In search of: The perfect biodegradable lubricant
Jean Van Rensselar, Contributing Editor | TLT Cover Story June 2011
Such a product doesn’t exist yet, but if it did it would look something like this.
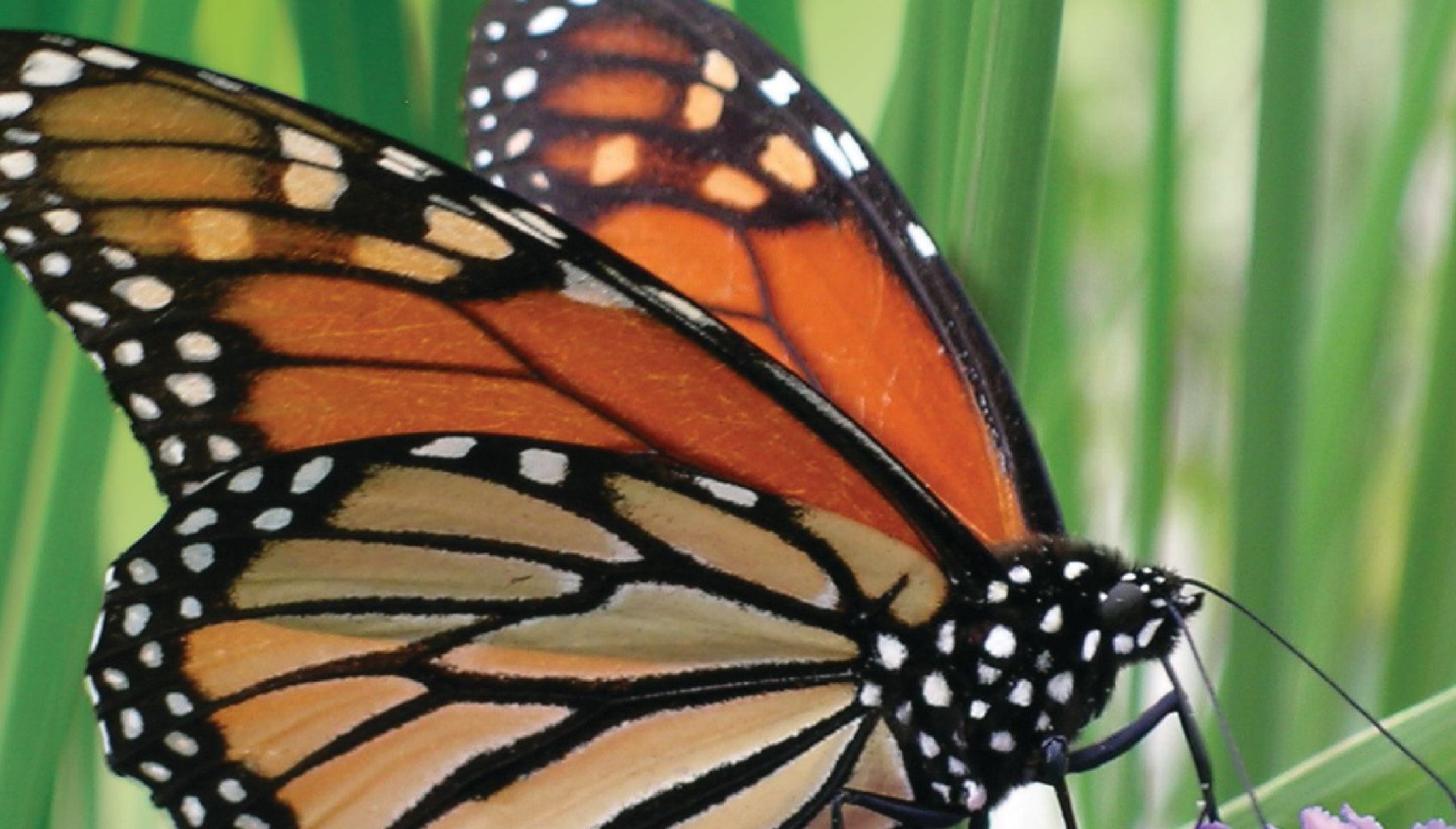
www.canstockphoto.com
KEY CONCEPTS
•
The perfect biodegradable lubricant would be eco-non-toxic, biodegrade quickly and into non-damaging components, perform acceptably and cost-effectively and be capable of sustainable large-scale production.
