The riddle of steel: A-UHSS
Jean Van Rensselar, Contributing Editor | TLT Cover Story July 2011
How advanced ultra high-strength steel is saving lives, conserving fuel and revolutionizing the way cars are made.
KEY CONCEPTS
• A-UHSS is revolutionizing the auto industry due to low weight, high strength and the ability to absorb and repel energy.
• Unique properties require specialized lubrication considerations.
• Issues such as repair and rescue need to be resolved.
Most people have, at one time or another, watched in awe as a race car driver walked away from what seemed to be a horrific accident. Built into that car and unseen to spectators is a roll cage that prevents the car from collapsing and either injuring or killing the driver. Thanks to advanced ultra high-strength steel (A-UHSS), many people are driving what seem to be pretty average passenger cars that have the same state-of-the-art protection. They’ll never know it and never appreciate it—until they get into an accident and their car turns into a crash-protecting machine that both repels and absorbs energy in a carefully engineered sequence that Detroit has mastered.
It’s a safe bet that people driving cars built after 2005 are protected by some A-UHSS. This includes areas that would logically contribute to crash protection such as door collision beams, A-pillars, B-pillars, the roof rail, the lower rocker area from the A- to C-pillars and possibly cross-members running beneath the floor pan or across the roof. In some cars, like the Chevy Volt, there is basically a cocoon of A-UHSS.
A-UHSS is revolutionizing both the steel and auto industries. With demands to dramatically increase gas mileage without reducing crash safety and with steel the primary component of nearly all motor vehicles (about 60%), it only makes sense that the savior for both industries would be an extremely lightweight yet high-strength steel that significantly reduces vehicle weight while actually enhancing safety. Reducing a car’s weight by 10% will reduce gas consumption anywhere from 3% to 7%. A-UHSS can make this happen.
There are a number of types of A-UHSS, each with a slightly different production process. Each type has some benefits and drawbacks, and there are unintended consequences of using this type of steel to make cars. Yet without a doubt, A-UHSS is the future, and the average amount of A-UHSS in vehicles is increasing every year (even though the cost of this steel can be 100% higher than traditional alternatives).
OVERVIEW
For those involved in automotive design and manufacture, things just got much more complex. Most of the new-to-market high-strength steels offer both cost and weight savings while improving performance. Their increased form ability allows parts to be consolidated; this means fewer individual parts (less welding, lower cost) and more manufacturing flexibility.
Pete Ulintz is a member of the North American Deep Drawing Research Group and product development manager for Anchor Manufacturing Group Inc., in Cleveland, Ohio, an automotive stamping supplier actively involved in industry research. He says, “Because the new generation of HSS (high-strength steel) offers increased form ability, automotive stampings are becoming more complex. Components that used to be two or three individual parts joined together, usually by welding, are now a single stamping. Also, die design strategies are changing due to higher forming loads and reverse energy loads—after punching and blanking. Die wear and dimension stability, due to increased spring back, are major concerns.”
The line between mild steel and basic high-strength steel occurs at a yield strength of about 210 mega pascals (MPa) [30 kilo pounds per square inch (KSI)] (1). A simple carbon-manganese (CMn) steel has yield strength levels between 280 and 350 Mpa (40 to 50 KSI). Adding carbon and manganese to increase strength isn’t practical for yield strengths greater than 350 Mpa (50 KSI) because of a sharp decline in key properties.
One approach to achieving yield strengths between 280 and 550 Mpa (40 and 80 KSI) is to use high-strength, low-alloy (HSLA) (or microalloyed) steels. HSLA steels usually have a microstructure of fine-grained ferrite strengthened with carbon and/or nitrogen precipitates of vanadium, titanium or niobium/columbium. To further increase the strength, manganese, silicon or phosphorus can be added.
A more advanced (and usually less expensive) method for creating yield strength levels is to use A-UHSS grades, specifically:
• Dual-phase (DP)
• Transformation-induced plasticity (TRIP)
• High hole expansion (HHE)/Stretch Flanging High-strength (SFHS)
• Complex-phase (CP)
• Martensitic
A less common type is MnB steel, which contains mainly manganese and boron. Boron A-UHSS varies from less than a millimeter thick to almost two millimeters thick (a U.S. quarter is just less than two millimeters thick).
