20 Minutes With Dr. Puliyur Madhavan
Karl M. Phipps, Managing Editor | TLT 20 Minutes June 2011
This Pall Corp. researcher with experience in filtration technology discusses the future of aerospace fluid systems.
PULIYUR MADHAVAN - The Quick File
Puliyur Madhavan is currently a vice president in the Scientific and Laboratory Services department at Pall Corp. in Port Washington, N.Y. He’s responsible for global scientific and technology support for filtration applications in the aerospace and defense, transportation and mobile equipment and industrial manufacturing markets. Primary application areas include filtration for fluid systems such as hydraulic, lube, pneumatic and fuel systems, onboard aircraft and vehicles, in industrial in-plant machinery, turbomachinery and power-generation fluid systems, as well as pulp and paper, mining, primary metals and offshore subsea areas.
Puliyur has more than 23 years of experience working in filtration technology specializing in aerospace fluid systems, especially power and propulsion fluid systems. He’s a member of several technical and standards development organizations, including STLE, SAE AE-5 Committee (Aerospace Fuel, Lube and Oxidizer Systems), SAE E-34 Committee (Aerospace Propulsion Lubricants) and has worked on programs with the IATA Fuels Group. In addition, he’s published numerous articles and technical papers relating to contamination control in aerospace fluid systems, and he is the author of several SAE standards related to filter performance evaluation and filter debris monitoring.
He received his doctorate in chemistry from the State University of New York at Stony Brook in 1982 and did post-doctoral research work at Brookhaven National Laboratory and SUNY at Stony Brook.
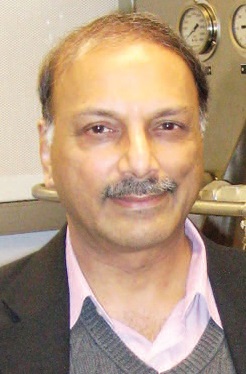
Puliyur Madhavan
TLT: How were you introduced to tribology as a work area?
Madhavan: During my graduate and post-doctoral work, my primary research area focused on theoretical surface chemistry as it applies to modeling chemisorption on transition metal surfaces. As I progressed in my post-doctoral work, my inclination moved toward more practical applications of surface chemistry.
When I began working in industry in the filtration technology area, I wanted to combine surface chemistry of filtration media and contaminant removal. However, one of the first programs I became involved in was surface wear of hydraulic and lubrication system components, related to solid contamination and the impact of fine filtration in reducing component wear. Coincidentally, this was my first introduction to tribology applied to such fluid systems, and I found the discipline to be fascinating.
Subsequently, I moved into filtration applications in the aerospace arena, specializing in power and propulsion fluid systems. This was a happy melding of my fascination for airplanes and aerospace when I was growing up. I discovered a newfound interest in applied tribology and filtration technology, which culminated in me focusing in this area. I have never regretted this decision.
TLT: What challenges do you foresee for the aerospace industry in the future?
Madhavan: In the aerospace fluid systems area, some of the short- and long-term challenges include composite and ceramic materials, alternate fuels and higher thermal stability lubricants and fuels.
Failure modes of metals and metal alloys have been studied for several centuries, and their tribological analysis and modeling is considered to be well established in aerospace applications. In contrast, composites are relatively new. They have been used in certain structural components of aircraft over the years, and recently their use has been extended to fluid systems such as fuel tanks and also to individual components in fluid systems. The challenges this brings forth from a tribology perspective is the characterization of composite component wear and failure modes and the ability to detect impending failure modes on aircraft without complex equipment and procedures.
Ceramic bearings are at the advanced research stage and pose a similar challenge in terms of their wear and failure modes. Traditional aerospace bearings, especially those used in gas turbine power plants, have been extensively studied and modeled in terms of their properties and fatigue failure characterization. The modeling has included the effects of fluid characteristics (viscosity, lubricity, etc.) and fluid contamination on bearing fatigue life. A similar level of understanding would have to be developed regarding material failure modes and specific bearing failure modes for ceramic bearings.
Drop-in alternate fuels, comprised primarily of synthetic hydrocarbon blends in the appropriate chain length range and blended with current jet fuels (50% mixture), have been approved for use by ASTM and other agencies. These fuels have properties that fall in the range of current jet fuels and only pose moderate challenges to the industry in terms of potential elastomeric swell and contamination by biodiesel fuels that are transported in the same pipelines presently in Europe. A major challenge would be alternate fuels that include non-hydrocarbon basestocks including esters (such as those used in biodiesels) which would pose serious materials compatibility issues as well as performance issues. It is unlikely that these fuels will be specified in the foreseeable future.
Turbine lubricants, currently in use, are widely acknowledged to have reached their thermal limits in terms of turbine-power plant lubrication system applications. While several chemical classes of compounds such as perfluoropolyethers (PFPE), perfluoroalkylethers (PFAE) and perfluoropolyalkylethers (PFPAE) have been considered, primarily in military applications, they are not currently in use in commercial applications due to several disadvantages of these lubricants for commercial use. However, going forward, the industry will need to address this issue.
Higher thermal stability fuels may sound like an oxymoron, but thermal degradation of fuel is a key issue in the fuel systems used in high-performance engines utilized mostly in military applications. This leads to the formation of carbonaceous deposits and altered combustion characteristics. Furthermore, this leads to decreased fuel efficiency and thermal energy and increased maintenance.
