Trends in Industrial Gear Oils
Jean Van Rensselar, Contributing Editor | TLT Cover Story February 2013
Today’s machines are smaller, hotter and overloaded—making proper lubricant selection even more critical.
KEY CONCEPTS
• Smaller gearboxes mean reduced oil reservoirs, higher loads and more stringent demands on lubricants.
• Because gearboxes are burdened with increasingly hotter operating environments, improved thermal stability in gear oils is an imperative.
• The trend toward lowering gearbox manufacturing costs, while at the same time allowing for increased in-use productivity, places ever more stringent demands on gear oils.
AN ALARMING 30% OF U.S. INDUSTRIAL COMPANIES recently surveyed said they experienced a lubricant-related gearbox failure within the last year (1). These failures were most likely related to extreme operating temperatures that created break-point stress on such industrial gearbox parts as seals, bearings and gear teeth.
These higher operating temperatures are precipitated by the demand for more power in a smaller footprint and decreased oil volume. Today’s equipment also needs to handle increased loads and deal with a host of contaminants, including water. Dealing with these demanding conditions requires gear oil that is formulated to reduce stress in a number of ways.
The following are basic requirements for industrial gear oils:
• Appropriate viscosity
• Oxidative and thermal stability
• Solid load-carrying capacity
• Demulsibility (the ability to shed water)
• Resistance to foaming
• Protection against rust and corrosion.
The difference between automotive and industrial gear oils is that industrial gear oils must perform in conditions and applications that vary significantly. Examples are the highly contaminated conditions that exist in mines and the highly aqueous conditions in steel mills. It’s not surprising then that gear base oil and additive manufacturers need a thorough grasp of the performance requirements of advanced machinery and the end-user’s needs.
Additives protect seals and improve thermal, oxidative and viscosity stability. They also provide micropitting resistance, bearing corrosion protection, foam resistance and enhanced demulsibility and load-carrying capacity.
There are many gear oil standards such as North America’s AGMA 9005- E02 EP, Europe’s DIN 51517-3 and Germany’s SEBI 181 226. The newest is the Siemens (Flender) MD specification. In addition, OEMs often use standard tests together with their own requirements. There are also specifications for specific industries such as food processing. The increasing strictures of these specifications and the unique challenges posed by technologically advanced gearboxes require advanced gear oils to fully protect components.
While using the wrong lubricant for the job and incorporating certain additives that promote micropitting can cause gearbox failure attributed to the lubricant, the two most common culprits are excessive heat and water contamination.
TRAITS OF A GOOD GEAR OIL*
LOW VISCOSITY. As the lubricant travels through the filter system, contaminants, (which may originate outside the system or result from inside wear) should be removed. Slow-moving, highly viscous lubricants can be difficult to filter. They can cause pressure at the filter to increase. If sufficiently high, it will trigger a system bypass and allow contaminant-laden lubricant to circumvent the filters. Less viscous lubricants flow more easily through the filtration system where contaminants are effectively removed. This reduces the likelihood of machinery damage and increases equipment life.
Another benefit of using a lower viscosity gear oil is that it may not need to be changed as often, resulting in less costly downtime. Industrial gears operating under heavy loads require extreme-pressure protection for gear components, but mainstream industrial gear oils do not always provide high extreme-pressure performance at low viscosity grades. This means that not just any low viscosity fluid will perform well.
DURABILITY. Industrial gear oils formulated for extended durability keep gears operating correctly and protect equipment by prolonging life, minimizing downtime, maximizing productivity and reducing maintenance costs.
DEMULSIBILITY. Water can get into the system (especially the reservoir) in many ways, leading to corrosion and compromised performance. Because of this, gear oil must be formulated to quickly separate water through the range of temperatures found in industrial gearboxes. This will extend the life of the oil and the machinery.