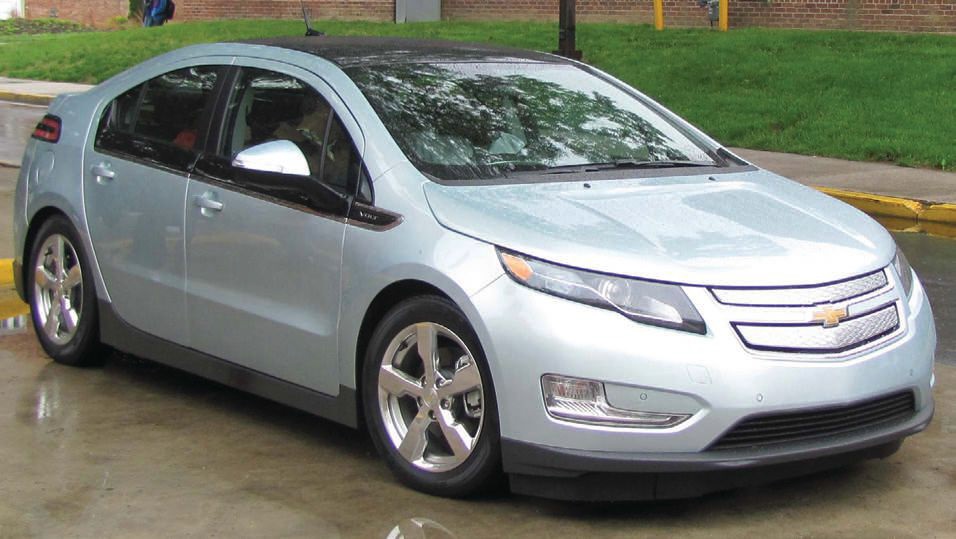
More than 70% of the Chevy Volt’s total structure is made from high-strength steel.
THE AUTO INDUSTRY
The auto industry is the current A-UHSS use leader. While U. S. automakers have been plagued by design and reliability issues, they excel in their strategic use of A-UHSS. In conjunction with optimized manufacturing techniques, A-UHSS offers reduced product weight, reduced cost, better crash performance and streamlined manufacturing process consolidation.
Motor Trend magazine voted the Chevy Volt plug-in electric as its 2011 Car of the Year. This honor was largely made possible by advanced engineering that included the liberal use of A-UHSS. More than 70% of the Volt’s total structure is made from high-strength steel, making it safe, durable and energy efficient—at a price. The base price is $40,000.
Where a single grade of steel was once sufficient for a car’s frame, today’s frames are composed of a mélange of different types and strengths of steel. These steels are selected by computer modeling areas of high and low stress and areas most impacted in severe crashes. The strongest steel is used in parts like door beams to stop another car’s bumper from encroaching on the passenger compartment. Another area is windshield pillars to keep the roof from collapsing onto the chassis in a rollover. New U.S. regulations dictate that the roof must be able to withstand three times the vehicle’s weight in a rollover. This is double the previous standard and not achievable with mild steel.
Even though it may make sense to use A-UHSS in a particular area, there are other logistics to be concerned about. For instance, a part made of A-UHSS could reduce weight, but it also might require more money to produce the necessary tools and dies. A-UHSS may also require different welding methods, something that can throw a cog into the assembly line.
While A-UHSS allows parts to be thinner, some parts, like exterior panels, are already so thin—less than a millimeter or 1/25 of an inch—that lack of rigidity becomes an issue. In other words, no matter how strong the steel is, there’s a thinness threshold.
With the new push for lighter weight cars, the steel industry is facing stiff competition from the aluminum and plastics industries for some parts. Strong, yet form able AUHSS products are allowing the steel industry to stay ahead.
STLE-member Ted McClure is a manager at TribSys LLC in Valparaiso, Ind., which contracts friction testing and also manufactures specialty friction test equipment. The company was a consultant and testing contractor for the Auto/ Steel Partnership Tribology Team investigating the tribology of advanced high-strength steels from 2001 until 2008.