•
Except for niche applications, there’s nothing like that on the market now.
•
Four classes of good alternatives exhibit a wide range of lubrication properties and biodegradability.
There is a lot of ambiguity in the terms people use to describe eco-friendly products. Toxic means one thing to a biochemist and something else to an environmentalist. The same goes for other relevant terms such as biobased and biodegradable. Creating a uniform definition of these terms (using them in their strictest sense) would eliminate a lot of the misunderstandings, false claims and disappointments that taint these products and, in some cases, discourage their use.
Producing a truly eco-friendly lubricant is vastly more complex than producing, for example, an eco-friendly cardboard box. A basic cardboard box only has to contain things while even a basic lubricant must satisfy a demanding set of parameters. Add in an eco-friendly requirement, and things get very complex very quickly.
The earliest lubricants were biobased and biodegradable—think vegetable oils and animal fats. The discovery of petroleum and its lubricating properties changed everything. Suddenly there was a miracle substance that could be morphed into just about anything used for fuel and lubrication for a fraction of the cost of vegetable and animal products.
Petroleum shortages, skyrocketing costs and, most of all, concern for the environment created renewed interest in biodegradable lubricants. Product development began in earnest about 1990. While viable biobased, biodegradable lubricants were produced, a number of factors, including cost and availability of raw materials, has prevented their widespread use except in very specialized areas or where mandated, i.e., waterways, farmlands, forests and protected parks.
Manufacturers are beginning to realize that the green movement isn’t really a movement anymore. It’s a fact of life and an expectation for some products—more and more this includes lubricants.
“The cost of a tarnished public image and/or lost productivity due to clean-up measures can be detrimental to the future of any business,” says STLE-member Brian Goldstein, The Dow Chemical Co.’s product marketing manager for Lubricants & Fuel Additives in Houston.
Test of biodegradability is performed in a control standard test environment where test bacteria break down the lubricant while consuming oxygen and producing carbon dioxide. An oil spilled on frozen ground, for example, may not change over an extended period of time. (Courtesy of UNI-NABL Center)
THE HIDDEN MAGNITUDE
A small oil spill and even a series of small oil spills often go unnoticed. Unless the spill occurs in a highly regulated facility in a highly regulated industry in a very public location or causes immediate and obvious damage, no one (not even the person responsible for the spill) will likely be aware of it.
The National Oceanic and Atmospheric Administration (NOAA) estimates that over 700 million gallons of petroleum enter the environment each year. Only half of it is the result of irresponsible and illegal disposal. Industry experts estimate that 70% to 80% of hydraulic fluids leave systems through leaks, spills, line breakage and fitting failure, and about 40% of that ends up in the environment (
1).
Some debate exists as to whether it’s more important that the spilled oil be visible (to aid clean-up) or that the oil be invisible (water soluble and dispersible) as long as it has negligible environmental impact.
“This depends on if the spill is over land or water,” explains STLE-member Kevin Kovanda, president of American Chemical Technologies in Fowlerville, Mich. “Over land any fluid chemistry would be easy to clean-up, but over water clean-up would be very difficult for fluids that float (unless they were in a stagnant pool). In moving water, as soon as the fluid is spilled it is migrating to a different area, and damage is occurring.”
This visibility debate is really about the desirability of sheen-producing oils that essentially flag the spill. Putting the flag issue aside, Goldstein explains that the damaging effects of sheen are more than just cosmetic.
“When considering any lubricant for use in environmentally sensitive areas, one must evaluate the impact on various wildlife species, proximity to water bodies and regulations,” he says. “It’s the chemical and environmental properties of a lubricant that need to be examined to determine the risk of using such products in sensitive environments.”
Two key challenges with use of mineral oil in sensitive environments include their inherent propensity to create a sheen on water and their inability to disperse within water. This means that mineral oils will float on top of a water body, reflect the sunlight needed by aquatic species and remain in concentrated pools on the water or at shorelines.”
STLE-member Lou Honary, University of Northern Iowa Professor and Director of the UNI-NABL Center in Waterloo, Iowa, believes that the issue of sheen needs to be redefined when it relates to biobased oils. “A biobased oil will also produce a sheen initially,” he says, “but exposed to light and oxygen and in the presence of water, it will quickly emulsify and break down to harmless constituents. Thus sheen may need to be redefined as something that persists over water for a given period of time.”