Various additives are used in high thermal stability fuels such as JP8+100 fuels to improve thermal stability. While these fuels reduce engine maintenance by keeping the fuel system and associated engine turbomachinery components cleaner, many materials in the current engines are incapable of handling the higher temperatures required to realize the full benefits of higher thermal energy associated with the higher thermal stability fuels. This poses a challenge to the industry.
Given the projected increase in air traffic and regulations, a long-term challenge includes emissions control for aircraft engines.
Given the projected increase in air traffic and regulations, a long-term challenge includes emissions control for aircraft engines.
Turbine lubricants are widely acknowledged to have reached their thermal limits in terms of turbine-power plant lubrication system applications.
TLT: What is the most interesting aspect of your job?
Madhavan: One of the many interesting aspects of my job is troubleshooting contamination-related problems in aircraft/engine fluid systems. The diversity of applications, as well as the various technical areas that must come together to arrive at a final solution, is both fascinating and, at times, very challenging.
For example, arriving at the root causes of reduced filter element service life in a fluid system (i.e., premature filter element plugging) can involve combining information about fluid system design and operation, fluid chemistry, analytical chemistry, tribology and filtration technology to arrive at the solution. Needless to say, such projects are usually time-consuming bound with respect to determining a solution as quickly as possible and in many ways are akin to detective/ forensic work, of which I am a fan.
The combination of practical, application-related and academic projects, including research projects and those related to industry standards committees, also makes my job very interesting.
Traditional aerospace bearings have been extensively studied and modeled in terms of their properties and fatigue failure characterization.
TLT: Why do you think there is an overlap between tribological academic research and industrial challenges?
Madhavan: With regards to the aerospace industry, the bridge between academic tribological research and the industrial challenges is natural. The aerospace industry has a long-established practice of close collaboration with military research institutions, national research laboratories and academic institutions for research in structural and fluid system component materials, including fluids.
Some of the main drivers in the aerospace industry are safety, reliability, fuel efficiency and longer maintenance intervals, and this trend will continue. This requires novel, lightweight aircraft materials, advanced fluids technology and the ability for fluid (and other) system components to have a long mean-time-between-replacement (MTBR), i.e., higher reliability. The study of failure modes of fluid system components such as pumps, bearings, gears and valves is essential for improving the reliability of key fluid systems such as engine lubrication and fuel systems, helicopter transmissions and aircraft hydraulics systems, all of which are critical systems in aircraft engines.
Thus the cutting edge technologies employed in the aerospace industry are strong drivers of academic research, which results in a natural progression of basic academic research (often funded by the industry or government), leading to more directed applied research and eventually culminating in the actual application of the technology or materials to product platforms by industry.
Incidentally, this is also increasingly true for other industries such as the automotive industry and mobile equipment in the mining industry.
Significant work has been carried out in filter debris analysis in aircraft fluid systems, especially in engine lubrication systems.
TLT: How can filtration technology be applied to aerospace fluid system condition monitoring and tribological aspects such as fluid system component wear?
Madhavan: In aerospace fluid systems such as aircraft engine lubrication and fuel systems, helicopter transmissions and airframe hydraulic systems, the filter element can provide useful information about the fluid system’s condition. The filter element can offer real-time indication of abnormal contaminant ingression or generation in the fluid system and can also assist in the root cause analysis, as described below.
The build-up of filter-element differential pressure with service time, once normalized for fluid flow rate and viscosity changes, is a function of contaminant loading of the filtration medium. Once a range of normal filter-element differential pressure build-up curves has been established, an accelerated differential pressure build-up would indicate abnormally high contaminant loading conditions associated with accelerated component wear, abnormally high external contaminant ingression (possibly through seal leaks) or generation of fluid breakdown products (such as coke formed from the thermal breakdown of engine lubricants). Since modern aircraft-monitor filter-element differential pressure builds up on a continuous basis, the indication of abnormally high contaminant loading of the filter can be obtained on a real-time basis. Another useful benefit of continuous filter-element differential pressure monitoring is the ability to predict remaining filter element service life.
Evaluation of the debris captured by the filter element can supply valuable information on the origin of the contamination loading the filter element. Environmental debris would be indicative of external seal leakage or operation in an excessively contaminated environment. Large concentrations of characteristic metallic wear debris would denote accelerated component wear. The presence of fluid breakdown products could be due to thermo-oxidative degradation (coke) or additive precipitation. Chemical elemental analysis of the debris could pinpoint specific component wear modes. In this manner, the filter debris could provide insight into tribological processes associated with component wear in fluid systems.
Significant work has been carried out in filter debris analysis in aircraft fluid systems, especially in engine lubrication systems. Sophisticated correlations have been established for specific military engine models between filter debris and accelerated lube system component wear and impending failure modes. On the commercial side, many operators evaluate filter debris for diagnostic purposes. Some engine filter elements incorporate a pull-out diagnostic layer that can be removed on site for examination of collected debris. The porosity of the diagnostic layer is tailored to capture larger debris of significance from a component wear perspective.
You can reach Puliyur Madhavan at puliyur_madhavan@pall.com.