The mysterious world of lubricant additives
Dr. Robert M. Gresham, Contributing Editor | TLT Lubrication Fundamentals September 2012
This handy primer is your guide to these multifunctional and all-important chemicals.
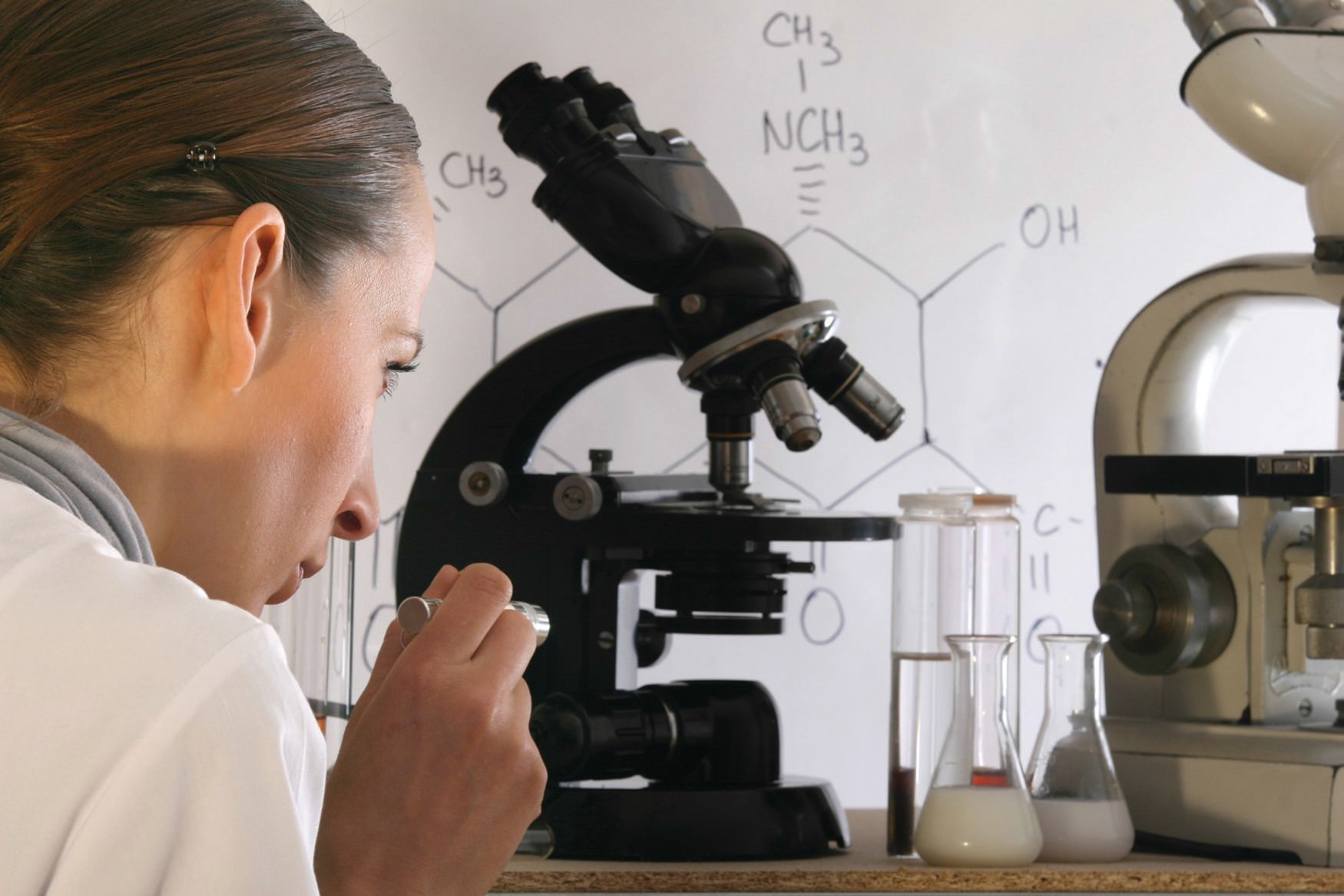
www.canstockphoto.com
KEY CONCEPTS
• Lubricants in most applications clean, cool, lubricate and seal.
• Additives are chemical components or blends used at a specific treat rate to provide one or more functions in the fluid.
• Additives can carry negative attributes. A skilled chemist, preferably one CLS-certified, is needed to safely manage these materials.
Generally in most applications, lubricants must clean by washing away wear debris or metal chips in metalworking operations,cool by removing heat from machine or machining surfaces, lubricate by separating moving surfaces and seal by filling voids and gaps in surfaces.