Types of Eco-Friendly Hydraulic Fluids
Source: Click here.
ELIMINATING AMBIGUITY
Specification criteria for environment-friendly lubricants can include (
2):
•
They cannot contain lead, barium or halogenated compounds.
•
They cannot contain any carcinogenic material.
•
Any nitrites and tin they contain must be less than 0. 25%.
•
They cannot have any toxic effects on aquatic organisms.
The term biolubricant is correctly applied to all lubricants that are rapidly biodegradable and non-toxic. The terms biobased, biodegradable and environmentally non-toxic often are used interchangeably but shouldn’t be.
Rainwater dilutes the oil and the oil begins to emulsify and at the same time algae begin to grow. (Courtesy of UNI-NABL Center)
BIOBASED
Biobased is a term that was introduced by the U.S. Department of Agriculture to aid the promotion of renewable crop, oil-based products. To be biobased, a lubricant needs to be formulated with a renewable basestock. Most biobased base oils are biodegradable, but when formulated with chemical additives as finished lubricants they may no longer be because microorganisms cannot completely break them down into innocuous carbon dioxide. Even biobased lubricants that are biodegradable may still be toxic to the environment, especially if they contain large quantities of chemical additives as performance enhancers.
BIODEGRADABLE
Biodegradable lubricants meet certain standards for biodegradation and could be derived from any source including non-renewable petroleum or renewable oils. While a biobased oil is renewable, a biodegradable oil may be from either renewable or non-renewable sources.
Lubricants that are biodegradable are capable of breaking down naturally into common elements and assimilated back into the environment. But just because something is assimilated back into the environment doesn’t mean it’s not harming the environment. Because nearly everything will biodegrade if given enough time, another important factor is exactly how long the substance takes to biodegrade—100 days or 100 years? Again, biodegradability does not equate to environmental friendliness.
ASTM 6064 defines biodegradable as a function of the degree of degradation, time and test methodology. There are two descriptors for biodegradability widely used by the EPA and Coast Guard:
readily and
inherently.
Readily biodegradable. A substance that is readily biodegradable will degrade 80% in 21 days in a controlled standard test environment. This property is most desirable because the substance will degrade before it causes environmental damage. Vegetable-based lubricants, some PAGs and some synthetic ester-based lubricants exhibit this property.
“There is evidence that some fluids rated as readily biodegradable do not degrade as rapidly as promoted if the environment they are spilled onto is not fertile enough for biodegradation or the bacteria concentration is too low,” Kovanda says.
Inherently biodegradable. Substances that are inherently biodegradable are merely capable of biodegrading, as there are no time or degree parameters. Not uncommonly, these products are petroleum-based, conventional fuels and lubricants that are correctly but misleadingly labeled as biodegradable. Inherently but not readily biodegradable products can persist in the environment for years, causing significant damage. Really, the only environmentally safe aspect is that they are biobased and contain no heavy metal additives, making them less toxic than other petroleum-based lubricants.
There are two commonly used measurements for biodegradation. The first is primary degradation, which measures reduction of the carbon and hydrogen bonds (C-H) in the initial solution—the reduction of the amount of the lubricant. The most widely used test to measure this decrease is the CEC-L-33-A-93.
The other measurement is secondary (ultimate) degradation. This measures the evolution of CO
2 through the biodegradation process. ASTM D6384 defines ultimate biodegradation as total substance utilization by microorganisms resulting in the production of carbon dioxide, water, inorganic compounds and new microbial cellular constituents (biomass or secretions or both). But even this definition is undergoing revision. The common test for this is the ASTM D4684 or the OECD 301 (
3).
ENVIRONMENTALLY NON-TOXIC
Toxic to some means lethal or debilitating. This implies that formulations that are non-toxic to the environment (plants and wildlife) may still be harmful. Others use the term more narrowly. For example, the lubricant standard for aquatic toxicity is the concentration that either affects 50% of the species or causes 50% mortality (the loading rate that has a 50% effect [EL50] or causes 50% mortality [LL50] after the stated time).
Standard tests for eco-toxicity generally apply to the aquatic environment. Typically, the tests are for acute toxicity, which measures the concentration required to kill organisms anywhere from 1-4 days.
THE PERFECT PRODUCT
Given all this, the perfect environmentally-friendly lubricant would:
1.
Be non-eco-toxic
2.
Biodegrade quickly
3.
