‘Control the lubricant, control the process’
Peter A. Oglevie | TLT Shop Floor June 2012
Make sure you connect all the dots when designing a lubrication system.
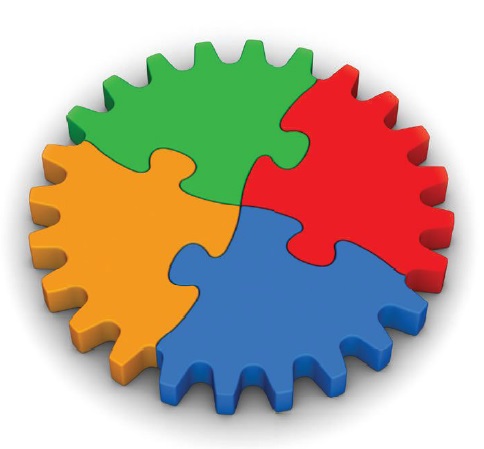
Make sure the pieces fit—what happens in one part of the shop can effect how another part does its job.
www.canstockphoto.com
I’M REPLACING THE DECK ON MY HOUSE and need to decide which cement to use for the footers under the deck. I also must choose which fasteners to tie the deck into the structure of the building and what alloy of fasteners to tie the wood together. I know my limitations and I know I need help. Before any work starts, it is time to hire an engineer and get some degree of control on the deck-building process.
The some degree is determined by engineering. For instance, if I want the deck to support 6,000 pounds, what cement do I have to use for the footers? If I use treated lumber, do I have to use stainless steel fasteners? If I choose to build the second story deck, how many bolts do I need to anchor it to the current structure to achieve the load I anticipate?
The shop floor is every bit as complicated because you are dealing with a process. What happens in one part of the shop can affect how another part of the shop does its job. The job of managing processes is usually handled by a manufacturing engineer. It is his job to make sure that any new products the shop floor produces fits into the processes he has in place. He must also make sure any new lubricant introduced onto the shop floor does not interfere with other operations in the plant.
A wise man (my father) once told me, “If you do not control the lubricant, you cannot control the process.” My goal this month is to remind everyone of this very point.
I remember one of the most successful processes I ever set up. A company was looking to put in a line of machines to produce engine oil filters. It had just started the project when I became involved. The manufacturing engineer had no idea as to what he would use for a lubricant. He did not even have the machines or dies. He had, however, made many of the decisions regarding the type of lubricant he would use. He had already ordered in-line washers for cleaning the parts coming out of the presses.
When I was called in, we were limited in our choices of lubricants by the time, temperature and chemistry offered in the washer he had ordered. I, of course, had many more questions about his goals. We came up with one more limitation for the lubricant. The wash system had to be able to go down the sewer without treatment.
With all the limitations in mind, I asked about the die shop that would be making the tools for the job. He was taken by surprise by the question and herein lies the point. He had given the drawings, specifications, materials and timetable to the die shop with no consideration given to the lubricant. I pointed out to him that unless we supplied a lubricant to the die shop for testing, the workers there would use whatever lubricant made the part work—and chances were good it would not come off in his washer or be acceptable to his sewer system. He would lose control of his process even before the dies reached his shop floor.
We were early enough in the die-development process to get the changes made to tool steels. This allowed us to meet his requirements for washers, which had already been specified and fit the product into his process. I will not say it all went smoothly, it never does. I spent a lot of time tweaking the product with the chemist, and we were on the verge of losing all of our work on a couple of occasions. In the end, however, we pulled a newly engineer lubricant and a smooth process out of our hat.
Now back to the deck. Early on I hired an engineer, and in the past year since I have been working to answer his questions about soil, building structure and existing footing. He has my specifications for a 6,000-pound load. He will supply a structural blueprint and make decisions as to fasteners, cement and tying the deck to the existing structure. I just build what he engineers.
Pete Oglevie is president of International Production Technologies in Port Washington, Wis. You can reach him at poglevie@wi.rr.com.