“Incorporation of these materials into vehicles occurred rapidly and is continuing,” McClure says. “Combining these high-strength materials with other design and manufacturing advances, including hydro-forming and warm and hot forming, is offering new opportunities for vehicle weight reduction. These advanced materials, though, present additional forming challenges, including increased spring back; much higher contact pressures and temperatures resulting in galling and accelerated die wear; high snap-through forces which can damage presses; and edge cracking.”
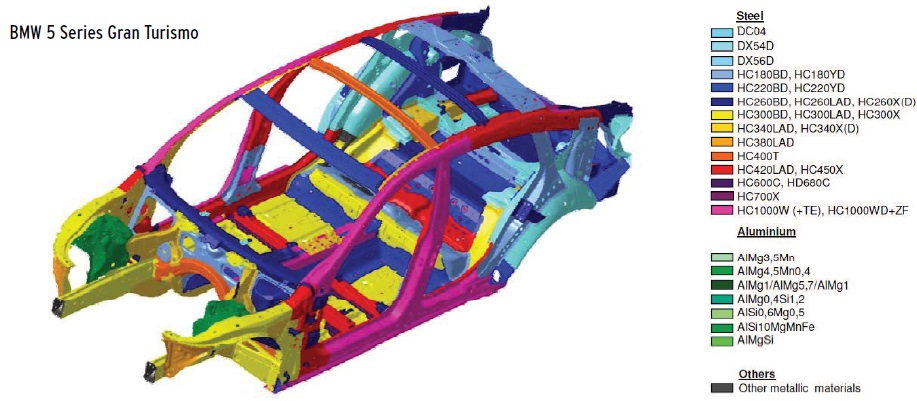
Figure 1. Steel and Aluminum Frame Composition in a BMW 5 Series Gran Turismo (Courtesy of Taylan Altan, CPF, The Ohio State University)
FIVE TYPES
There are five basic types of A-UHSS. Depending on added properties, strength classifications can change. For example, DP steel can be either high-strength or A-UHSS.
1. Dual-phase (DP) steels. DP steels have a microstructure of soft ferrite with a dispersion of hard martensite. The strength level of these grades is proportionate to the amount of martensite in the microstructure.
In its raw form, its yield strength (YS) is significantly lower than its tensile strength (TS), with a YS-to-TS ratio of about 0.6. The YS-to-TS ratio for HSLA steels is closer to 0. 75. The lower DP YS-to-TS ratio leads to higher elongation values and better form ability.
HSLA steels begin to lose form ability as soon as deformation starts. But because of the soft ferrite matrix of DP steels, they maintain their form ability further into the press stroke and can better distribute the strains throughout the product.
HSLA steel is not bake-hardenable (strengthening does not occur after the steel goes through a paint-bake cycle), but DP does have this property. This bake hardenability and the higher level of work hardenability can contribute to an increase in yield strength of about 140 Mpa (20 KSI) after forming and baking. In contrast, HSLA steels only have an increase of about 20 Mpa (3 KSI).
DP steel also absorbs energy better than HSLA steel. Relative to the yield strength, the DP steel tensile strength is higher than that of HSLA steels. This improves crash performance. For crash performance equivalent to that of HSLA steel, a DP steel can be downgauged 10%. DP and HSLA steels have about the same degree of weldability, but slightly different processes may be required.
Ideal auto applications for DP steel include those that require high strength and formability, like wheel and bumper reinforcements.
2. Transformation-induced plasticity (TRIP) steels. As with DP steel, the microstructure of TRIP steels is composed of mainly soft ferrite. But where DP steel has martensite as the only other phase, TRIP steels have a composite of martensite, bainite and retained austenite. The relative amounts of these chemicals give TRIP steels their distinctive properties.
During the forming process, as strain increases, retained austenite in TRIP steel gradually converts to martensite. But the volume and shape alteration in the microstructure absorbs the strain and increases the ductility. At higher strains, the high-work, work-hardening rate persists in TRIP steel, while the rate in DP begins to abate. This work-hardening advantage is a primary reason for the better formability of DP steel over HSLA steel, and this is also what gives TRIP steel a further edge over DP steels.