Biodegrade into components that are not immediately damaging to the environment.
But to be commercially viable, it must also:
4.
Perform acceptably
5.
Be capable of sustainable large-scale production
6.
Be cost effective.
Tough but not impossible, experts say. Let’s examine these six properties.
1. NON-ECO-TOXIC
There are many biobased and biodegradable formulations that are environmentally toxic, just as there are many nonbiobased and non-biodegradable formulations that are not toxic to the environment. Among and within the three types of lubricant basestock classifications (mineral, synthetic and biobased) there is a wide range of toxicity. The perfect environmentally-friendly lubricant would be completely non-toxic at any concentration.
Honary explains, “We use the term non-toxic very carefully when talking about biobased lubricants. Our laboratory tests have shown that pure mineral oil and pure soybean oil are both safe to
daphnia magna, which are considered indicator species and are used for testing aquatic toxicity (OECD 208). Pure mineral oil has been prescribed for human consumption for years for digestive issues. At the same time, our experience has shown that some chemical additives that are considered safe for human consumption are toxic to
daphnia magna. To be considered non-eco-toxic, substances may require testing for toxicity to plant, human and aquatic life.”
2. BIODEGRADES QUICKLY
The OECD 301 series of biodegradability tests are often used as a reference for biodegradability, requiring a lubricant to biodegrade a minimum of 60% over 28 days. This means inherently and readily biodegradable.
3. BIODEGRADES INTO NON-DAMAGING COMPONENTS
The main differentiators between primary and ultimate biodegradation are the end-products. A substance that qualifies as a primary biodegradable just has to be able to change its physical or chemical properties. On the other hand, an ultimate biodegradable can be completely broken down by microorganisms into CO
2 and water (
4).
4. PERFORMS ACCEPTABLY
Our ideal lubricant also must be able to compete with similar but non-biodegradable lubricants on properties such as:
•
Lubricity
•
Viscosity and rheology
•
Solubility
•
Thermal stability
•
Oxidative stability
•
Hydrolytic stability
•
Flash & fire points
•
Volatility.
As eco-friendly as users want to be, in real-world use biodegradable lubricants aren’t a viable option unless they satisfy at least the basic functions of a well-performing lubricant. Honary believes the current USDA standards established for biobased labeling may need further enhancement because the labeling is primarily based on the percent of biobased content and the result of life-cycle analysis.
“This leaves the performance criteria to the lubricants manufacturer,” he says. “Considering the diversity of specifications by various original equipment manufacturers, many biobased-labeled lubricants on the market today have varying degrees of performance specifications, which leads to doubt and skepticism by the major lubricant users. The most successful commercially available biobased products are those that perform equally and cost the same as petroleum products. Those happen to be biobased greases ranging from truck grease to railroad curve grease to food-grade grease.”
5. LARGE-SCALE PRODUCTION
The perfect eco-friendly lubricant would have to be derived of components and processes with sustainable high volume capabilities.
This is where things get a little sticky with biobased lubricants, such as those made of canola oil, corn and particularly soy. While there is disagreement on this, some experts say that there is actually not enough arable land in the U.S. to allow the biobased lubricant market to produce enough soybeans to satisfy the current market for lubricants and biofuels.
One acre of land is only capable of producing 47 gallons of soybean oil every year, enough to lubricate one piece of heavy equipment for about six months. Experts figure that in order to meet U.S. demand alone, soybeans would have to grow on 612 million acres of land. Right now there are only 470 million acres of arable land (
5).
6. COST EFFECTIVE
It doesn’t matter how quickly and completely a lubricant biodegrades or how well it performs if no one can afford it. Of course, during the R&D phase and for a few years following, small economies of scale will make even the most viable lubricants unaffordable. The goal is to find something that works and increases production efficiency, quickly enough to bring the cost close to its non-biodegradable competitors. In some areas though, especially those considered lost-in-use applications, the cost parity already exists.
WHAT'S OUT THERE NOW?
Sixty years ago, before their environmentally friendly properties were widely recognized, PAGs were originally marketed as fire-resistant fluids, quenchants and textile fluids. Then natural esters were introduced as environmentally-friendly fluids and later synthetic esters. As the green movement grew, researchers began to take a second look at PAGs.
Right now there are four classes of biodegradable lubricants. Within those classes are some good products on the market now and more being developed.
