Complexity in oil analysis: Part VI
Jack Poley | TLT On Condition Monitoring September 2012
Maximizing your company’s uptime is important for executing a profitable operation.
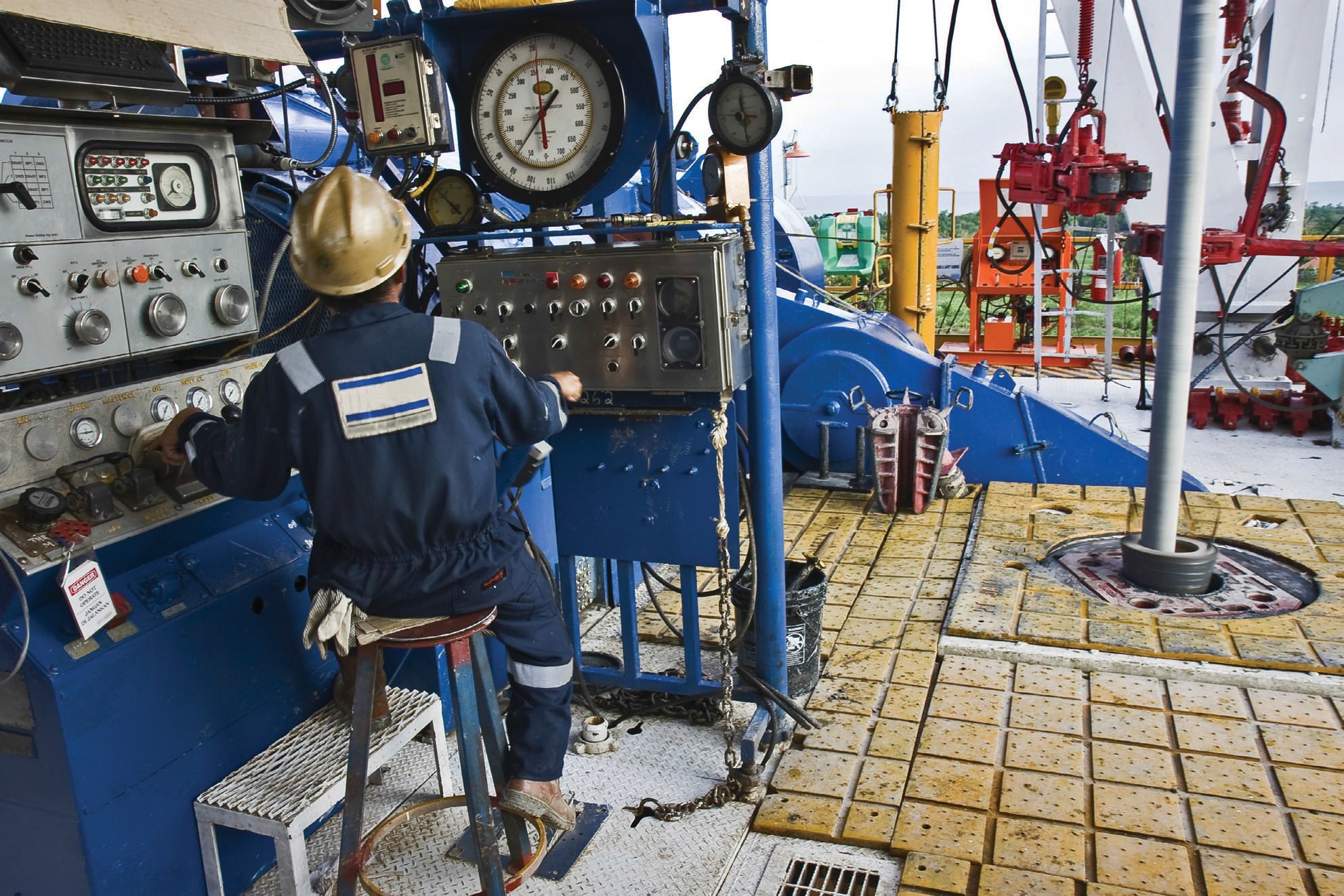
www.canstockphoto.com
DRILLING THROUGH THE EARTH’S SURFACE FOR HYDROCARBON ENERGY AND LUBRICANTS is a process that has existed for over 150 years. Like most processes pursued vigorously, drilling has produced numerous technological advances in techniques and the machinery supporting those techniques.
Today’s oil rigs are bigger, better and more productive than ever before. They are also much more complex and expensive than in times past. It should come as no surprise, therefore, that the vast majority of drilling operations employ both oil and vibration analysis routinely to help ensure uninterrupted production. As usual, condition monitoring is employed as an economic tool to minimize downtime and avoid major repairs where possible, all toward maximizing overall production.
Drilling can be divided into two major categories: onshore and offshore. Like the terms imply, one is land-based and the other is first penetrating water to get to the surface to be drilled beneath the water. Offshore drilling is usually assumed to be in saltwater seas but also occurs in marshes and lakes. Offshore drilling is easily the severest of hydrocarbon drilling applications, representing the harshest general operating conditions, as well as difficult service support access due to an inherently remote operating site.