DEDICATED FOR INDUSTRIAL USE. There are two types of industrial gear lubricants. The first, so-called universal gear oils, are formulated so they can also be used in automotive gear applications. Universal fluids (formulated for automotive and industrial use) may contain components that are unnecessary for and/or harmful to industrial gears. On the other hand, they may omit components that are critical to industrial use (demulsibility additives). Gear oils for industrial applications are formulated with additives necessary for protection and optimal functioning.
SMART ADDITIVES. Conventional additives that improve extreme-pressure properties in gear oil are often susceptible to thermal instability, which encourages sludge. But additives are available that improve thermal stability, discourage sludge formation and provide extreme-pressure protection. This allows high extreme-pressure performance and cleanliness throughout the full range of viscosities.
* Based on five factors cited by Lubrizol product manager Tim Cooper.
MICROPITTING
While it’s fairly easy to spot micropitted gear teeth with a basic flashlight (they appear dull, etched and/or stained with gray speckles and sparkles), micropitting can be difficult to see under fluorescent lighting.
STLE-member Bob Shorter, industrial specialist for Chevron Global Marketing, explains, “Micropitting on gear teeth is the result of metal-to-metal contact at the asperity scale where plastic or elastic deformation creates material loss that manifests as micropits. Micropitting is a function of many things, including gear manufacture and quality, EHL viscosity calculation/ selection, the EP additive package, base oil selection, debris/contamination and operating parameters, including temperature and load.”
Micropitting starts with fatigue cracks on the surface (or just below the surface) of the gear teeth. These pits are caused by metal-to-metal contact of rough surfaces. But because cracks can form below the surface of the gear teeth, high-speed gears with smooth surfaces and good film thickness also can become pitted.
STLE-member Ravi Shah, staff engineer at Chevron, explains, “Typically, lubrication in this equipment is under a hydrodynamic or elastohydrodynamic (EHD) regime. In the EHD regime, when the surface roughness of bearings or gears matches the lubricant film thickness, parts of the two surfaces come in contact with each other causing micropitting.”
“Surfaces subjected to heavy loads, high temperatures and a lubricant that doesn’t have a high enough viscosity will experience micropitting,” Shah adds. “Presence of water will also aggravate micropitting. Certain properties of lubricant basestocks and additives (i.e., antiscuff agents) affect micropitting, as does viscosity. On the other hand, some lubricants can stop the process.”
STLE-member Tim Cooper, Lubrizol’s industrial product manager for Europe, Africa and the Middle East, explains, “There are various theories regarding the causes of micropitting,” he says. “It is often talked about in relation to the wind turbine industry, but we see it in many other applications, too. In some cases, micropitting may lessen over time, while in others it can ultimately lead to vibration, noise or even more destructive phenomena such as macropitting.”
HEAT
When it comes to heat-related issues, gear oil serves two functions: it removes heat in the machinery generated by friction, and it protects itself from viscosity breakdown due to heat. The viscosity of a lubricant decreases as the temperature increases. So the viscosity of the oil must be high enough to provide an adequate lubricating film but not so high that it creates friction within the film itself.
With the constant pressure to increase operating loads, gearboxes are burdened with increasingly hotter operating temperatures. As a result, improved thermal stability in gear lubricants is an imperative. Today’s gear oils need to be formulated to withstand the entire temperature range that the gear could be exposed to (both within the system and in the ambient environment). This will not only help to maximize the life of the gear oil but also of the gears themselves.
WATER CONTAMINATION
“Contamination is a key interest for some industrial customers,” says Nelson Tam, Lubrizol’s industrial product manager for ROA (Rest of Asia). “Their most common problem is foaming and lowering of demulsibility performance. Contamination is most common in gearboxes in cement plants and plants that handle coal—such as coal mines and coal-fired power plants.”
Shah adds that contamination also can occur in the proximity of sea/water sources and where the temperatures vary significantly between daytime and nighttime.
