Afton Chemical Corporation
Elbow Grease: The Work behind the Art
By Joe Kaperick, Customer Technical Service Advisor – Grease Technology | TLT CMF Plus November 2012
Formulating grease is often referred to as an art, but what sometimes gets overlooked is the work behind the art. A successful formulation requires tremendous resources, expertise and grease of the elbow variety. Like a successful artist, the grease formulator needs to have the proper tools of the trade: a broad palette of additive chemistry, a well-lit (and ventilated) studio and a wide range of tools to create and evaluate potential masterpieces. As many professional artists will attest, the creative process is a painstaking route that can involve a huge amount of effort to create a single finished piece and the toolkit can be a critical factor in both the timing and quality of the final product. Afton’s Grease Team has assembled an exceptional array of instruments and techniques to help drive innovative development and to increase the formulator’s understanding of the science behind the art.
Surface techniques
Understanding the interaction of the grease with the surfaces that it’s intended to protect is critical to the creation of a successful finished product. The effect of performance additives on friction and wear, and their interaction with tribolayers formed under operating conditions can be studied with a variety of tools.
The
PCS High Frequency Reciprocating Rig (HFRR) is useful for examining the boundary lubrication regime measuring friction, wear, and film formation of grease formulations. In these tests, a small sample of grease is placed at the interface of a ball and a disk. The ball is oscillated through a path that can range from 20 µm to 2 mm at a frequency of 10 to 200 Hz. Loads of up to 10 N can be applied at temperatures ranging from ambient to 150°C. Although the standard materials are ANSI 52100 steel, the ball and disk material can vary from brass to chrome to plastics to suit the application for which the grease is being developed.
The
PCS Mini-Traction Machine (MTM) allows thin-film friction coefficients of greases to be measured under EHL, mixed and boundary lubrication conditions. A ball and disc in contact are driven independently to create mixed rolling/ sliding contact and traction measurements are taken as a function of speed (0.02 to 2 m/s), temperature (75 to 125°C), load (20 to 50 N), and slide-to-roll ratio (1 to 70). The frictional force between the ball and disc is measured by a force transducer. A special attachment for use with greases controls flow of grease onto steel disc and replenishes grease supply into contact area to avoid lubricant starvation.
Use of
PCS Spacer-Layer Imaging Method (MTM-SLIM), see
Figure 1, allows tribofilms formed on surfaces to be studied. Test conditions are employed to ensure that boundary lubrication conditions are present to observe the formation of tribofilms by anti-wear additives. Constructive and destructive interferences of a source light are used to find the thickness of the film. See
Figure 2.
Figure 1. MTM-SLIM with grease scoop attachment.
Figure 2. MTM-SLIM Analysis of Boundary Film.
A
JEOL JSM-5800LV Scanning Electron Microscope (SEM) equipped with a ThermoElectron Nanotrace Detector for performing Energy Dispersive X-ray Spectroscopy (EDX) allows chemical analysis of the tribofilm formed during MTM testing as well those from bearing tests and other materials. The area of interest is examined with SEM images and EDX spectra. This allows for visual examination as well as semi-quantitative measurement of elemental concentrations on surfaces of interest.
Structural tools
Understanding the complex behavior of the thickener/oil mixture allows the formulator to predict performance under “real world” conditions including wide ranges of heat, torque and speed.
The
Anton Paar MCR 301 Oscillatory Rheometer (OR) allows for the study of the flow and deformation of greases under an applied force or stress. This allows qualitative or quantitative analysis of lubricating formulations which cannot be easily defined by a single value such as viscosity. A variety of different techniques can be employed using the rheometer and measurements of characteristics such as yield point and flow point give valuable information about greases’ structural properties as well as the effects of force, temperature, time and additive chemistry.
The use of the
Anton Paar Tribology Cell accessory with the rheometer, see
Figure 3, uses the ball-on-three-plates principle to generate Stribeck curve and friction measurements of greases. It has a normal load range of 1 to 70 N, maximum speed of 3000 rpm and a maximum torque of 300 mN??m (friction force: 58.8 N). A Peltier temperature control allows temperatures from -40 to 200 °C and a moveable sample holder ensures equal load on all surfaces which can be varied to suit the application being studied.