Whether onshore or offshore, drilling is an expensive endeavor and maximized uptime is of paramount importance to an effective profitable operation.
How do we go about supporting these systems? First, we must understand them.
COMPONENT TYPES
The drilling industry employs a wide variety of components:
•
Diesel Engines – must be at least separated by the manufacturer.
•
Hydraulics (including axial-piston and simple gear) – differentiation required.
•
Compressors (primarily reciprocating and rotary screw) – differentiation required.
•
Gears (numerous varieties that should be separated out when there are enough samples of the same ilk) – top drives must be ferreted out.
What’s the best way to know how to relate to these disparate components? Go to a rig and watch it operate, if you can. You get a feel for the duty cycles encountered, for one thing, which will affect the way you go about evaluating. For example, a top drive, the sophisticated gear system that turns the drill bit, and arguably the most important single component on the rig, will be tasked to operate at various loads and speeds dependent on the depth and angle of the bit and, of course, the nature of the material in which the bit finds itself at any given moment. This frequently results in up/down wear patterns in Fe and Cu (the other two wear metal members of the Big 4; Al and Pb, are not usually prominent, i.e., they are typically <2 ppm).
This up/down routine should make it clear that you will need to verify if the top drive was under an unusually harsh duty cycle within a given sampling interval such that a significant increase is more attributable to stressful usage (controlled abuse) rather than unexplained or unjustifiable wear absent of this activity or from obvious lube contamination with, say, water. In these controlled abuse cases, the rig manager is not going to stop the drive to check on wear unless something else is preventing him from drilling altogether. He is utilizing his equipment for what it was meant to do: generate revenue. More on this later.
TOP DRIVE PATTERNS
Here are some typical data collections for four consecutive samples at roughly equal time intervals (presented chronology from right to left):
Figures 1-2. Two normal wear patterns (Note the subtle oscillation, indicative of duty cycle). There is little to make of this type of movement (the moves from 2-14 and 4-25 for Fe, respectively, are precautionary flags for a jump trend. No other data are of interest).
As shown in Figure 3, here’s a pattern that absolutely you are confident will result in a failure before the next sample, if such failure has not already occurred. Let’s inspect this!
Figure 3.
Whoops, they kept operating and the wear improved (
see Figure 4). How did that happen? If one changes oil frequently,
one can control wear, can’t one? I believe the top-drive replacement came about right after the 142 Fe, but couldn’t find the timing data on it to be perfectly sure. Naturally this rig doesn’t faithfully report lube hours (or component hours, either). The 60 and 70 Fe might be benign wear-in. The copper may be indicative of thrust and bearing cage metal, as the unit settles in. The IA (Intelligent Agent) is programmed to “get off the pedal” once a component is identified as “new” or “newly overhauled,” thus, while the 9 Cu is flagged for a jump trend from its previous patterning, the 14 Cu is ignored (for now).
Figure 4.
Following are two separate top drives; both (obviously) contaminated with drilling mud, the fluid used to cool and lubricate the drill (
see Figures 5 and 6). The previous two data sets also indicated drilling mud, but this was withheld for purposes of the principles being discussed. Peripheral metals like Ba, K, B, sometimes Si, even Al (the latter surely not a wear metal from the drive itself) are the indicators usually found in a variety of muds.
Figure 5.
Figure 6.
One would expect a failure at 1400+ Fe, but, no, that didn’t happen. Repeated draining and flushing forestalled it in time for replacement. A drive replacement was brought in, and this drive (located offshore) will have been rebuilt onshore.
Looking at these last two examples, one wonders (I used to) why we’re asked to test and evaluate if no one’s going to take any action. But this is the nature of the drilling business, and it turns out that it’s also the nature of a top drive, generally speaking. The wisdom is: if the drive begins to show evidence of significant drilling mud contamination, there’s a seal failure, and it’s simply not practical to attempt to replace it while the drive is in place. In most cases, it’s probably impossible without drive removal. So if the decision is made that the top drive is irreparable in practice, then another drive must be brought in to perform an exchange, the least interruptive action to the overall production of the rig.
Whether onshore or offshore, drilling is an expensive endeavor.
www.canstockphoto.com
What
does happen in the interim is that the lube is changed (often including a flushing) virtually every sampling interval or even more frequently in order to minimize the abrasive effects of the mud, but that’s the only concession that will usually be made. There is a certain amount of Russian Roulette occurring at these moments in time, and I’m aware of some failures of top drives where the replacement didn’t arrive on time or wasn’t ordered on time, but that’s the exception to the operating rule. More often than not, they seem to get away with it.
The phrase “The end justifies the means,” comes to mind. And as I loudly hinted in the previous column, your job is not to do or see to the maintenance indicated, but, rather, to indicate that timely maintenance could be effective, based on the data and your experience in assessing it. It is someone else’s decision to accept your recommendation, or not.
Jack Poley is managing partner of Condition Monitoring International (CMI), Miami, consultants in fluid analysis. You can reach him at jpoley@conditionmonitoringintl.com.
For more information about CMI, visit www.conditionmonitoringintl.com.