Abrasive dust particles can penetrate the oil film and cause surface distortion and wear. Water contamination can rust gear surfaces and, in the extreme, destroy the gear completely. Consider that just 1% of water in an industrial gear oil can reduce bearing life by up to 90% (2). And the damage and contamination can quickly escalate.
The effectiveness of a gear oil is compromised when the oil and water do not separate and the oil becomes diluted. Experts agree that using a gear oil that quickly separates from water is the most effective way of reducing the risk and consequences of water contamination. Gear oil with improved water separation properties not only allows faster and easier water draining, it also reduces the frequency of oil changes.
Another way to manage water contamination is to identify potential contamination points early on and institute measures to reduce the ingress and counteract the effects. The strategy is to prevent water from entering the system in the first place. A secondary strategy is to limit the water’s ability to damage components. A good way to do that is to opt for a lubricant designed to maintain its properties even when small amounts of water enter the system.
“All industries are susceptible to contamination,” Shorter says. “Some of the worst environments are generally those industries that are dealing with climate elements.”
TRENDS
“The general trend is toward gears operating under heavier loads and higher temperatures, smaller sumps (lubricant volume) and higher power density,” Shah says. “The demand on the lubricant is significantly increased, requiring better EP performance, micropitting resistance, oxidative properties, lower sludge-forming tendency and better foam performance.”
Today’s increasingly smaller gearboxes are made from lighter weight materials. At the same time, they must produce more power, be more durable and more reliable. The bearing loads and speeds of the gear teeth are also trending higher. This means that a smaller gearbox with less lubricating oil needs to support gears with much higher workloads. Not surprisingly, this results in higher temperatures, but it also results in accelerated oxidation. Oxidation is a particular problem for industrial gear oils because it contributes to sludge formation.
“Just like many other types of equipment, industrial gearboxes are experiencing a drive toward higher power densities that place greater demands on the lubricant,” Cooper explains. “In some cases, they are also using steel qualities, which have propagated the amount of micropitting fatigue in a range of applications and industries. Other trends include energy-efficient oils and longer-life oils to extend drain intervals.”
Cooper adds, “Oils today are formulated with a greater level of durability in mind—resistance to micropitting fatigue, greater thermal stability and (very important) the realization that performance must be retained through the life of the oil. As an example, it’s no longer acceptable to market oil that has good foam control or water-shedding properties when new but after a few months of service the properties fall away, leaving the gearbox operator with an under-performing system.”
Even with regular lubricant maintenance, punishing operating conditions of higher heat, higher loads, higher pressures and contaminants can compromise a gear system. The lubricants must withstand increasingly harsh environments that also quickly deplete essential gear oil additives.
FOUR TYPES OF GEAR OILS
R&O INHIBITING GEAR OILS. Rust and oxidation (R&O) inhibiting gear lubricants perform well over a range of gear sizes, speeds and outside temperatures. They lubricate well if both the gears and bearings are lubricated from the same reservoir. Because they do not adhere to the gear tooth surface, it’s best if the gear teeth are constantly relubricated. R&O inhibiting gear oils can be conditioned with heat exchangers and filters for consistent temperature and cleanliness.
EP GEAR OILS. Extreme-pressure (EP) gear oils are recommended for gear drives subjected to conditions of high load, medium-to-high slide and high-power transmit. EP gear oils can contain additives that are corrosive to brass and bronze components. But EP gear oils that utilize chemistries noncorrosive to these components are available. These oils also perform well over a range of gear sizes and speeds and outside temperatures. Gear teeth must be continually relubricated.
COMPOUNDED GEAR OILS. Compounded gear oils lubricate gear drives where the high sliding of gear teeth requires a friction-reducing agent to minimize heat and improve efficiency (enclosed worm gear drives). Unlike R&O and EP oils, they do not perform well over a wide temperature range and have a high operating temperature of 180 F (82 C). Like R&O and EP oils, constant relubrication of the gear teeth is encouraged.
