Energy-efficient automobiles
R. David Whitby | TLT Worldwide July 2011
Manufacturers are using lightweight materials to build more fuel-efficient vehicles.
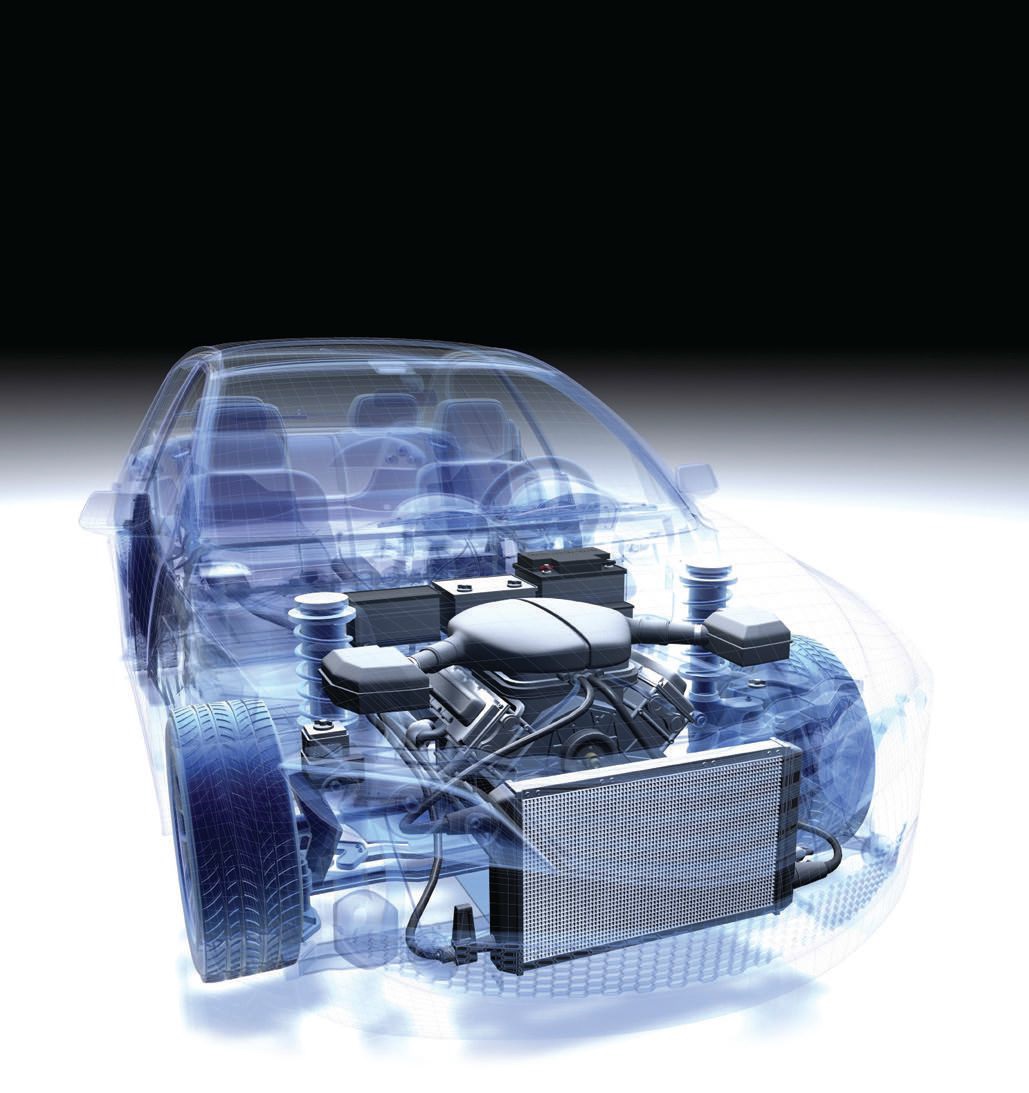
www.canstockphoto.com
Using low-weight steel for automobiles (e.g., saving vehicle weight) is one method for increasing energy efficiency, though there are other methods being developed by manufacturers and suppliers.
If you wanted to expend the least amount of energy when walking somewhere, you wouldn’t carry a backpack full of rocks. Similarly, to improve a car’s energy efficiency, getting rid of extra weight helps.
From a physics perspective, the loads on a passenger car are the force needed to accelerate vehicle weight when driving uphill, rolling resistance, aerodynamic resistance, internal resistance and to generate power for auxiliaries. The first three are proportional to vehicle weight and establish a strong relationship between weight and energy consumption. However, the energy consumed by a vehicle is also determined by its performance characteristics such as maximum power, top speed and aerodynamics. Consequently, it is possible for two cars with similar weights to differ significantly with regard to energy efficiency.
The input energy in the gasoline or diesel fuel that powers a conventional vehicle is dissipated in numerous ways. A recent GM analysis found that for a typical car, 32.4% of the fuel’s energy is lost in the hot exhaust gases, 28.4% is used in cooling, braking and coasting accounts for 7.4% and vehicle aerodynamics accounts for 5.9%. Another 7.4% is lost in engine friction, transmission friction accounts for 2.9% and the auto’s various accessories (air conditioning, electric windows, radios, CD players, etc.) use 3.9%. Only 11.8% of the input energy appears at the car’s wheels to drive it along.
Generally, as a vehicle’s weight decreases, its fuel efficiency improves. Less power is needed to move a lighter vehicle than to move a heavier one. However, manufacturers must also balance vehicle weight against passenger safety. Cars that have the strong, solid construction needed to protect passengers in crashes also tend to be heavier than cars that crumple easily. Also, safety features such as airbags and stability control add weight.
By using lightweight materials to replace steel, manufacturers can build more fuel-efficient vehicles without sacrificing safety, durability and comfort. Common lightweight materials include aluminum alloys, plastics, magnesium alloys, carbon fibre and metal matrix composites (materials that combine metal and non-metal components). For every 10% of weight eliminated from a vehicle’s total weight, it has been estimated that fuel economy improves by 7%.
Researchers must also find cost effective ways to mass produce vehicles constructed with lightweight materials. Current aluminum technology can cut half the weight out of a conventional body structure, and many manufacturers are already using it extensively.
In 2010 BMW and SGL established a joint venture to manufacture car parts made of carbon fibre-reinforced plastics, and Mercedes-Benz and Toray Industries formed a similar joint venture this year. Carbon fibre is about 50% lighter than steel and, as well as improving fuel efficiency, carbon fibre-reinforced plastic parts also make car bodies stiffer and better able to withstand crashes.
However, these lightweight technologies are not the only ways in which manufacturers are achieving better energy efficiencies. BMW is a leader in stop-start technology, which switches cars’ engines off when they are stationary at red lights or heavy traffic. Other manufacturers have introduced similar technologies. Seven- and eight-speed automatic transmissions and dual-clutch transmissions provide fuel efficiency benefits compared with manual gearboxes. Using lower viscosity, friction-modified engine oils and transmission fluids also helps to improve fuel efficiency.
New “run-flat” tires (which can withstand loss of pressure long enough to drive to a tire-change workshop) mean that cars do not need a spare tire or the equipment required to change a tire, saving more weight.
Even greater energy efficiencies are achieved with gasoline/electric or diesel/electric hybrid vehicles, usually with regenerative braking. In the end, manufacturers are looking for any strategies to improve fuel efficiencies.
David Whitby is chief executive of Pathmaster Marketing Ltd. in Surrey, England. You can reach him at pathmaster@dial.pipex.com.