The growth of biobased metalworking fluids
Jean Van Rensselar, Contributing Editor | TLT Cover Story August 2012
They’re playing an expanded role in protecting the environment and offer superior performance in some applications.
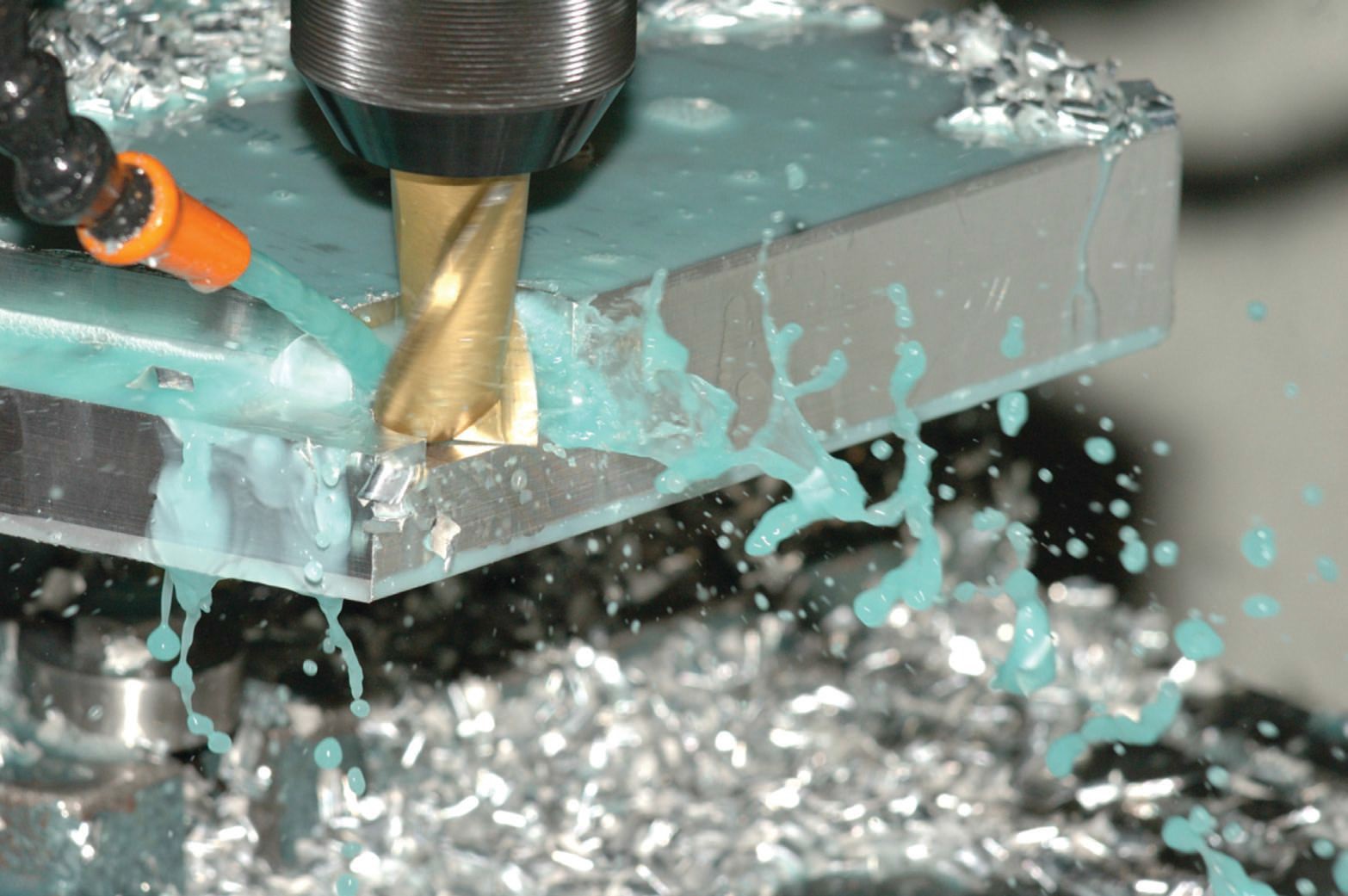
www.canstockphoto.com
KEY CONCEPTS
•
Biobased MWFs in some cases offer superior performance compared to their conventional counterparts.
•
Biobased MWFs have a significantly higher flashpoint than conventional MWFs, making them a safer choice for work areas at high risk for fire.
