Please describe a problem you encountered resulting from grease incompatibility.
TLT Sounding Board May 2013
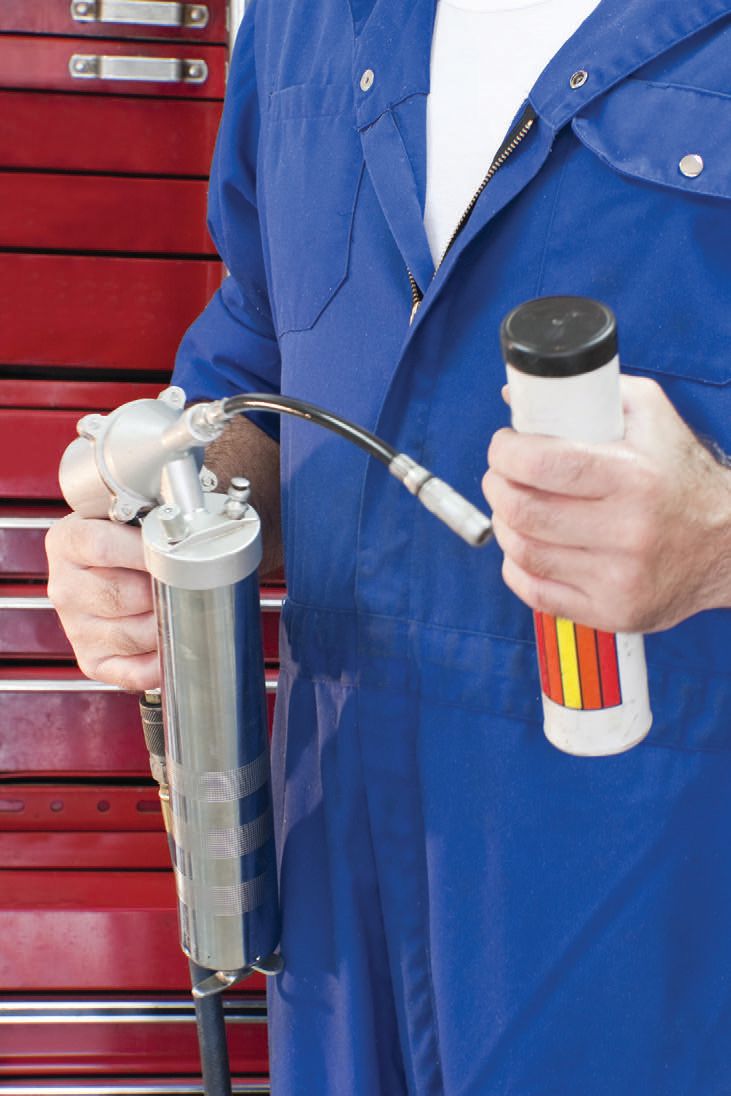
www.canstockphoto.com
When it comes to grease-related problems, TLT readers have seen it all: hardening, softening, thinning, fouling and product running all over the place. Incompatibility is usually the problem, with readers most often citing a mix of polyurea and lithium complexes. However, when selecting a grease, proper attention also must be given to base oil and, as always, viscosity. Readers offered many resolutions to their grease problems, including personnel training, compatibility research and testing, better labeling, purging the old grease before applying the new, more frequent lube changes and restricting grease activities to a handful of individuals. (For more grease technical information, see Dr. Bob Gresham’s Lubrication Fundamentals article.)
Much grease is sold with a carnival approach. Many times selling technique is based on issues irrelevant to the issue at hand. Very little, if any, attention is given to base oil type and viscosity or thickeners. High commission rates from specialty companies which train their salesmen in these methods drive this approach: “Our grease is the best there is and can solve all your problems. Trust me, it is a steal at $10 per tube.”
The problem is usually needing to add grease or service a component where the current lubricant in place is unknown, causing a mixture of soaps.
Motor bearing failure from mixture of greases (lithium complex and silica). Resolved through training personnel, tagging equipment with lube information and restricting greasing activities to only a few individuals.
Too hot. Changed to a synthetic product.
Polyurea versus others and aluminum complex.
Replacing obsolete grease in a nuclear power station. Greases that were fully compatible on paper, down to the thickener chemistry, failed in the lab. I performed lab testing for critical, significant and safety-related applications and shared that information for personnel in other power plants.
None in service, only in lab testing. Do not mix incompatible greases in the first place.
No mixing of greases in our plant, so no compatibility problems to report.
Polyurea and lithium complex incompatibility resulted in grease thinning and leaking out of the bearing.
Heavy loaders using a lithium complex. Switched to a bentonite grease without full purging and experienced “squeaking” kingpins.
In a steel rolling mill, a basic lithium complex grease was changed out for another grease recommended by another mill supervisor who had used it for years and had better bearing reliability. The same supplier provided both greases and did not raise any question about compatibility, including compatibility with the soluble oil in the coolant, which did get into the bearings. The new grease was added without removing the original. I believe it contained or was referred to as a “boron” grease. The result was grease that turned black and watery and stank terribly. Bearing failures shot up. The problem was resolved by returning to the original grease and increasing greasing frequency to minimize the effects of coolant washout. The lesson to be learned here is to clean out bearings before changing greases, thereby making compatibility with another grease a non-issue. Also, consider external contaminants, including water, in any compatibility test or choice of grease in the first place.
