Keeping up with contacts
Drs. Wilfred T. Tysoe & Nicholas D. Spencer | TLT Cutting Edge April 2012
Industrial companies sponsor basic research into contact-lens tribology.
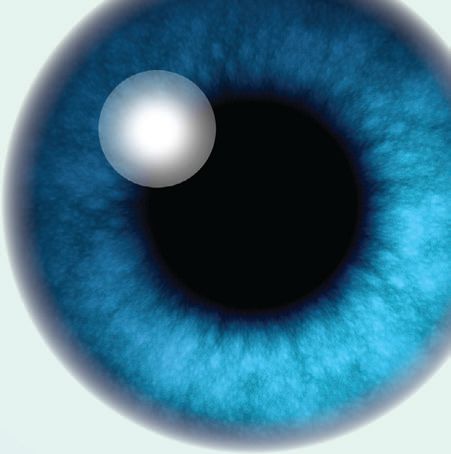
www.canstockphoto.com
IN SEPTEMBER DR. PHILIPPA CANN OF IMPERIAL COLLEGE IN LONDON, who also serves as an editorial board member of STLE’s affiliated journal
Tribology Letters, organized the first International Conference on Biotribology (ICoBT), which attracted luminaries from some 38 countries. In addition to the predictably large number of contributions on artificial and natural joints, a significant number of papers were presented concerning the growing areas of skin tribology and contact lenses.
Interestingly, while many of these studies were industrially sponsored, the results nevertheless were communicated to the scientific public.
Several of the contributors to ICoBT have recently published their presented work in
Tribology Letters. Notable among these is a comprehensive review (
1) on skin friction by Siegfried Derler of the Swiss Federal Laboratories for Materials Science and Technology in St. Gallen, Switzerland and Lutz Gerhard of the Technical University of Eindhoven, Netherlands.
Skin friction is of great practical importance for applications ranging from the design of sports clothing and swimming-pool walking surfaces to the avoidance of bedsores in long-term hospital patients. From the review, it is clear that skin friction displays enormous variation, even when taking into account the fact that skin is a highly nonlinear viscoelastic material. Much of the variation can be attributed to the degree of skin hydration, but overall it can be stated that the adhesion contribution to skin friction dominates over that from deformation. The review contains a valuable compilation of skin-friction data from many researchers, measured on several different areas of the body and against a wide variety of countersurfaces.
In the August 2010 TLT, we reported about efforts at the University of Florida to measure friction on corneal epithelial cells (
2). Two recent papers in Tribology Letters, again by the Florida group (
3), along with the group of Samuele Tosatti at the Swiss company SuSoS, together with their collaborators at the ETH Zurich (
4), have focused on the contact-lens countersurface. The friction of a contact lens against the eyelid is one of the central factors influencing comfort for the wearer, but contact lenses have proven to be a challenging area in which to conduct tribological research, partially because the contact pressures involved in the application are so low (3-5 kPa), and thus the availability of test equipment in this range has been limited until recently.
Test methods were central to the paper of the Tosatti group, who made efforts to ensure that both the countersurface and the test fluid were physiologically relevant. To this end, they employed a glass countersurface that had been modified first by hydrophobization and then by adsorption of mucin in order to mimic the inner surface of an eyelid. The lubricant solution, which was to mimic tears, consisted of a buffered salt solution containing human serum plus the protein lysozyme. Friction results on a number of commercially available contact lenses revealed that those containing the hydrophilic polymer poly(vinyl pyrrolidone) (PVP) showed the lowest friction coefficients (generally less than 0.05), while those without PVP showed µ values in the range of 0.1 to 0.6.
Scott Perry’s group at the University of Florida focused on surface composition (measured by x-ray photoelectron spectroscopy) and friction (measured by atomic force microscopy) of several contact lenses based on silicone hydrogels. Additionally, they investigated the effect of contact lens pretreatment in a solution of a poly (ethylene oxide)- poly (butylene oxide) (EO-BO) copolymer, which served as a model additive in a contact-lens storage solution.
Surface hydrophilicity is clearly of importance in imparting low friction to contact lenses. Of the three types of lenses examined, two were hydrophilic by virtue of a plasma-treatment step during their manufacturing process. The other lens was not plasma-treated but contained PVP as an internal wetting agent. As in the Tosatti study, the PVP-containing lens showed the lowest friction coefficient. Interestingly, only the plasma-treated lenses showed significant adsorption of the EO-BO copolymer at the lens surface, thus only these lenses showed any reduction in friction upon treatment with polymer. The results show not only that lens solutions can impact lubricity of lenses but also that the extent of this effect can depend on the type of lens employed.
Clearly contact lenses bring enormous benefits to millions of wearers, and any improvement in their effectiveness or comfort can be extremely valuable. The increasing desire of the lens manufacturers to sponsor basic research in understanding lens materials chemistry and tribology is a significant development, and their willingness to allow its publication in the public domain is to be applauded.
REFERENCES
1.
Derler, S. and Gerhardt, L.-C. (2012), “Tribology of Skin: Review and Analysis of Experimental Results for the Friction Coefficient of Human Skin,”
Tribology Letters,
45 (1), pp. 1-27.
2.
Tysoe, W.T. and Spencer, N.D. (2010), “Sliding on Cells,” TLT,
66 (8), p. 72.
3.
Huo, Y., Rudy, A., Wang, A., Ketelson, H. and Perry, S.S. (2012), “Impact of Ethylene Oxide Butylene Oxide Copolymers on the Composition and Friction of Silicone Hydrogel Surfaces,”
Tribology Letters,
45 (3), pp. 505-514.
4.
Roba, M., Duncan, E.G., Hill, G.A., Spencer, N.D. and Tosatti, S.G.P. (2011), “Friction Measurements on Contact Lenses in Their Operating Environment,”
Tribology Letters,
44 (3), pp. 387-397.
Eddy Tysoe is a Distinguished Professor of Physical Chemistry at the University of Wisconsin-Milwaukee. You can reach him at wtt@uwm.edu.
Nic Spencer is professor of surface science and technology at the ETH Zurich, Switzerland. Both serve as editors-in-chief of STLE-affiliated Tribology Letters journal. You can reach him at nspencer@ethz.ch.