Basic lubricant identification in the field
Stacy Heston | TLT Best Practices January 2012
This step-by-step plan reduces the chances of mixing incompatible products.
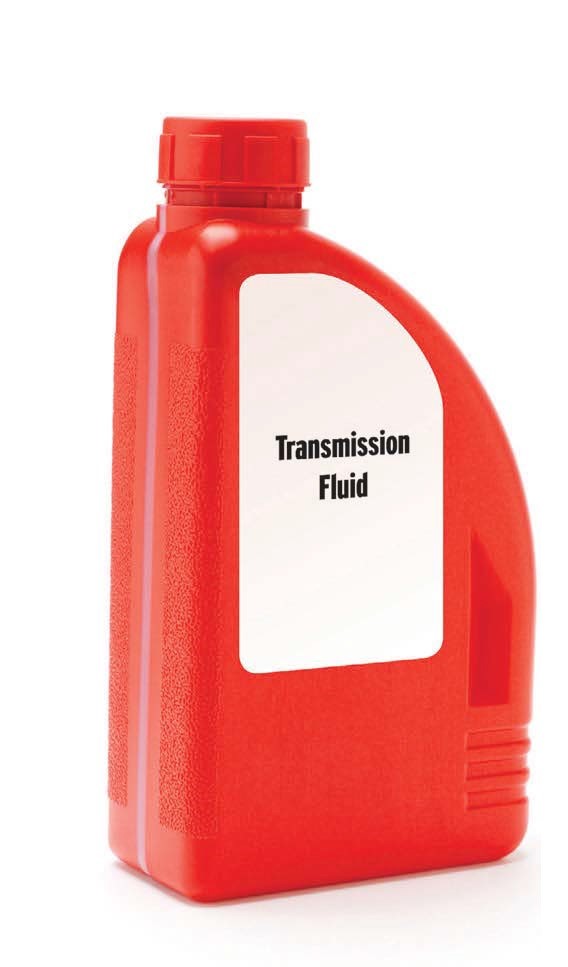
www.canstockphoto.com
KEY CONCEPTS
•
Four key characteristics are used in developing a lubricant-identification system.
•
Viscosity for any given component is selected based on speed, load and operating temperature.
•
Using a color-coded system is an efficient way to identify lubricants on site.
IDENTIFYING LUBRICANTS IN THE FIELD, from determining the method for identification to the physical tasks of installing the identifiers on the components, can be a daunting task. In addition, any identification system has to be complex enough to individually identify lubricant requirements and ensure that incompatible or incorrect lubricants are not introduced into a component. The level of complexity depends on the number and types of lubricant on site.
In one plant, for example, there were approximately eight identified oils on site. Two of these were used as gear oils. This site identifies lubricants by type and color codes them.
The identified gear oils are color coded red; however, one is an ISO 460 antiwear gear oil and the other an ISO 68 rust and oxidation gear oil. These two gear oils have different applications, and their additives packages are potentially incompatible. This single level of lubricant identification increases the possibility of cross contamination or the installation of the improper lubricant if a lubricant technician were to grab the wrong red container.
Let’s examine key properties that should be identified and their importance to the overall lubrication program.
Lubricant formulators look at several different types of tests and specifications when designing a lubricant in order to ensure basic properties inherent to a lubricant type are met, such as the 4-Ball Wear Test, Foam Sequence or Copper Strip Corrosion. While these are important properties for a lubricant, they are not commonly used to select a lubricant for an application or to identify it. Key properties for lubricant selection and identification begin with:
1.
Lubricant type
2.
Viscosity
3.
Base oil type
4.
Additive package.
For greases, the thickener type also should be considered.
These four characteristics should be reviewed for each lubricant on site as they act as the starting point for identifying lubricants in the field to ensure incompatible lubricants are not installed. If duplications in lubricant information exist, then a consolidation of lubricants may be necessary.
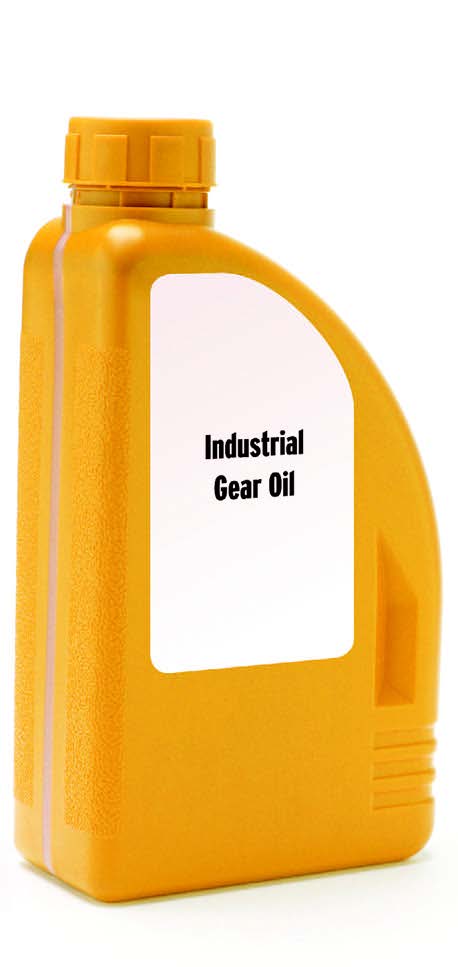
www.canstockphoto.com
VISCOSITY
Viscosity is generally defined as a lubricant’s resistance to flow and is categorized into absolute and kinematic. For selection purposes, the kinematic viscosity using ASTM D445 provides the lubricant’s resistance to flow under gravity.