•
The proper additive package can increase the performance and extend the useful life of a MWF.
To keep up with the growing demand for metalworking fluids that are made from renewable resources, formulators are developing biobased products that, in many cases, perform as well or better than conventional MWFs at a comparable price.
As straight oils, research shows that biobased MWFs can perform significantly better than mineral oils. This is also true to some degree for vegetable stocks emulsified into soluble oil and semisynthetics.
The U.S. Department of Agriculture defines biobased this way: “A product determined by the Secretary (of Agriculture) to be a commercial or industrial product (other than food or feed) that is composed, in whole or in significant part, of biological products or renewable domestic agricultural materials (including plant, animal and marine materials) or forestry materials (
1).”
In the case of biobased MWFs, the basestock is most likely soybeans, rapeseeds (canola), sunflowers or corn. STLE-member John Hogan, technical service manager for metalworking additives for The Lubrizol Corp. in Wickliffe Ohio, explains, “When selecting the best vegetable basestock, there are several factors that need to be considered: end-use application of the product, oxidative stability, saturation level and additive selection. Availability of basestocks in different countries, in different seasons and over the long term is important to consider in the initial selection of the basestock.”
As with most biobased products, in order for MWFs to perform as well as their non-biobased counterparts, chemicals need to be added that compromise the biobased nature of the fluid to differing degrees.
Hogan says, “The use of renewable resources may be desirable, but that does not necessarily make a product green or sustainable. When evaluating the use of renewable materials relative to petroleum products, lifecycle analysis and total environmental impact must be considered. This means the energy consumed and the waste emissions along the entire spectrum of the product must be considered: gathering raw materials, manufacturing the product, distributing the product, product use and disposal/recycling of a MWF must all be considered in evaluating its environmental impact.”
Although biobased MWFs were once a poor substitute for conventional MWFs (offering little advantage other than safety and significant performance disadvantages) new formulations, genetically modified crops and additives are leading to performance that is at least comparable and, in some cases, superior to conventional MWFs. This means that facilities can finally use biobased MWFs to protect their workers
and improve performance without incurring significant additional cost.
STLE-member Craig Mott, executive vice president of Colonial Specialty Chemical in Tabernacle, N.J., explains, “Market drivers include OEM requirements, Federal government mandates and the green movement. Also, additive/surfactant technology is helping the performance of green fluids; this means there are more vegetable oil options, such as improved oxidation, available for the formulator.”
Formulators, distributors and users are confident that biobased MWFs, even with a slew of additives in them, are safer and perform as well or better than conventional MWFs with little price disparity.
In addition to reduced environmental impact, there are genuine performance advantages to using biobased MWFs. But there are still a few issues to be worked out before they become generally accepted (and preferred) alternatives to conventional MWFs.
ADVANTAGES
In addition to helping to protect worker health and the environment, biobased MWFs have a number of performance advantages. Viscosity, lubricity and flashpoint are three areas where biobased MWFs really shine. This is especially true for straight biobased oils and less so for solubles and synthetics.
Greater viscosity stability. Vegetable oil has a high natural viscosity. As the machining temperature increases and as ambient temperatures fall, biobased MWFs tend to hold their viscosity levels better than conventional MWFs.
Better lubricity. Unlike conventional MWFs, biobased oils have a slight polar charge. This charge naturally attracts the oil to metallic surfaces and is resistant to being wiped off. This polarity also leads to better corrosion protection.
Higher flash, fire and smoke points. Biobased MWFs have a significantly higher flashpoint than conventional MWFs—around 200 degrees higher. This makes them a safer choice for all workspaces, especially those that are tightly enclosed and/or near open flames.
Workers at the U.S. Naval Air Depot at Cherry Point, N.C., are seeing the benefits of biobased MWFs every day. There are about 160 machines at the facility using MWFs. After giving a prototype biobased MWF a fair trial, users came to the following conclusions:
•
The flashpoints of straight oils used in the past were 350 F to 400 F. The prototype has a flashpoint of 640 F. Because of its high flashpoint, the biobased prototype provides better heat dissipation and produces less smoke when machining.
•
The graphite-like material from the molybdenum disulfide source in the prototype allows metals to be processed with less friction and less torque compared to the MWF they were previously using.
•
The prototype provides better tool life compared to the MWF previously use.
•
Biobased MWFs lead to a safer and healthier environment (
2).
