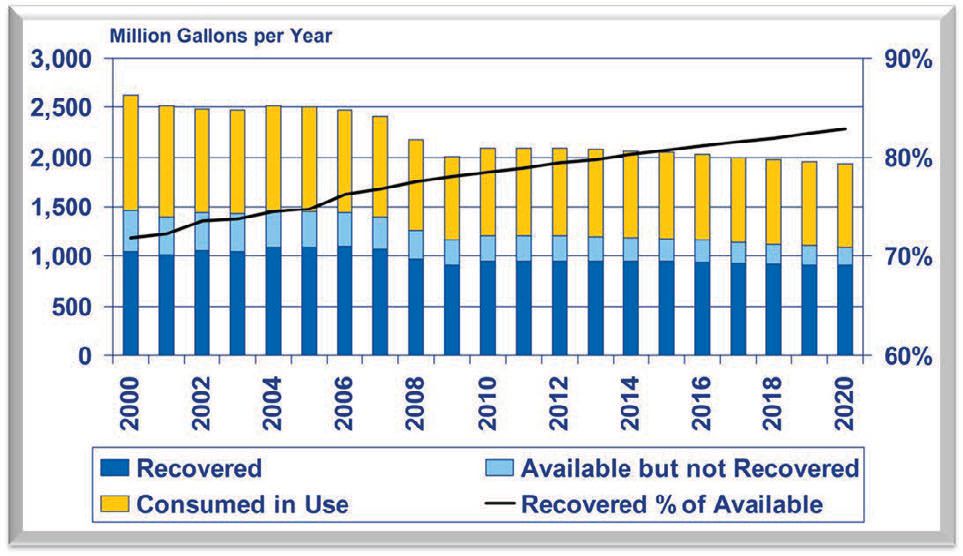
HYDROTREATING PROCESS
Safety-Kleen re-refines used oil through a hydrotreating process. The route of the used-oil stream begins inside a dehydration unit, where water is flashed into steam and ethylene and propylene glycols that incidentally found their way into the batch from the supplier are removed. The dehydrated oil is then sent to a fuel-stripper vacuum tower, where it is heated to a higher level to remove any lowboiling, residual fuels such as fuel oil and kerosene.
“Once the oil has been defueled, it comes into vacuum distillation, which is actually two steps,” Miller says. “There is a [vacuum] tower where we heat the oil up and turn it into two cuts, a medium and a heavy. The heavy cut represents the bulk of the contaminants that are in the oil.”
The heavy cut is separated out and enters an evaporation process where the feed stream is subjected to high vacuum and heat to vaporize the oil. This step produces a gooey, asphalt-like substance known as asphalt extender. “The bulk of the [asphalt extender] is additive packages in the oil,” Miller says. “There’s a lot of rubber…also the stuff that makes the oil black when it comes out of your car, including carbon, coke, contaminants and metals.”
With a high percentage of the contaminants now removed, the remaining amber-colored oil, referred to as vacuum oil, is fed to the hydrotreater. The process that occurs in the hydrotreater can vary from refinery to refinery, based on selected temperatures and pressures. Once the oil is hydrotreated, it is steam stripped to remove any kerosene-boiling range leftovers and excess hydrogen before being sent through a standard vacuum fractionator. In the hydrotreating process used by Safety-Kleen, three cuts, RHT70, RHT120 and RHT240, are produced. “It really comes out beautiful,” Miller says. “It’s remarkable what hydrotreating can do to used oil.”