The strain level of the retained austenite-to-martensite transformation can be engineered by adjusting the carbon content. With lower carbon levels, transformation starts as forming begins. This yields excellent formability and strain distribution. As carbon levels increase, retained austenite is more stable and remains in the final part. The transformation occurs at strain levels greater than those produced during forming and stamping. A significant benefit of TRIP steel is that the transformation from austenite to martensite also occurs during subsequent deformation, providing better crash energy absorption during a car collision. But the additional alloying required to get the TRIP effect makes spot welding more challenging than it is for other steels.
3. High hole expansion (HHE)/stretch flanging high-strength (SFHS) steels. Parts stamped from HHE/SFHS steel grades are increasingly replacing cast and forged parts made of other materials. HHE/SFHS steels are ideal for applications requiring significant sheared edge elongation (or hole flanging). The HHE/SFHS microstructure is primarily ferrite and bainite, along with a small amount of retained austenite. HHE/SFHS steels have high strength, high formability and high hole flanging (sheared edge extension) capacity. The ferrite-bainite microstructure allows high hole expansion values.
4. Complex-phase (CP) steels. CP steel has a microstructure similar to TRIP steel except that CP steel has no retained austenite. With the hard phases like martensite and bainite and further strength from fine carbon or nitrogen precipitates of niobium, titanium or vanadium, CP steel strength ranges from 800 to 1,000 Mpa, (145 KSI) which makes the steel excellent for auto parts that require a high capacity for energy absorption such as anticrash rods, bumpers and B-pillar reinforcements.
5. Martensitic steels. Martensitic steels have a microstructure of 100% martensite. Minimum tensile strength is typically between 900 and 1,500 Mpa (130 and 220 KSI). Because of its limited elongation, martensite produced at a mill is usually roll-formed. More complex shapes can be fabricated by hot forming and quenching a lower carbon grade.
These grades can have carbon content like that of low-carbon steel (greater than 0.2%). Manganese, molybdenum, boron, silicon, chromium and vanadium in various combinations increase hardenability. Excellent applications for martenistic steels are those that require high strength and good fatigue resistance, with relatively simple cross sections such As auto-side sill reinforcements, door intrusion beams and bumper reinforcement beams.
COMMON STEEL TYPES
Notice that some steel types cross categories, depending on added properties. For example, some A-UHSS, such as some TRIP and DP steels, are stronger and less malleable than some martenistic steels.
Standard (Mild) Steels
• Commercial steel (CS)
• Drawing steel (DS)
• Deep drawing steel (DDS)
• Interstitial-free (IF)
High-Strength Steels
• Bake hardenable (BH)
• Isotropic (IS)
• Carbon-Manganese (CMn)
• High-strength low alloy (HSLA)
• Dual Phase (DP) - Complex phase (CP)
• Transformation induced plasticity (TRIP)
• Martensitic (MART)
Advanced Ultra High-Strength Steels
• Dual Phase (DP)
• Transformation induced plasticity (TRIP)
• High hole expansion (HHE)/ Stretch Flanging High-strength (SFHS)
• Complex phase (CP)
• Martensitic
• MnB steel
PRODUCTION PROCESS
A-UHSS begins the same way mild steel begins with molten iron. The molten iron and usually added scrap becomes steel when oxygen is forced into the melt in a basic oxygen furnace. The gas oxidizes the iron while removing impurities and most of the carbon.
Additional steel strength is created by alloying, primarily with carbon. But depending on the metal and how much of the alloy is used, alloying can be costly. The auto industry, in particular, is keen to keep costs down.
The next step in transforming the steel requires altering the configuration of the steel’s crystalline structure with temperature. Processes like cold-rolling, annealing and quenching are used. The steel sheet (which has already been rolled once during the initial process) is rolled again at room temperature and then heated to a high temperature (above 1,300 F) before being rapidly cooled (quenched) by water. The rapid cooling then converts the austenite to martensite. This precise, fast and continuous rapid cooling process creates added strength with far less alloying. By precisely controlling the rate of cooling, the proportion of ferrite and martensite can be varied to produce steels with differing strengths and formability capabilities.