MWF Quick Primer
MWFs have many applications, but all have the basic purpose of lubricating and cooling the work piece-tool interface, flushing scrap and residue from the work area and improving the surface finish on end-products.
MWFs are categorized into the following four classes:
•
Straight/neat/cutting oil. Ultra-refined oils that are not diluted with water but may contain additives.
•
Soluble oil. Composed of anywhere from 30% to 85% severely refined basestock, water and emulsifiers.
•
Semisynthetic fluids. Containing 5% to 30% severely refined oils, 30% to 50% water and several additives.
•
Synthetic fluids. Composed of compounds that do not contain any petroleum oil.
Each of the four classes also may contain additives such as biocides, corrosion inhibitors, extreme pressure chemicals, defoamers, emulsifiers, stabilizers, dispersants and dyes.
CHALLENGES
Poor oxidative stability, poor hydrolytic stability, microbial growth promotion, warranty issues and higher cost are the five main drawbacks to using biobased MWFs. However, with the right formulation expertise, these challenges are easily overcome.
Poor oxidative stability. This is a significant concern because, among other undesirable effects, it causes expensive tools to wear more quickly. STLE-member Lou Honary, professor and director of the National Ag-Based Lubricants Center, University of Northern Iowa (UNI-NABL Center) in Waterloo, Iowa, explains, “While oxidation stability remains a big concern in most applications where vegetable oils are used, the oils is carried out with the chips or as a film on the machined part, thus the residency of the oil is shorter in the machine than applications like gear oil or hydraulic oils. Nevertheless, oxidation stability is important because most other attributes like solubility and compatibility with additives are easier to address.”
Poor hydrolytic stability. Conventional MWFs are resistant to hydrolytic reactions because they do not contain ester linkages and thus don’t hydrolyze (break down). This is not the case with biobased MWFs. The good news is that a genetically modified basestock that is naturally more hydrolytically stable is currently being developed. Other ways to overcome the poor hydrolytic stability are through additives and/or chemical modification.
Microbial growth. Unlike conventional MWFs, biobased MWFs tend to promote microbial growth—the oil biodegrades in the machinery. This compromises performance and creates a noxious odor. The addition of an approved antimicrobial can minimize these problems.
Prohibitive manufacturer warranties. In some cases, using biobased MWFs could void the manufacturer’s warranty. The U.S. Department of Agriculture, in an effort to promote responsible use of biobased products, is working with OEMs on the issue of maintenance warranties. Specifically, the USDA has been contacting manufacturers, industry associations and service professionals to request information about and ultimately resolve warranty issues. As additional information becomes available on the project, the USDA will post it on the BioPreferred Website:
www.biopreferred.gov (
3).
Cost. The level of cost disadvantage depends on the basestock. In addition, additives required for equalizing oxidative/ hydrolytic stability and microbial growth issues add to the cost. But as petroleum prices continue to escalate and some countries offer tax incentives for using biobased products, the cost differential is becoming less pronounced.
Mott says, “As far as the cost of biobased MWFs, when compared to conventional MWFs, there is still a premium, but this gap is narrowing considerably with petroleum trading at $120 a barrel. Vegetable oils have also moved up in price but not as much as petroleum.”
The basestock for biobased MWFs most likely is soybeans, rapeseeds (canola), sunflowers or corn.
FORMULATION
The development of biobased MWFs has been a research focus for scientists at the UNI-ABIL Research Program since 2002. The center has been formulating alternative, biobased MWFs using renewable crop basestock to minimize environmental, health and safety concerns without compromising performance.
Honary says they’ve discovered that while certain additives like sulfur used for wear protection are effective regardless of the base oil, it may be necessary to use different antioxidants for vegetable oils than those used for mineral oils. The same logic applies to emulsifiers, antibacterials and pH improvers.
He adds that vegetable oils have two main areas that need consideration during formulation and use: oxidative stability and cold-temperature performance. “Since most metalworking applications are indoors, the cold temperature issue becomes relatively irrelevant.” Honary explains: “This makes it easier to focus on improving the oxidative stability while formulating MWFs.”
Mott says that for water-based systems, emulsion stability is the most common customer concern they hear about. “The end-user cannot tolerate their MWFs splitting out in use,” he says. “This is where newer surfactant technology has really helped the formulator. These new surfactants are doing a very good job in keeping the emulsions very stable in both small and large central systems.”
