20 Minutes With Bridget Crocker
Karl M. Phipps, Managing Editor | TLT 20 Minutes September 2011
This product-development specialist explains how to maximize the benefits of additives while reducing the costs to operate them.
BRIDGET CROCKET - The Quick File
WORK EXPERIENCE
• Technical manager in the Metal Processing Specialties Division at PCC-Chemax, Inc., Piedmont, S.C., where she has worked for three years. Responsible for new-product development; functional testing of current additives; technical service, including finished fluid formation recommendations; and support for customers and sales representatives.
• Began metalworking fluids career working with John (Jack) Kimes and Harish Patel in 1994 at Gateway Additive Co. in Spartanburg, S.C. as the company’s first laboratory technician. After two years, she was promoted to senior formulating chemist working with soluble oil and semisynthetic base additives, as well as corrosion inhibitors. In 1997 Gateway Additive was acquired by The Lubrizol Corp.
• Spent 11 years with The Lubrizol Corp. in Spartanburg, S.C., as a research and development chemist. Primarily worked with soluble and semisynthetic base additives but was promoted to technical service chemist working with finished fluid formations for end-users.
EDUCATION
• Bachelor’s of Science, business management (with an emphasis on sales and marketing) – Kaplan University, Fort Lauderdale, Fla.
• Associate’s degree in science, chemistry – Spartanburg Community College, Spartanburg, S.C.
PROFESSIONAL AFFILIATIONS
• STLE (member since 1999)
• STLE Carolinas Section
• Independent Lubricant Manufacturers Association
• Society of Manufacturing Engineers
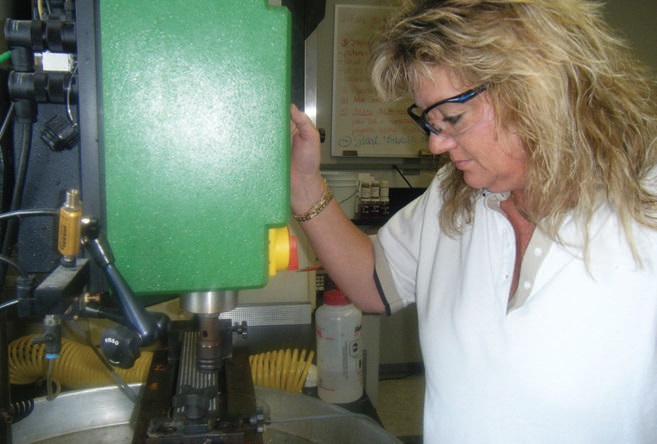
Bridget Crocker
TLT: IN THIS ECONOMIC CLIMATE, HAVE YOU SEEN A PUSH FROM MWF MANUFACTURERS TO TRY TO GET MORE OUT OF THEIR PRODUCTS?
Crocker: Absolutely. MWF manufacturers have always focused on optimizing machine performance, but in today’s economy we’ve seen an insistent push by additive companies to optimize their profits by reducing their manufacturing costs. However, when that cost is associated with machining parts, the first step is to look at the finished fluid that is being used. In fact, some companies will even change to a higher cost fluid in the hope that it will save them more money in the long run.
These fluids are more robust so more parts can be made per shift. They also exhibit longer sump life so fewer clean-outs are needed, and concentration of the coolant can be used at lower amounts, among other attributes.
TLT: WHAT ARE SOME WAYS THAT ADDITIVES HELP TO IMPROVE THE ECONOMICS OF A FORMULATION?
Crocker: Additives can be advantageous to improving the economics of a formulation. A good example is chlorinated-paraffin replacement esters. Some of its economic advantages include (1.) lowering high disposal cost of chlorine during wastewater treatment, (2.) less to no high rework, (3.) scrap cost due to flash rusting on parts because of chlorine and (4.) lowering the cost of energy to clean excessive chlorine containing fluids off parts.
In addition, these esters along with in-process rust preventatives are capable of inhibiting corrosion on parts during storage and transit due to the thin film they deposit on the parts. This is opposite to chlorine containing fluids, which can cause high corrosion rates. Using these chemistries, flash rusting can be eliminated.
TLT: IS IT DIFFICULT TO CONVINCE CUSTOMERS THAT A HIGHER-PRICED MATERIAL CAN BE USED AT A LOWER USE LEVEL, THEREFORE ACTUALLY REDUCING THE OVERALL COST OF THEIR PRODUCT?
Crocker: Yes, it can be quite difficult to convince some that higher-cost materials can actually reduce the overall cost of a product by maintaining equal or better performance. Additive manufacturers must demonstrate to their customers the advantages of moving toward such a material.
For example, PCC Chemax has some materials in the rust-preventative segment that can be used as little as 10% in a finished formulation because they are 100% active, whereas other materials for rust prevention have to be used anywhere from 50% to 100% in a formulation because they have oil and solvent as fillers in them (
see photos).
Today, additive manufacturers will really be doing themselves a favor by showing their customers that with improved performance attributes, they can more likely better evaluate their products and, in doing so, crunch raw material cost. As a result, what they find is that the costs are the same or in some cases less than the current formulation.
In the case of the rust preventatives developed by PCC Chemax, which are 100% active, end-users find the added costs gives them more flexibility because of changes in the viscosity of the base oil and/or flash point of the solvent being used.
You can reach Bridget Crocker at bcrocker@pcc-chemax.com.