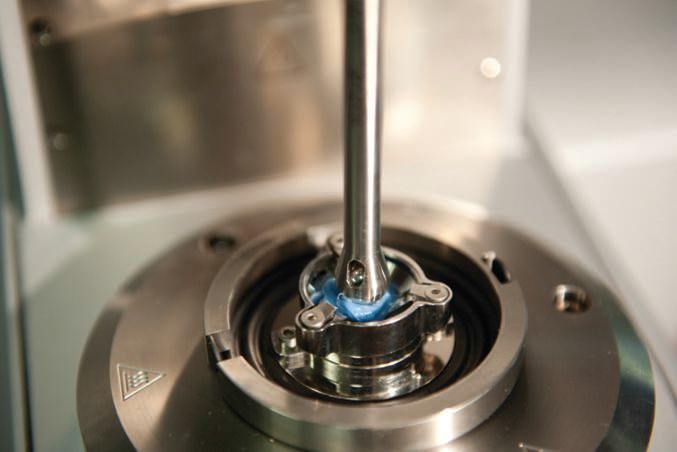
Figure 3. Rheometer with Tribology Cell.
A newer accessory for the rheometer is the
Anton Paar Bearing Attachment, see
Figure 4, which allows testing of grease characteristics in actual bearings of interest. It can be operated under the same conditions as the Tribology Cell to generate friction data at various loads, speeds and temperatures which can be more directly applied to predict field performance of specific grease formulations.
Figure 4. Rheometer with Bearing Attachment.
Rig tests
The workhorses of the grease industry are rig tests designed to measure extreme pressure, friction and wear properties under various conditions. Afton’s rigs are kept busy evaluating various customer grease formulations and new component research.
•
Timken Extreme Pressure Tester fitted with a Falex grease delivery device allows determination of Timken OK load values using ASTM D 2509.
• The
Four Ball Wear tester measures the average wear scar worn into the fixed balls by rotating one ball against them under various conditions as outlined in ASTM D 2266.
• The
Four Ball Weld tester rotates one ball against three fixed balls for 10 second intervals at each load level under standard conditions as described in ASTM D 2596.
• The
Fafnir Fretting Wear test rig employs two ball thrust bearings oscillated under standard test conditions with the fretting wear reported according ASTM D 4170.
• An
Optimol SRV, see
Figure 5, uses a ball-on-disk method to measure both the wear scar generated on the test disk and the coefficient of friction during the test run. A wide variety of loads, temperatures, stroke lengths and frequencies can be used to study performance aspects of grease formulations including but not limited to those outlined in ASTM standards D 5707 (friction and wear) and D 5706 (extreme pressure).
•
Forschungsstelle fur Zahnrader und Getriebebau (FZG) rig assesses the relative load-carrying capacity of greases and oils used to lubricate steel gears; can be used for wear testing especially for open gear applications.
Figure 5. Optimol SRV tester.
Physical characterization
A state-of-the-art analytical lab is the Swiss Army knife in any formulator’s toolbox and Afton’s lab is no exception. From elemental analysis (including digestion techniques for those hard to dissolve grease samples) to spectroscopic techniques (NMR, FTIR) to chromatography (HPLC and GC, with or without mass spec, and a host of other detectors) to oxidation and thermal testing (PDSC, TGA) to a broad range of physical characterization methods, this tool is indispensable to the grease formulator.
As for the “well-lit (and ventilated)” workspace, Afton’s recent 30,000 square foot expansion includes a brand-new grease “studio” with plenty of bench space for modeling new formulations. The $10 MM expansion allows plenty of room to spread out the expanding industrial business testing needs. This new lab now contains a wide variety of blending and testing equipment to support Afton’s grease customers including:
•
Hobart mixers for blending up to 10 gallons finished grease formulation
•
Speedmixer for quickly blending and deaerating up to 500 g grease formulations; allows easy blending of design matrices for performance evaluation
•
Standard grease equipment for measuring penetration, dropping point, copper corrosion
•
EMCOR dynamic corrosion test rigs as well as standard bearing corrosion tests (and humidity cabinet, as needed)
•
Shell Roll Stability for testing stability of greases under low shear conditions at a range of temperatures with or without the presence of water
•
Various test rigs to measure separation of oil from grease at test temperatures
•
Hegman gauge and D 1404 apparatus to measure grease cleanliness
•
Lab-scale grease pilot plant allows production of specific grease thickener formulations, as well as evaluation of polymer and additive effects on finished greases
This array of tools complements our line of innovative componentry that is essential in supporting the creative process of developing successful grease formulations. This line includes components offering AW/EP, rust and corrosion protection, friction modification, thickening, as well as additive packages serving needs from core building blocks to customized applications.