Lube 101 tells us that oil viscosity is one of the most important properties of lubricants. Likewise, the chemistry of the oil (synthetics, Group I, II or III mineral oils, etc.) is critical for the intended application. But once the formulator identifies the right oil for the application, the properties of the oil are augmented by lubricant additives.
Lubricant additives are used in MWFs, oils and greases. Often the additives are dissolved or dispersed in a medium that makes it easier to use in its intended application such as a water or oil-based MWF, engine oil or grease. Aside from the thickeners in greases, additives generally perform the same functions in greases and oils. In MWFs, many of these same additives are also used for these same purposes.
But in MWFs, additional additives also must be present to perform yet even more tasks. MWFs must promote tool life by removing heat, cooling, (because, just as with oils and greases, heat kills), lubricate the interface between the tool and work piece, clean by carrying chips away and preventing in-process corrosion.
These are the macro issues. However, embedded in these functions are events that need to be prevented, including:
• poor surface finish
• chemical attack on the work piece
• mechanical damage to the work piece
• metallurgical change to the work piece
• thermal damage
• electrical changes to the work piece.
But these are just the operational parts. Additionally, MWFs can contribute to a number of negative things, all of which must be minimized:
• mist leading to respiratory problems
• dermatitis
• fungal and microbial growth.
All of these can lead to employee health and safety issues, plug filters and cause other operational problems.
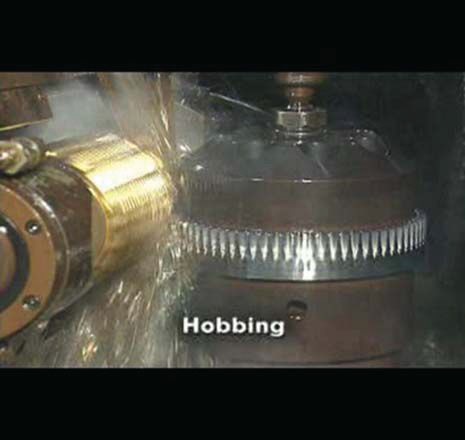
The properties of the oil are augmented by lubricant additives.
Speaking as a chemist, whether it be grease or oil but especially with a MWF, these issues pose a formidable set of interrelated and interacting problems. How do chemists balance all these different issues? Aside from choices of base fluid material, they use a mystifying array of additives.
First, what do we mean by additives? Additives are a chemical component or blend used at a specific treat rate to provide one or more functions in the fluid. Ideally, additive components are multifunctional and generally used at treat rates from < 1% to 35%. They are soluble in mineral oil, water or both in some cases.
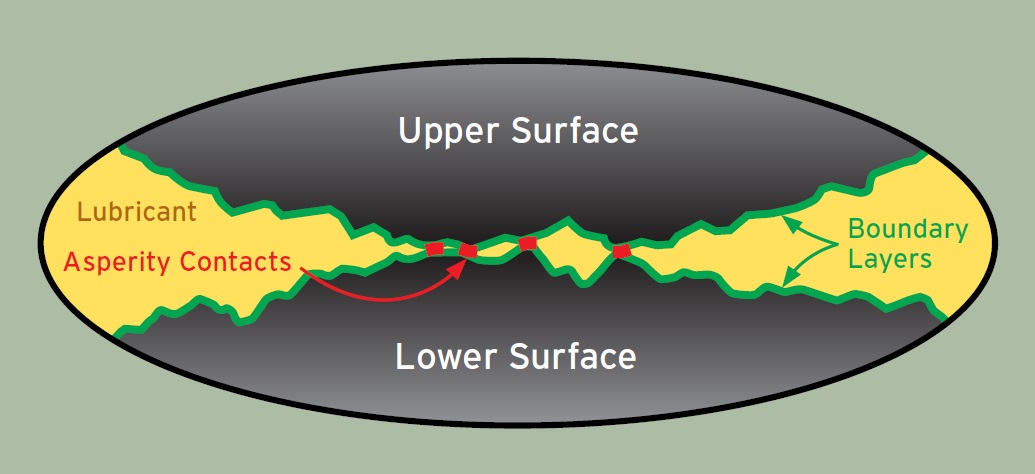
Second, additives provide or assist in a wide variety of functions:
• boundary lubricity
• extreme pressure (EP)
• corrosion inhibitors
• reserve alkalinity boosters
• metal deactivators
• emulsifiers
• couplers
• water conditioners/softeners (chelating agents)
• antimisting
• antimicrobial pesticide
• antifoam additives and defoamers
• dyes.