SYNTHETICS. Synthetic gear oils are primarily used in applications where mineral-based industrial gear oils are unable to perform. Synthetic gear lubricants can contain R&O inhibitive additives and/or EP additives. Synthetic gear lubricants offer advantages such as improved thermal and oxidation stability, lower volatility and evaporation rates, improved energy consumption and reduced flammability.
NEW GEAR OILS
As a result of increased demand on the lubricant, some lubricant companies, including Chevron, are developing higher quality lubricants with improved EP, micropitting resistance, oxidative properties, lower sludge forming tendency and better foam performance. Some lubricants are moving to synthetics using Group III, IV and V components (3). There are two major considerations in the formulation of new industrial gear oils:
• Increased emphasis on cost reduction (longer lubricant life)
• Design changes to improve gearbox efficiency (smaller gearboxes with less oil capacity).
The good news is that newer oils are formulated with high levels of extreme- pressure properties across a spectrum of viscosities. This gives smaller gearboxes carrying high loads extra protection. But additives to improve extreme-pressure properties can decrease thermal stability, resulting in the formation of sludge. Industrial gear oil additives do exist, however, that provide the balance of thermal stability and extreme-pressure protection. The combination of these two factors adds value by prolonging the life of gearboxes and maximizing efficiency (4, 5).
Regarding the Asian market, Tam explains, “The general trends in Asia are not different from other zones. But more customers in Asia are looking at cost-effective products, which means special and long-drain products—they would like a product developed with their own base oil. Asian customers are always interested in long-drain intervals, energy efficiency, low cost, OEM approval and high loading.”
The trend toward lowering gearbox manufacturing costs, while at the same time allowing for increased in-use productivity, places even more stringent demands on gear oils. This means high load-carrying capabilities that maintain gearbox cleanliness will be the norm for gear oils.
SYNTHETIC FLUIDS
Synthetic industrial gear oil goes where mineral gear oil can’t—at temperature extremes, in exceptionally high loads, in challenging operating environments and when there are special requirements.
Shah explains, “Replacing fluid in a gearbox located 100 meters high is not an easy task. As a result, synthetic products are finding more and more use in manufacturing wind turbine gearbox lubricants. The same is true of other difficult and demanding applications involving factors such as high loads, extremes of temperature or vibrations.”
The most commonly used synthetic industrial gear oils are ester oils, synthetic hydrocarbon oils and polyglycols. It’s important to note that while synthetics have many advantages, in some instances they do not perform as well as mineral-based oils.
The specific advantages of synthetics (which vary according to the basestock) can include the following:
• Better viscosity protection in high temperatures
• Better low-temperature properties
• Better thermal and oxidative resistance
• Reduced volatility and evaporation
• Better lubricity
• Reduced flammability (depending on the basestock)
• Resistance to residues and deposits at high temperatures
• Extended drain intervals
• Reduced energy consumption.
Disadvantages may include the following:
• Reactions (such as corrosion and hydrolysis) in the presence of water
• Compatibility issues with materials such as some metals, paints and elastomers
• Poor miscibility with mineral oils
• Higher price (usually but not always).
Synthetic industrial gear oils can contain rust and oxidation-inhibiting additives and/or antiwear/EP additives. “Synthetics offer an alternative for the end-user, but Group II+, Group III and Group IV base oils are all viable choices,” Shorter says. “These base oils often lead to longer lubricant life, better performance and ultimately value for the end-user.”
SELECTING THE CORRECT GEAR OIL*
There are two primary considerations for selecting the correct gear oil for an application:
GEAR SPEED
The now superseded Industrial Gear Lubrication Standards, AGMA 250.04, used center distance as the primary criterion for gear lubricant selection. The new version of this standard, designated AGMA 9005-D94 Industrial Gear Lubrication, has adopted pitchline velocity as the primary selection criterion. The pitchline velocity determines the contact time between gear teeth. High velocities are generally associated with light loads and very short contact times. For these applications, low-viscosity oils are usually adequate. In contrast, low speeds are associated with high loads and long contact times. These conditions require higher viscosity oils. EP additives may be required if the loads are very high.