Formulation is a complex science. Hogan explains, “Vegetable basestocks normally require somewhat higher emulsifier content with a different hydrophilic- lipophilic balance for water-extendable products. Selection of emulsifiers and sources of alkalinity are important to consider in order to prevent interactions with the basestock over time that can degrade emulsion stability.”
“Higher quality, high oleic content basestocks are generally easier to emulsify and yield more stable products,” Hogan says. “Longer fatty chains and increased unsaturation generally require higher emulsifier treat rates. Inclusion of antioxidants is essential to limit oxidation and maintain emulsion stability. Selection of the right antioxidant is critical not only for limiting oxidation but also because it can impact aesthetics of the fluid.”
He also points out that while there is a great deal of emphasis on the use of vegetable basestocks to formulate green MWFs, there also are additive technologies based on renewable materials. The new additive technologies are designed to provide the lubrication properties of vegetable oils and are easier to utilize in some water-extendable fluids.
Gene Tripp, sales manager for Performance Biolubes in Cedar Falls, Iowa, says, “Finding the right additives and getting them to remain in the formulation are the real challenges. When it comes to additives, the fewer you use the better. The more ingredients you use and the higher quantity only adds to the cost.”
Fuchs is a formulator and proponent of synthetic esters. The company’s product manager for Cutting & Grinding Fluids, Jonathan Chow, explains: “Variability of supply, hydrolytic stability and oxidation stability have led us to prefer synthetic esters derived from natural vegetable oils. These give much better robustness and consistency. The higher price can be justified by superior performance.”
USDA’s BioPreferred Program
The purpose of the U.S. Department of Agriculture’s BioPreferred® program is to promote the increased purchase and use of biobased products with the effect of reducing petroleum consumption, increasing the use of renewable resources and better managing the carbon cycle, which may contribute to reducing adverse environmental and health impacts. The USDA BioPreferred program has two major initiatives:
•
Product Labeling. The USDA certifies and awards labels to qualifying products to increase consumer recognition of biobased products.
•
Federal Procurement Preference. USDA designates categories of biobased products that are given preference by Federal agencies when making purchasing decisions.
Official audits of biobased products designated as BioPreferred began in March. The purpose of the audits is to ensure the integrity of the voluntary biobased product certification and labeling initiative and the preferred federal procurement initiative. The audits provide oversight and monitoring of the products affiliated with the program to ensure that the products’ biobased content information is accurate and meets the requirements of both initiatives.
For more information, visit
here.
RECYCLING, WASTE TREATMENT AND DISPOSAL
While the term recycling generally refers to collecting and repurposing, when applied to MWFs the term refers to the common practice of continuously treating and reusing MWFs in the machinery. Once the MWF has reached the end of its useful life, it is almost always treated and disposed of—not recycled in the traditional sense. This is due to the fact that, in most cases, it’s already been recycled as much as possible in the machinery.
RECYCLING
The goal of any MWF recycling program is to maintain a stable fluid at optimal performance as long as possible. No matter whether it involves conventional or biobased MWFs, the goal is inherently green since it significantly reduces the amount of waste product in the environment. The same benefits of recycling conventional MWFs apply to biobased MWFs as well (reduced use, little or no equipment downtime, etc.). But in the case of biobased MWFs, aggressive recycling also reduces the strain on natural resources such as crop production.
“If the oil is stable, the recycling of vegetable oil can be done the same as that of the mineral oil-based MWFs,” Honary says. “That is, using centrifuge or other means of recovering the base oil for reuse.” He adds that this is assuming that the vegetable oil doesn’t oxidize during use, which could change it to polymer and render it unrecyclable.
MWFs can only be recycled a limited number of times before they reach the point of disposal. The factors limiting coolant recycling are biological hardness, selective depletion and tolerance to water hardness minerals.
‘Finding the right additives and getting them to remain in the formulation are the real challenges.’
TREATMENT
Waste treatment and disposal of spent MWFs involves first removing the water and then isolating the hazardous components. The remaining product is then hauled away for incineration or recycling. Costs of fluid handling can account for more than 15% of total machining costs (
4).
When treating biobased MWFs, the following three waste treatment processes used for conventional MWFs apply.
Physical treatment. Various physical treatment methods are used effectively to treat MWFs for disposal. Evaporation is a common treatment for small amounts of oily wastewater—fewer than 3,000 gallons a day. The process uses heat to remove water from the used fluid, which has the effect of concentrating the fluid. While this avoids the necessity for sewer discharge, it may require an air discharge permit. Another common physical treatment method that is best for moderate waste fluid volumes is membrane separation via ultra-filtration or reverse osmosis.