“Traditionally, natural- and synthetic ester-based lubricants have been used widely in environmentally sensitive areas as alternatives to mineral oils,” says STLE-member Martin Greaves, The Dow Chemical Co.’s Technology Leader for UCON Fluids & Lubricants in Horgen, Switzerland. “Many of these offer good equipment reliability and favorable environmental performance such as high levels of biodegradability.”
Following are the four major classes of biodegradable lubricants.
A plant growth chamber is used to determine terrestrial plant toxicity of biobased lubricants. (Courtesy of UNI-NABL Center)
TRIGLYCERIDES
The first biobased lubricant bases were unsaturated ester (triglycerides) oils of vegetable and animal origin. Overall, they have good lubricating properties, far superior to those of mineral oil. Vegetable oils also have a very high viscosity index (223 for soybean oil vs. 90 to 100 for most petroleum oils). Vegetable oils also have high flash/fire points: 610 F (326 C) for soybean oil vs. 392 F (200 C) for mineral oils (
6).
But they come up short in a few important areas. Vegetable oils, in their natural form, are not oxidatively stable enough for all lubricant use without modification (which increases cost). Another negative is the high pour point. There are also problems with thermal stability, as most natural vegetable oils need significant modification and performance-enhancing additives to withstand reservoir temperatures greater than 80 C (176 F) for extended periods of time.
Finally, they are susceptible to hydrolytic degradation and, if not properly treated with demulsifiers, could break down when exposed to water. It’s worth noting that the shortcomings of triglycerides are compensated for by their flexibility. Chemical modifications can be made at any of three reaction points:
1.
Ester group: hydrolysis and transesterification/interesterification
2.
Carbon–carbon double bond: selective hydrogenation and epoxidation
3.
Hydroxyl group (in case of castor oil): hydrolysis, selective/ complete hydrogenation, epoxidation and dehydration.
Most important, vegetable oils get the highest environmentally friendly score of any lubricant substance with 90%-100% biodegradability and significantly lower CO
2 emissions. Additional environmental benefits include low aquatic toxicity and low volatility. Tests have shown that most vegetable oils biodegrade over 70% within a 28-day period, compared with petroleum oils that biodegrade about 15% to 35% (
7).
In addition to the arable land production restrictions mentioned above, a primary consideration is the food vs. fuel debate; it’s difficult to justify turning edible crops into biofluids when significant global populations are going hungry. One way to address this would be a global ban on the export of non-edible crop-based fluids. This would permit the exportation of food but not fuel made from food. The U.S., for example, could export soybeans and edible soybean products but couldn’t export soybean-based biofuels.
According to Honary, vegetable oil-based formulated lubricants and greases have found their niche in many specialized markets, especially in lost-in-use applications. He explains, “Now that we have nearly 20 years of experience with vegetable oil-based lubricants, the emphasis is shifting to nonedible industrial crops that do not compete with food and through either selective planting or genetic modification can be grown in arid lands.”
Triglycerides, while not inherently the most oxidatively stable lubricants, accommodate additives well. They get high marks for biodegradability but are questionable as far as large-scale production and cost are concerned. Their success at this time seems to be in applications where the products tend to end in the environment.
“At this time, greases made with vegetable oils are performance and price competitive in applications such as truck greases, rail curve greases, food machinery greases and most all marine and mining applications,” Honary says. “But for vegetable oil-based hydraulic oils, gear oils and other liquid lubricants that persist in the machines, the price will be higher, and proper maintenance will be vitally important.”
The sheen rule
There is a common misperception that the U.S. Coast Guard approves oils based on whether or not they leave a sheen. In actuality, the Coast Guard does not recommend or endorse any fluids. But the issue of leaving a sheen is addressed in U.S. Regulation (40 CFR 110), which is, in substance, as follows:
DISCHARGE OF OIL REGULATION (40 CFR 110)
Under the legal authority of the Clean Water Act, the Discharge of Oil regulation, more commonly known as the “sheen rule,” provides the framework for determining whether an oil spill to inland and coastal waters and/or their adjoining shorelines should be reported to the federal government. In particular the regulation requires the person in charge of a facility or vessel responsible for discharging oil that may be “harmful to the public health or welfare” to report the spill to the federal government. The regulation establishes the criteria for determining whether an oil spill may be harmful to public health or welfare, thereby triggering the reporting requirements, as follows:
•
Discharges that cause a sheen or discoloration on the surface of a body of water
•
Discharges that violate applicable water quality standards
•
Discharges that cause sludge or emulsion to be deposited beneath the surface of the water or on adjoining shorelines.