Customer made a decision to go from a lithium complex to bentone based on a supplier recommendation. Major issues with oil bleed and bearing failures. Purged out the bentone and went to calcium sulfonate and have been happy ever since!
I always recommend completely flushing out the old grease with the new grease to avoid compatibility problems.
Adding polyurea grease to lithium grease. Adding polyurea grease to lithium grease does not create an immediate problem, but in the long run it will affect the performance of the grease. The bearing was replaced at the first opportunity.
A customer was using a clay-based grease, and an incompatible grease was applied on top. The grease hardened in the lines, forcing the whole bearing and lines to be removed and flushed.
Calcium complex and lithium complex grease mixed in roller bearings created a mess and caused multiple bearing failures.
Some thickeners do not work well in high temperatures; others have the same problem in high speeds. I have found that polyurea thickeners are the best choice in high speeds, especially electric motors where PTFE-thickened products work best in high temperatures. It also depends on what you consider high temperature. In both these instances, the customer was using a general purpose grease. During the plant survey, we respected the correct products for longer bearing life.
Do you consider compatibility when using or recommending grease for a particular application?
Almost never
2%
It depends on the application
13%
I consider general information on grease thickener compatibility
75%
I complete or request compatibility testing
29%
Based on results from some 13,000 TLT readers. Total exceeds 100% as some readers chose more than one answer.
Not a personal experience, but an observation: Most wheel bearing greases used/ sold in the U.S. these days are based on lithium complex thickeners. When browsing the shelves at a local auto parts store, I observed products from multiple suppliers that were lithium complex-based. I also found a product being sold as wheel bearing grease that was based on an aluminum complex thickener. I was much concerned, knowing that lithium complex and aluminum complex thickeners are, at best, marginally compatible. If someone is unaware of the possible incompatibility of the thickeners and simply adds the aluminum complex grease on top of lithium complex grease already in their wheel bearings, they may do much more harm than good by relubricating instead of leaving the wheel bearings alone. The possible incompatibility could result in a bearing failure much more quickly than it would just running on the existing grease in the bearings.
Substituted one food grade grease for another on a Rosskamp Pellet Mill. Grease softened and ran out.
I have experienced both thinning and thickening of grease with incompatibilities. Most often it is thinning. Proper purging of the prior product typically corrects the issue. Thickener incompatibility can cause two reactions: (1.) Set up hard like concrete, (2.) turn liquid and run out of the bearing. I have seen both.
Severe softening of grease mixture in a centralized system. Greases mixed were calcium sulfonate and aluminum complex thickeners of NLGI 2 consistency. Issue was resolved by purging system and recharging with one grease only.
My co-worker encountered an incompatibility problem. Thickener: Organoclay. Additive: Lead naphthenate for EP properties. The additive degelled the grease. Countermeasure was to seek another EP additive.
Filling machine grease was not compatible with the product in the equipment.
Switched to a product that was compatible with water-based fluids. Went to a synthetic grease from a conventional lithium grease.
None, to my knowledge. But I don’t understand grease compatibility and this scares me!
Replaced the reducer in two cases! One with a lithium grease mixed with the OEM’s polyurea and the second with a polyurea mixed with the OEM’s lithium.
An electrical switch grease was chemically aggressive toward copper, causing metal corrosion and ultimately electrical failure. The offending grease additive was changed and the issue resolved.
Electric motors with OEM polyurea grease being relubricated with aluminum complex 210 cSt at 40 C base oil grease. Caused softening, running and poor lubrication. Corrected by supplying polyurea-based grease with a clear tube (acrylic) grease gun, calibrated gun delivery. Wrote a detailed relubrication procedure.
Hardening grease.
Some cases required extensive purging procedures. Others required a machine shutdown to remove bearings for complete removal of grease. Grease thickeners most often mixed polyurea and lithium or lithium complex.
The grease was dissolving into the coolant. It was lithium-based and depositing itself all over the machine walls. It was replaced with dirty-looking moly grease, but that grease didn’t dissolve.
I’ve never experienced an incompatibility problem because this is always assessed before a product change.
Base oil depleting out of the grease. Purged the system. I believe it was calcium and aluminum thickeners.
Problem encountered when lithium-based grease was mixed inadvertently with aluminum complex grease. Issue was resolved by purging grease mixture and refilling with the correct grease.
I have not had any problems myself but have seen issues where there is incompatibility that was almost always due to thickener compatibility issues. This is an area where most end-users aren’t aware of the possible problems.
Mixed soap NLGI Grade 2 turning into soup and running out of the application. We resolved it by completely purging the systems of the previous grease by regreasing every shift. Not sure of previous soap type, but the replacement is lithium complex.
Blending incompatible greases often creates much higher oil bleed than either grease by itself.
Fortunately, I’ve never experienced that problem. I’m rather obsessive compulsive about compatibility.
Editor’s Note: Sounding Board is based on an e-mail survey of 13,000 TLT readers. Views expressed are those of the respondents and do not reflect the opinions of the Society of Tribologists and Lubrication Engineers. STLE does not vouch for the technical accuracy of opinions expressed in Sounding Board, nor does inclusion of a comment represent an endorsement of the technology by STLE.