The Lubrizol Corporation
Longer Life Grease
Extending Re-Greasing Intervals and Improving High Temperature Protection
By Ping Zhu, PhD, Global Grease Commercial Manager, The Lubrizol Corporation | TLT CMF Plus November 2011
Now is the right time for longer life lubricating greases. In today’s economic climate, equipment owners and operators are looking for options to optimize performance while reducing maintenance costs. Those drivers, coupled with extended re-greasing intervals, the introduction of ‘greased for life’ bearings and the increasing use of automated greasing systems have created an even greater demand for premium longer life greases that provide superior performance under higher operating temperature and load conditions.
Lubricating grease is a critical design component in the lubrication of rolling element bearings for both industrial and automotive applications. Formulating grease to extend its useful life requires careful choices in terms of base oil, thickener and a properly balanced additive package. Lubrizol’s premium, multifunction grease additive, Lubrizol® 5288, has been proven to provide longer bearing life, while minimizing bearing wear, even in high temperature applications.
Building a Longer Life Grease
Developing the optimum long life grease requires a careful selection of three essential elements: base oils and thickener (which are combined to form base grease), and the additive package. The temperature, speed, and load conditions under which the grease will function are a key consideration in base oil selection. Bright stock or viscosity modifiers are frequently used to increase base oil viscosities to target blend oil viscosity range. Thickener structure and content must also be taken into account, with thickeners ranging from soap-based to non-soaps such as urea derivatives.
The final ingredient in the long life grease formulation is the additive package, which again requires careful consideration. Extending grease life is a delicate balancing act that must take into account the interaction of additives, with both synergistic and antagonistic effects considered. An example of this interconnectedness is the role of antiwear additives and antioxidants. Without proper antiwear protection, wear occurs. The debris caused by wear acts as a catalyst to induce degradation of the grease and thereby compromises oxidation stability. On the other hand, without oxidation protection, the grease will prematurely oxidize, leading to the formation of sludge and deposits, which can be abrasive and cause wear and reduce bearing performance. Unless these and other performance characteristics are balanced within the formulation, the resulting end product will fail prematurely.
In today’s global market, a grease’s environmental acceptance is also a high priority. Greases designed to extend bearing life offer the advantages of reduced grease consumption and waste, less frequent re-greasing and lower environmental impact. In addition, by choosing additives that are less harmful to the environment, the hazard-risk phrase of finished grease can be minimized with minimal compromise of performance. The resulting products can offer improved environmental acceptance, which is a valuable market differentiator.
Developing the Right Formulation
Great additive formulations don’t just happen. While the components of the package are critical, they are not the only factor. Formulating expertise, testing capability, failure analysis and a strong foundation in tribology are all essential ingredients in the formulation of Lubrizol 5288.
However, formulation does start with the components. The building blocks of Lubrizol 5288 were chosen carefully. We considered factors such as the compatibility of individual additives with the base grease and with each other, compatibility of the additives with seal materials, the thermal stability of the additive at anticipated operating temperatures, and sometimes, even color and odor. The storage stability of the additive package was also important to consider to meet the needs of both suppliers and customers. And, of course, global chemical registration status and environmental and human risk of the additives were an integral part of the process in the selection of the components. Lubrizol 5288 was designed to be in compliance with global chemical regulations and not to trigger EU risk phrase labeling of the finished grease, when used at the recommended treat rate.
The development of Lubrizol 5288 required repeated testing using different component options and treatment ratios. It was here that the expertise of Lubrizol’s formulators proved its true value. Decades of formulating experience combined with a deep knowledge of statistical design of experiments (DOE) enabled Lubrizol to streamline and optimize potential formulations.
Testing Validates Performance
Lubrizol 5288 treated greases were tested according to the ASTM D4950 NLGI GC-LB standard, Results showed that in suitable base greases, the Lubrizol 5288 additive package meets or exceeds the NLGI GC-LB automotive service grease specification (
See Chart 1) providing grease manufacturers with a reliable solution for producing greases with excellent thermal stability, oxidative resistance and protection against wear, rust and corrosion.
Chart 1: GC-LB Test Summary of Grease Additized with Lubrizol 5288. Lubrizol 5288’s performance exceeded the requirements of the GC-LB specification for the highest performance under a wide temperature range for an automotive wheel bearing and chassis lubricant.
