Consistently consistent grease
Dr. Robert M. Gresham, Contributing Editor | TLT Lubrication Fundamentals December 2012
Several tests help us ensure that what we want is what we get—all the time.
KEY CONCEPTS
• Manufacturers strive to make grease’s consistency consistently consistent.
• If the consistency of a grease isn’t thick enough, it has a hard time staying put. Too thick, and we have trouble pumping it.
• Several tests help keep grease consistent, and NLGI has a classification system.
ONE OF THE MAIN GOALS IN MANUFACTURING is to make the same product the same way to the same specifications—or consistently consistent. In the case of one of the properties of grease products, we strive to manufacture grease to a consistently consistent consistency. Sound like I’m playing with you? Perhaps, I am—just a little.
What is consistency in grease? Consistency is a basic property describing the softness or hardness of a grease, i.e., the degree to which grease resists deformation under the application of force. Consistency is the one property that is always specified on purchase (except in the retail world). The consistency of grease depends a little bit on the viscosity of the base oil and some additives, and, to a much greater extent, the type and proportion of the thickener.
Why do we care if the consistency of the grease is consistently consistent? One of grease’s jobs is to stay put. Grease is a semi-solid that in most applications is supposed to remain where it is applied to provide lubricant when it is needed. Most equipment designs are based on the grease staying put in order to lubricate and also to act as a seal to prevent contamination from entering into the contact area. In some designs, the grease is asked to “slump” or flow but slowly. Further, the consistency might need to be adjusted to enable pumping through a central lubrication system, especially in winter. This property, slumping, is illustrated in the pictures shown in Figure 1.
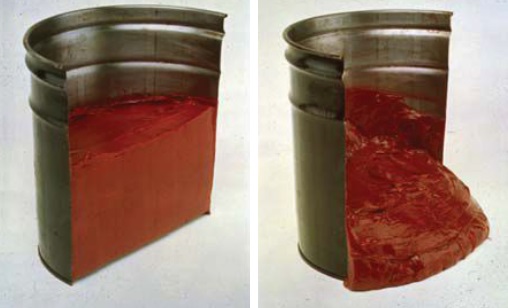
Figure 1. (Courtesy of John Doner, ExxonMobil)
Consistency is usually measured by means of The Cone Penetration Test, per ASTM D-217. The results also can be affected by recent agitation or applied shear stress. To take this phenomenon into consideration, grease is usually subjected to “working” (a standardized churning process) prior to measuring its penetration value. The Cone Penetration Test is one of the most commonly performed tests on grease products. In the test, a brass cone is dropped into the grease and the degree to which the cone penetrates into the grease is measured on the dial in millimeters. Figure 2 shows a picture of the penetrometer, the device used to measure penetration.
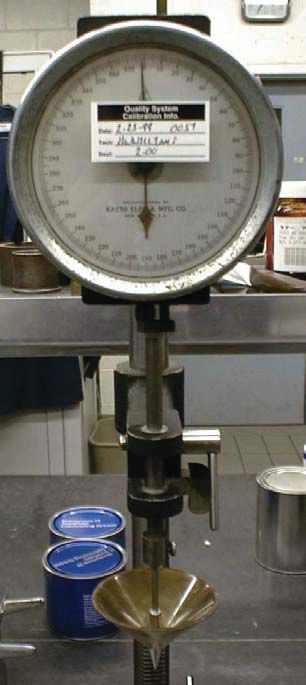
Figure 2. (Courtesy of John Doner, ExxonMobil)
The sequence in Figure 3 shows varying degrees of penetration or consistency with the left-hand picture depicting the beginning alignment of the cone, the middle picture shows the cone dropped into a thicker grease, and the right-hand picture shows the cone dropped into a slightly less thick grease.

Figure 3.
Grease can be affected by agitation or shear stress. To determine this property, we drive a perforated plate through the grease via a so-called stroker for a specified number of cycles, usually 60 strokes. But for applications where shear stability is critical, 100,000 strokes are applied. This equipment is shown in Figures 4 and 5.
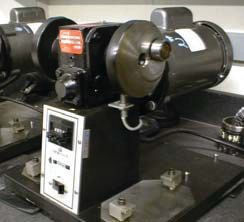
Figure 4. Stroker
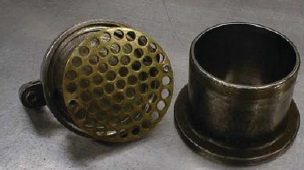
Figure 5. Perforated Plate
The National Lubricating Grease Institute (NLGI) has developed a classification system for rating the consistency of greases based on the millimeters the cone penetrates the grease, as shown in Table 1.
Table 1.
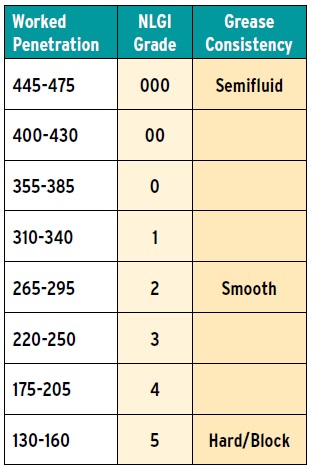
Grease with a penetration of 265- 295 millimeters is classified as a NLGI No. 2. This grade is far and away the most common, certainly the default grade for most equipment designs (and usually what you buy in retail stores). It has a nice smooth consistency that allows the grease to be easily spread onto surfaces, pretty much stays put and yet is thin enough that it can be pumped in many systems operating at moderate ambient temperatures.
Every time we discuss test methods and the results that we obtain, we need to take into consideration the precision and accuracy of the test method. Accuracy seeks to answer the question, “Did you get the correct measurement value?” Bias is a systemic error that contributes to the difference between the mean of a large number of test results and an accepted reference value. The accepted reference value is considered the true value and therefore, bias has to do with the degree to which that true value is not obtained. Thus, in general, through calibration, bias can be reduced or eliminated. Precision has to do with the variability of the test method itself.
Does the method provide the same number every time, or does it vary, and if so, by how much? In ASTM parlance, precision is stated in their published standards as the repeatability and the reproducibility of the method. Repeatability has to do with the difference between two test results performed by the same operator in the same laboratory with the same apparatus on the same test material under constant operating conditions. Reproducibility has to do with the difference between two single and independent results obtained by different operators working in different laboratories on identical test material in the normal and correct operation of the test method.
The method for measuring consistency of greases, ASTM D-217, states that the method’s worked penetration variability for greases, like a No. 2, for more than one lab and operator is 20 units. Thus, in a given situation, the test results could vary by 40 units (+/-20) and statistically have the same result.
Table 2. Reproducibility and Reproducibility of ASTM D-217
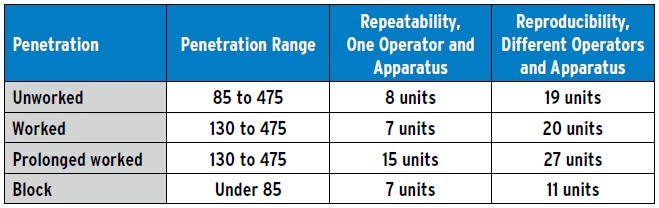
So what we find at the end of the day is that to make a grease of consistently consistent consistency, we must use a method that in and of itself is not especially consistently consistent. Fortunately, for the industry’s needs, the method seems to be neither a blessing nor a curse; rather, it is good enough. But specification writers need to be aware of these kinds of issues when they write their specifications.

Bob Gresham is STLE’s director of professional development. You can reach him at rgresham@stle.org.