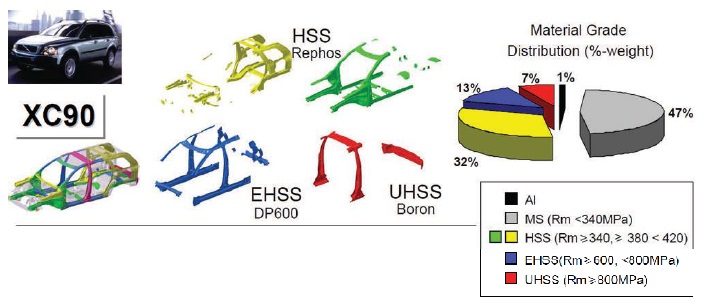
Figure 2. Material Grade Distribution as a Percent of Weight in the Volvo XC-90 (Courtesy of Taylan Altan, CPF)
ISSUES
There are some issues in the manufacture and handling of AUHSS that make the material a challenge. Frank J. Kenny is the R&D director at IRMCO in Evanston, Ill., which has collaborated with and supported academic groups studying the forming properties of A-UHSS and the best lubricant choice for this grade of steel. Kenny says, “Advanced high-strength steels continue to present challenges to metal formers. Generally speaking, A-UHSS itself is much more aggressive on press-working tools. Premature tool wear becomes a paramount concern for metal formers.” Two primary issues are spring back and stretch-flangeability.
SPRINGBACK
After a flat-rolled metal is cold-worked and as the forming force is released, the metal tends to revert to its original shape due to its natural elastic recovery properties. Basically, spring back is caused by unbalanced stresses in the formed part and is influenced by a number of factors, including tensile strength, yield strength (after forming rather than the flat sheet) and thickness.
Spring back is a concern with all high-strength steels, including A-UHSS. However, the higher strength of A-UHSS usually creates more spring back. DP steel has much greater spring back than HSLA steel because the parts made from DP steel have greater yield strength after forming. Also, the DP steel’s tensile strength is about a third greater than that of HSLA steel. The good news is that spring back can be controlled to some degree by adjusting tooling parameters.
STRETCH FLANGEABILITY
Stretch flanges are created by expanding the radius at the cutouts in sheet metal blanks during the forming process. The process increases the flange edge length as the metal deforms. Auto industry examples include cutouts in automotive window panels. When the circumferential strain is large enough, necking and cracking failures occur. Stretch flangeability is also referred to as edge ductility and hole expansion performance.
Martensite and other secondary phases of the A-UHSS grades reduce stretch flangeability; as strength increases, the degree of the problem increases with it. A clean edge cut is especially important for blanked or sheared edges and punched holes in A-UHSS. Cutting tools also need to be sufficiently sharp. Worn tools result in a 20% reduction in hole expansion (stretch flangeability) in mild steels but a reduction of 50% or more in DP and TRIP grades (2).
“The challenges arise from the unique properties of A-UHSS,” McClure says. “One needs to understand that there will be higher forces, contact pressures and resulting high-die temperatures. These considerations affect press, tool and lubricant selection. There is a lot of interest in servo- drive presses, which offer enhanced control of the forming process. Servo-drive presses may be one way to help optimize forming processes for certain advanced materials.”
LUBRICATION CONSIDERATIONS
As A-UHSS becomes the new standard for auto manufacturing, understanding how well the lubricant works with the material and tooling design becomes critical. Using lubricants designed for A-UHSS grades is important for a number of reasons, not the least of which is that high press forces lead to higher temperatures that can cause some lubricants to break down or burn.
“When considering a metal-forming operation, there are three major factors to start with—the tool/die, the workpiece and the lubricant,” McClure says. “Workpiece material changes often require changes in the forming processes, the die material and die coatings and the lubricants. Changing any one of these might require re-evaluation of the others.”
McClure explains that there is currently much research into die materials and die coatings in order to deal with the higher forces generated in forming high-strength steels.
A-UHSS may require hard die coatings to prevent excessive wear and galling, and a lubricant may behave very differently on a coated die compared with an uncoated one. A lubricant that performs well on uncoated tool steel dies and punches may be ineffective if the change is made to a coated tool.
Taylan Altan, professor and director of the Center for Precision Forming (CPF, formerly ERC for Net Shape Manufacturing) at The Ohio State University in Columbus, Ohio, says, “Since these materials have a high strength, they need more wear-resistant die materials or inserts as well as lubricants that can withstand higher pressures and temperatures at the die/material interface.”