Lubrizol 5288’s performance was confirmed in industry standard bearing tests, including the DIN FE9 High Temperature Bearing Grease Oxidation Life Test (
Chart 2) and the DIN FE8 Bearing Wear Test (
Charts 3 and 4). Both bearing tests were run under accelerated conditions to mimic real-world bearing performance in a shorter time. For FE-8 wear test, two sets of operating conditions were chosen to demonstrate the speed and load conditions typically seen in both automotive and industrial applications.
Chart 2: FE9 High Temperature Bearing Grease Oxidation Life Test: The performance of a grease in the FE9 test rig is a measure of high temperature thermal and oxidative stability. Lubrizol 5288 met and exceeded test requirements.
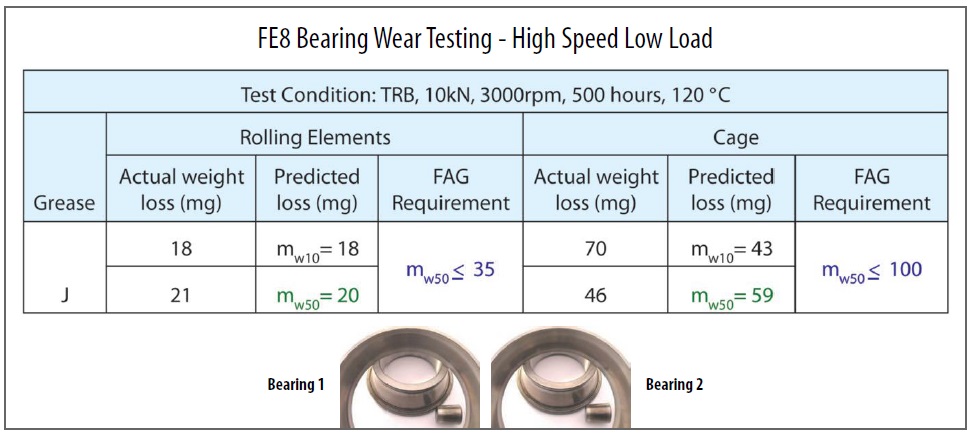
Chart 3: FE8 Bearing Wear Testing – High speed/low load conditions. This test is used to measure temperature, torque and wear in automotive service applications. Lubrizol 5288 met and exceeded test requirements.
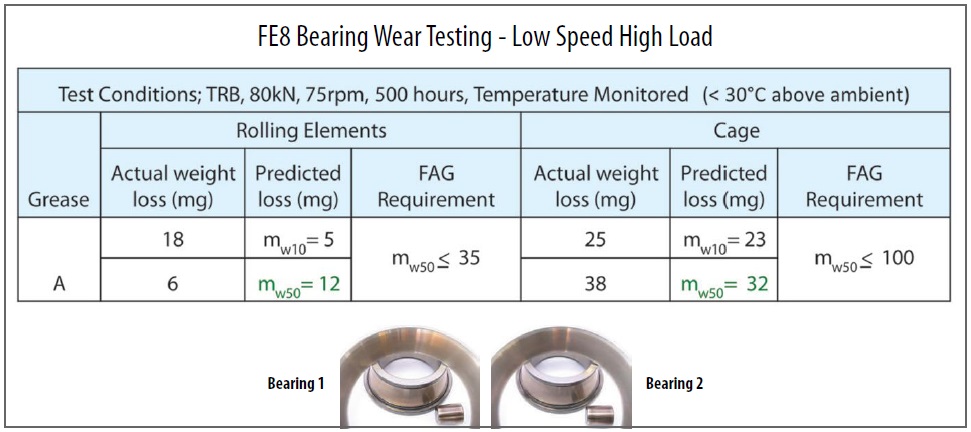
Chart 4: FE8 Bearing Wear Testing – Low speed/high load conditions. This test is used to measure temperature, torque and wear in industrial applications. Lubrizol 5288 met and exceeded test requirements.
A Premium, Multi-Functional Additive Package for Long Grease Life
Lubrizol’s new multifunctional additive package was specifically designed and formulated to improve grease life.
Compatible with lithium, lithium complex and urea thickened greases, it has been proven to meet or exceed key industry specifications. Available globally, it is in compliance with global chemical regulations and does not trigger risk phrase labeling on the finished grease.
The new additive package creates value for end users by extending grease service life with potentially longer re-greasing intervals as well as improved bearing life, reduced downtime and lower overall maintenance costs. Lubrizol 5288 can benefit the environment through the use of less harmful chemistry and reduced grease consumption and waste.