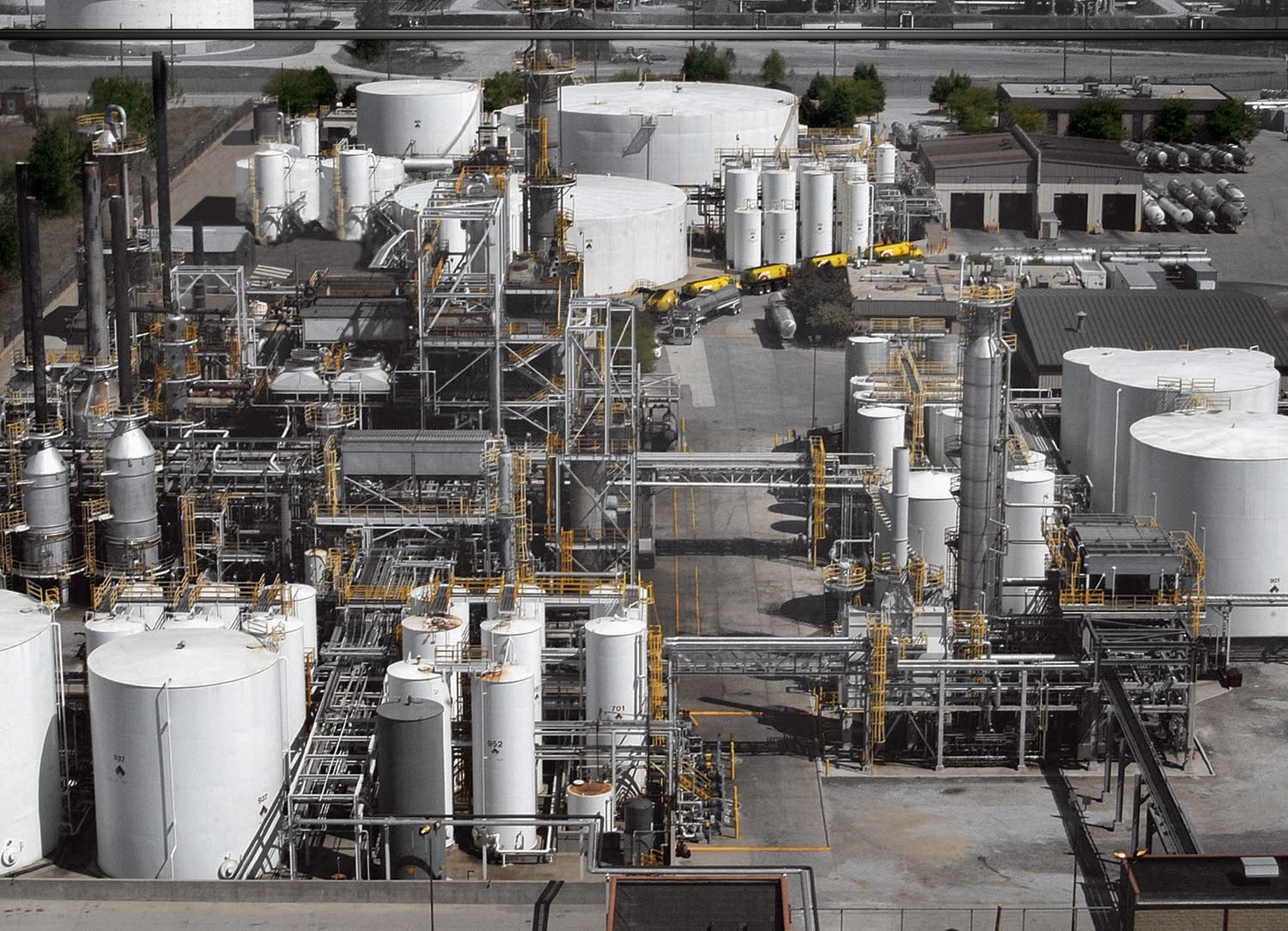
Safety-Kleen’s re-refinery plant in East Chicago, Ind., is the largest in the world.
TYPICAL RE-REFINING YIELDS:
• Water – 8 to 9.5%
• Fuels – 7%
• Glycols – 2%
• Asphalt Extender – 13%
• Lubes – 78%
GOOD HOUSEKEEPING
“The advent of the quick lube is probably one of the best things that has happened for the environment,” Miller says. “Back in the day, many people used to run [used oil] down the storm sewer, or pull the car under the tree in the backyard. We really didn’t have a place to take it. Quick lubes and used-oil regulations took care of a lot of that.”
In accordance with the Environmental Protection Agency’s mission to protect human and environmental health, there are four accepted methods for recycling used oils:
1. Re-refining
2. Direct burning
3. Processing used oil so it’s suitable for burning
4. Adding used oil as a supplement to other fuels.
Once common practices such as road oiling and pest-foliage control are now strictly limited. In most cases, they have been made illegal under state and federal environmental requirements.
As part of its You Dump It, You Drink It campaign, the EPA stresses the proper handling and recycling of used motor oil among do-it-your-selfers. The EPA states that improper disposal of just one vehicle’s worth of used oil has the potential to contaminate 1 million gallons of fresh water. Because used motor oil is insoluble, degrades slowly and contains loads of contaminants and heavy metals, preventing it from touching the ground is the best defense against oil contamination in waterways and potable water sources.
The EPA has a strict set of guidelines that must be followed by sellers of used oil for energy recovery or burning, including a requirement that the oil be tested for certain contaminants (e.g., lead and arsenic). However, depending on the size and laboratory capabilities of collectors, these levels of quality control may not always be followed to the letter. With three of the EPA’s four approved oil-disposal methods related to burning, collecting as much used oil as possible is vital to the success of re-refiners who are fighting to keep this highly valuable and reusable resource from going up in smoke.
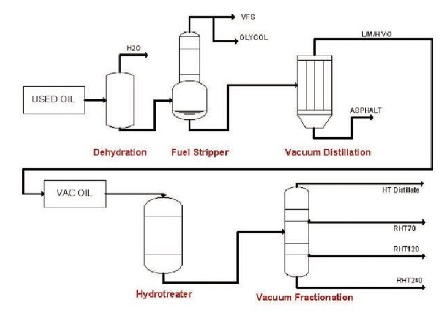
Typical re-refining process
HOW RE-REFINED OIL STACKS UP?