Because the Oil Pollution Act of 1990, which amended the Clean Water Act, broadly defines the term oil, the sheen rule applies to both petroleum and non-petroleum oils (e.g., vegetable oil). The regulation also provides several exemptions from the notification requirements.
Source: click here.
POLYALKYLENE GLYCOLS
Polyalkylene glycols (polyglycols, PAGs) biodegrade easily and can be formulated in a wide viscosity range (
8). Polyglycols offer many of the same benefits as synthetic esters but offer far superior hydrolytic stability. As with esters, care has to be taken in determining compatibility with some seals and paints. In general, PAGs offer excellent lubricity, high Vis and perform well at temperature extremes, making them a good choice for all-season use. A down side is that they don’t blend with mineral or polyalphaolefin oils.
According to Kovanda, PAGs are the only fluid that passes the EPA Static Sheen Test (
9). Also, they are nearly non-toxic in terms of aquatic environments in that they do not turn acidic in the presence of water, and they possess the only fluid chemistry that does not form sludge and varnish as the fluid degrades.
“We presently have our PAG-based fluids running successfully in tunnel-boring equipment, hydro-electric plants, dredging, locks and dams, amusement parks, mobile equipment, cruise ships and in several pieces of U.S. Army Corps of Engineers (USACE) equipment,” Kovanda says.
Recently the PAG-based fluid that Kovanda’s company developed was chosen over synthetic ester for use in the winches on the USACE floating crane.
The two major families of polyglycols are random copolymers of ethylene oxide and propylene oxide and polypropylene glycols. Polypropylene glycols are not water-soluble, but random copolymers of ethylene oxide and propylene oxide are water-soluble. This is an issue because many methods for assessing biodegradability are applicable only to non-water-soluble lubricants.
Another disadvantage of PAGs (and PAOs) is their poor solubility with some additives. Because the additives themselves must ideally be biodegradable, this limits the additives that can be used to formulate effective biodegradable PAG/PAO-based lubricants.
Another disadvantage of PAGs for some existing specifications (such as the European Eco-Label adopted in 2005), is that they are not derived from renewable feedstocks. This is a key requirement of that specification. For example, the renewable content of hydraulic fluids is set at a level greater than 50%. Natural and some synthetic esters offer a high renewable content and are therefore preferred. Greaves says it’s likely that in the future there will be PAGs that are derived from renewable feedstocks. The technology exists now but is not widely used.
“No other major family of lubricant base oil is available that offers water solubility,” Greaves says. “It is this property that can provide unique features for lubricants used in environmentally sensitive areas.
But there is a down side to this also. Because PAGs are totally water-soluble, there is concern for the use of these fluids near critical areas such as potable water intakes. At the request of the USACE, Kovanda developed spill-modeling data to predict what would happen if an oil spill occurred in, for example, the Mississippi River and how fast it would disappear and biodegrade. Small, medium and large river flows were analyzed. In essence, the data predicts how far a given size spill would travel and the amount of time before it dilutes to a safe concentration.
Given all this, PAGs have some excellent lubrication properties but like other synthetics are not as cost effective as mineral oil. PAGs get an A+ for biodegradability.
SYNTHETIC ESTERS
Esters have been used in synthetic lubricants for more than 60 years. Synthetic esters are a diverse family of synthetic lubricants that can be customized to physical and performance specifications. Synthetic esters, which include diesters and polyolesters, are made from organic acids and alcohols and were originally formulated as a better-performing alternative to triglycerides. They are sometimes used without additives (in very high temperature applications) or blended with polyalphaolefins (PAOs) or other synthetic basestocks to maximize lubrication properties.
When a biodegradable product needs to perform outside the average temperature range, synthetic esters are the first choice since they can operate in temperatures exceeding 400 F (204 C) and still maintain long fluid life.
In addition to excellent high- and low-temperature performance, synthetic esters offer low volatility and good lubricity. Synthetic ester fluids have a long service life and are available in a wider viscosity range than other types of biodegradable lubricants.