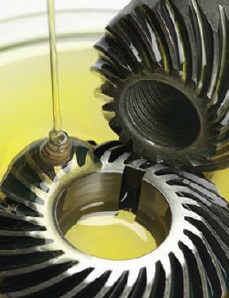
www.canstockphoto.com
TEMPERATURE
Ambient and operating temperatures also determine the selection of gear lubricants. Normal gear oil operating temperature ranges from 90 F to 100 F (50 C to 55 C) above ambient. Oils operating at high temperatures require good viscosity and high resistance to oxidation and foaming. Caution should be exercised with abnormally high temperatures. High operating temperatures indicate oils that are too viscous for the application, excess oil in the housing or an overloaded condition. Each of these conditions should be investigated to determine the cause and correct the problem. Oil for gears operating at low ambient temperatures must be able to flow easily and provide adequate viscosity. Therefore, these gear oils must possess high viscosity indices and low pour points.
*Click here.
SIEMENS MD SPECIFICATION
Cooper explains that the latest Siemens MD specification not only looks into conventional aspects of gear and bearing lubrication (wear protection, corrosion resistance, etc.) but also takes into consideration compatibility between the lubricant and every component within the gearbox that it will come into contact with. He adds, “Thus there is a very strong emphasis on elastomeric seal and paint compatibility with the oil. This can place limitations on the types and amount of additive chemistry that can be deployed to deliver the necessary lubrication properties.”
Before Siemens MD approves oils for use in Flender helical-, bevel- and planetary gear units, the manufacturer must warrant that the oils are of CLP quality according to DIN 51517-3 (6). There are also many other application-specific properties that must be met.
The qualification testing and submission of the approval documentation must be conducted by the oil manufacturer or marketer. This means gearbox users cannot request an approval.
ADDITIONAL OEM GEAR OIL SPECIFICATIONS*
In addition to standard specifications for industrial gear oil, many gear manufacturers’ specifications contain additional demands, such as the following:
• Intensified scuffing tests
• Micropitting tests at 140 F (60 C) and at 194 F (90 C)
• A roller bearing wear test
• A low-speed wear test
• A pitting test
• A test to determine load-carrying capacity
• A filtration test
• A foaming test
• Low-temperature tests (for behavior and flow)
These additional bench tests attempt to replicate the extreme conditions to which gearboxes and gear oils are subject and quantify the performance of the various formulations.
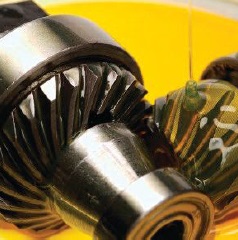
www.canstockphoto.com
*Click here.
All tests must be conducted no more than one grade above the lowest viscosity of the oil. The exception to this rule is the Flender foam test, which must be tested in the highest viscosity grade. All test data must be carried out on oil samples of the same composition according to the formulation table (which must be enclosed). In addition to the testing and performance requirements, the material safety data sheet (MSDS) and technical data sheets (TDS), including the temperature-viscosity curves for each visincosity grade, must be submitted for approval. The lubricants must be identified by submission of an IR (infrared) reference spectrum and ICP (inductively coupled plasma) reference values for the viscosity grades requested for approval (7).
All test data must be generated within a Siemens-approved laboratory for application-specific testing. Siemens will not accept test data generated in an unapproved laboratory (8). For the approval of a viscosity range, oil manufacturers must guarantee that the performance level obtained in a test on a specific oil are consistent for that product independent of production location or viscosity grade across the viscosity range. In addition, the oil manufacturer has to warrant that the required properties do not only apply to fresh oil, but that they also do not deteriorate within permissible tolerances through the entire period of use. The period of use for mineral oils must be at least 10,000 operating hours or two years maximum, and for synthetic oils at least 20,000 operating hours or four years maximum, assuming an average oil operating temperature of 176 F (80 C).