That’s quite a list! Thus, it is easy to see why chemists look for additives that can be multifunctional and why with so many different chemicals in a formulation, additive compatibility, both with other additives as well as the base fluid, is of critical importance.
Are you mystified yet? In the future, we will take a look at biocides and defoamers in MWFs, but for now let’s take a very quick look at the most common of the performance-related additive types.
Boundary Lubricity Additives enhance the lubricity of the fluid by adsorbing on the surface of the metal to form a film, reducing metal-to-metal contact. These additives typically have a polar group that interfaces with metal and tail that is compatible with mineral oil or water. Examples are lard oil and canola oil. Solid lubricants also are used for boundary lubrication.
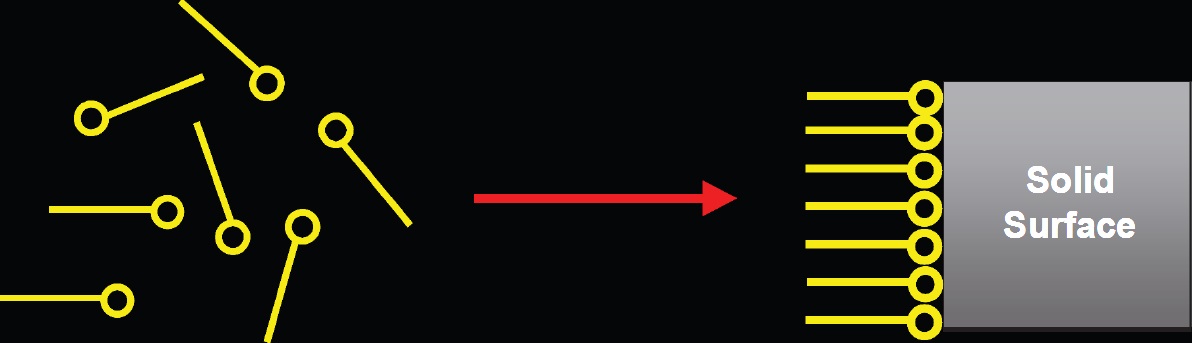
Extreme Pressure Additives are a special type of boundary lubricity additive that actually reacts with the metal surface, instead of adsorbing on the surface, to form a metal salt layer between mating surfaces that reduces friction, wear and damage. In metalworking, the layer is between the tool and the work piece.
These different additives have different temperatures of activation. Thus, the chemist also chooses the additive according to the application conditions so that the additive is, in fact, activated at operating temperatures. Examples of the various chemistries are ZDDP, chlorinated paraffins, sulfurized lard oils, phosphate esters and overbased calcium sulfonates.
Corrosion Inhibitors prevent the fluid from corroding the machine surfaces, metal work piece, cutting tool and machine tool. Corrosion inhibitors perform in two ways by either forming a protective coating on the metal surface (as shown in the graphic below) or by neutralizing corrosive contaminants in the fluid. Examples are overbased sulfonates (we saw where some of these also can act as extreme pressure additives), alkanolamides, aminoborates and aminocarboxylates.
Reserve Alkalinity Additives maintain the fluid’s corrosion protection by neutralizing acidic contaminants and by maintaining the pH in a suitable range, essentially a buffer. These additives also can act as form emulsifiers with other components to stabilize the fluid. Examples are alkanolamines like monoethanolamine (MEA), triethanolamine (TEA), aminomethylpropanol (AMP) and 2-(2-aminoethoxy) ethanol.
Metal Deactivators prevent the MWF from staining nonferrous alloys (such as copper and brass) and reduce corrosion when dissimilar metals contact each other. They act by forming a protective coating on the metal surface. Examples are mercaptobenzothiazole, tolyltriazole and benzotriazole.
Detergents stabilize dirt and wear debris in oil formulations. Emulsifiers stabilize oil-soluble additives in waterdilutable MWFs by reducing interfacial tension between incompatible components by forming micelles (a submicroscopic aggregation of molecules, as a droplet in a colloidal system). These droplets then can remain suspended in the fluid. Milk is an emulsion. In MWFs, examples of emulsifiers are sodium petroleum sulfonate and alkanolamine salts of fatty acids.