The ultimate goal of used-oil re-refiners is to carry out a process that gives new life to used, contaminated oil by refining it back into ready-to-use base oil. To be brought back into service as part of a new lubricant product, re-refined base oils have to measure up to virgin base oils derived from crude feed streams. A quick comparison of kinematic viscosity, the viscosity index and cold cranking simulator (CCS) viscosity at a given temperature will reveal that re-refined base oils compare favorably to virgin basestock.
“The re-refined viscosity index certainly measures up quite well in comparison to other Group II base oils,” says Rodney Walker, technical director of refining for Safety-Kleen in Richardson, Texas. “Another characteristic that is of importance is the volatility range of the base oil, specifically when you are developing driveline products and engine oils, particularly on the light-duty side or gas-fueled engines.”
A direct comparison between a blended Group II formulation using crude-derived base oil and one derived from re-refined base oil with the same additive treat rate shows the re-refined base oil requires less Group III oil to meet American Petroleum Institute guidelines. “The specific reasons for this formulation having greater amounts of Group III in one versus the other are the Noack volatility and the cold-temperature properties,” Walker says. “The re-refined has a much better Noack volatility than the Group II derived from crude feed stream, while still using the same Group III oil.” The result is a substantial cost savings for lube manufacturers who use re-refined base oil.
Base Oil Comparisons
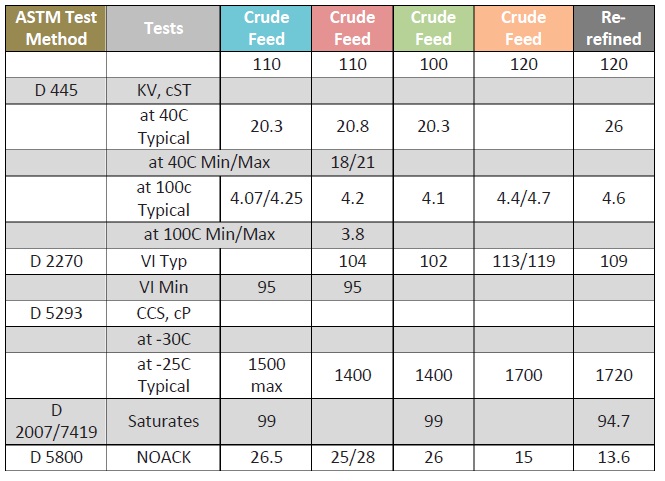
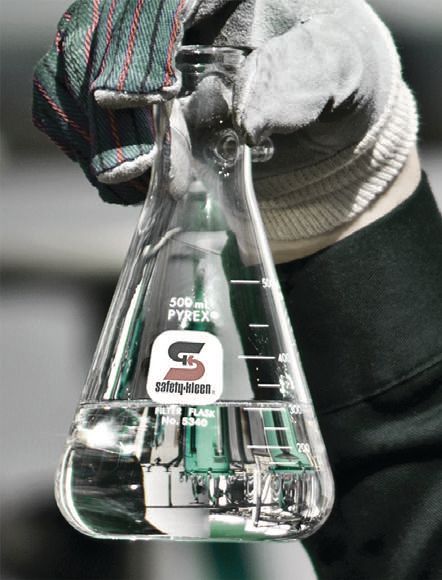
‘Re-refined base oils can be every bit as good as, if not better than, what the majors are producing from crude.’
THE FUTURE
The viewpoint that used oil is a valuable resource that can be recycled and reused again and again is gaining momentum, as evidenced by the increased amount of used oil being re-refined. Though supplies of used oil have fallen over the past decade, with the planned construction of new re-refineries throughout the nation, the ability to run the available stock through the re-refining process continues to grow.
With new technologies and years of experience, the re-refining industry is also putting to bed past beliefs that re-refined base oil is inferior to base oils produced from crude. “We’re aware of re-refined oil that has undergone a heavy-duty diesel engine fleet study of greater than a million miles,” Walker says. “From a product quality standpoint, [re-refined oil] meets and exceeds many crude-derived base oils in finished formulations.”
“Re-refined base oils can be every bit as good as, if not better than, what the majors are producing from crude,” Miller says. “We’re excited about what is happening with new re-refineries, and it’s really an exciting business to be in right now.”
Unlike the process of burning, where the used oil has only two lives—its initial life as a lubricant and its final life as a fuel—re-refining is a true means of resurrecting a valuable natural resource.
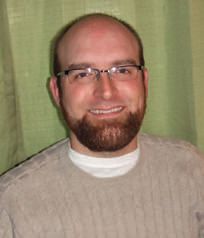
Josh Fernatt is a freelance writer who can be reached at josh.fernatt@gmail.com.