Chemical treatment. Chemical treatment uses inorganic or organic chemicals to destabilize or separate emulsions of MWF waste. From a cost perspective, chemical treatment makes more sense for large volumes of MWF waste. Chemical treatment produces a byproduct that, with further treatment, will recover some fluid. Unlike physical treatment, it will treat and remove metals.
Biological treatment. The high organic content of biobased MWFs makes them excellent candidates for treatment via bacterial degradation. But as with all other MWFs, the high oil content of these fluids means that other methods also must be used. Biological treatment for the reduction of organics typically follows either chemical or physical treatment.
Non-hazardous waste can be treated onsite using one of these methods, but ultimately they must be disposed of at a treatment facility or municipal sanitary sewer system (with permission).
DISPOSAL
Even though biobased MWFs are biodegradable, because of additives, dissolved metals and other contaminants, there are still disposal issues. The decision to dispose is usually based on either time in use, loss of key properties or contamination (including biological contaminants) that exceeds a prescribed limit.
For operations that generate a relatively small amount of MWF wastewater, contract hauling or evaporation probably are the best disposal methods from cost and practicality perspectives.
Before disposal, facilities with spent MWFs need to determine whether the MWFs are hazardous. A substance is considered hazardous by the EPA if it contains any hazardous material. However, metal cuttings removed from MWFs are exempt from hazardous waste disposal requirements and can be recycled.
In the case of an inadvertent release into the environment with no intervention, straight mineral oil biodegrades anywhere from 15%-35%, and straight vegetable oil biodegrades 70%-100%.
SUMMARY
What would seem to be a relatively small expenditure for most companies can have a big impact on the bottom line. Researchers estimate that MWFs comprise less than 5% of total plant expenditures yet can impact more than 40% of the plant’s operational budget.
Honary doesn’t consider biobased MWFs to be a novelty anymore, pointing out that The UNI-NABL Center licensed several biobased MWFs and coolants for commercial use in 2000, and the products are currently in the market performing successfully.
Mott also sees mostly blue skies for biobased MWFs. “The industry is moving to green fluids to better comply with OSHA standards and improve on best practices,” he says. “Vegetable-based fluids offer improved worker safety and health benefits as well as economics in terms of tool life. From a right-thing-to-do viewpoint, I also believe individuals and companies want to go green when they can because it just makes sense to do so. It is much more a part of the discussion today than it was 10 years ago. I see continued growth for vegetable oils. Year-over-year sales for vegetable-based oils used as basestocks have been a good area of incremental growth in our industry.”
Experts agree that with additives being roughly equal, there is a definite environmental advantage to going green.
Best Practices For Maintaining Coolant Quality (5)
Coolants need to be filtered and recycled regularly and the equipment completely cleaned at least annually. Assuming that workers are continuously removing metal chips and tramp oil, the Ohio EPA recommends the following coolant system cleaning practices for maintaining optimal fluid quality:
•
Remove the coolant.
•
Remove all metal chips and fines.
•
Clean any oily residues that remain on any surface.
•
Fill the sump with a good cleaner using clean water and circulate the cleaner through the coolant system for several hours.
•
Apply cleaning solution to the machine surfaces that are not contacted by the coolant during machine operation.
•
Pump cleaning solution from the sump.
•
Wipe cleaning solution residues from the sump.
•
Rinse the entire coolant system with clean water. Wipe off cleaned surfaces that are not contacted by the rinse water cycling through the system. Rinse the system again if necessary to remove all residues.
•
Recharge the system with reclaimed or new coolant immediately to protect metal surfaces against corrosion.
REFERENCES
1.
[FSRIA, section 9001]
2.
Naval Air Depot Cherry Point Prototypes Alternative Metal Working Fluid, 2006, summary available
here.
3.
7CFR Part 2902: Designation of Biobased Items for Federal Procurement; Final Rule, 5/14/08, click
here.
4.
“Metalworking Fluids—Clearing Away the Mist?” ANN OCCUP HYG, (2005), 49(4), pp. 279-281. Click
here.
5.
From
here.
Jean Van Rensselar heads her own communication/public relations firm, Smart PR Communications, in Naperville, Ill. You can reach her at jean@smartprcommunications.com.