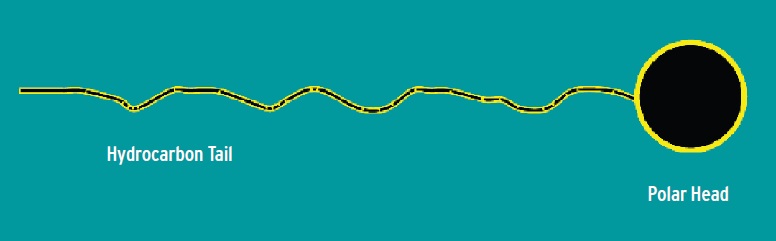
Detergents and emulsifiers all are similar in that they typically have a so-called polar (hydrophilic) head and a hydrocarbon (hydrophobic) tail. The nature of these two parts depends on the application. Dispersing and/or emulsifying dirt, oils etc., is what you do when you wash your hands—you form micelles to solubilize and disperse the dirt and oils.
Couplers assist in stabilizing water-dilutable MWFs in the concentrate to prevent separation of components. Couplers facilitate formation of emulsions for soluble oils. Examples are propylene glycol, glycol ethers and nonionic alkoxylates.
Chelating Agents (also known as water softeners or conditioners) reduce the destabilizing effect of hard water (calcium and magnesium ions) on MWF emulsions. Chelating agents bind calcium and magnesium salts to prevent them from reacting with anionic emulsifiers such as fatty acid salts of alkanolamines. An example might be ethylenediaminetetracetic acid (EDTA).
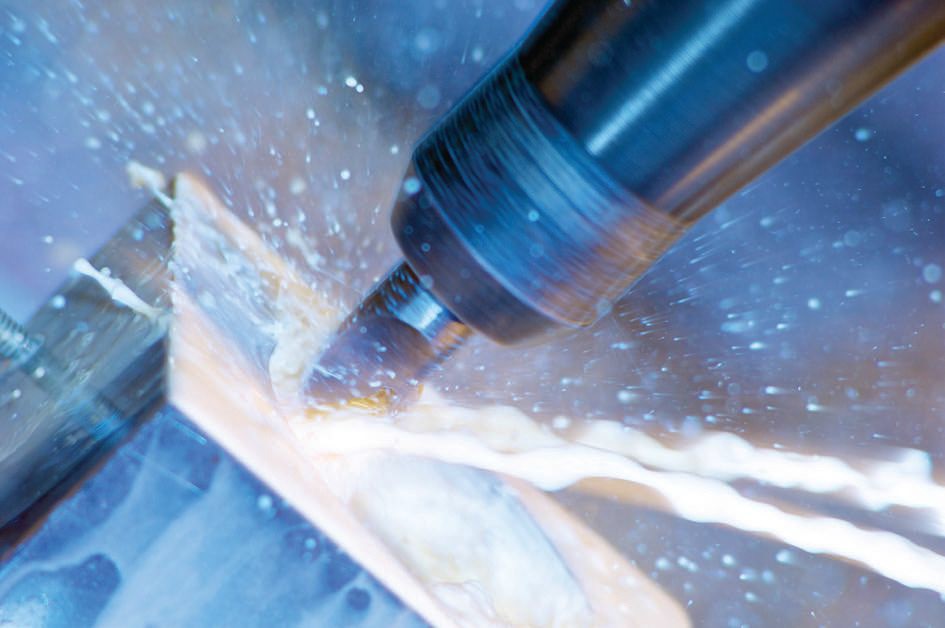
Additives must perform even more tasks when the lubricant is a MWF.
www.canstockphoto.com
Antimist Additives minimize the amount of lubricant that disperses into the air during machining. They are typically polymers and/or wetting agents. For oil-based systems, ethylene, propylene copolymers and polyisobutenes are used. For water-based systems, polyethylene oxides are typical.
Finally, Dyes give the lubricant or MWF a specific color type desired by the customer. After all, “Everybody knows red grease is better than green grease!” Right! Their main value is in water-diluted fluids to indicate that product is present, since some of these can be clear and water-like in appearance. However, dyes carry some negatives as well, as they can stain skin and paint. Some water-soluble dyes are unstable and can change color. And some dyes can pass thru waste treatment systems, resulting in pollution downstream.
Clearly, this is quite a list, and a chemist’s skill is needed to keep everything under control. Arbitrary use of additives at the tankside carries substantial risk, if not done under the supervision of a chemist familiar with the original formulation. Thus, it is important to have a good working relationship with top suppliers of lubricants, MWFs and additives. The pages of this issue of TLT are full of ads from such companies.
STLE certification holders are aware of all these issues. They maintain good relations with suppliers, and they can keep your system in balance and safely working at optimum performance levels. Indeed, this is what they do best.

Bob Gresham is STLE’s director of professional development. You can reach him at rgresham@stle.org.