The user needs to consider compatibility of the lubricant with the specific combination of workpiece and die materials. Because of higher die temperatures, some lubricants may smoke excessively, or they may oxidize on the workpiece more quickly, causing problems with finishing further down the road.
A-UHSS is significantly more difficult to draw than conventional cold-rolled grades, but the quality of the forming lubricant helps. “Due to higher forming forces and blank holder pressures, friction and heat are major issues with AUHSS materials,” Ulintz says. “Better lubricants are required that don’t break down at the higher process’s high temperatures. For deep drawing, lubricants that significantly reduce friction and aid material flow under the blank holder are required.”
Extreme-pressure (EP) lubricants have long been considered the best way to achieve high-performance tool protection on demanding deep-drawn or heavy-gauge formed parts—in particular, sulfur and chlorinated EP additives blended with straight oil could improve tool life.
“Generally speaking, forming these metals puts a higher demand on the metalworking system tooling, material and lubricant,” Kenny adds. “A less robust lubricant is more likely to fail. We have encountered numerous potential customers that have gone back to chlorinated oils to deal with the metalworking demands of A-UHSS. Bargain lubricants generally do not hold up well over time, and the metalworking system suffers.”
However, with the introduction of A-UHSS and tighter environmental/disposal requirements, EP is no longer the oil of choice. The high heat necessary to form A-UHSS causes EP oils to underperform, no longer providing the tool-protecting barrier required for extreme-temperature (ET) applications (3).
EP versions of high-solids polymer (HSP) lubricants do provide adequate protection. However, HSP lubricants have a thin viscosity when applied; as the temperature rises the viscosity becomes thicker and more persistent. In fact, these heat-seeking ET fluids will attach to hot metal, creating a friction-reducing film barrier. This protective barrier allows the tool to stretch and form metal without splitting, thus controlling friction and metal flow.
“Again, selection of the lubricant is dictated in part by the specific combination of workpiece and tool surfaces being used, along with the consideration of much higher forces and temperatures,” McClure says.
Such lubricants do exist. Altan says, “We need lubricants with pressure additives that can withstand high pressures as well as the temperatures, up to 150 C/302 F or so, that are generated at the die surface. These lubricants are available. At our center we evaluate the performance of those lubricants for many lubricant suppliers and OEMs.”
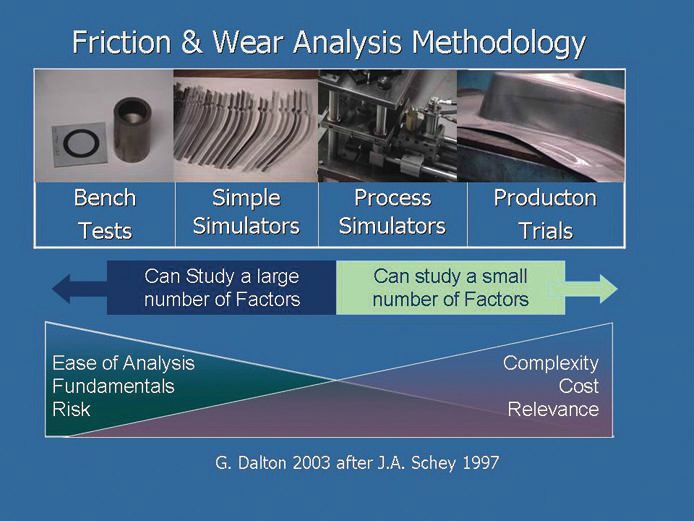
Figure 3. Friction and Wear Analysis Methodology (Courtesy of Ted McClure, TribSys LLC)
LUBRICATION TESTING
The best way to examine and address lubrication issues is through lab testing that recreates real-world use conditions. “There are many simulators on the market that come in and out of vogue. But there is no one perfect predictor,” Kenny says. “While we try to prescreen candidates in the lab, there is inevitably more work to be done in press trials.”
McClure notes that there are many test options, including bench and simulation tests. Simulation tests scale down a specific process in order to bring the exact operation into the laboratory setting. If well done, these tests should, and often do, correlate very well with field experience. Examples include draw bead simulation, hydro-forming tube expansion, cup or dome-forming tests and tapping torque in metal-cutting. However, they are specific to the operation being scaled down and are generally more expensive and time-consuming than the second type of laboratory test, bench tests.
