What challenges does the bearing global supply chain present to you?
TLT Sounding Board October 2011
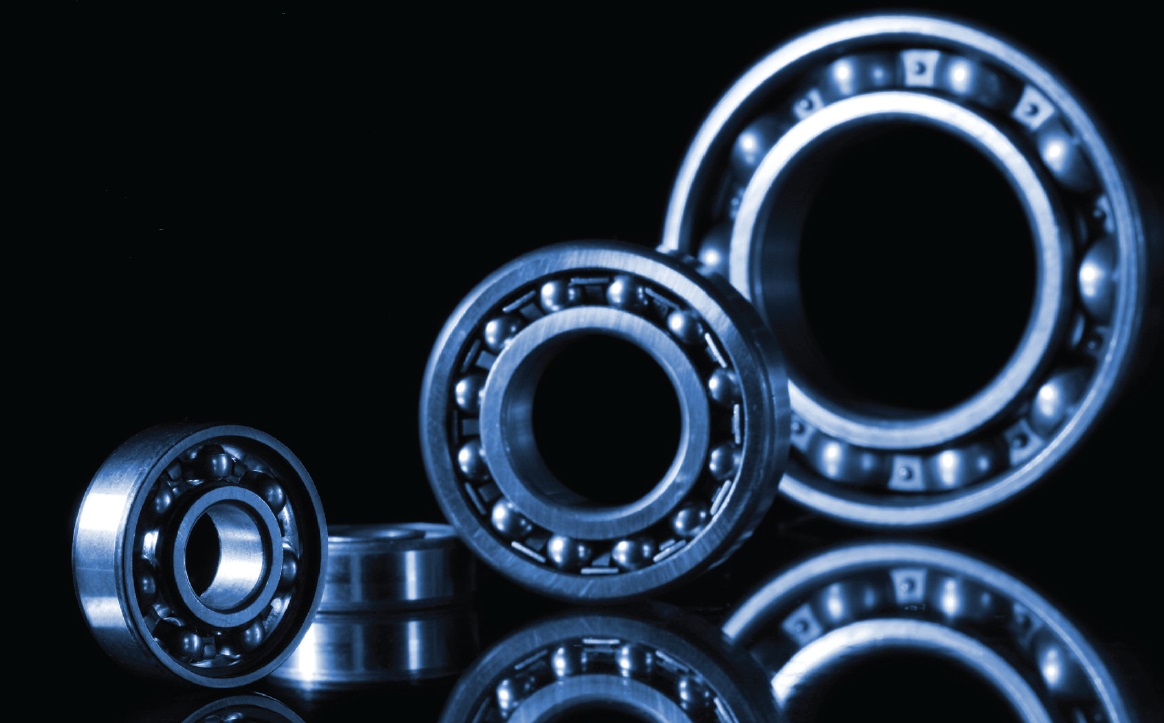
www.canstockphoto.com
Lack of availability, keeping prices low for customers and insufficient predictive tools topped the list of reader challenges when it comes to acquiring bearings on a worldwide basis. Another frequently mentioned challenge was lack of detailed instruction on how to lubricate the bearing. Long lead times, particularly for specialty-environment bearings, remains an issue. And many readers commented on inconsistency when it comes to specifications and quality for bearings with multiple global manufacturing locations. “The quality of manufacturing varies with the location,” noted one reader.
Availability of quality bearings.
Keeping prices lower for our clients and ensuring that they are getting the best quality without paying too much.
Lower prices.
Not enough detailed information on the bearings offered in regard to lubrication.
Bearing performance predictive tools.
Serious differences in bearing quality depending on where the factory is located.
None. I have an abundance of bearings in my desk drawer. It’s a lifetime supply!
Maintaining consistent quality and reliable delivery, particularly when the same bearings are manufactured in multiple continents.
Larger double-row spherical bearings have a delivery time greater than weeks.
Ability to meet customer expectations. Ability to obtain “qualified” test bearing for lubricant testing.
Use of new high-quality materials.
What is your greatest frustration with bearings over the past year?
Cost
10%
Quality/performance
31%
Availability
36%
Technical support
26%
Availability of test data
31%
Other
17%
Based on results from some 13,000 TLT readers. Total exceeds 100% because some readers chose more than one answer.
Defense Federal Acquisition Regulations (DFAR). Quality of steel.
Cost of bearings for lab tests.
Key element in a large field of machineries and applications.
It seems like lead time is a major issue for a lot of mechanical components, especially highly engineered products from Europe.
Reduced cost at the expense of quality and in some cases delivery time.
Performance evaluation and providing technical support.
Increasing product cost and shifting manufacturing to various locations.
Lack of high-level input and teamwork regarding bearing lubrication.
Availability of bearings for special environments (e.g., vacuum, dry atmosphere).
Having quality bearings available at all times. Also to keep the cost of bearing supply acceptable.
Assuring that we are receiving high-quality bearings, not counterfeit ones.
Opportunity to sell grease.
Bearing manufacturers resourcing to Asia after approval of domestic production.
Complete re-testing is then necessary.
Long lead times for specialty (low-volume bearings). Potential differences between sources due to insufficient standards.
Availability, availability and availability!
The technical support and the diffusion of the marks.
Stock outages of some bearing types and sizes due to high demand in other parts of the world.
What form of testing is most important for proper bearing qualification?
Dimension/Material inspection
37%
Lab endurance testing
23%
Field testing
58%
Software modeling
7%
Other
14%
Based on results from some 13,000 TLT readers. Total exceeds 100% because some readers chose more than one answer.
What testing would or do you perform to improve your understanding about quality of bearings from the global supply chain?
Advance protective coatings.
Diamond-like carbon coatings have promise to achieve both hardness and low friction.
Solid materials.
Antibacterial-coated, steel, polymer replacement of hex chrome sealers. Application techniques and surface preparation.
Waiting on a five-year rust preventive for machined parts that are easily washed off.
Magnetron-sputtered coatings. Vacuum sputtering and ion-plating electrophoresis.
Ultra-thin coatings.
Cross-lined polymer.
Diamond-like carbon and microsurface texturing.
Nanoadditives.
New boriding treatments, low-temperature, super-carburization treatments for steels, new durable coatings for rolling element bearings.
Diamond-like carbon, laser texturing, isotrophic superfinishing.
Nanotechnologies.
Laser surface texturing technology.
Nanocomposite metal carbide reinforced amorphous hydrocarbon.
Superfinishing to improve efficiency.
Plasma and HVOF.
We are working in physical vapor deposition coatings, plasma electroxidation, nitruration, solgel coatings, laser cladding.
We are in that business, and you don’t have enough space to address all of the coatings, materials science and surface treatment technologies that are emerging.
Polymer ceramic coatings, molybdenum and boride lubricant-less coatings.
Self-lubricating hard coatings, textured surfaces exhibiting microlubrication effect, superlubricity additives, biomimetic coatings, triboconditioning.
Editor’s Note: Sounding Board is based on an e-mail survey of 13,000 TLT readers. Views expressed are those of the respondents and do not reflect the opinions of the Society of Tribologists and Lubrication Engineers. STLE does not vouch for the technical accuracy of opinions expressed in Sounding Board, nor does inclusion of a comment represent an endorsement of the technology by STLE.