Selecting the correct grinding wheels
R. David Whitby | TLT Worldwide March 2012
Use this five-step checklist to increase productivity.
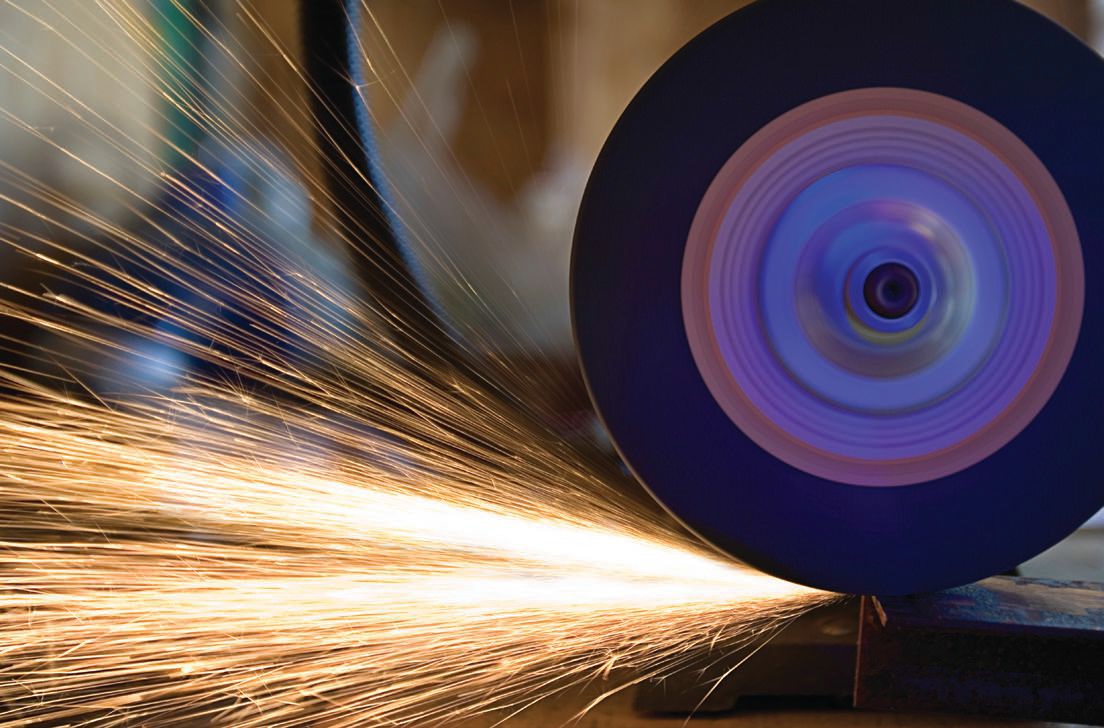
Using the right grinding wheel is paramount for success.
www.canstockphoto.com
SUCCESSFUL GRINDING REQUIRES SELECTING THE CORRECT GRINDING FLUID AND GRINDING WHEEL. Selecting the correct grinding wheel for a given application requires considerable experience or assistance from a trusted supplier. By choosing the right supplier, productivity will increase and profits will grow.
The six key attributes of a grinding wheel are:
•
Grit size
•
Grain formula
•
Resin
•
Coating
•
Dressing
•
Balancing.
There are three typical types of bonded abrasive wheels: vitrified, resinoid and rubber- bonded. Vitrified wheels are generally applied to tough materials such as high-alloy steel. Resinoid wheels tend to be less brittle and are preferred for heavy-duty steel and cast-iron applications. Rubber-bonded grinding wheels are used in a variety of operations: fine-finish, centerless and internal grinding. Perhaps the most important factor is abrasive type, with hardness ranging from standard green grit to CBN (cubic boron nitride) diamond.
Dynamic balancing of grinding wheels also is important. Schmitt has just released one of the smallest in-spindle balance heads available for automatic dynamic balancing of production grinding machines and highspeed spindles. As part of Schmitt’s SBS range, the internal balance head is designed for applications where space inside the grinding or machining spindle is limited. Applications include tool and cutter grinders with small spindles, cutting using super-abrasive or diamond wheels.
These machines often run direct-drive spindles with grinding wheel surface speeds above 100m/s. At this velocity, a perfectly balanced grinding wheel or toolholder assembly is essential. Even very small amounts of imbalance result in high centrifugal forces on the spindle, causing excessive machine vibration that can lead to poor surface finish, bad geometry, decreased dresser life and reduced spindle life. Excessive grinding wheel imbalance also can lead to shorter wheel life and higher costs, particularly when working with expensive CBN or diamond wheels.
Engis now offers customers the opportunity to have diamond and CBN grinding wheels designed and manufactured to suit specific applications. Electroplated tools incorporate a single layer of either diamond or CBN particles bonded to the tool surface by a nickel matrix. Engis’s electroplated bonding system, Electrogrip, allows manufacture of tools with a variety of forms and contours. These are used in many applications that require the grinding of deep forms such as splines, slots, gear teeth and other deep grooves.
Saint-Gobain Abrasives has created a five-item checklist to assist production engineers.
1.
Matching wheel speed to tool speed is critical. The safe operating speed of a wheel should never be exceeded.
2.
The tool’s mounting systems should always be matched to the system required by the wheel. Never use flanges that are undersized or the wrong type. If the wheel does not fit on the tool without alterations, then it may be the wrong wheel for the tool.
3.
A grinding tool must not be used without a wheel guard.
4.
A wheel should not be borrowed from another job. The perfect wheel for one job type may be disastrous on another.
5.
Wheel shape (type), grit size, abrasive, grade (bonding-holding-strength), wheel structure (space) and bond for the job all affect a wheel’s strength and safe operating speed.
Saint-Gobain’s latest innovation, Norton Quantum, is a patented ceramic grain combined with innovative bond technology developed to enhance grain performance. The bond is designed to optimize grain-to-bond adhesion, which improves grain retention and allows maximum benefits to be gained from the grain. This provides an optimized balance between sharpness (free cutting) and toughness (wheel life).
According to Saint-Gobain, Norton Quantum grinds with lower force, which reduces distortion and metallurgical damage of the workpiece when grinding. This, combined with the improved form-holding of the new bond technology, leads to high-part quality and lower reject levels. Also, Quantum grinds with lower power, allowing for higher material removal rates typically 30% to 50%, while the new bond technology allows for speeds up to 100m/s, further reducing cycle times.
For each application, using the right grinding wheel is paramount for successful grinding.
David Whitby is chief executive of Pathmaster Marketing Ltd. in Surrey, England. You can reach him at pathmaster.marketing@yahoo.co.uk.