Bench tests create specific tribological conditions that may be common to several operations. Application of the test data requires an understanding of the test condition and how it applies to the metalworking process being studied. In that sense, it can be less reliable than simulation in predicting performance of lubricant/tool/workpiece combinations in the field. However, some bench tests have shown excellent correlation with field performance, and they are generally less costly and time-consuming to run.
“This is particularly important to metal-forming lubricant formulators who may want to evaluate many additives and combinations of additives for effectiveness on different tool/workpiece combinations,” McClure says. “Often work will begin using bench tests, then progress to simulation and ultimately field trials. The bench test should minimally be able to use the same surfaces being used in production, for example electro-galvanized steel against D2 tool steel, if these are in use in the operation.”
Examples of commonly employed bench tests include twist compression, four-ball, pin-and-vee block, and Reichert.
“Real-world stamping can be simulated very well in a research setting using various types of commercial Finite Element Analysis (FEA) software,” Altan explains. “However, it is important to have the reliable material data—flow stress and formability—and friction data such as the coefficient of friction that may vary with die/material interface pressure and temperature. Often people who simulate sheet forming using FEA do not input the proper data into the software. As a result, the output may not be quite reliable, i.e., it won’t emulate the actual production conditions in the shop.”
REPAIR AND RESCUE CONSIDERATIONS
The presence of A-UHSS is increasing in most new cars, leading to increased fuel efficiency and better crash performance. This is great news for consumers, not so great for those involved in body repair. On newer vehicles, the old rules no longer apply. A single part may be made from several different types of steel, and there is virtually no way to identify A-UHSS by sight.
Right now the only way to detect it without reading the repair specs is through shop tools that struggle and/or fail. It also helps to know where A-UHSS is most likely to be found, areas that would logically contribute to crash protection such as door collision beams, A-pillars, B-pillars, the roof rail, the lower rocker area and cross-members beneath the floor pan or across the roof.
The only universal recommendations for repair specifies that heating should not be used to straighten A-UHSS because the temperature required to straighten damaged steel causes the mechanical properties of the work-hardened part to degrade.
There is still a large amount of research that needs to be conducted to determine the limits of repair ability. The steel and auto manufacturers are currently working overtime to hone and document repair techniques in areas such as welding, drilling and cutting.
Then there’s the issue of emergency rescue. Rescuers are now aware that many new vehicles they encounter at a crash scene will have key structural parts made of A-UHSS. The difference between workers in a body shop and rescue workers, though, is that rescuers don’t have access to repair specs and have no way to tell (other than tool failure) what the parts are made of. Because the primary rescue tool, the hydraulic rescue cutter, will stall when trying to cut through A-UHSS, this is a significant problem. Failed manufacturing and repair tools are one thing, failed rescue tools, which may mean the difference between life and death, are quite another.
FINALLY…
A-UHSS is currently being considered for applications that extend far beyond the auto industry. Its use should continue to grow as handling and repair issues are resolved. With the increasing pressure on car makers to reduce weight without compromising style and increasing cost means that the market for A-UHSS will remain strong. In a sense, A-UHSS is also one of the saviors of the steel industry. This massive application A-UHSS is the perfect way to defend the steel market as the material of choice for auto-making.
“Government regulations, as well as market conditions and fuel prices, dictate that automakers continue to improve fuel economy while maintaining or improving crash worthiness of vehicles, without increasing costs,” McClure says. “A key enabling technology to accomplish these objectives is the use of alternative materials, including A-UHSS.”
REFERENCES
1. A Pascal is equivalent to one Newton per square meter. A megapascal is one million pascals.
2. Introduction to advanced high-strength steels - Part II, click here.
3. From Advanced Lubricant Technology For High-Strength Steel, by Brad Jeffrey, full article available here.
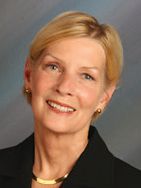
Jean Van Rensselar heads her own communication/public relations firm, Smart PR Communications, in Naperville, Ill. You can reach her at jean@smartprcommunications.com.