Testing wind turbine bearings
R. David Whitby | TLT Worldwide July 2012
German manufacturers design new test rig used for rotor bearings in wind turbines.
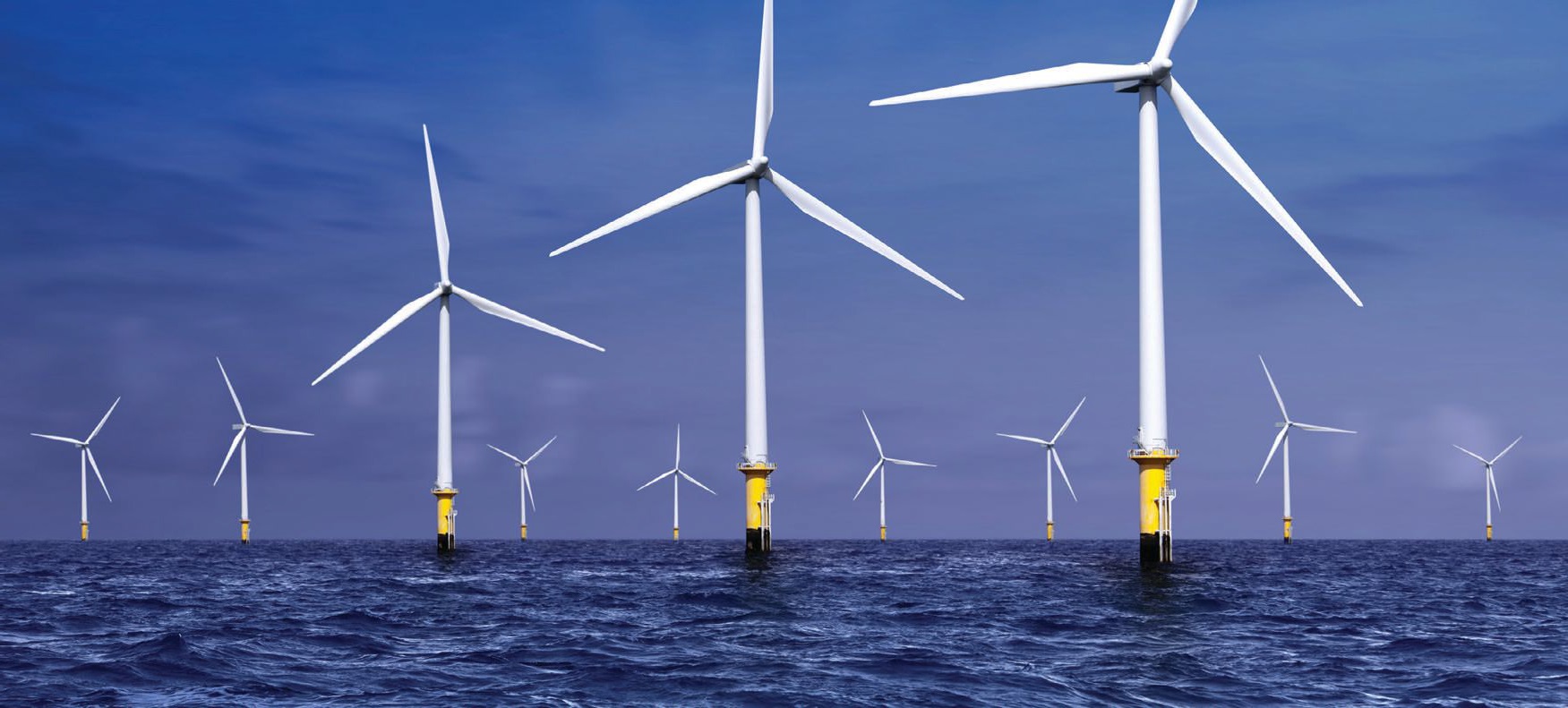
www.canstockphoto.com
Offshore wind turbines are getting bigger and being deployed further out at sea. The advantages are the winds are stronger and more stable than on land using larger megawatt wind turbines. This is potentially good news for European Union member states, which are required to derive 20% of their energy from renewable sources by 2020.
Offshore wind turbines tend to be more complex and costly to install and maintain. One component that has to work throughout the entire life of the wind turbine is the main rotor bearing—a vital part that must operate for 20 years.
In order to optimize bearing design, Schaeffler has invested €7m in Astraios, a large-size bearing test stand located at its Schweinfurt plant in Germany. The test stand, which is 16 meters long-by-6 meters wide and 5.7 meters high, will be used primarily for testing rotor bearing supports for multi-megawatt (MW) wind turbines.
Schaeffler has designed the test bench to simulate the static and dynamic loads and torque that are experienced in multi-MW, mainly offshore wind turbines. It will enable bearings measuring up to 3.5 meters and weighing up to 15 tons to be tested using simulations of the forces that act on wind turbines of up to 6 MW. It is also capable of various movements, including a 5 degree tilt.
The test stand contains four radial and four axial hydraulic cylinders that are fixed to a loading frame. The radial cylinders simulate the weight of a rotor hub with rotor blades, while the axial cylinders generate the wind loads. The rotors and the hub in a large wind turbine can weigh more than 100 tons, which acts on the bearing and generates a static radial load and static nodding moment.
To replicate this, each of the four radial cylinders can generate a maximum force of one meganewton (MN). Similarly, the axial cylinders can provide up to 1.5 MN for simulating the static axial load, as well as the dynamic nodding and yawing moments comparable to the lifting, lowering and turning of the turbine’s nacelle.
The tensioning frame represents the connection side of the nacelle where the unpredictable nature of winds can be replicated. Varying moments are generated on the rotor hub, depending on the position of the rotor blades. Winds acting on the tops or bottoms of the rotor blades generate a dynamic nodding moment. Dynamic yawing happens if the wind turns and blows more strongly from the side.
According to Schaeffler, the new test stand differs from other test benches because it will be able to examine both static and dynamic loads, which is important for offshore turbines, especially when they run in very gusty conditions. Test data for the stand is often provided by Schaeffler’s customers and Germanischer Lloyd, the Hamburg, Germany-based, classification and technical supervisory organization. This is then fed into SARA (Schaeffler Automation System for Research and Development Applications), which is Astraios’s control system. SARA controls the test bench as well as gathering data from sensors embedded in the bearing.
The data is analyzed to generate force, torque and temperature profiles. Three hundred sensors embedded in the bearing also supply information on rolling bearing kinematics and temperature, friction behaviors, stresses and deformations, lubricant distribution and rolling bearing wear. The data on the bearing’s performance can then be used to improve the bearing’s design.
The test rig can run between 10 and 15 rpm. A single test for a bearing can take a number of days, due to a number of load changes, meaning some tests have to run for 200 hours. Several tests on a bearing can take two months or longer, depending on the customer for the wind turbine. Front-end engineering, creating prototype bearings and identifying different materials can also add time to the process. As a result, development of a new design might take 8 to 12 months, according to Schaeffler.
Fortunately, Schaeffler is applying the findings to other large bearing designs.
David Whitby is chief executive of Pathmaster Marketing Ltd. in Surrey, England. You can reach him at pathmaster.marketing@yahoo.co.uk.