A positive attitude
Peter A. Oglevie | TLT President's Report October 2011
Along with improved culture come higher quality product, increased work flow and cost savings.
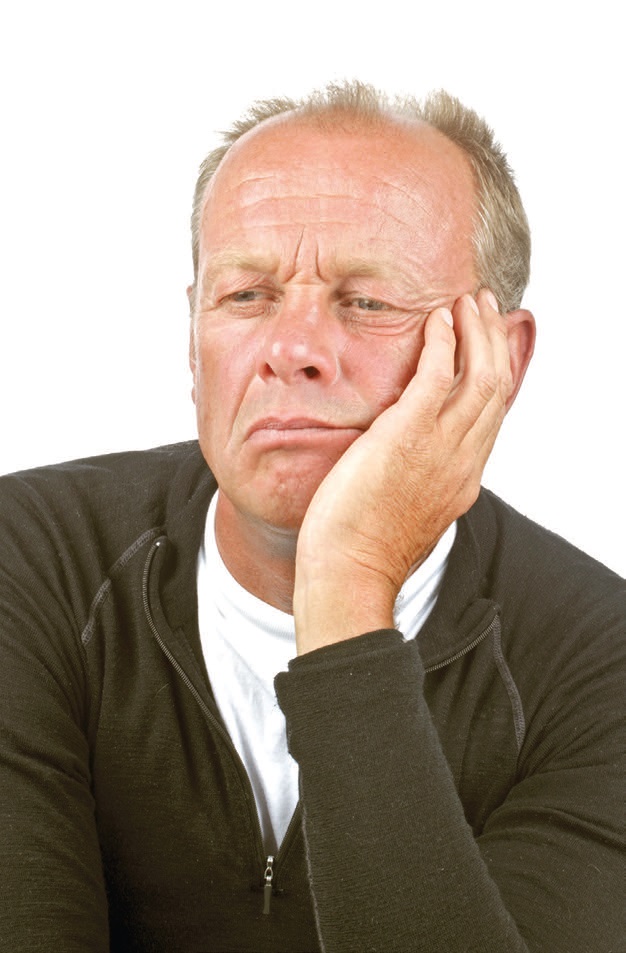
An indifferent attitude on the shop floor can lead to poor production and shortened tool life.
www.canstockphoto.com
YOUR ATTITUDE IS EVERYTHING. I just lost Elsie, a dear friend and tenant. Elsie was 93 years old. She was one of those people who always made the best of what she had and made those around her happy. She had a positive attitude. Even when she was giving me the riot act she could diffuse the sting with a smile. Elsie was the perfect tenant—she treated her apartment as if she owned it. Like her, it was always neat and clean.
I have worked on the shop floor in places where this is not the case. I remember working with a company to replace oil-based stamping lubricant with a new water-based lubricant. When I first met the operator at the press, he told me straight out, “This test is going to fail.” I observed the machine and found oil dry build-up on the floor. The press was covered in oil, and the operator was so used to the mess he didn’t even notice.
I decided to work on the attitude problem as I cleaned the press. I got my shop coat on and began asking questions while I was cleaning. How do you get your clothes clean after working here all day? How often do you replace your shoes? Do you honestly like this smell? These questions opened his mind to what we could do for him, not just his company.
Once the press was cleaned, the operator was amazed at how nice his machine looked and became aware of the pigpen he had been working in. As I was introducing the new water-miscible lubricant, I intentionally spilled a little on the floor. The operator, like Elsie, read me the riot act for messing up his clean floor. I knew I had him. I pulled the mop bucket out and cleaned up the mess in a few seconds.
By this time I was making a friend out of a foe. All I had to do was perform the work. For this I had some new equipment up my sleeve.
I introduced the operator to an airless spray system. He immediately took me to the back room where three such machines sat in idle disrepair. “These machines don’t work, we tried them,” he said. I asked him to keep an open mind. It might be improper training and use, not the machine, that is the problem.
I took out a calculator and asked the operator the size of the part. We used a work piece formula to apply .001 inches per side of the strip stock. This gave us a volume output for the airless spray system to get us started. We set the pump volume to this amount, bleeding all of the air from the system. The machine produced a perfect spray pattern. My new friend was beginning to smile, and his attitude was now one of “we can do this.”
We fired up the press. I gave the die a quick spray with the lubricant and asked him to run the press in stroke mode to check the location of the spray nozzles. They were fine, so I asked him to set it to automatic mode. The press ran, the spray worked and we made good parts. More important, very little lubricant made its way onto the floor or the machine.
I visited the operator a few weeks later to follow up. He smiled and commented on a few minor points. We took care of them. I asked about his clothes, shoes, etc. His answers and attitude were positive. His machine was neat and clean, and I could not find any oil dry within its perimeter. This I am sure helped his tool life. His fellow operators were asking when they could get into the act.
In the end this test saved the company money and along the way improved an entire shop floor’s attitude. It was their shop. I never again saw oil dry on the floor or oil on the presses, which were neat and clean. Maybe not as clean as Elsie’s floor, but she did not use as much oil for cooking either.
I will miss Elsie, a positive woman with a positive attitude. You would, too.
Pete Oglevie is president of International Production Technologies in Port Washington, Wis. You can reach him at poglevie@wi.rr.com.