Synthetic esters exhibit a highly desirable and unique combination of low-temperature viscosity and clean high-temperature operation. They also have relatively higher lubricity, a higher flash point, lower volatility and a lower rate of evaporation than most lubricants. They make good solvents and dispersants that prevent deposits of varnish and sludge. Importantly, they are highly biodegradable.
Blendable diesters can be combined with PAOs to form base oils that are biodegradable, have good solubility, resist oxidation and have good temperature viscosity properties. Blending synthetic diesters with canola oil yields similar results.
The most common concern when formulating fluids with ester basestocks is compatibility with the elastomer material used in the seals, as extra consideration must be taken for seal compatibility. Another potential disadvantage with esters is their propensity to react with water or hydrolyze under certain conditions. They are also significantly more expensive than mainstream lubricants.
Synthetic esters have excellent lubricating properties, are highly biodegradable but often must be blended with other fluids (bringing up new issues of biodegradability). They are also costly.
A closer view of the plant growth chamber used to determine the toxicity of biobased lubricants. (Courtesy of UNI-NABL Center)
POLYALPHAOLEFINS AND RELATED HYDROCARBONS
Developed in the 1930s, polyalphaolefins (PAOs) are polymers produced from a simple olefin acting as a monomer. An equivalent (more common) branding term is polyalkene. They don’t react with water and are compatible with most metals.
PAOs are readily biodegradable and offer good low-temperature performance, hydrolytic stability and low volatility. They are a good choice in applications where low viscosity is necessary. While higher-viscosity PAO fluids exist and also perform extremely well, for the most part only inherently biodegradable (they do not biodegradable quickly enough to be readily biodegradable).
Among the advantages of PAOs is the fact that they can be customized for a variety of applications by manipulating the chemistry. Other favorable properties include:
•
Low environmental toxicity
•
Better than average biodegradability (among all types of fluids)
•
Low deposit formation
•
Thermal stability (across a wide temperature range)
•
Hydrolytic stability
•
Sheer stability
•
Low corrosivity
•
Compatibility with mineral oils.
The wide temperature performance range of PAOs, combined with excellent chemical and physical properties, makes these fluids a good choice for lubricants in general. However, their subpar biodegradable performance, when compared to other biodegradable fluids, gives them a distinct disadvantage in environmentally sensitive applications.
FOR NOW…
The perfect biodegradable lubricant hasn’t been developed yet, but there are some very good alternatives. The most pressing needs are improving lubricating properties in a way that doesn’t reduce biodegradability and bringing down the cost. Until that day when the perfect biodegradable lubricant is developed and available, there are other ways to lubricant usage more environmentally friendly:
•
Use less lubricant
•
Use formulations that extend the useful life of lubricants
•
Use formulations that can be re-refined
•
Use biobased lubricants that are best for lost-in-use applications.
For now, in environmentally sensitive applications, selection of the best product from a number of good alternatives is of primary importance. But perhaps the best approach for protecting the environment is to prevent leaks and spills in the first place through monitoring and maintenance. Even readily biodegradable lubricants need to be properly cared for to avoid unnecessary contamination.
“Different regions of the world have different views and policies pertaining to what an environmentally friendly lubricant should be,” Goldstein says. “This is an ongoing discussion. Despite all of the work that goes into spill-prevention programs, it is still inevitable that accidental spills will occur. Lubricant selection needs to be a well defined provision of a spill-prevention program.”
REFERENCES
1.
“The Care and Feeding of Biodegradable Lubricants Lessons Learned in the Real World,” By Fred Sullivan, Transocean, Inc., and Mark Miller, Terresolve Technologies, Ltd., click
here.
2.
Developed at the 2010 Bangalore workshop was jointly organized by the Department of Mechanical Engineering, IISc and the Tribology Society of India, Karnataka Chapter.
3.
Ibid, Sullivan, Miller.
4.
Experts like Martin Greaves and Kevin Kovanda say that for an oil to be considered biodegradable, it should be ultimately biodegradable.
5.
Ing, Adam, Biobased Lubricants: A Viability Study, 2009. Available
here.
6.
Biodegradable/Biobased Lubricants and Greases, Lou A. T. Honary, University of Northern Iowa, click
here.
7.
Ibid
8.
Higher molecular weight polyglycols degrade at slower rates.
9.
Appendix 1 to Subpart A of 40 CFR 435.
Jean Van Rensselar heads her own communication/public relations firm, Smart PR Communications, in Naperville, Ill. You can reach her at jean@smartprcommunications.com.