Occam’s Toothpaste
Evan Zabawski | TLT From the Editor June 2012
Often the simplest answer is the best.
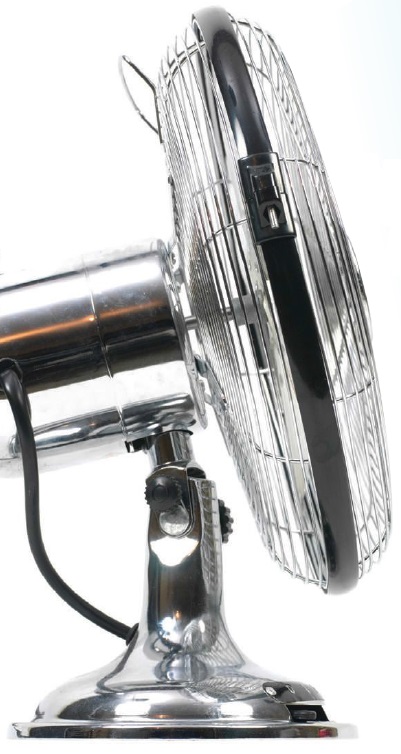
Other things being equal, a simpler explanation is better than a more complex one.
SOMETIMES WHEN I AM TRAINING, I WILL HAVE A GROUP THAT CONSISTENTLY OVERTHINKS its answers. The following question often results in this overthinking: Given an oil analysis report that shows a decrease in both viscosities and all the additive metals, what single action can explain these results? Often the answer given is that the additives have all depleted and, therefore, the oil is breaking down, causing the viscosity to change.
To suggest all the oil’s additives are depleting is both unlikely and an assumption. When a lubricant breaks down, it often oxidizes and viscosity increases. When most additives deplete, they remain in the oil and are still measured by routine oil analysis. To further suggest that the loss of additives has much to do with the decrease in viscosity would only be correct—if the example were a multigrade or VI Improved oil, which is another assumption.
If the answer still proves elusive, I segue into a discussion about seeking the simplest answer. Rather than taking the discussion to the philosophical level, I try and keep it grounded in reality. There is an anecdote I like to share, which doesn’t really provide any insight into the correct answer, but it lightens the mood and offers a humorous perspective on the simplicity of the answer I am seeking.
The anecdote is based on the philosophy of Occam’s Razor. The term is attributed to Franciscan monk and English logician William of Ockham and is often summarized as “other things being equal, a simpler explanation is better than a more complex one.” The reference to razor refers to shaving away any unnecessary assumptions.
The anecdote describes a toothpaste factory that has an excessive number of empty boxes coming off the production line. As the story goes, the CEO got the top people in the company together to come up with a solution.
After several months and millions of dollars, they came up with a solution. Scales were to be installed on the production line immediately after the packaging stage. If a box did not weigh enough, a bell would sound and lights would flash, and the production line would stop automatically so that a line worker could remove the empty box and restart the line.
After the scales and alarms were installed, the factory was no longer shipping empty boxes. The CEO thought that the project was money well spent until closer inspection of the statistics revealed an anomaly. The scales had picked up more than a dozen empty boxes every day for the first few weeks, but recently there were none.
Concerned the scales were not functioning properly, the CEO sent engineers to check them. The engineers reported that the scales and alarms were functioning properly. The answer was simply that no empty boxes were reaching the scales.
Rather puzzled, the CEO went down to the factory floor for a firsthand look. Just in front of the scales sat a cheap desk fan, blowing empty boxes off the line and into a bin. The CEO asked a nearby worker what the fan was doing there. The worker replied that the fan was installed because they had gotten tired of walking over every time the bell rang.
Once we all have a chuckle, I ask the group again if they can think of a simple and likely answer to the change in results. At this point, someone usually says that the system has been topped up with the wrong oil. We discuss that this wrong oil must be lower in viscosity and have different additive chemistry. The only fair assumption being that the oil already exists on site.
The answer fits and is a reasonably common occurrence. Most important, it is simple. We don’t always need to think outside of the box. Sometimes there is no box.
Evan Zabawski, CLS, is the senior reliability specialist for Fluid Life in Edmonton, Alberta, Canada. You can reach him at evan@fluidlife.com.