Flow under gravity is important during the operation of a component as the component’s speed affects the required viscosity. If the ISO classification is not reported on the lubricant’s product data sheet, look for the viscosity reported in centistokes (cSt) at 100 C for automotive lubricants or 40 C for industrial lubricants.
Viscosity for any given component should be selected based on speed, load and operating temperature. These four factors affect the formation of the lubricant film. If the viscosity is inadequate for the operating circumstances due to lubricant mixing, the component may experience a lubricant film that is too thin, causing metal-to-metal contact, or a film that is too thick, causing overheating.
General rules of thumb: the slower the speed, the higher the viscosity requirement; the heavier the load, the higher the viscosity requirement. Specific viscosity requirements should be calculated using appropriate techniques for the component type.
ADDITIVES
Additive packages are another primary concern when identifying lubricants in the field. Of the many additives that are used to formulate lubricants, the additives identified specifically with the lubricant type or names are the ones to pay close attention to: antiwear, rust and corrosion inhibitors and extreme pressure.
The three additive types are designed to be adsorptive or chemically reactive with the component surfaces, meaning they form protective layers on the component surfaces. Unlike other lubricant property additives, such as pour point depressants or viscosity index improvers, these additives do not impart lubricant properties
per se, but, rather, they are heterogeneous and separate from the oil to form films on the surface due to the polarity and reactivity of the molecules.
Rust and corrosion inhibitors typically adhere to a surface to impede contact of water or the environment with the component surfaces. These additives can be oil- or water-soluble with the amount of rust and corrosion prevention dependent on the interaction between the adsorbed film, oxygen in the system, heat and mechanical processes.
Antiwear additives also are adsorbed to component surfaces and are activated by temperature. Zinc dithiophosphates are the most commonly used antiwear additives and have oxidation inhibitor and corrosion inhibitor properties. However, the primary function is antiwear, and this limits the compatibility with rust and oxidation inhibitors which are typically sulfonates or oxidates.
Extreme pressure additives perform the same general function as antiwear additives but operate under a high load. These additives are activated by high temperature in conjunction with high pressure. Extreme pressure and antiwear additives are designed to provide protection from adhesive wear during the boundary and mixed film phases of lubrication during component operation. Typical extreme pressure additives include disulfides, polysulfides, phosphites and phosphoric acids.
Mixing lubricants that are designated as antiwear, extreme pressure or rust and oxidation lubricants can cause issues with the adsorption of the films. While most lubricants exhibit all of these properties, the chemistry used to achieve them is different based on the designation. The adsorptive films do not form during the initial introduction of oil but build up over time. When a conflicting film type is introduced into a system, it interferes with current film and begins creating a new film type that may not meet the needs of the application. For component applications where specific films are required, mixing of lubricant additive packages can have disastrous effects.
Table 1.
BASE OIL
Base oil is the foundation of a lubricant making up approximately 70%- 99% of the final product. It dictates the fluid’s viscosity and the specific formulation of additives or inhibitors that can be used. There are three general types of base oil groups: mineral, synthesized hydrocarbons and synthetics. Compatibility of the base oils focuses on the molecular structure that makes up these fluids.
Mineral oils are further broken down into API Group I, II and III, but these base oils are generally compatible. The variation in the groups revolves around the specific refining process used, as well as the general molecular chemistry. In some cases, Group III base oils are considered synthesized hydrocarbons due to the hydrocracking process to which these oils are exposed.
Synthesized hydrocarbon, or API Group IV, base oils are derived from crude oils and have a consistent molecular structure that imparts properties of shear strength, oxidation stability, high viscosity index, etc., that exceeds that of a typical mineral oil. Common Group IV base oils include polyalphaolephins (PAO) and alkylated aromatics whose basic molecular structure mimics that of a mineral oil. These base oils are generally compatible with mineral base oils.
Synthetic base oils, or Group V, are more variable in their content and are derived from a variety of compounds, organic acids (in the case of esters) and ethylene and propylene oxides (in the case of polyglycols). These compounds lead to molecular structures not necessarily seen in the other API groups. General compatibility guidelines exist for these fluids. However, it is important to verify the compatibility of specific products because of the chemical variability within Group V and with the other groups. Group V synthetic base oils include esters, polyglycols and phosphate esters.
Within the ester category are diesters and polyol esters. These base oils are typically seen in compressor and jet engine oils, with polyol esters commonly used in refrigeration applications. Esters are compatible with mineral base oils, but polyol esters may react with component seals and coatings. Although mixing an ester with a mineral oil may not cause an issue with the oil, a risk of component seal damage could result. If various base oils are in use for compressors, the base oil should be identified.