API/DIN CLASSIFICATION OF GEAR OILS
Gear oils are classified by the American Petroleum Institute using GL ratings:
• GL-1 – Designed for gearboxes operating at low sliding speeds. It does not contain any EP additives and is often used in applications containing parts made of yellow metals. Additives can increase resistance to oxidation, protection from corrosion and freezing point.
• GL-4 – Designed for gearboxes and main hypoid gears operating at high rotation speeds and low torques.
• GL-5 – Designed for gearboxes and main hypoid gears operating at high rotation speeds with impact loads and low torque or at low speeds and high torque.
Gear oils are generally classified in Europe using the DIN 51517 standard. The following DIN 51517 classifications of gear oils are used most often:
• DIN 51517 CGLP – Contains additives that protect from corrosion, oxidation and wear at the mixed friction spots, as well as additives which improve characteristics of sliding surfaces.
• DIN 51517-3 CLP – Contains additives which protect from corrosion, oxidation and wear in the mixed friction zone (this is the Siemens MD specification).
• DIN 51517-2 CL – Contains additives that protect from corrosion and oxidation, suitable for average load conditions.
“Some of the challenges of the specification include extensive and expensive testing of lubricants against a battery of tests outlined in the specifications,” Shah says. “Additionally, sometimes there are differences in results when run at different labs. It would be helpful if these tests become standardized DIN and/or ASTM tests.”
The formulations tested and approved by Siemens MD must be identical to the oils produced commercially under the approved fluid name. Any changes to the approved formulations beyond permissible tolerances within production must be noted in writing and sent to Siemens MD. Unacceptable changes will result in voided approval and removal of the oil brand from the approved lubricant list.
Tam says, “Asian customers ask for Siemens MD-approved products, and commercially we have a problem if we cannot deliver such products. It is particularly challenging for some customers who need approval in their own base oil.”
“The pending Revision 14 to the Siemens/Flender specification addresses some of the technical challenges, but the certification/approval process timeframe continues to be slow,” Shorter says (9). Lubricant approval is limited to five years (10, 11).
The Siemens MD specification and its revisions are a giant step forward in ensuring the quality and performance of critical industrial gear oils. OEMs, formulators and end-users welcome the tight regulation of basestock, additives and end products.
With tougher operating conditions, the demands on industrial gearboxes have reached levels that no one could have anticipated even five years ago. As OEMs and operators struggle to ensure the reliability and longevity of equipment, new industrial gear oils that offer protection against high heat and contamination are a key weapon in their arsenal.
REFERENCES
1. Study conducted by Shell and cited here.
2. From: click here.
3. Group I is solvent dewaxed oil; Group II is hydroprocessing and refining oil; Group III is further refined hydroprocessing and refining oil; Group IV is chemically engineered synthetic, including PAO (polyalphaolefin) oil; Group V is a blend of oils.
4. DIN 51517 Part 3, U.S. Steel 224, ISO 12925-1 CKC/CKD, Cincinnati Machine, AGMA 9005-E02, and GM LS-2 and David Brown S1.53.101.
5. From: click here.
6. Except tests acc. ISO 6247 and DIN ISO 1817.
7. IR and ICP test machinery are used to identify the fingerprint of a lubricant.
8. The list of approved laboratories and contact details can be found here.
9. Revision 14 is designed to streamline the approval process.
10. From: click here.
11. Revision 13 includes the following changes: a second approval criterion for the foaming test; temperature-viscosity curves for each viscosity grade must be submitted; some wording was changed.
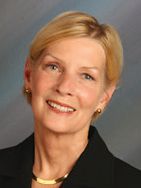
Jean Van Rensselar heads her own communication/public relations firm, Smart PR Communications, in Naperville, Ill. You can reach her at jean@smartprcommunications.com.