Complexity in oil analysis: Part IX
Jack Poley | TLT On Condition Monitoring March 2013
Despite some limitations, sensors are playing an expanding role.
ONE OF THE THINGS that oil analysis (OA) could not do early on, actually until quite recently, was provide instant gratification in terms of real-time data. That domain was unique to vibration analysis, wherein accelerometers were affixed to machinery housings in various strategic locations to measure deflection readings from problems such as misalignment, imbalance or excessive clearances.
The turn of the 21st Century saw this disparity between vibration and OA resolved with the advent of quality sensors that could withstand immersion and exposure to hot lubricants and their contaminants while providing useful data from which to draw such conclusions as:
1. Lube condition contamination or deterioration via dielectric strength
• Fuel dilution
• Fuel soot
• Acid build-up
• Water
• Glycol
• Oxidation/Additive Depletion
2. Moisture, via relative humidity measurement
3. Viscosity
4. Wear metals
• Ferrous debris, with detection capability down to 40
• Nonferrous metal debris with sensitivity down to 135.
More such devices will make their way to the lube circuits of various machines as technology continues to progress, fueled by a demand to be apprised of a component’s condition in the moment. The advent of lube circuit sensors, of course, gave way to the notion of three-tiered oil analysis: online, onsite, offsite (see Figures 1-3).
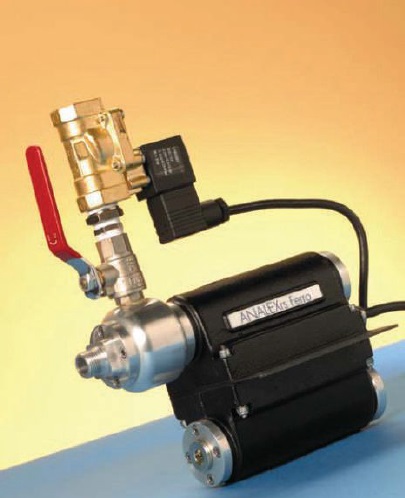
Figure 1. Online sensor for ferrous debris monitoring. (Courtesy of Parker Kittiwake)
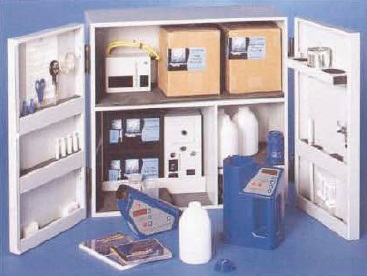
Figure 2. Onsite portable testing kit. (Courtesy of Parker Kittiwake)
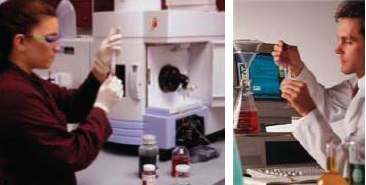
Figure 3. Offsite, full-service lab with complete testing capabilities.
While the age of lube circuit sensors promises increased insight and timeliness as to machine condition, a new complexity, that of past information from static samples versus continuous data from sensors, likely will be sorting itself out for a number of years. Samples represent snapshots in time, i.e., the apparent state of the machine and its lube on a given date.
Sensor data can be provided on a second-by-second basis, if necessary, resulting in 3,600 data points an hour. Even collecting such data on an hourly interrogation interval, which would be longer than typical, still results in 24 data points in a single day. It is easy to realize that there is a need to reduce these data in some logical, useful fashion so as to make it manageable when tracking a machine.
If we go back to our comparison with vibration, there is use in recording data points continuously and storing them for interrogation at a moment of interest while at the same time setting alarm trends or limits. The readings taken from vibration sensors constitute the only source of vibration data—not so with OA.
OA sensors, while a quantum leap in the inspection of lubes, have not been perfected to the point where they are omniscient, or nearly so, such that routine offsite or at least offline sampling can safely be halted or even significantly curtailed. Here are some reasons:
• Abnormal dielectric readings do usually signify an issue with the lube, but the reading itself is not specific enough to identify the cause. Additional testing offline (Tier 2) or offsite (Tier 3) always will be necessary to isolate the problem, or problems.
• Sensors are not available for every data type one might prefer to apply to OA. Or one may simply have decided not to include a specific type of sensor for economic or installation reasons.
• While ferrous debris and nonferrous wear debris can be detected via sensors, the particle size limit is relatively high compared to conventional UV spectrometers that can detect the smallest particle sizes—those below 5 μ which most rubbing wear modes reveal. What wear metal debris sensors do accomplish, however, is to increase the particle size range that can be addressed in lubricants, expanding the scope. The larger particles, of course, are more indicative of problems with a small time window to address. This is perhaps the metallic debris sensor’s most important function, that of potentially identifying short-term failure modes that may have escaped conventional OA.
Still, it would seem that the best strategy, given available technology, would be to employ both sensor and offline/offsite testing in concert, gleaning the best of both capabilities. Once the economics of three-tiered composite strategy bear scrutiny in a given operating environment, or for specific machinery types, it is clear that a more encompassing, increasingly probative monitoring scheme becomes available. Critical machinery will lead the way in acceptance of this clearly advanced approach that avails the best indicators available.
In April we’ll explore some notions of how live streaming data can be resolved and usefully coupled with static data from extracted oil samples.
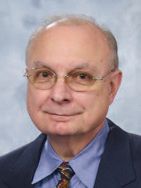
Jack Poley is managing partner of Condition Monitoring International (CMI), Miami, consultants in fluid analysis. You can reach him at jpoley@conditionmonitoringintl.com. For more information about CMI, visit www.conditionmonitoringintl.com.