Polyglycols are commonly used in hydraulic fluids, as well as gear and bearing oils, but lack compatibility with mineral base oils and the additives compounds used in mineral base oils. This base oil type is common in applications where a high flash point is required. Phosphate esters are known for their fire resistance and typically are used in hydraulic systems and turbine lubrication systems. Their compatibility to mineral base oils varies, but they lack miscibility (
see Table 2).
Table 2.
DEVELOPING A PLAN
Once lubricants have been identified by lubricant type, viscosity, base oil type and additives, a system for identifying lubricants required for a component needs to be developed. Some approaches include the use of shapes, colors and/or text to identify the required lubricant characteristics for the component. Identifying lubricants on a component by product name should be avoided to minimize confusion if lubricant suppliers should change. General lubricant requirements for a component do not change.
For a site with a complex number of lubricants, the following outlines an approach that utilizes color coding and text.
COLOR CODING
Color coding is an efficient way to initially identify the lubricants on site. In cases where a site has a small number of lubricants, identification can stop with color coding. Table 3 outlines some basic color associations.
Table 3.
TEXT IDENTIFICATION
Text identification is necessary for characteristics with multiple options that may be too cumbersome to identify with color, shapes, symbols, etc. Viscosity, base oil type and, in some instances, additives fall into that category.
Viscosity identification is straight forward—the ISO classification or other standard classification as determined by the specific fluid type should be expressed in text form. For example: 22, 32, 46, 100 or 220 for ISO; 10W, 20W or 30W for SAE engine oils; or 80W, 85W or 90W for SAE gear oils.
Base oil types should be identified using an abbreviated nomenclature that is clear and concise for the lubricants on site. Table 4 outlines some basic and common abbreviations for base oil types.
Table 4.
Additive identification is best identified with test, as well. Although there are three general additives that should be identified, additional additives might require identification in specialized instances. As was mentioned earlier, rust and corrosion, antiwear and extreme pressure should be identified as a minimum. However, additional additives or performance properties might require identification to prevent specialized lubricants from being used in situations where they exceed the requirements for a component and are not economical for use.
DECAL SHAPES
Although not explicitly outlined, decal shapes can add an additional layer of identification, especially to distinguish between grease and oil. Shapes also can provide a different approach from distinguishing between oils that are otherwise similar except for one key characteristic such as food grade versus non-food grade.
PUTTING IT TOGETHER
Once the four main characteristics of a lubricant (lubricant type, viscosity, base oil type and additives) have been identified for all lubricants on site, the development of the coding system can begin. The amount of specifics required varies from plant to plant based on the number of lubricants. In large organizations with multiple plant sites, it may be advantageous to develop such a coding system at the corporate level and, in turn, develop a single-source lubricant supplier.
Once lubricant information has been gathered to identify the lubricants, color codes need to be assigned based on lubricant type. If no overlap of color exists, then the development of the lubricant-identification system for the site can stop here. If multiple lubricants share a color assignment, then additional information must be included.
After lubricant type color coding has been assigned, viscosity should be identified in the form of text identification on a color-designated decal. At this point, the code needs to be reviewed to identify duplications. If multiple lubricants share a color assignment and viscosity, then further identification will be required.
Table 5.
*ISO standard 12922 Lubricants, Industrial Oils and Related Products (Class L) – Family H (Hydraulic Systems) – Specifications for Categories HFAE, HFAS, HFB, HFC, HFDR and HFDU provides abbreviation for further differentiation between fire-resistant hydraulic fluids, if required. Otherwise, it is recommended to keep with simplified abbreviations to limit the possibility of confusion.
Next, add in the appropriate designation for the base oil type. If no differentiation is provided through this step because all lubricants are mineral-based, then this step can be skipped. However, if any differentiation is provided, regardless of lubricant type, then the inclusion of the base oil type should be done for all lubricants.
Finally, additives and properties should be added to the coding. Although the coding should be kept to a minimum, specific additives or property requirements should be included to ensure that required characteristics are made known. This concept also applies to the identification of the base oil type. If a particular hydraulic system requires a zinc-free fluid but it is the only hydraulic fluid on site, the zinc-free notation should be included to minimize risk of a zinc-additized lubricant from being used later. Similarly, if a particular base oil type such as a PAO is required due to operating conditions, it should be identified (
see Figure 1).
Figure 1.
CONCLUSION
Understanding the minimum characteristics and why they should be identified is the first step in the development of a lubricant-identification system. Identifying these key characteristics minimizes the possibility of cross contamination with incompatible or improper lubricants. The level of identification should be customized to reflect the needs of the site. However, the more detail provided, the less risk of losing key performance and lubricant property requirements as time goes on.
Stacy Heston is a lubrication subject matter expert and provides reliability-centered lubrication program development services and training to a wide variety of customers. Among her professional credentials are STLE’s CLS and OMA I certifications and the International Council of Machine Lubrication’s Machinery Lubrication Technician I & II certifications. You can reach her at heston.stacy@gmail.com.